A while back, we tore down the now infamous hoverboard, with the intention of uncovering how the product was made so cheaply and easily by manufacturers large and small in China. For this teardown, we decided to go to the opposite end of the spectrum and see what changes when an experienced industry leader designs and manufactures a similar product. At a retail price of $1,300, the Segway miniPRO is six times the cost of the hoverboard, so it better be good.
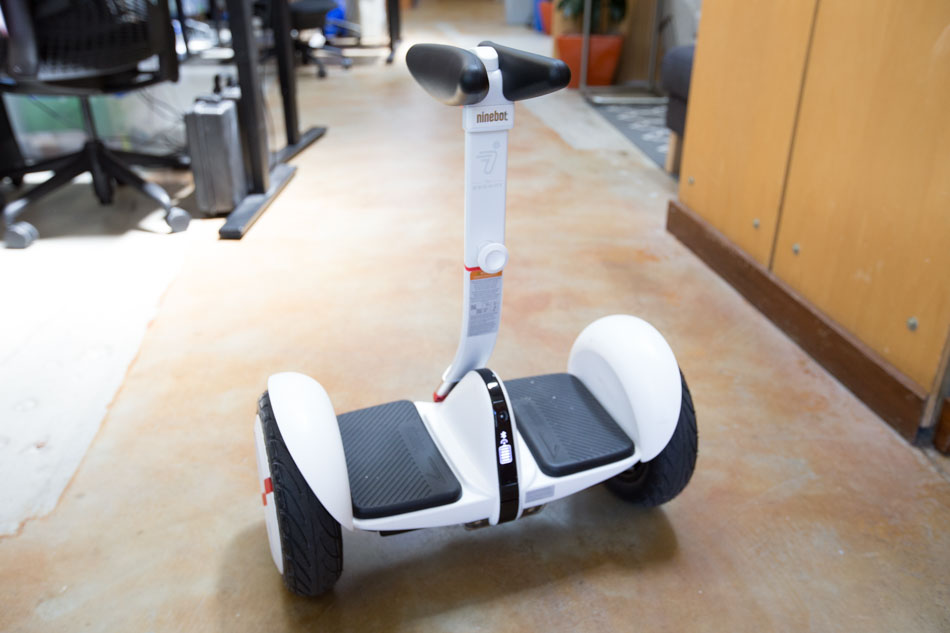
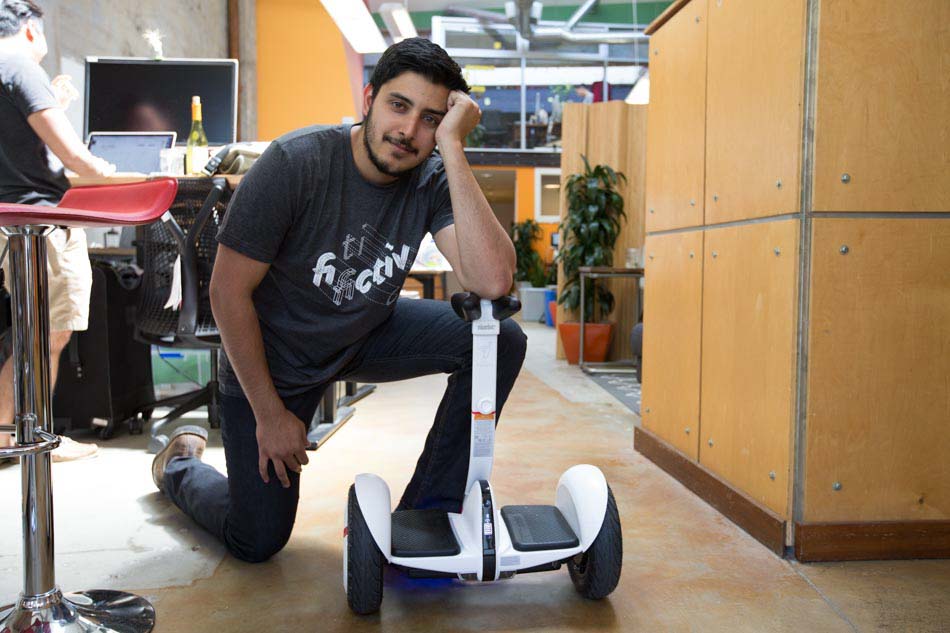
In all honesty, I had a hard time tearing this one down. Once you step onto the miniPRO, it only take a few short rides to get fully acclimated, unlike the hoverboard, where even an experienced rider constantly risks losing balance or badly stubbing a toe. The stability is much better; the larger tires help tackle city terrain; and the center arm allows for much improved steering control with your legs.
Ninebot obviously gave a lot of thought to the end user, and it immediately shows in the riding experience. Sadly for me, I have a “job” to do, and sometimes that involves tearing apart things that I wish I could just ride around the office delightedly.
Steering
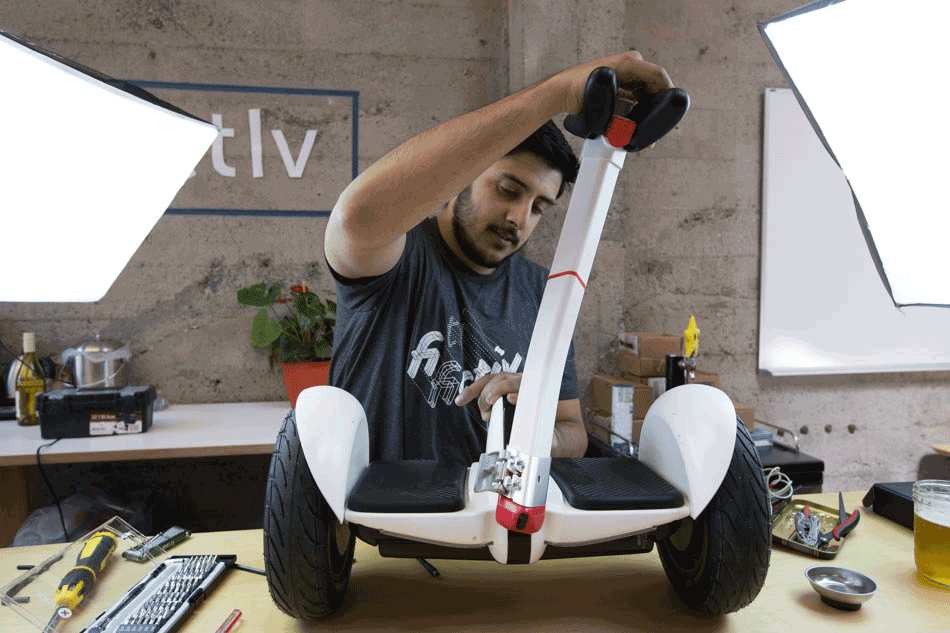
To start the teardown, I removed the center steering arm from the body, which was held on by a quick release clamp and tensioned by a couple of screws. This is great for storage or transportation. The connection between the arm and the body of the miniPRO is a focal stress point, as it’s responsible for all steering as riders move their legs left and right.
Much like the brake pedal in a car, this connection point needs be strong because it can’t fail when you need it most! This connection point combines a guide rail to ensure the arm reattaches correctly and ribbing for added strength.
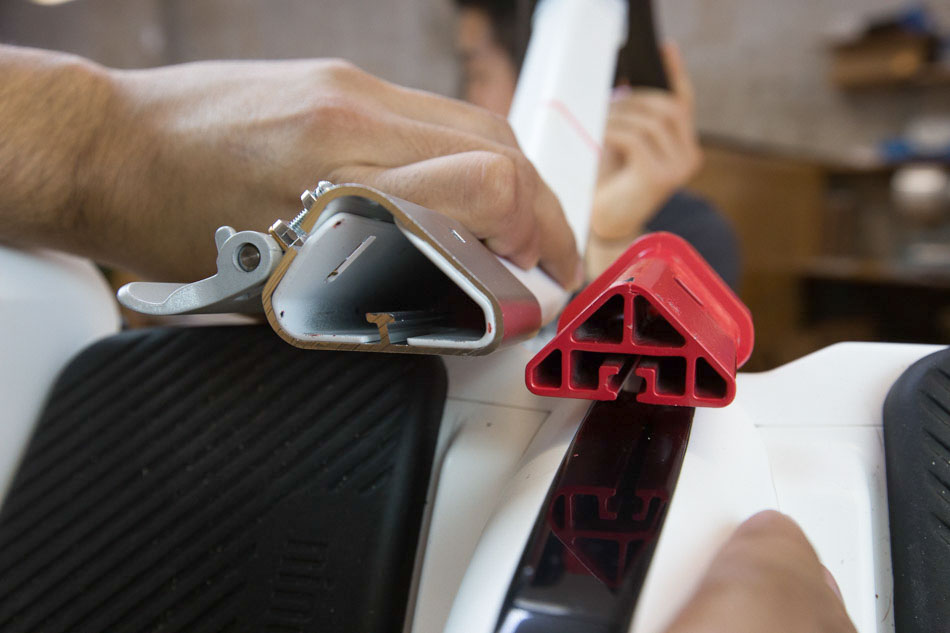
At the top end of the steering removed steering arm, you’ll see the knee pads. These were made with a rigid plastic core for structural strength, encapsulated by a polyurethane foam that gives it a smooth and cushioned finish. It’s just like a bicycle seat.
The manufacturing process is similar to insert molding or overmolding: The rigid plastic has been injection molded separately, and then it gets inserted into another mold, where the polyurethane foam comes in. The polyurethane goes through a chemical reaction and expands around the rigid core.
This process is called R.I.M. (Reaction Injection Molding). Here’s a great video that explains it.
Moving to the body of the miniPRO, I started by removing that ribbed connector that attaches to the arm. Underneath, you’ll see the other end, which is a solid steel knob that translates the linear movement of the rider’s movements to a rotational motion that can be read by the PCBA to initiate the turn.
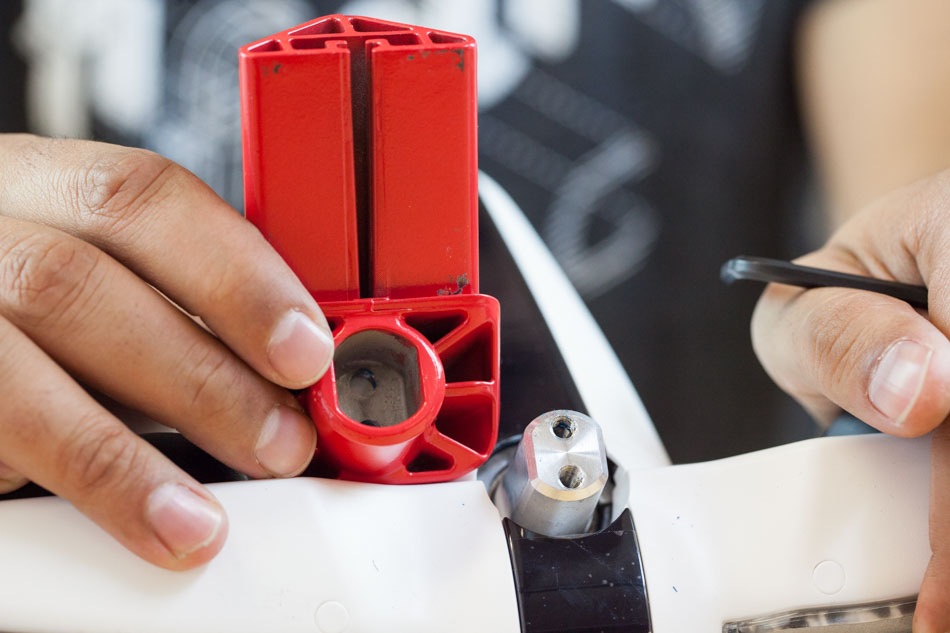
Internally, the rotation of the steel knob is measured by a Hall effect sensor that translates the change in electromagnetic field into a voltage output. The mechanism to make it all work is quite ingenious.
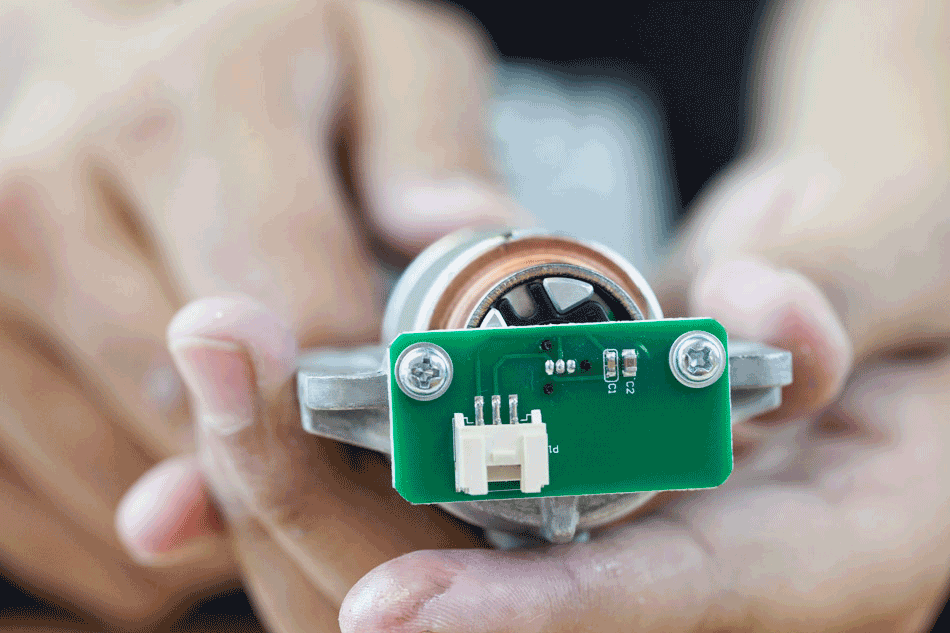
- The entire solid steel knob sits in a magnesium alloy encasing, where it can rotate freely. The hall-effect sensor is fastened in place to the encasing. The opposite end of the steel knob has three magnets that face the sensor.
- Between the magnesium alloy encasing and the steel knob is a black plastic guide covered in dampening grease, which slows down the rotation and creates consistently smooth rotation.
- Brass covers are used at both contact points, for a low coefficient of friction that allows the metal knob to rotate easily.
- Attached to the inside of the of the Hall effect sensor is a stationary energized magnet around which the steel knob rotates.
- As the magnets from the steel knob rotate around the stationary, energized magnet, the distance from the Hall plate can be determined by measuring the change in the electromagnetic field.
- This measurement is then translated to a voltage output to each wheel, which helps you turn.
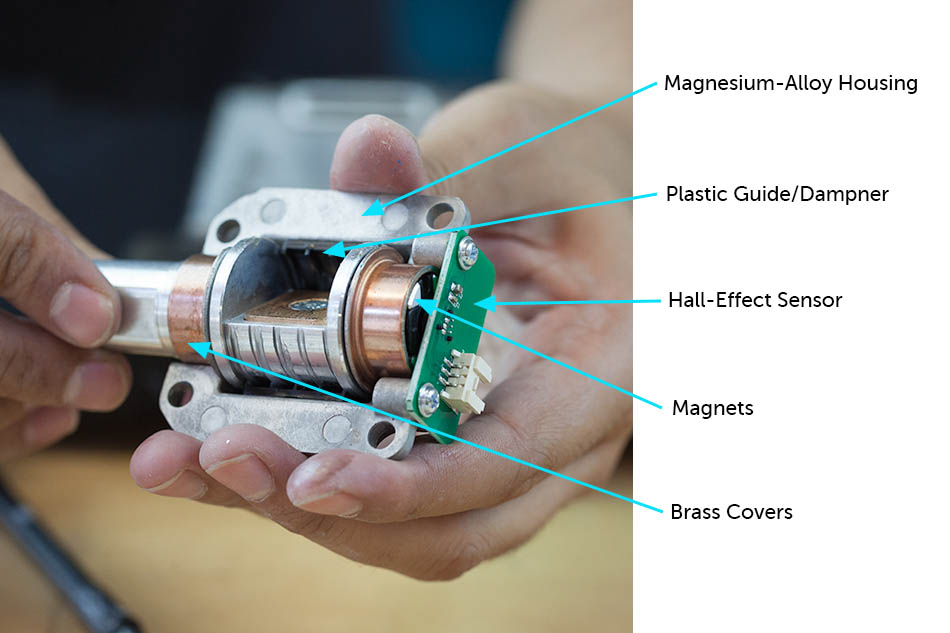
Battery + Communication
Removing the steering arm makes the product much easier to flip over and access the screws on the bottom side. It’s this point where we really start to see how this high-end product differs from a cheaply made hoverboard.
Removing the screws was no walk in the park—they were secured with plenty of loctite, which prevents vibration loosening. After finally getting the screws off, I removed the battery and found a gasket that sealed all the internal electronics from dust and water, which was a major flaw in the design of the hoverboard. The miniPRO has an IP54 rating, meaning dust penetration and splashing water won’t impact its functionality.
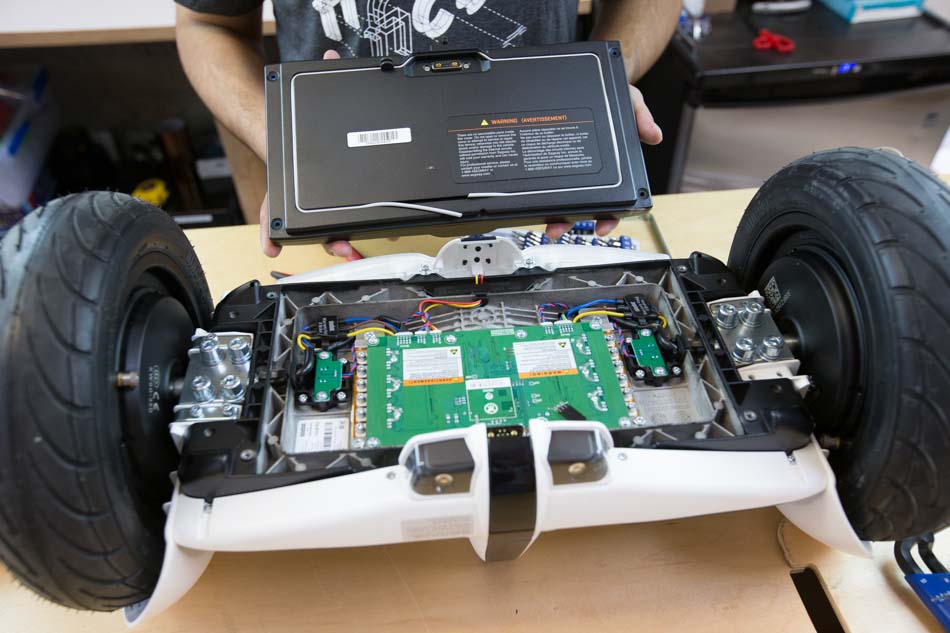
Some of the other improvements that instantly stuck out to me were:
- Better wire routing and management
- High-quality wire connectors for reliable connections and easy repairs (no super glue holding down connections here!)
- Enclosed and reliable Li-ion battery
- Lots of screws to hold down the PCBA and reduce vibration
It’s also worth mentioning that the hoverboard has such a bad reputation for catching fire/burning down homes that the UL, a global science safety organization, actually released a new certification specifically for self-balancing scooters (UL-2272). The Segway miniPRO is the first self-balancing scooter to be certified under this standard.
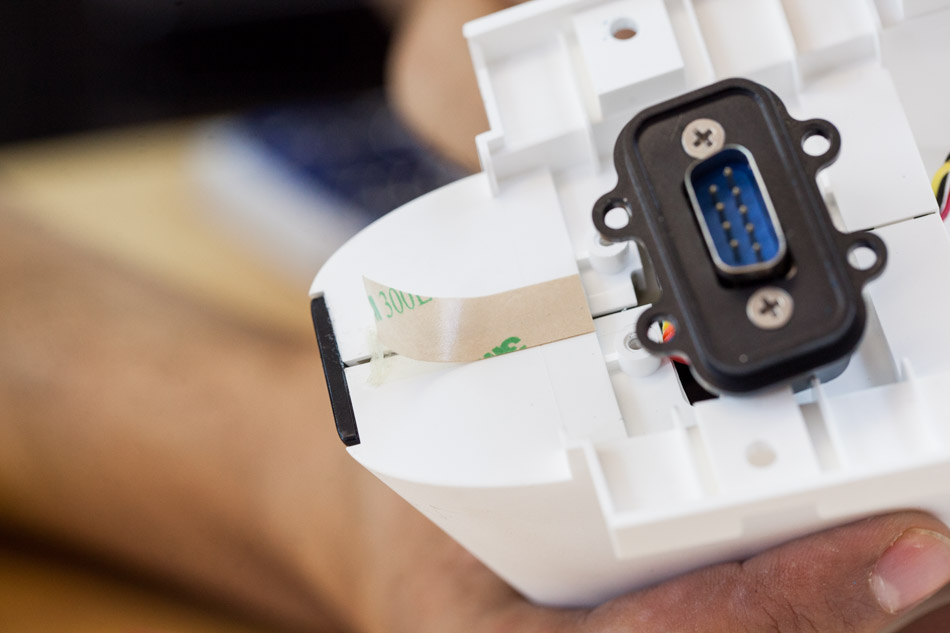
An interesting note is the Combination Sub-D connector for the battery and PCBA, which usually means that in addition to power being provided, there’s some communication between the two. This makes sense because the product comes with a handy app you can download that gives you info about the miniPRO. The app even lets you control the Segway with your fingers and drive it around.
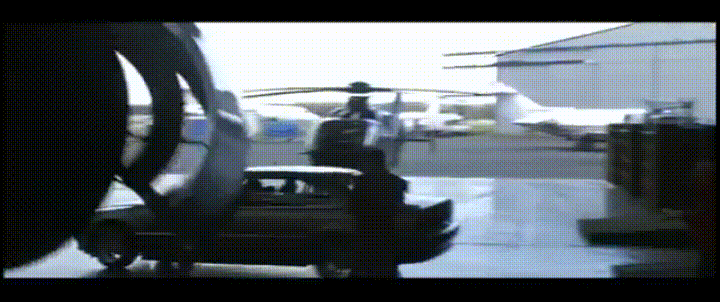
This Combination Sub-D connector is what makes the auto-sleep/wake-up, in-app battery performance details, overheating protection, and finger control features possible.
Wheels + Motor
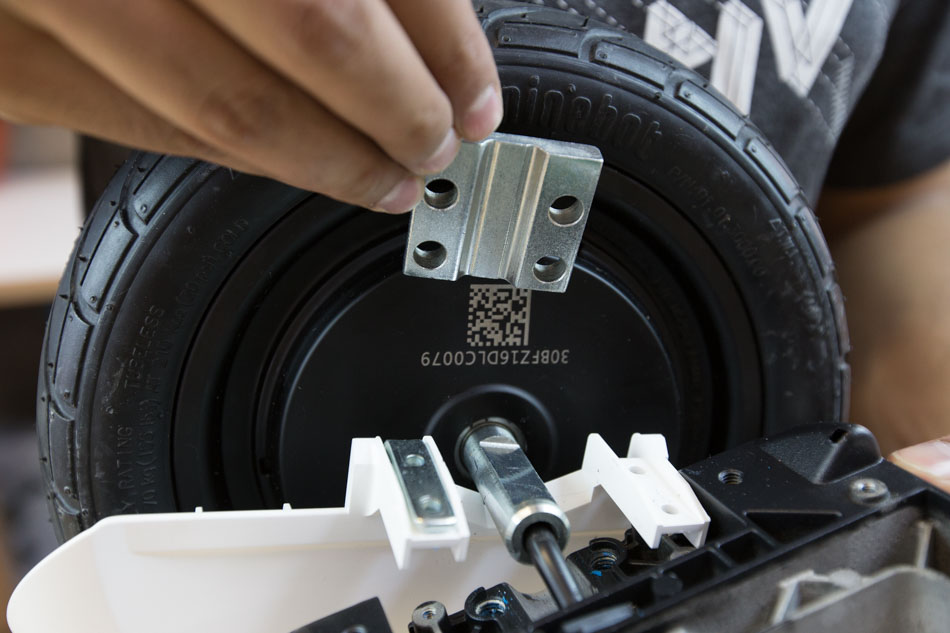
Much like the hoverboard, the motor is located inside the wheel, but a few minor changes in how the motor/wheel are enclosed have huge impacts.
- The wheel is absolutely sealed and impossible to get off without a proper tire removal tool. I pretty much ruined a screwdriver trying to pry off the wheel. This bodes well for its resistant to water and dirt as it takes on the elements.
- The plastic wheel well doesn’t cover the exterior facing side of the wheel, which means if you get a flat, you can repair it without having to take the entire product apart.
- The wheel wheels are held on by 2 L-brackets to the main body, as opposed to a single large body. Considering that in the case of an accident, the wheel wells are the most susceptible to damage, consumers have some ease of mind knowing they can replace just the damaged portion, instead of having to live with a damaged body.
Since we couldn’t get the wheel open, I’ll have to take a guess that like the hoverboard, there’s a Hall effect sensor on the motor that measures the chassis position with respect to the wheel and ramps the motor up or down.
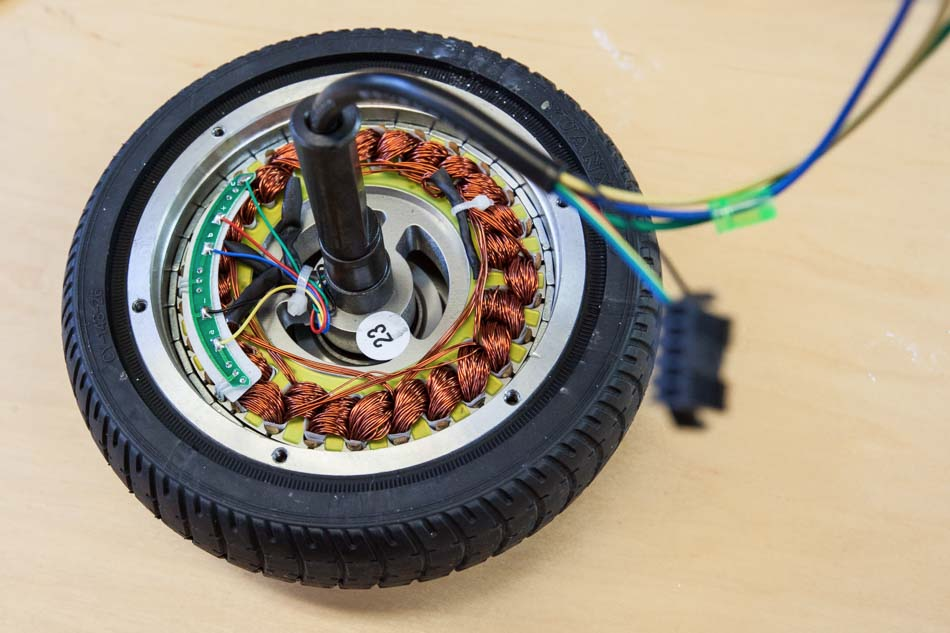
Chassis

The chassis on the Segway miniPRO was insanely light, which it makes sense, because it’s made of magnesium alloy—the best strength to weight ratio material available. Compare this to the hoverboard’s aluminum, which is light but sacrifices structural integrity.
When you cash out for a material that’s two to three times more expensive per
pound than aluminum, you want to show it off. The underside of the chassis is actually exposed, so it was painted black in specific areas.
Main Takeaways
The Segway miniPRO costs five times the price of the original hoverboard, and for good reason. The quality of materials used are much higher, the technology to control the speed and steering is superior, and the design is optimized for a product that going to be put to the test by the elements.