About the team
Industry: Consumer Electronics
Product: Ultimate Lightning McQueen robotic toy
Location: Boulder, CO
Why Fictiv
Customer challenges: Need access to a wider range of materials for prototyping
Favorite features: Rapid turn on 3D parts
Result: With test validation from high resolution parts, team was able to transition quickly into production
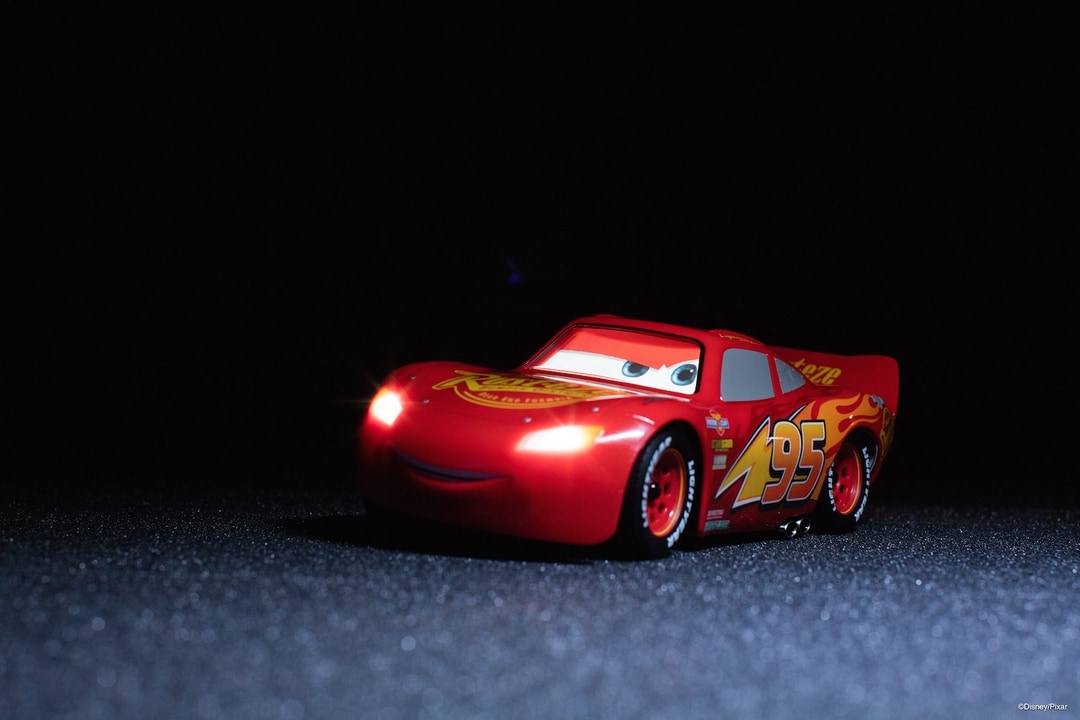
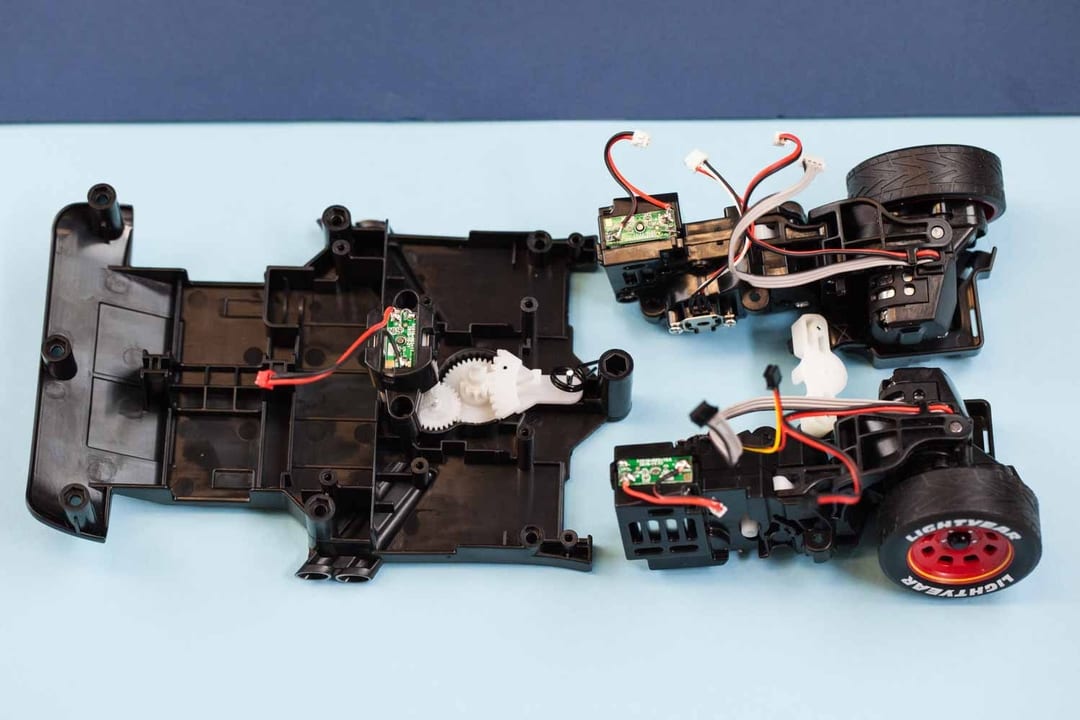
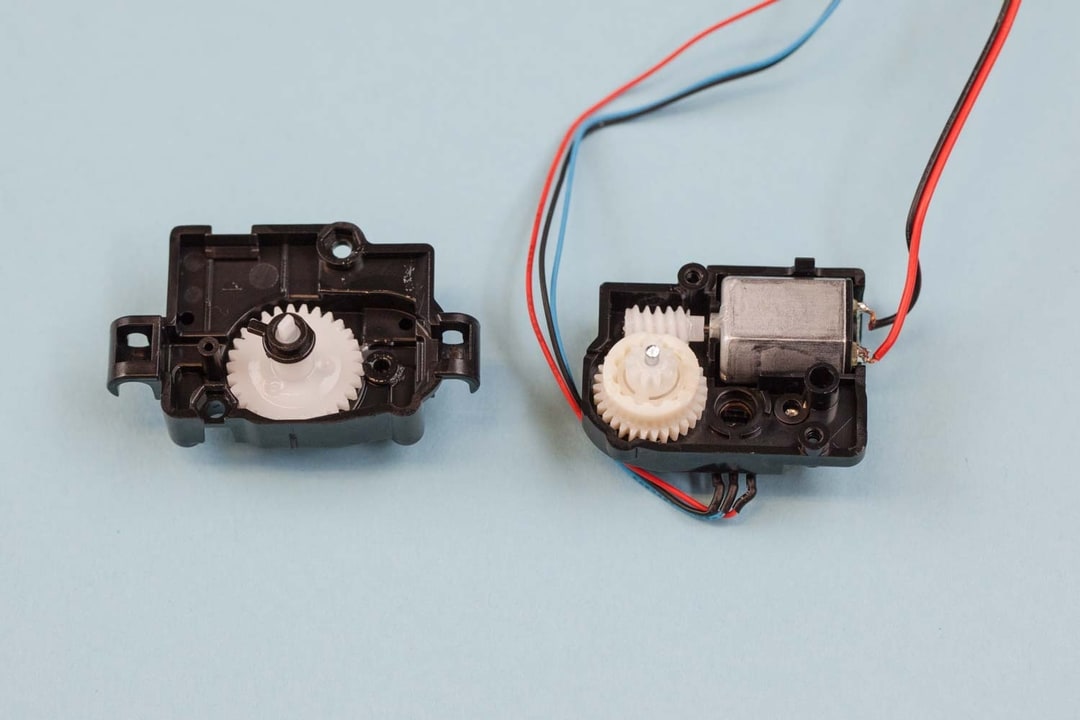
Since the launch of their BB-8 droid, Sphero has built a reputation as a company that delivers some of the most detailed, life-like robotic toys on the market. After winning hearts with the lovable BB-8, Sphero partnered with Disney to release a range of dynamic new toys including their app-enabled R2-D2 and BB-9E droids and the Ultimate Lightning McQueen race car.
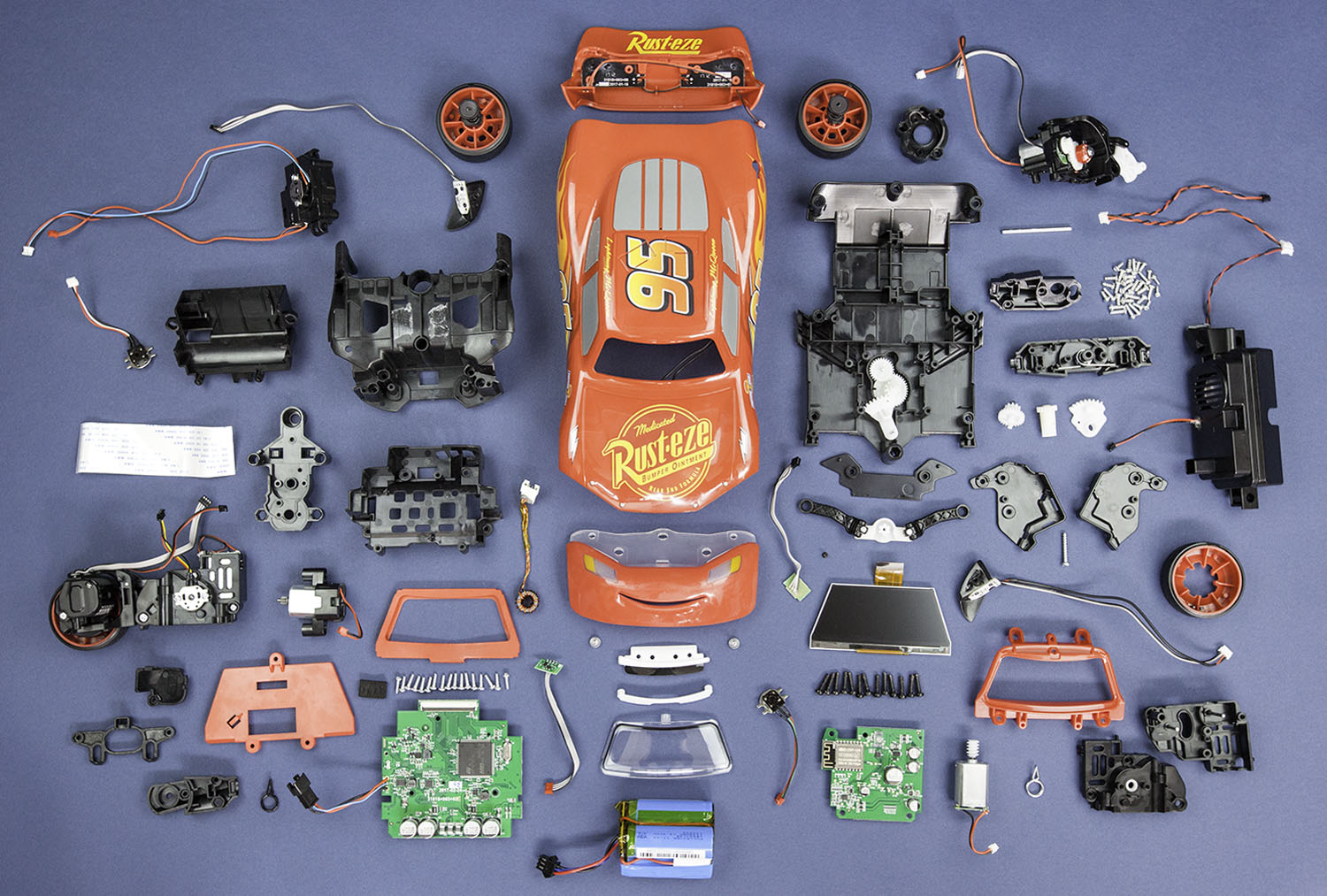
Fictiv and Sphero have partnered together on several projects—most recently, Sphero chose Fictiv’s Polyjet 3D Printing Service to expand their prototyping capabilities and develop Lightning McQueen’s small, complex gears.
Managing Complexity with Subsystem Prototypes
To build toward a proof-of-concept for Lightning McQueen, the Sphero team approached the prototyping process as a series of subsystems.
“Subsystem prototypes are really important,” said Doug Webster, Senior Mechanical Engineer at Sphero. “It was too complex to go from zero to a complete product, so each subsystem had its own prototyping effort.”
For the initial prototypes, the team started with FDM 3D printing to build a chassis to mount breadboards onto and attach a variety of sensors and microprocessors to control and steer the wheels.
“We were looking for a partner that could help us expand our material choices, and that’s where Fictiv stepped in.”
Partnering with Fictiv to Expand Prototyping Capabilities
As part of these initial subsystem prototypes, the Sphero team faced a challenge with the very small, complex gear teeth — part of Lightning McQueen’s driving and suspension gear boxes.
Smooth, emotive suspension and high performance driving characteristics were considered two of the highest priority subsystems for bringing this product to life; to give the robot smooth motion that could truly recreate the animator’s intent was absolutely critical. So prototyping these subsystems received many man-months of attention.
“We were having non-stop issues with gear teeth breaking and not coming in smooth,” said Webster. “We were developing these really tiny 0.3 mm gears in both the suspension and drive gear boxes to save space and with our internal 3D printers it just wasn’t going well.”
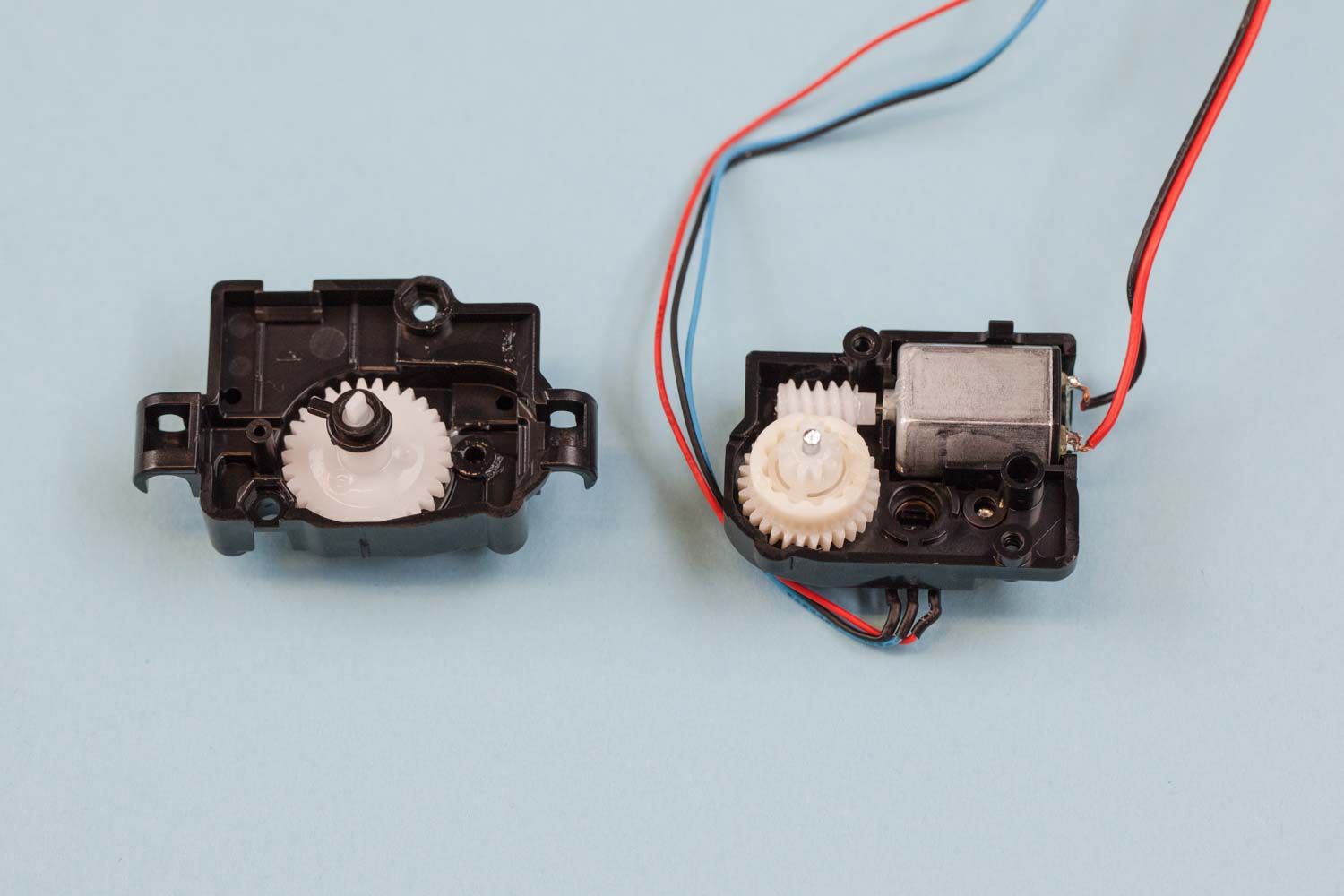
At this point, the team turned to Fictiv to expand their prototyping capabilities.
“We were looking for a partner that could help us expand our material choices, and that’s where Fictiv stepped in,” said Webster
“We were prototyping so fast so if we waited even two weeks for parts, the design would’ve changed. Fictiv was able to provide rapid turnaround.”
ABS-Like Material for Strong, Low-Friction Parts
Sphero chose Fictiv’s ABS-Like material for its increased strength and smooth surface to reduce gear friction.
“Our goal was to tune the motors and get resistances close to that of the future injection molded production gears, so we could dial in the power requirements,” said Webster. “Without low-friction, well-built gear teeth we couldn’t accurately estimate how much current the motors were going to draw, which was a necessary datapoint for the battery selection and for modelling drive train losses.”
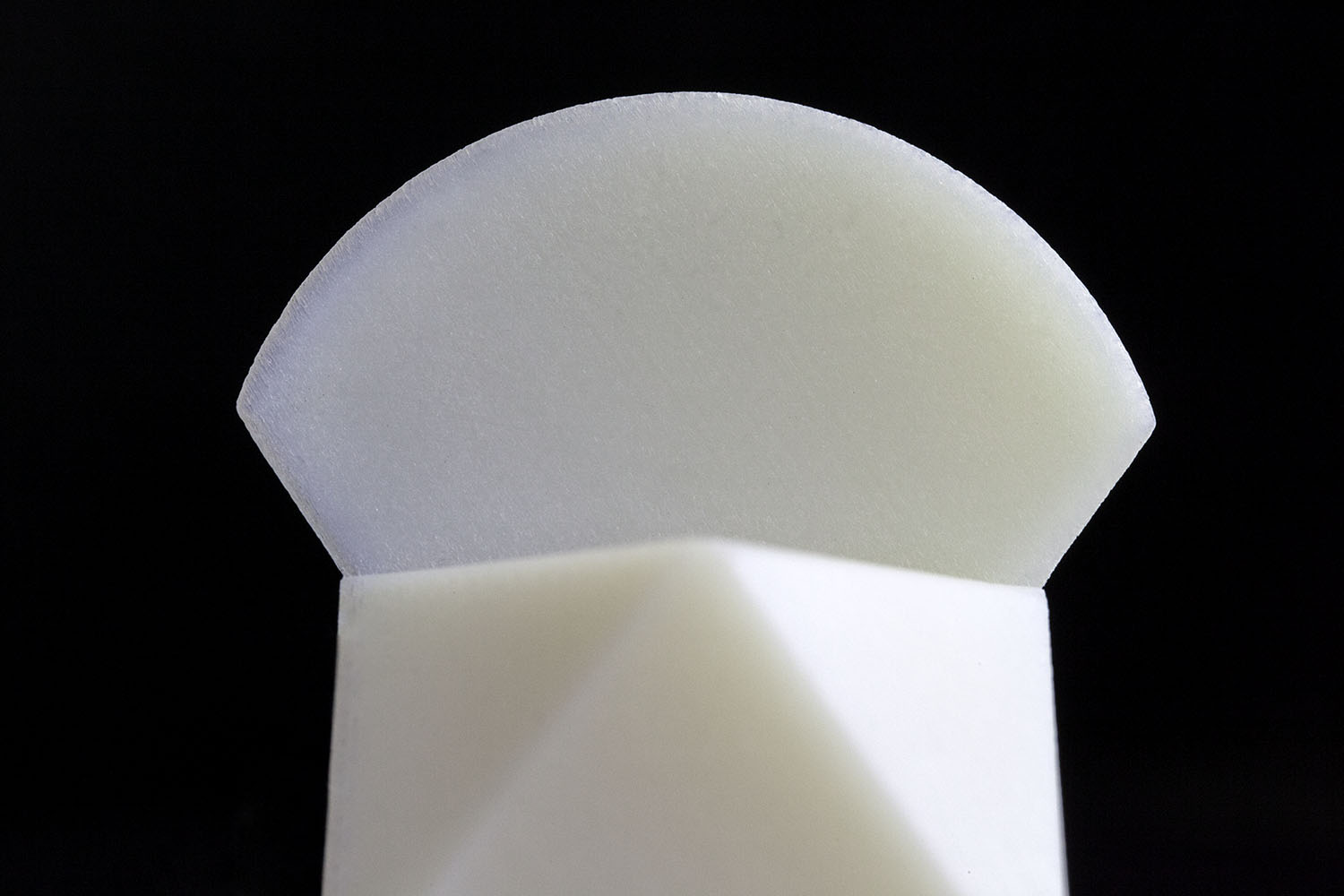
“Getting high-quality gears allowed us to transition from prototype-style design to something much more production-oriented, so we could prove out our ideas quickly,” said Webster. “We were prototyping so fast so if we waited even two weeks for parts, the design would’ve changed. Fictiv was able to provide rapid turnaround.”