Time to read: 8 min
CNC (Computer Numerical Control) machining is a modern manufacturing process that involves the use of computer software and machinery to create complex and precise parts and components. One of the most important factors that determine the quality and accuracy of CNC machining is the choice of material.
Selecting the right material for CNC machining can be a challenging task, especially for those who are new to the process. There are several factors to consider, including the material’s strength, durability, hardness, machinability, and cost.
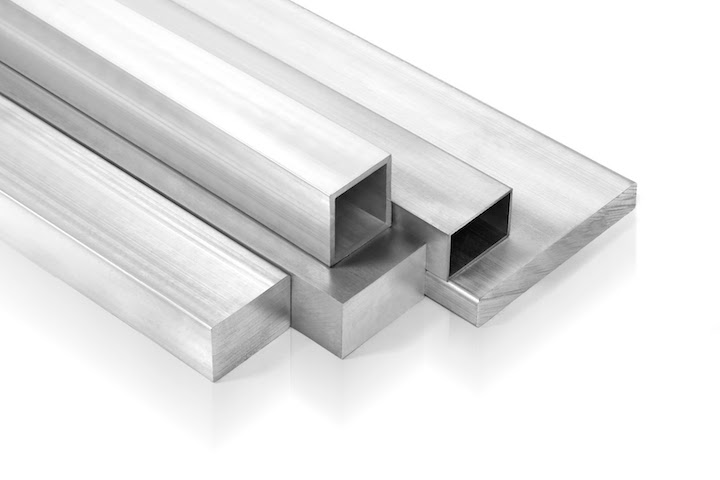
In this guide, we provide an overview of the most commonly used materials for CNC machining, including their properties and applications. We will also discuss the advantages and disadvantages of each material, as well as the factors to consider when selecting the best material for your specific project. By the end of this guide, you’ll have a better understanding of the different materials available for CNC machining and be able to make an informed decision when choosing the best material for your project.
Table of Contents
Commonly Utilized CNC Machining Materials
Consider Finishing Requirements
Consider Pricing, Availability, and Lead Time
Consider Statutory, Quality, and Regulatory Requirements
Consider Other Design Requirements
Consider How the Material Behaves During Machining
Commonly Utilized CNC Machining Materials
While your material selection is dependent on a multitude of factors, there are some tried & true material choices for CNC machining. These materials are utilized often because they provide a good combination of machinability, cost, availability, strength, and environmental resistance. Here are the most commonly chosen materials for CNC machining and the most prominent reasons they are chosen for CNC machining:
- Aluminum: lightweight, good strength-to-weight ratio, easy to machine
- Steel: strong and durable, though certain grades can be difficult to machine
- Stainless steel: corrosion-resistant and strong, but more difficult to machine than regular steel
- Brass: good machinability, good electrical conductivity
- Copper: good electrical conductivity, but can be difficult to machine
- Plastics: easy to machine, available in a variety of types and colors
- Titanium: strong and lightweight, but difficult to machine
Pro-Tip: Click the links above for quick information about each material, including CNC machining processes, tolerances, design recommendations, relative cost, material properties, and more!

The first and most important thing to consider when choosing a material for CNC machining is its properties. Both metals and plastics have the following set of relevant material properties:
- Electrical: electrical conductivity, permittivity
- Thermal: coefficient of thermal expansion, specific heat, thermal conductivity
- Mechanical: strength, hardness, ductility, malleability, elasticity, toughness, brittleness, stiffness
- Chemical: corrosion resistance, reactivity, flammability
- Optical: reflectivity, transparency, refractive index
- Acoustic: sound absorption/insulation, sound transmission
- Other Physical Properties: density, appearance, melting point, boiling point
Pro-Tip: Our resource center has a wealth of knowledge and insights to help you discern the difference between the most commonly used material properties, click on the links above or check out our full list of articles.
While that may appear to be an overwhelming list of properties to evaluate, it’s a good idea to sort the types of material properties based on priority for your specific application. For example, if you’re designing a heat exchanger, you will likely rank thermal properties pretty high and not need to consider optical or acoustic properties.
There are entire textbooks written on material selection (check out our adaptation of a textbook method) and chances are you’ve picked up some tips based on your experience. The good thing is that materials are pretty consistent, so once you have experience using certain materials, you’ll be much faster at narrowing down a list of potential candidates.
Here are some of the most important properties to consider when narrowing down your list of CNC material candidates, along with some of the materials that provide the best value for each:
- Surface Hardness: If your project requires a specific surface hardness, such as for wear resistance or impact resistance, then you need to choose a material that can achieve that hardness through machining or other processes.
- Conductivity: If your project requires electrical or thermal conductivity, copper and aluminum have good electrical conductivity, while steel and titanium have good thermal conductivity.
- Chemical Resistance: If your project requires chemical resistance, then you must choose a material that can withstand those chemicals, like stainless steel and titanium.
- Environmental Factors: Some applications require materials that can withstand extreme temperatures, corrosion, or other environmental factors. Consider the environmental factors that your project will encounter and choose a material that can withstand those conditions, like stainless steel and titanium.
- Weldability: If your project requires welding, then you will need to choose a material that can be welded — aluminum and steel are more commonly used for applications requiring welding than others.
- Machinability: Some materials, such as aluminum and brass, are easier to machine than others, such as titanium and stainless steel. Consider the machinability of the material when making your selection.
Consider Finishing Requirements
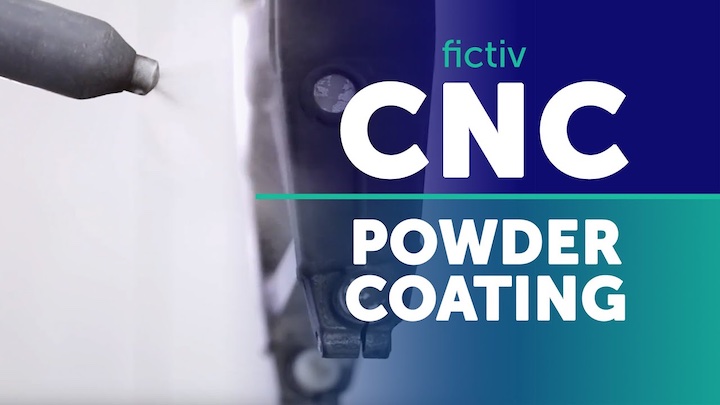
Finishing refers to the form and function of the surface of a part and can be a result of surface finishing, coating, plating, or painting the CNC machined parts. Coatings may be applied via an electrolytic process, by surface modification via a chemical reaction, or by spraying the parts such as with powder coating.
Surface finishing often means smoothing or roughening up a surface and can be accomplished with a variety of media, or processes such as grinding, honing, tumbling, polishing, blasting, lapping, and buffing. Plating is a typically electrochemical process whereby metals are deposited on the surface of a part to achieve a material property not inherent to the part itself, it can be electroless (electroless nickel) or done for aesthetic purposes (like jewelry).
Finishing may be an afterthought in your design process, but that isn’t the best practice. You should carefully review any specifications surrounding the finish requirements for your part because there may be material compatibility issues if you don’t. So, follow these general guidelines:
- Consider surface finish requirements. If surface finish is important for your project, then choose a material that can be machined to the required finish. Some materials, such as aluminum and plastics, can be machined to a very smooth finish. Others, such as cast iron, may require additional processes to achieve a smooth finish.
- Not all plating types are compatible with all base materials. For example, if your customer requires nickel plating, you don’t want to design your part from aluminum. However, stainless steel is a good choice for nickel plating, so use the specification for plating to help guide you to a compatible material.
Pro-Tip: Surface preparation is key to ensuring the integrity and adhesion of coatings, plating, and paint. Research the best preparation methods and if you don’t know where to start, there are many industry specifications that can point you in the right direction.
Consider Pricing, Availability, and Lead Time
- Raw Material Cost: Cost is always a factor when choosing a material. Some materials, such as high-end aerospace alloys, can be very expensive, while others, such as plastics, can be much more affordable. So, consider the cost of the material and whether it fits within your budget.
- Machining Cost: The cost of machining the material must also be considered. Some materials require more time and effort to machine than others, which impacts the overall machining cost.
- Availability: Availability is another important factor to consider when choosing a material. Some materials are difficult to source or require longer lead times, which can delay your project. Consider the availability of the material and whether it can be obtained within your required timeframe.
- Lead Time: Finally, the lead time required for your project can also impact your material selection. Some materials may have longer lead times than others, which can impact your overall project timeline.
Consider Statutory, Quality, and Regulatory Requirements
Ensuring that you meet statutory, quality, and regulatory requirements is often the job of a design engineer, and meeting those requirements starts with choosing the right materials. Here is a graphic to help simplify the hierarchy of competing requirements:
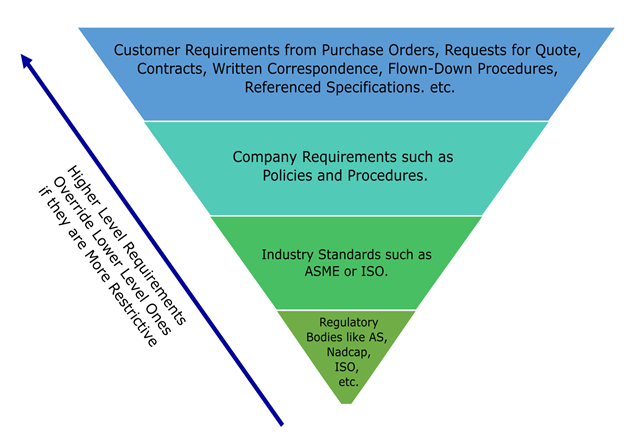
Use these tips to simplify picking the best material for regulatory, statutory, customer, and quality requirements:
- If your project requires specific certifications, such as aerospace or medical certifications, then you must choose a material that meets those requirements — so check the certification requirements before making a selection. Examples of regulatory requirements include RoHS, REACH, and Conflict Minerals Regulation.
These requirements can be complex, so it’s important to thoroughly understand and research them before selecting a material — and check that your material type can be tested for the certification process that it must undergo to be certified. Not all materials are compatible with all testing procedures.
- The sustainability of your materials should also be considered. Some materials, such as aluminum and steel, are easily recyclable, while others, such as plastics, are more difficult to recycle or not recyclable at all. Your sustainability requirements may include checking the carbon emissions for your material during procurement and/or raw material refining.
Other Design Requirements to Consider
- Tolerances: The tolerances required for your project can also impact your material selection. Some materials may be more difficult to hold tight tolerances on than others, which can impact the overall quality of your finished parts.
- Size and Shape of Parts: The size and shape of your parts can also influence your material selection. Some materials may be better suited for machining large or complex parts, while others may be better suited for small or simple parts.
- Quantity of Parts: The number of parts needed for your project can also impact your material selection. Some materials may be more cost effective for larger quantities, while others are better suited for smaller quantities.
- Part Complexity: The complexity of your parts can also impact your material selection. Some materials are better suited for machining complex geometries, while others may be better suited for simpler parts.
Consider How the Material Behaves During Machining

It’s also advisable to look at how the material behaves during machining using the following guidelines:
- Machining Process: The type of machining process you plan to use can also impact your material selection because some materials are better suited for certain machining processes, such as milling or turning, than others.
- Tool Wear: The material you choose impacts the wear on your machining tools. Some materials, such as high-temperature alloys, can cause excessive tool wear and may require specialized tooling to machine.
Fictiv – Complex Parts at Ridiculous Speeds
No matter how complex your designs, or the materials you need to bring them to life, Fictiv can produce the custom, CNC-machined tight tolerance parts you need. Our manufacturing experts can help you select the right material for your application, and our online platform simplifies custom part sourcing with intelligent, streamlined, automated workflows.
Fictiv is your operating system for custom manufacturing that makes part procurement simpler, easier, and more efficient. We deliver high quality mechanical components, fast.
Create an account and upload your part to see what our instant online CNC quote process, design for manufacturability feedback, and intelligent platform can do for you.