Time to read: 5 min
There’s an old saying in business that “Nothing happens until someone sells something”. We don’t know for sure who said it, but we certainly understand its truth. Similarly, nothing in injection molding gets produced until melted thermoplastic enters the mold cavity. Yes, there are plenty of steps before this crucial one, but plastic must flow into the cavity in order to produce molded parts. If there’s a problem with the location, type, or size of the gate through which this material flows, part quality suffers.
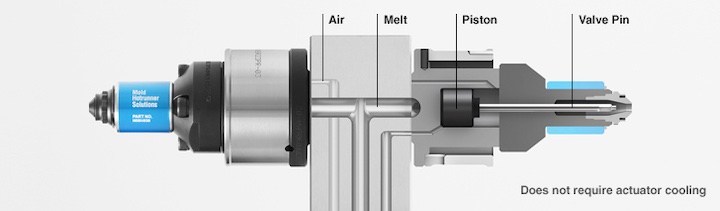
Hot runner system with valve gate. Source: Mold Hotrunner Solutions Inc.
So what’s a gate? As explained in What You Need to Know About Injection Molding Gates, plastic injection molding forces molten plastic toward and through a gate, an opening that lets material enter the mold cavity. Sprues and runners allow the material to flow, but the gate controls access to where molding happens.There are two basic classifications of gates: cold runner and hot runner.
- Cold runner gates are the most common. Molten material is introduced into the injection mold through a sprue and a system of runners that are not heated (i.e., cold). With cold running gates, the plastic that’s in the sprue and runner are ejected with the part, and this plastic is then scrapped or reground.
- With a hot runner system, the molten plastic travels through a heated cylinder as it moves through the mold and delivers this hot material directly to the gate of the part. This produces less waste and provides greater control over temperature and pressure as the material enters the mold cavity.
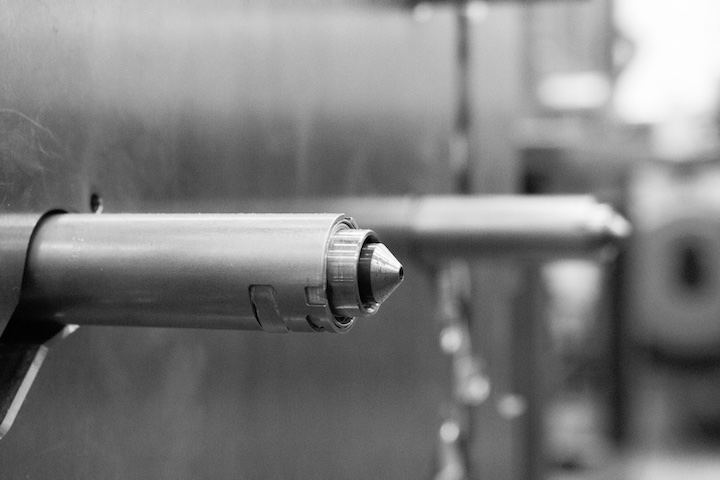
Exposed valve gates
Valve Gating in Hot Runner Systems
There are two options for hot runner systems: standard and valve gate.
- In a standard hot runner system, plastic material flows directly from a heated cylinder into the gate and mold. Because there’s no shutoff mechanism, a thin string of plastic attaches to the gate location on the part. This material is small and easy to remove, but it represents material loss and, more importantly, control loss.
- With a valve gate system, the hot tip has a pin in the mechanism’s center that can be opened and closed during the molding cycle. This shutoff mechanism provides greater control during injection molding and a complete shutoff of material after injection for less waste.
Valve Gating Advantages
As with any technology, there are reasons to use it and times when it’s not required. There are three main reasons to use a valve gate in your next injection molding project: less waste, more control, and fewer defects.
Less Waste
Valve gates reduce material waste because the valve is opened and closed during the injection cycle — cold runners have a large sprue and runner system, and standard hot drop runners lack a valve shutoff.
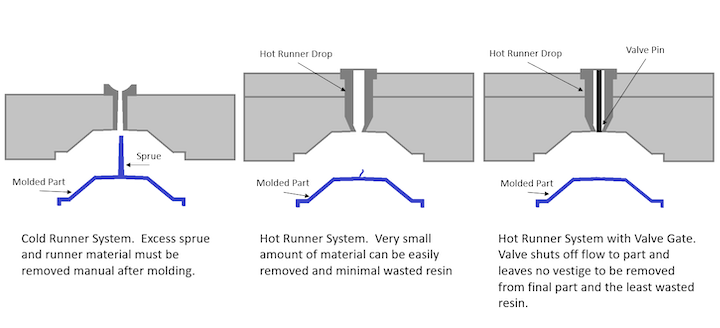
Cold runner, hot runner, and hot runner with valve gate.
Reducing material waste is a good way to reduce part costs. If your project calls for making tens of thousands of parts, each small increment of material savings add up quickly. For production programs with high material usage, valve gates will reduce the amount of material that is wasted and, therefore, the amount you need to pay for material.
More Control
Another advantage to using valve gating is the amount of control it gives you over the injection molding process. Because you have control over exactly when and how much material enters the tool, you have tighter control of the parameters that go into making a quality part. Also, heating the material in the cylinder gives you better control of the material’s temperature as it enters the mold.
Fewer Defects
With these tighter controls of material flow and heat, you gain important advantages in controlling part blemishes during the injection molding process. Usually, a part is packed and the plastic is “frozen” in the sprue to keep material from flowing back out of the cavity. With a valve gate, however, the valve holds the material in place. This provides more consistent control and leads to parts with fewer pressure-related issues like sinking.
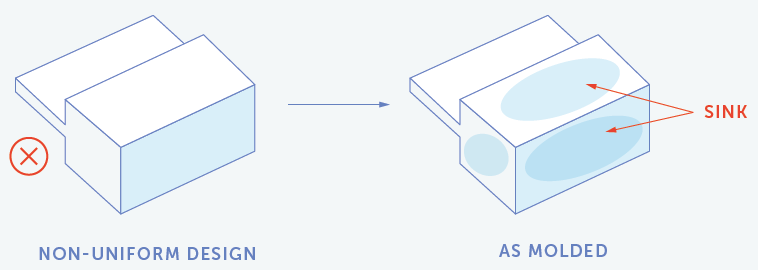
Sink marks are a common type of injection molding defect
With tighter heat controls, you can keep the material at the proper temperature to make sure the plastic keeps flowing and fills the mold cavity completely. Valve gates also make weld lines less of an issue and give greater control to correct them if they do occur. These injection molding defects happen when two cool flow-fronts come back together again after separating.
In larger and more complex parts that have multiple gates along a long distance, the timing of the valves can be set so that as the flow-front from one valve reaches the second gate, the second valve opens to allow material to begin flowing, thus reducing the weld of one material front to the other. This is referred to as sequential valve gating because the valves are opened and closed in sequence to produce the best part. This is not possible with a standard hot drop or a cold runner mold.
Valve Gating Disadvantages
However, valve gates aren’t recommended for every project. There are reasons to use them, but plenty of times when they are not required. Using valve gates when they’re not necessary adds more cost to the project than actually benefits the part.
Up-Front Costs
For projects with simpler and smaller parts, the cost of adding a valve gate can be substantial. When you look at the total number of parts that are produced from a mold, valve gates are best for large parts with lots of material scrap or large quantities of parts where wasted material adds up over thousands and thousands of parts. A single valve gate system costs thousands of dollars, which significantly increases the costs of the molds and isn’t cost-effective for many applications.
Maintenance and Repairs
Valve gates are also more complicated and costly in terms of repair and maintenance. They have many moving parts and heating elements that can break and, therefore, need to be replaced. Maintenance takes time and tools may have to be sent out to be repaired which costs you time and money. As with anything mechanical, the greater the complexity, the more expensive the repair.
Close the Valve and Start the Process
There are so many decisions to make in plastic injection molding, and everything impacts final part quality and performance. Gating is one of the keys to making sure that you get a good part for your next project, so you want an expert injection molding partner to help you get it right.Fictiv is your custom operating system for custom mechanical parts, and our injection molding experts have years of experience working with every type of valve gate. We’re happy to work with you to figure out which gating, tooling, material, and approach will work best for your next project. So, create a free Fictiv account and upload your part design today to find out what our injection molding service can do for you!