Time to read: 5 min
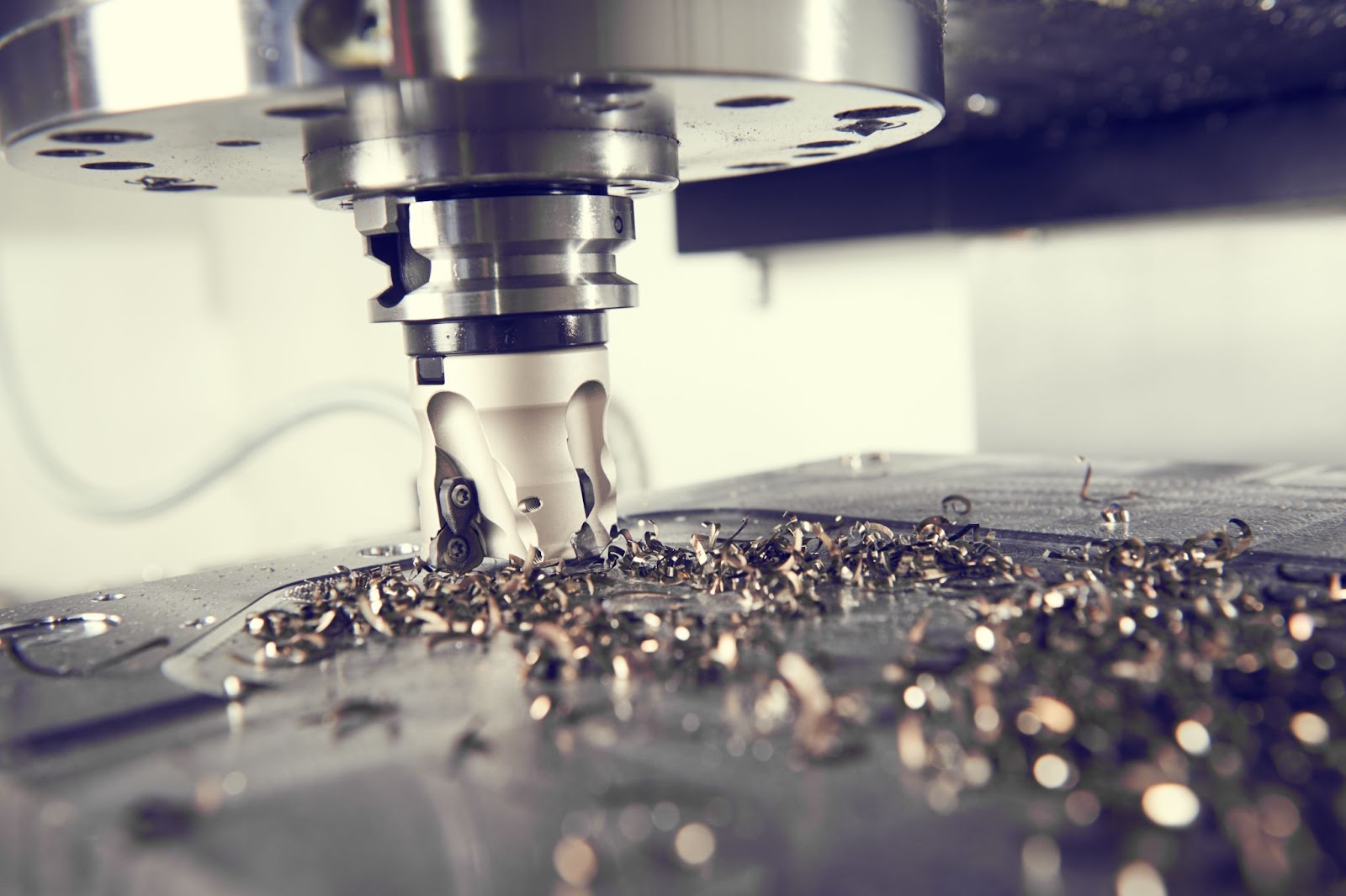
When choosing a metal for your application, there are countless options, and each has pros and cons. Material strength, ductility, toughness, fatigue resistance, hardness, and conductivity are key properties that must be considered when choosing your metal for CNC machining. And depending on the metal, your machining methods and costs can greatly differ due to their unique properties. Below we’ll go over some basic characteristics of commonly used metals and discuss choices to be made when CNC machining them.
Aluminum
Aluminum is one of the most commonly used metals due to its low density (weight) and attractive material properties that include high strength, high ductility, and high corrosion resistance. Aluminum is also highly machinable, depending upon the heat treatments used on the material.
Because of its versatility, there are no encompassing typical uses for aluminum — it’s used by nearly every industry for a range of applications. To give you some context, here are some some common industry-specific examples:
- Automotive: Used heavily in the automotive industry for frames, engines and other component parts due to the high strength-to-weight ratio.
- Consumer Products: Used as material for low-cost frames in bicycles as a compromise between high weight/low-cost steel and low weight/high-cost carbon fiber.
- Construction: Used for building components like windows and doors when weight and corrosion resistance is critical for the application.
- Aerospace: Used extensively for framework, wings, structures, fuel tanks, and fuselages, again thanks to its high strength-to-weight ratio.
Steel
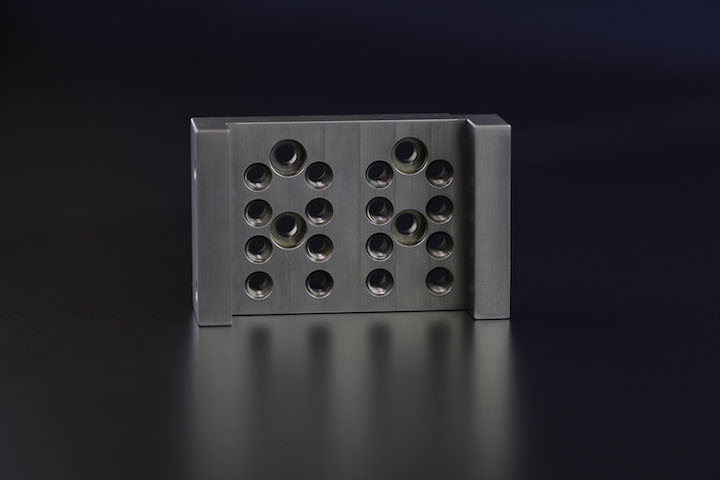
Steel is also among the most commonly used materials due to its relatively low cost and useful material properties. There are a variety of steels to choose from that are made using different alloying elements to achieve a range of material properties. The three most common types of steels are stainless, carbon, and mild steel:
- Stainless Steel: Widely used in all industries due to its high strength and high corrosion resistance that comes from its increased chromium and nickel content. Stainless steel also exhibits high formability and machinability and is used for a variety of consumer products ranging from utensils to appliances.
- Carbon Steel: These steels are marked by high carbon content which makes the steel harder and stronger than other steels. However, this high strength is a trade-off, because the higher carbon content lowers the material’s ductility and makes it more brittle than stainless steel. Carbon steel is also more expensive and is more difficult to machine than low carbon, or mild steel. High-carbon steel is often used for high quality knives since the strength allows for very high edge retention.
- Low Carbon/Mild Steel: These steels are the most common forms of steel due to the low cost but high strength that makes it a versatile material used in many applications.
Pro-Tip: For a detailed look at CNC machining steel alloys, check out our articles: “The Many Types of Steel, and What You Should Know about CNC Machining Them” and “Stainless Steel: Why Do We Call it Stainless?”
Copper and Brass
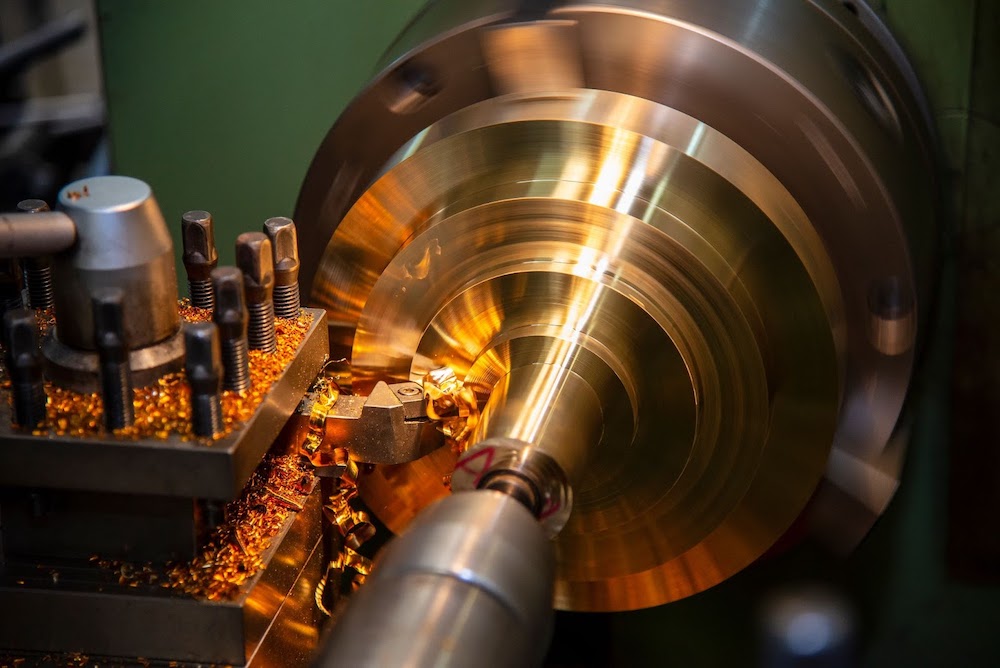
Copper, unlike steel and aluminum, is not typically used in structural applications because of its low strength and high ductility. Basically, copper is a “soft and squishy” metal, but what it lacks in strength, it makes up for with high thermal and electrical conductivity — it’s typically used for wires and cables.
When copper is mixed with zinc, the resulting alloy is brass. Brass not only retains much of copper’s thermal and electrical conductivity, but can also be alloyed with other elements to achieve higher strength, higher corrosion resistance, and lower friction. Common uses for brass are locks, gears, bearings, sleeves, and plumbing fixtures. Brass is also used for decorative items due to its shiny, gold finish and high formability and machinability which allows for intricate details.
Titanium
Titanium is one of the top-tier materials in the world of metals. Titanium is highly corrosion resistant and has an incredible strength-to-weight ratio. Titanium can be as strong as steel, but is far lighter, and is roughly 50-60% stronger than aluminum for the same weight. Titanium takes special effort to machine, though it is not as hard as some forms of steel. Titanium is also much harder to fabricate because it’s easily contaminated by oxygen, nitrogen, and hydrogen when heated — a condition known as embrittlement, which significantly compromises the integrity of the material’s structure.
Due to its high strength-to-weight ratio, titanium is extensively used in the aerospace industry for structural parts and in the marine industry due to its high corrosion resistance. So, why not use titanium to replace everything? Titanium is expensive due to high raw material and fabrication costs associated with producing finished material. This makes it cost-prohibitive for most high-volume applications.
Machining Factors
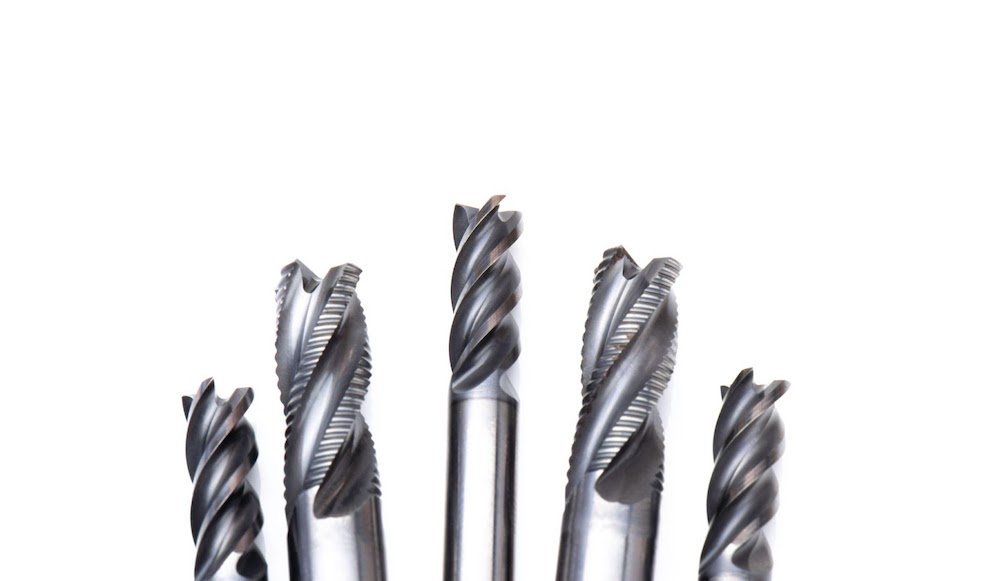
Machining rates (also known as feeds and speeds) ultimately control your material removal rate no matter which kind of metal you’re using. For example, with aluminum, its high machineability means you can remove a lot of material in one pass. But, aluminum’s low melting point means you must manage the heat generated during machining or the material will end up sticking to the tool. Depending on the grade of aluminum, your max feed and speed will change, as different grades and heat treatments can range from having a “gummy” material to extremely hard.
Pro-tip: As a quick reference, check out this guide for some standard feeds and speeds: “Feeds and Speeds: The Definitive Guide.”
Because various types of metals have a wide range of machinability, different cutting tool shapes and different cutting tool materials should be used depending upon your application. For example, if the material requires significant chip removal (or chip clearance), the number of flutes in a tooling bit should be increased or decreased to optimize your process. If maintaining a sharp edge on your cutter is paramount, you can prioritize hardness over toughness by using carbide tooling instead of high-speed steel tooling.
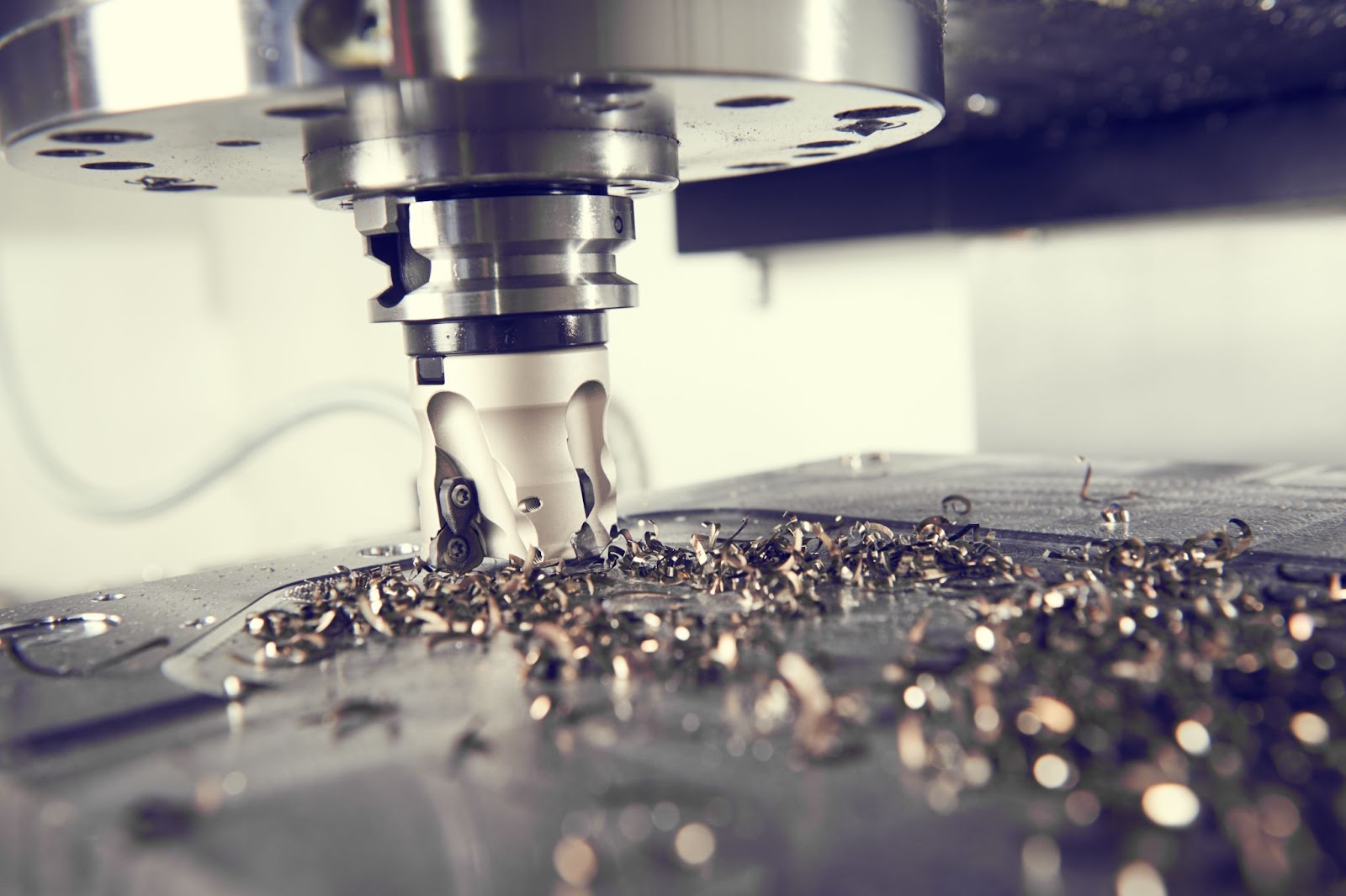
And tool material isn’t the only consideration. Tools can have a variety of finishes such as aluminum titanium nitride or zirconium nitride coatings to help improve friction and heat management while cutting. To make it even more complicated, the helix angle is also critical — changing this angle directly affects the heat build-up during machining and therefore affects your optimal feeds and speeds and resulting surface finishes.
Fortunately, there are mountains of information for finding the correct tool for every job, and there are always more material and tool designs in development. Plus, there are businesses that focus specifically on finding the right tool for your job. So, ask around for expert advice instead of trying to reinvent the wheel for your particular project — somebody has probably already faced and solved your issues.
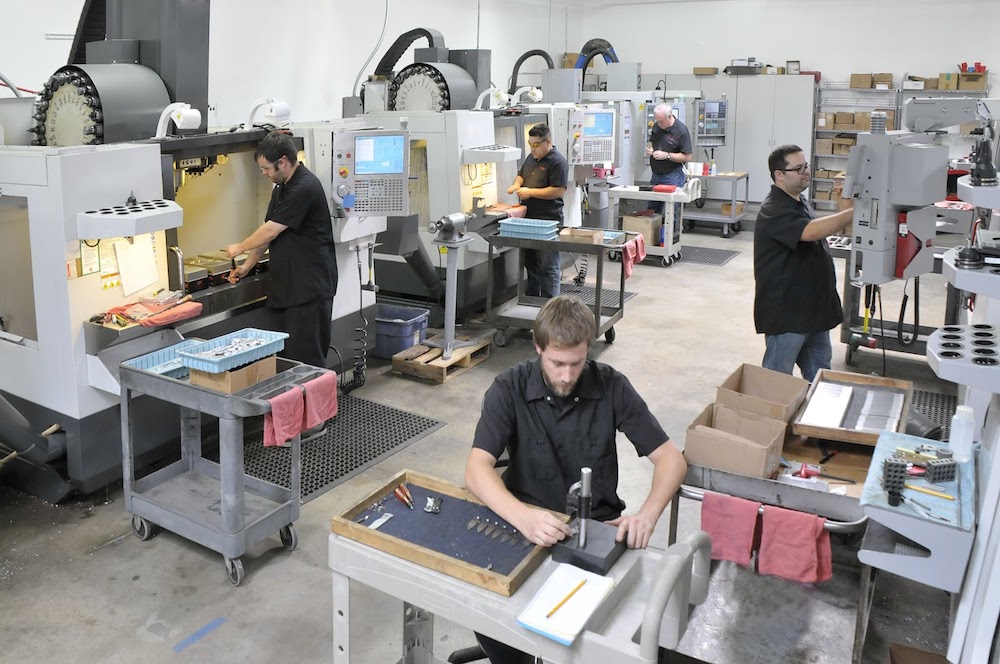
Conclusion
Now you have a handle on some common materials and how the properties of those materials affect the CNC machining process. Keep in mind that we discussed broad characteristics of these metals, and depending on the grade and chemical composition, the metallurgical properties of the metals you used can vary dramatically. And remember, the industry is constantly learning new ways to create better alloys, materials, and machining tools, so it’s a good idea to talk to an expert before making your material selection. Fictiv is your operating system for custom manufacturing that makes part procurement faster, easier, and more efficient. We’re experts at producing custom mechanical parts with intelligent, streamlined, automated workflows from a variety of materials. Fictiv offers high-quality, precision CNC machining services with instant quotes, DFM, and turnaround times as fast as 2 days!