Time to read: 6 min
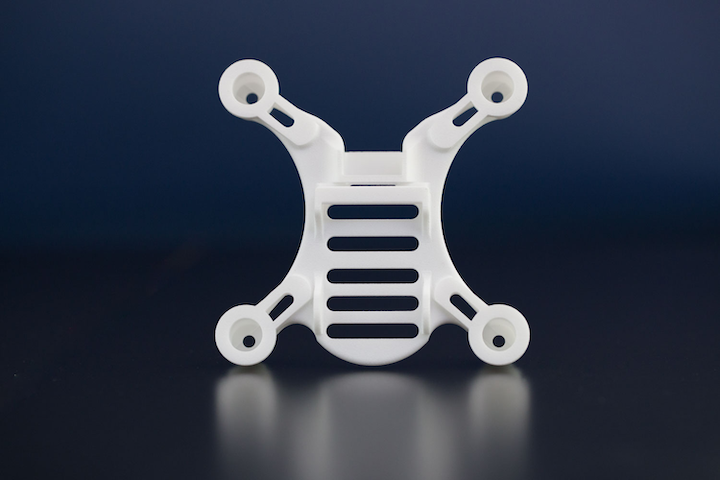
Many additive manufacturing processes offer low cost per part, high dimensional tolerances, and fast cycle times, but selective laser sintering (SLS) is one of the best options. SLS’s speed, resolution, and laser accuracy combined with advances in the raw materials allows for rapid iteration and high-quality finished parts. The self-supporting nature of the process enables advanced geometries that are incredibly difficult to manufacture using non-additive manufacturing methods.
Originally developed in the mid-1980s by Dr. Joe Beaman and Dr. Carl Deckard at the University of Texas, SLS has come a long way since then. Now, it’s used to build durable prototypes as well as end-use products, and is a crucial tool for building parts with complex geometries for functional applications. Read on to learn how SLS printing works, about SLS 3D printer machine components, the common materials for SLS 3D printing, and the benefits of SLS 3D printing.
SLS Printing: The Basics
Selective laser sintering is a powder-based additive manufacturing technology that uses a high-power laser to sinter small particles into a solid structure based on a 3D model. The 3D printing occurs in a build chamber where the laser sketches the part into the bed of powder one layer at a time. As the laser shines on the layer of powder, energy from the laser sinters the powder causing the small particles to fuse together into a solid piece.
As a quick refresher: sintering is the process whereby powder is formed into a homogenous solid by heating it to a temperature just below its melting point. When a layer is finished, the build chamber lowers by one layer and fresh powder is added so the process can repeat.
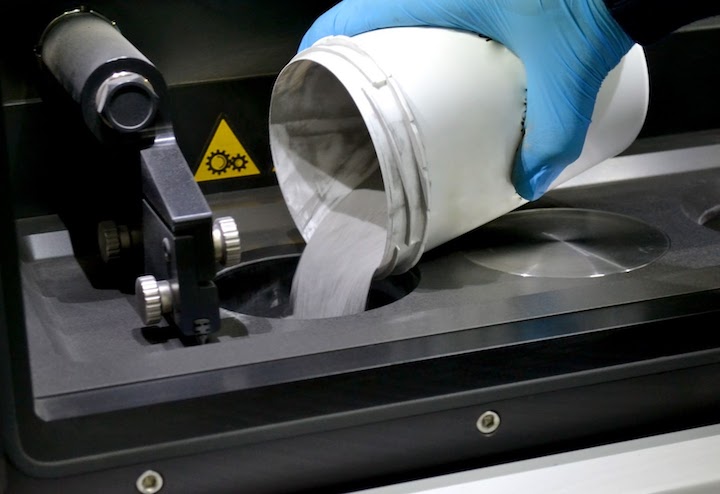
SLS 3D Printing: A Look Inside the Process
As a self-supported additive manufacturing process, SLS has capabilities and precision other processes lack. While other 3D printing processes require either support materials or 3D printed supports to be added to the design, SLS allows parts to be printed as-is. This unique capability saves time and reduces the skill needed to prepare a print for an SLS machine.
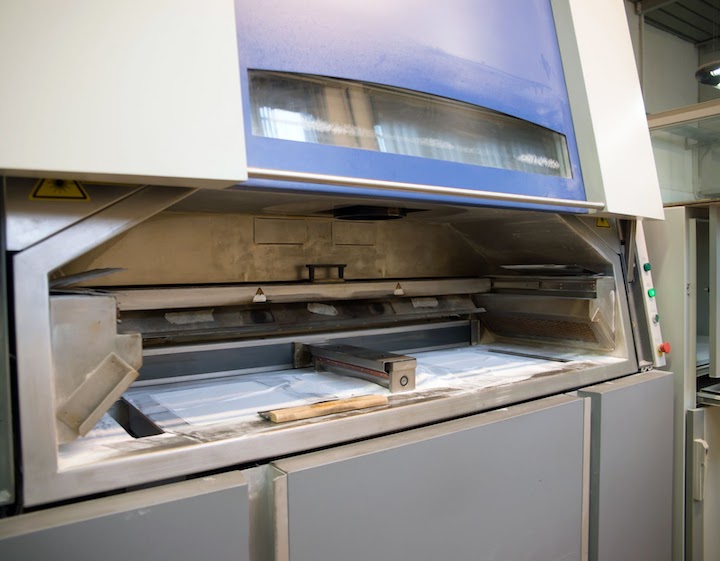
The SLS 3D printing process is broken into three distinct steps: printing, cooling, and post-processing.
Printing
The SLS printing process is unique when compared to other additive manufacturing processes like fused deposition modeling (FDM). First, the raw powder is preheated (so the laser requires less energy) and deposited in a thin layer on top of a platform in the build chamber.
The laser then scans or shoots the slice of the powder in the shape of the model for that cross-section, sintering material as it goes. The remaining unfused powder acts as a support layer as the build chamber lowers by one layer and more material is added. The process repeats itself until the build is complete.
Cooling
The finished printed part is then suspended within a bed of hot powder. To reduce defects and increase dimensional stability, the build chamber must cool down evenly, which can take up to half of the total build time. This cooling should be gradual, and cooling of the build chamber reduces mechanical defects and helps reduce warping.
Post-processing
Once cool, the excess powder is removed and recycled. To recover parts from the build chamber, the parts are sifted manually to remove excess powder, then cleaned with compressed air to prepare them for final processing.
SLS parts are known for the unique surface finish caused by the sintering process. For exceptional material properties and finish quality the part may be post-processed — sandblasting and media tumbling are used to improve the surface finish. Check out our Ultimate Guide to Finishing 3D Printed Parts for more details on finishing 3D printed parts.
SLS Machine Components
The key components of a selective laser sintering machine consist of the following:
- Laser
- Build chamber
- Scanning mirror
- Powder delivery system
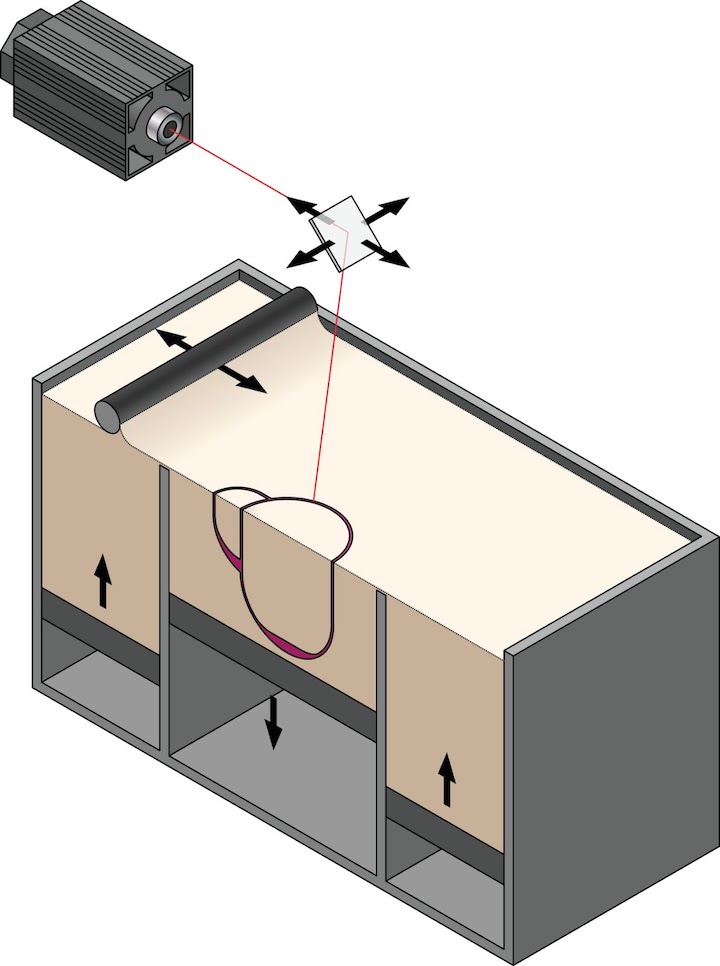
To reduce the power needed for the laser to sinter the powder, raw powder is preheated to approximately 85% of its melting temperature before being spread over the active build area. As the printer prepares to sinter a new layer, the build chamber is lowered by one layer as the powder supply chamber is raised.
A spreader then evenly distributes the warm powder as a fresh layer over the build chamber. The laser then fires and the printer makes small adjustments as needed to direct the laser at the desired areas — when the laser contacts the preheated powder the particles are fused together.
Once the layer has been fully sintered according to the design, the process begins again. Because the build chamber is fully self-supporting, large overhangs, thin walls, and sharp parts are all possible. The large volume of the build chamber and the self-supporting nature of the SLS process means parts are often nested throughout the build chamber to increase efficiency.
Materials Compatible with SLS
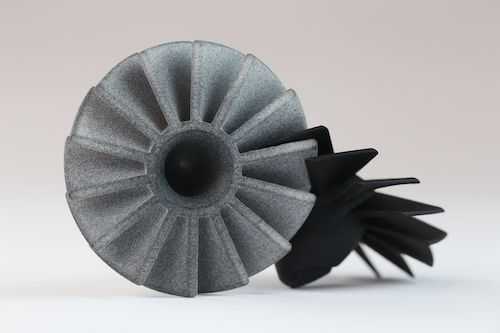
Nylon has high chemical resistance, is strong yet lightweight, has good mechanical properties, and is by far the most often used material with SLS. Variations of nylon powders are available and include carbon fiber-reinforced nylon composites. Many of these blends, such as MJF Nylon, or other composites create extremely strong and durable parts with unique material characteristics.
Other, less common materials compatible with SLS include elastomeric thermoplastics and castable polystyrene. Elastomeric thermoplastics are often used in prototyping due to their flexibility and resistance to tearing. Castable Polystyrene is great for prototype metal castings and is also used for low to medium-production runs. As previously mentioned, when metal powders are used in a similar manufacturing process, the technique is called direct metal laser sintering (DMLS).
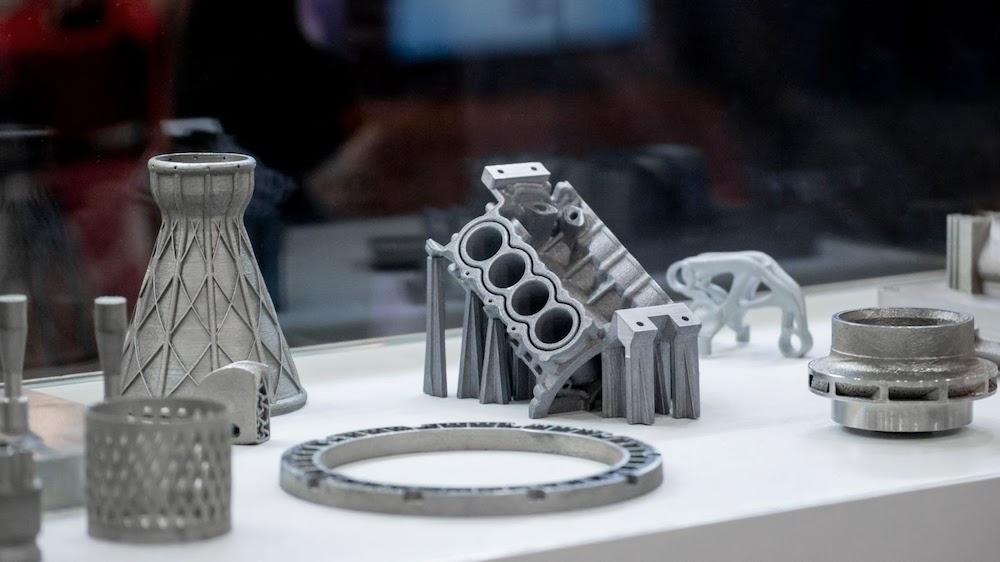
Advantages of Selective Laser Sintering
One of the biggest advantages of SLS is the excellent support naturally provided by the process due to unfused powder. By having the print be naturally self-supporting, complex geometries are possible — even those with interior features — and undercuts, thin walls, and negative features are all possible as well.
Pro-Tip: If you are interested in learning more about how to design parts with complex geometries/tight tolerances, check out Our Complete Guide to Designing Tight Tolerance Parts.
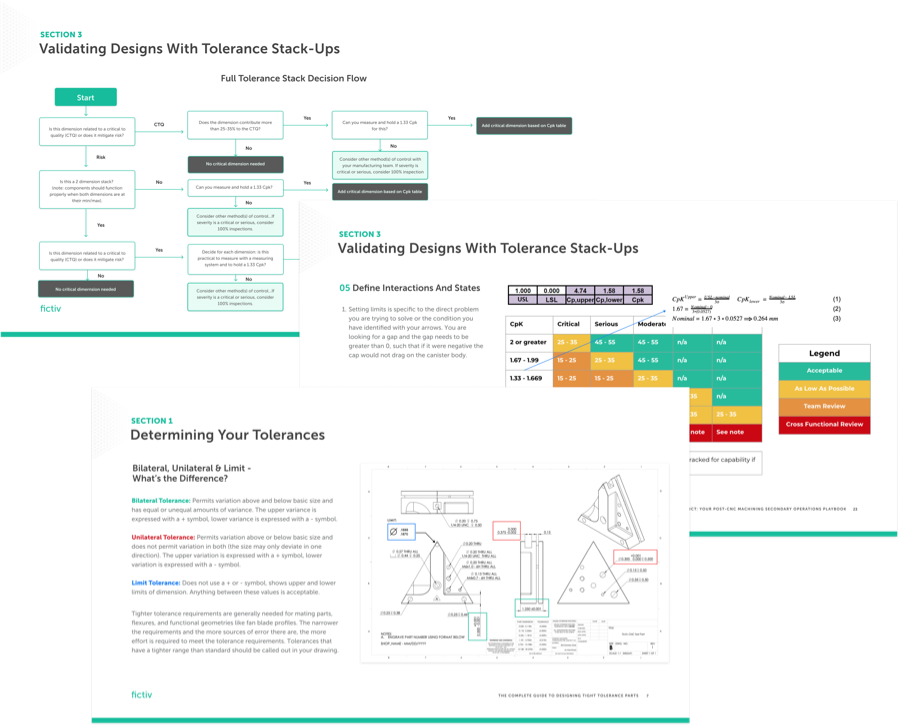
In addition to expanded printing capabilities, finished part strength is exceptional with the selective laser sintering process. Finished parts from SLS often rival injection molded parts in strength and durability, and even functional features like living hinges are possible with SLS printing.
No tooling is needed to produce a part through SLS, which makes the manufacturing process more attractive. Unlike injection molding and subtractive manufacturing processes, low-volume parts can be produced in the same, simple way as high-volume parts. For high-volume processes like injection molding, tools have to be machined and properly maintained between use, which costs large sums of money. For SLS 3D printing, as long as the design is stored digitally the part can be reproduced.
The Best Applications for SLS
While direct metal laser sintering (DMLS) fuses metals together, SLS builds parts from plastics. Selective laser sintering is unique because the temperature of the particles is kept below the particles’ melting point, unlike in the selective laser melting (SLM) process. Resulting SLS parts are incredibly strong and durable, due to the homogenous structure of the parts. SLS 3D printing creates parts ideal for functional applications, with even the most or complex geometries. Common features that are easily achievable with SLS include:
- Living hinges
- Snap fits
- Mechanical joints
- Internal features
The advantages of SLS make the process most attractive for complex, high-value parts. These parts bridge many different industries with SLS being most common in the Automotive, Medical Devices, and Aerospace industries.
SLS typically makes the most sense for prototyping or for low-volume, high value part production. Durable prototypes and proof of concept models are well-suited to the SLS process because they can be iterated upon quickly to make improvements before moving to higher-volume manufacturing processes. The ability to make living hinges makes it especially useful for prototyping parts that will be injection molded for production.
Additionally, low-volume, high-value parts are great candidates for SLS due to the lack of required tooling. SLS is also a great option to keep in mind for your maintenance, repair, and operations strategy.
Whether building durable consumer products prototypes or parts with complex geometries for medical applications, among additive manufacturing technologies, selective laser sintering is a key manufacturing process to consider. The incredible strength and ability to produce functional features can be hard to find in other additive manufacturing processes. And, with fast production rates, turnaround times can be incredibly short, as fast as 24 hours with Fictiv.
Complex Parts at Ridiculous Speeds
For all your 3D printing and finishing needs, Fictiv has you covered. We’re experts at producing custom 3D printed parts, in a variety of materials, and we simplify custom part sourcing with intelligent, streamlined, automated workflows. Check out our Selective Laser Sintering Services page to learn more. Fictiv is your operating system for custom manufacturing that makes part procurement faster, easier, and more efficient.
Create an account and upload your part to see what our instant quote process, design for manufacturability feedback, and intelligent platform can do for you.