Time to read: 6 min
TPU injection molding is used to produce parts made from thermoplastic urethane (TPU), a type of thermoplastic elastomer (TPE). There are six major types of TPEs, a group of materials that combine the properties of plastic and rubber. TPUs can be based on either polyester or polyether urethane. They’re recyclable and provide excellent tear strength, abrasion resistance, and flex fatigue resistance.
If you’re thinking about selecting a thermoplastic urethane (TPU) for your next injection molding project, this article explains TPU’s material properties, advantages, disadvantages, design guidelines, and processing parameters. And you can plan your project’s timeline using this handy tool.
Free Template: Injection Molding Gantt Chart
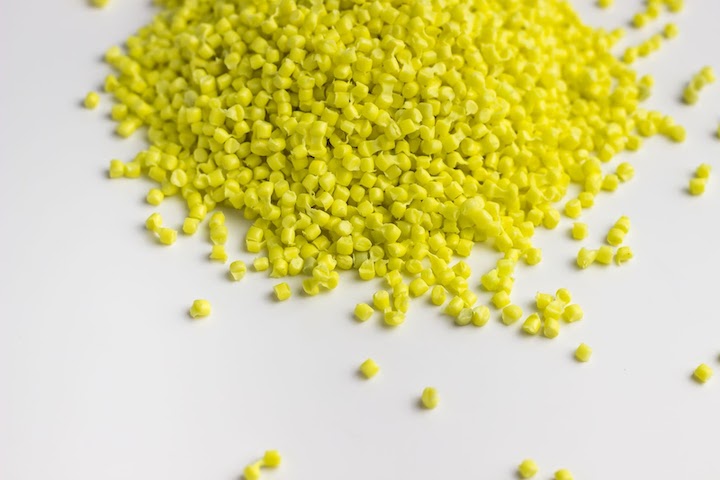
What are the advantages of thermoplastic urethanes (TPU)?
TPUs offer ten key advantages for injection molded parts.
- Elasticity: TPUs are highly elastic, so like rubber, they can be stretched and will return to their original shape.
- Toughness: TPUs are tough and durable, so they resist wear and tear, even under harsh conditions.
- Chemical resistance: TPUs resist a wide range of chemicals and can be used in harsh environments.
- Weather resistance: TPUs resist the effects of UV light (sunlight), ozone, and water. This makes them a good choice for outdoor environments.
- Low-temperature flexibility: TPUs can maintain their flexibility at low temperatures and withstand cold environments.
- Abrasion resistance: TPUs have a high degree of abrasion resistance. They’re great when there’s friction.
- Hydrophobic: TPUs are hydrophobic, which means that they resist the absorption of water. This makes them suitable for use in moist or wet environments.
- Good electrical insulation: TPUs are electrically insulating. Therefore, they’re often used in electrical and electronic applications.
- Biocompatibility: Some grades of TPU are biocompatible, meaning that they’re suitable for use in medical and dental applications.
- Versatility: TPUs can be used in a wide range of applications, from automotive and medical products to sporting goods and consumer electronics.
It’s important to note that the specific properties of a TPU vary by material grade. That’s why you need a partner who can help you with material selection and solve processing challenges.
What are disadvantages of thermoplastic urethanes (TPU)?
Injection-molded TPUs come with some disadvantages.
- Processing: TPUs can be more difficult to process than other types of materials, such as common types of thermoplastics.
- Cost: Because of their complex composition and processing requirements, TPUs can be more expensive to buy and use than other thermoplastics.
- Moisture sensitivity: some TPUs can absorb moisture, which can affect physical properties such as dimensional stability, mechanical strength, and electrical insulation.
- Adhesion: TPUs can be difficult to bond to other materials, such as metals and rigid plastics. Consequently, special adhesion agents or surface treatments are required.
- Chemical resistance: TPUs resist many different chemicals, but they can be vulnerable to certain solvents, such as ketones and esters.
- Aging: TPUs can age over time, leading to a decrease in mechanical strength, elasticity, and other physical properties.
- Surface finish: TPUs have a matte surface finish, which isn’t suitable for applications that require a glossy finish.
Keep in mind that these disadvantages can be mitigated or eliminated through proper processing, formulation, and optimal TPU grade selection.
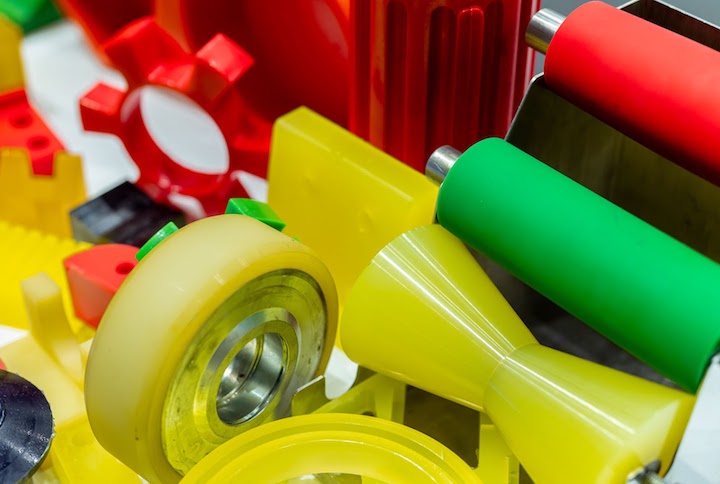
What are the injection molding design guidelines for thermoplastic urethanes (TPU)?
There are eight major design guidelines for injection-molded TPUs.
- Wall thickness: TPUs have a high degree of elasticity, which means they can fill thinner walls more easily than other thermoplastics. Evaluate wall thickness carefully and minimize it where possible to reduce weight and improve part strength.
- Draft angle: TPUs tend to stick to the mold surface, so you’ll need to apply a sufficient draft angle to ensure easy part ejection.
- Mold temperature: Because they are sensitive to temperature in general, TPUs can be sensitive to the temperature of the mold. To ensure consistent part quality, it’s important to carefully regulate mold temperature.
- Venting: TPUs are sensitive to pressure buildup during injection molding. Therefore, it’s important to provide sufficient venting to ensure proper flow and filling of the part.
- Gate location: For best results, place gates to minimize pressure buildup and reduce the risk of defects.
- Shrinkage: TPUs have a high degree of shrinkage, so it’s critical to identify your material’s shrinkage rate and account for it in your tool design.
- Overmolding: TPUs are commonly used in overmolding applications. For proper adhesion, carefully consider the compatibility of the TPU with the substrate material.
- Part size: Minimize part size where possible to reduce weight and improve part strength.
These design guidelines are general and your mileage will vary depending upon the TPU grade you select and your application.
How do you process thermoplastic urethanes (TPU) for injection molding?
TPU processing for injection molding involves several steps and requires specialized knowledge and equipment.
- Material preparation: TPUs are usually supplied in pellet form and must be dried prior to processing to remove any moisture — otherwise material properties and processing characteristics will be affected. The drying temperature and time depends upon the specific TPU grade and should be specified by the material supplier.
- Material feeding: TPU pellets are fed into the hopper of the injection molding machine and transported to the feeder barrel where they are melted and mixed. The injection molding machine should be equipped with a temperature control system to regulate barrel temperature and ensure consistent material melting and mixing.
- Injection: The melted and mixed TPU is injected into the mold under high pressure to fill the mold cavity and form the part. The injection pressure and mold temperature should be regulated to ensure proper filling and flow of the TPU and to minimize the risk of defects.
- Cooling: After injection, the mold is cooled to allow the TPU to solidify and take the shape of the mold cavity. The cooling time and temperature depends upon the specific TPU grade and the size and complexity of the part.
- Ejection: After cooling, the mold is opened and the part is ejected from the mold. The part is inspected for any defects and trimmed, if necessary, to remove the gate and any flash.
- Post-processing: TPU parts may require post-processing, such as painting, printing, or assembly, to meet specific application requirements.
Now that you understand the TPU injection molding process, it’s time to find out the best way to achieve project success.
How do you succeed with TPU injection molding?
Here are some tips for succeeding with TPU injection molding.
- Choose the right TPU grade: TPUs come in a range of grades that vary in properties such as hardness, tensile strength, and elongation. Choosing the right TPU grade helps to ensure that parts meet your requirements for performance, durability, and aesthetics.
- Proper material preparation: Properly prepare the TPU material by removing any moisture before processing. Drying the TPU at the correct temperature and for the specified time can help prevent material degradation and processing problems.
- Optimal processing conditions: Ensure that the injection molding machine is properly set up and that the temperature, pressure, and cooling time are regulated to ensure optimal processing conditions. Otherwise, inconsistent processing conditions may result in inconsistent part quality and dimensional stability.
- Good mold design: A well-designed tool is essential for successful TPU injection molding. The mold design should take into account the flow characteristics of the TPU material and the size and complexity of the part. A good mold design can help prevent defects, such as short shots, and ensure consistent part quality and dimensional stability.
- Post-processing: Some TPU parts may require post-processing, such as painting or assembly, to meet specific requirements. Plan for these post-processing steps in the initial design stage to ensure that the part can be easily modified, if necessary.
- Experienced provider: Work with an experienced and knowledgeable provider who can help you choose the right TPU grade, provide processing instructions, and assist with mold design and processing. An experienced provider can help ensure that you get the best results every time.
TPU injection molding offers many advantages, but it can also pose some challenges. When you partner with Fictiv, however, you’ll get expert design for manufacturing (DFM) feedback along with your quote. Fictiv understands the unique properties of TPU and has a global network of manufacturing partners who know how to process thermoplastic urethanes correctly, and so that your final parts meet your target specifications.
Ready to get started? Create a free Fictiv account and upload your design to get an injection molding quote today!