Time to read: 6 min
Injection molding with thermoplastic elastomers (TPEs) is a manufacturing process where TPE material is melted and injected into a mold cavity to form a specific shape. TPEs are a type of polymer that has both plastic and rubber-like properties, making them suitable for applications that require both flexibility and strength. The resulting molded part can have a wide range of physical and mechanical properties, depending on the specific TPE material used and the molding conditions. Injection molding with TPEs is commonly used by a variety of industries, including automotive, consumer goods, and medical devices.
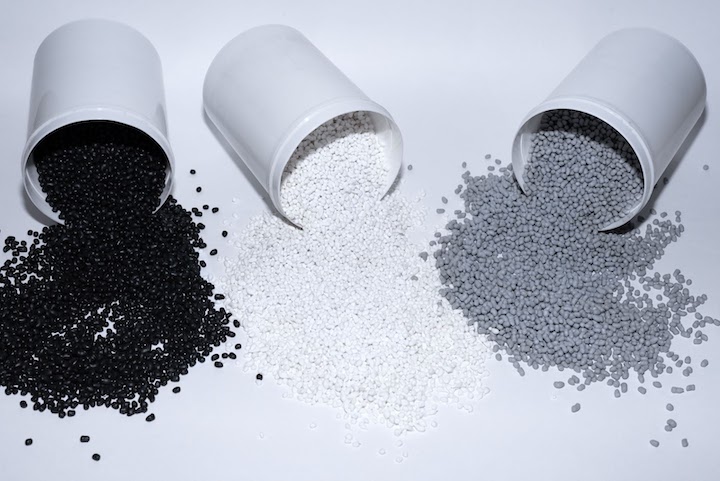
What are the advantages of thermoplastic elastomers?
Thermoplastic elastomers (TPEs) have a combination of rubber-like and plastic-like properties, which result in several specific material properties:
- Elasticity: TPEs have good elasticity and flexibility, which allows them to return to their original shape after being stretched or compressed.
- Tensile strength: TPEs have good tensile strength, meaning they can resist being stretched or pulled apart.
- Durability: TPEs are resistant to wear and tear, making them suitable for applications where parts are subjected to frequent stress.
- Chemical resistance: TPEs can be formulated to have varying levels of chemical resistance, making them suitable for use in a variety of environments.
- Temperature resistance: TPEs can be formulated to have varying levels of temperature resistance, with some TPEs suitable for use in high-temperature applications and others suitable for low-temperature applications.
- UV resistance: TPEs can be formulated to have varying levels of UV resistance, with some TPEs suitable for outdoor applications and others better suited for indoor applications.
- Surface finish: TPEs can have a variety of surface finishes, ranging from glossy to matte.
- Recyclability: TPEs can be melted down and re-processed into new parts, making them a more environmentally friendly option than some other materials.
The specific properties of TPEs can vary depending on the formulation and the specific application, so it’s important to choose the right TPE material for the specific requirements of the part.
What are the disadvantages of thermoplastic elastomers?
Thermoplastic elastomers (TPEs) have some disadvantages as well:
- Durability under high temperature: TPEs may have limited heat resistance compared to other materials, such as polypropylene or polycarbonate.
- Chemical resistance: TPEs are susceptible to degradation by certain chemicals, such as solvents and oils, which can reduce their lifespan.
- Surface finish: TPEs may not have the same high-quality surface finish as other materials, such as polycarbonate or acrylonitrile butadiene styrene (ABS), making them unsuitable for certain applications where appearance is important.
- Tear strength: TPEs have lower tear strength compared to other materials, making them unsuitable for applications that require high resistance to tearing.
- Cost: Depending on the specific application, TPEs may be more expensive than other materials, such as polyethylene or polyvinyl chloride (PVC).
- Part warping: TPEs are more prone to warping during the molding process compared to other materials, so they need more precise molding conditions to produce consistent, high-quality parts.
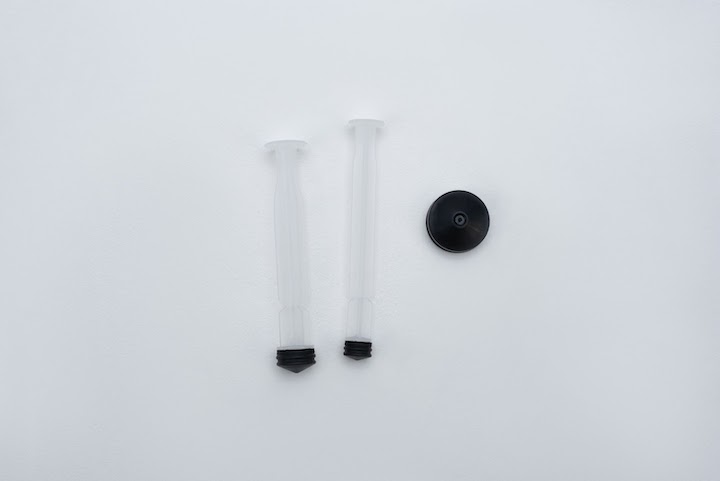
What are the design guidelines for injection molding for thermoplastic elastomers?
Designing for injection molding of thermoplastic elastomers (TPEs) involves several guidelines that can ensure proper and consistent molding, including:
- Wall thickness: TPEs have a lower shrink rate compared to other materials, so it’s important to maintain consistent wall thickness throughout the part to prevent warping or uneven shrinkage.
- Undercuts: TPEs are flexible and can be molded into complex shapes, but it’s important to avoid undercuts, as they make it difficult to remove the part from the mold.
- Draft angle: A draft angle is the slope on the side of the part that allows for easy removal from the mold, so designers should add a draft angle of at least 1 degree to each side of the part to prevent it from getting stuck in the mold.
- Venting: TPEs may produce some volatile organic compounds (VOCs) during the molding process, so proper venting is critical to allow the VOCs to escape and prevent defects.
- Gate placement: The gate, or the opening where the material is injected into the mold, should be placed in a location that will minimize stress on the part and prevent warping.
- Cooling: TPEs have a slower cooling rate compared to other materials, so it’s important to properly control the cooling rate to ensure consistent and high-quality parts.
- Material selection: TPEs come in a variety of formulations, each with different properties, so it’s important to choose the right material for the specific application and to consider factors such as temperature resistance, chemical resistance, and durability.
Pro-tip: If you want to learn more about designing for injection molding, check out our downloadable Injection Molding Design Guide.
How do you process thermoplastic elastomers for injection molding?
The process for injection molding thermoplastic elastomers (TPEs) requires precise control of the molding conditions, including temperature, pressure, and cooling time, to ensure consistent and high-quality parts. The process involves the following steps:
- Material preparation: TPE pellets are loaded into a hopper and fed into the injection molding machine.
- Heating: The TPE material is heated to a temperature above its melting point, turning it into a liquid that can flow and fill the mold.
- Injection: The liquid TPE material is injected into a mold under high pressure, filling the mold cavities and forming the desired shape of the part.
- Pack and hold: The mold is held under pressure for a specific amount of time to allow the TPE to cool and solidify. This step helps to ensure that the part has a consistent density and uniform strength.
- Cooling: The mold is cooled to a temperature that allows the TPE to solidify completely and form the final part. The cooling time varies depending on the size and complexity of the part, as well as the specific TPE material being used.
- Ejection: The mold is opened, and the part is removed. The part may need to be trimmed or finished to remove any flash or to improve its surface finish.
- Inspection: The finished part is inspected to ensure that it meets the desired specifications, and any necessary adjustments are made to the molding process.
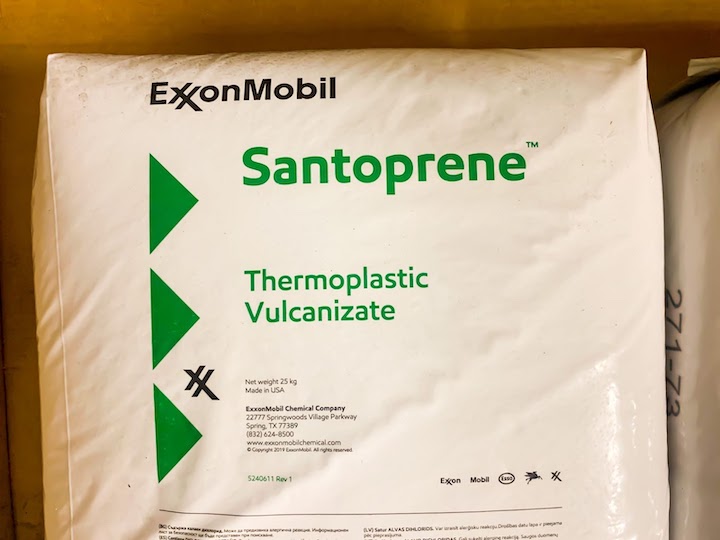
How do you succeed with injection molding with thermoplastic elastomers?
Success with injection molding of thermoplastic elastomers (TPEs) requires careful planning and attention to detail, including:
- Material selection: It’s important to choose the right TPE material for the specific requirements of the part, taking into account factors such as temperature resistance, chemical resistance, and durability.
- Design for manufacturing: The part design should account for the unique properties of TPEs, such as their low shrink rate, flexibility, and tendency to produce volatile organic compounds (VOCs) during the molding process. Proper wall thickness, draft angle, gate placement, and venting ensure consistent and high-quality parts.
- Proper processing conditions: The injection molding process requires precise control of temperature, pressure, and cooling time to ensure that the TPE material is properly processed.
- Manufacturing Expertise: It’s important to work with an experienced and knowledgeable injection molding provider who understands the unique properties of TPEs and has the expertise and equipment to process them correctly.
- Quality control: A robust quality control program is essential to ensure that each part meets the desired specifications and that the molding process remains consistent over time.
- Continual improvement: The injection molding process should be continuously monitored and improved to ensure that the best results are achieved. Regular evaluations of the process, including part measurements and material analysis, can help identify areas for improvement.
By following these guidelines and working with experienced and knowledgeable professionals, it is possible to achieve success with injection molding of TPEs and to produce high-quality, consistent parts.
Complex Parts at Ridiculous Speeds – Start Your Next Project With Fictiv
TPEs are a relatively common injection molding plastic, but a good plan and skilled production partner is still critical to avoid the added costs and risks that come with inadequate drying or improper processing methods. Fictiv has the global manufacturing network and production experts you need to get quality TPE parts. As your operating system for custom manufacturing, Fictiv has the skills and knowhow to support you from part design through prototyping and production.
Create your free Fictiv account and request an injection molding quote today — we mold complex parts at ridiculous speeds!