Time to read: 6 min
You just spent the last six months traveling to the red planet, Mars. You sit down for your first meal and you reach down to pick up your fork…but you realize you forgot it! Rather than waiting months or possibly years for the next group of people and supplies to come, you can simply upload a CAD file to the 3D printer you brought and print your fork!
This, of course, is just a fun example. The reality is that 3D printing technology will radically change how we complete space exploration missions, as well as the way scientific experiments are conducted in space. Let’s look at what’s being done now, with an eye toward the future.
3D Printing in Space: How it Works
3D printing on Earth is hard. 3D printing in space without gravity is really, really hard. In space, it uses a filament deposition modeling process, which takes a plastic filament, extruded through a hot tip, to heat up the plastic almost to melting point to get it malleable. This method is chosen for use in space, as opposed to liquid or powder resin, because the filament is easy to control in zero gravity.
Also, the International Space Station (ISS) has very strict requirements on what can be on the Space Station, and powder or liquid resin would cause too many concerns—what if something were to go wrong with the printer? The powder or liquid would be uncontrollable and could contaminate the entire spacecraft.
There is one existing printer called the Additive Manufacturing Facility that adheres to these strict requirements and is currently operating in space on the ISS.

Current 3D Printing in Space
The first 3D printer designed to operate in zero gravity was the Zero-G Printer, which was built under a joint partnership between NASA and Made In Space and launched into orbit on September 21, 2014. It served as a test bed for understanding the long-term effects of microgravity on 3D printing.

Then, in 2015, the Additive Manufacturing Facility (AMF) became a permanent manufacturing machine on the ISS, capable of off-world manufacturing in the hands of space developers everywhere who wish to get select hardware to space faster, more safely, and more affordably than traditional launch methods.
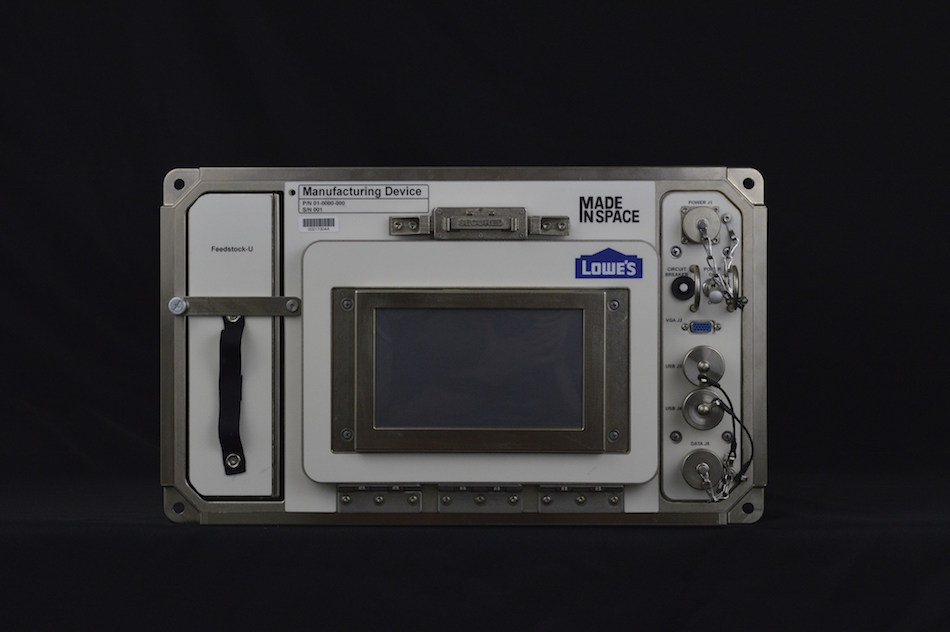
The R3DO is a zero-gravity material recycler designed so that material from waste products or previous prints can be melted down and turned back into 3D printing feedstock. This enhances the sustainability and overall efficiency of off-world additive manufacturing. This technology is extremely important when resources are scarce and you have to work with what you have. Think of what Matt Damon used in the Martian to grow his food…
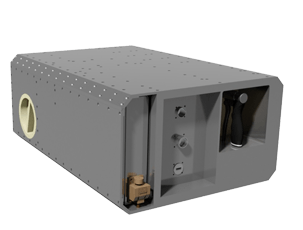
These printers were developed and manufactured by Made In Space, whose goal is to enable humanity’s future in space. It will be exciting to see how their products continue to evolve, as 3D printing in space becomes more sophisticated and the options and applications increase.

Why 3D Printing in Space is So Important
So why is this technology so important? There are lots of scenarios—for example, imagine a critical bolt on the ISS breaking. The astronauts would run out of oxygen if it couldn’t be replaced within minutes, and waiting for a re-supply mission would not be an option.
This type of scenario is exactly why NASA tested 3D printing a ratchet wrench on the ISS. NASA wanted to validate the process for 3D printing on demand, so they printed this 4.48-inch-long by 1.29-inch-wide, 104 layer plastic wrench.
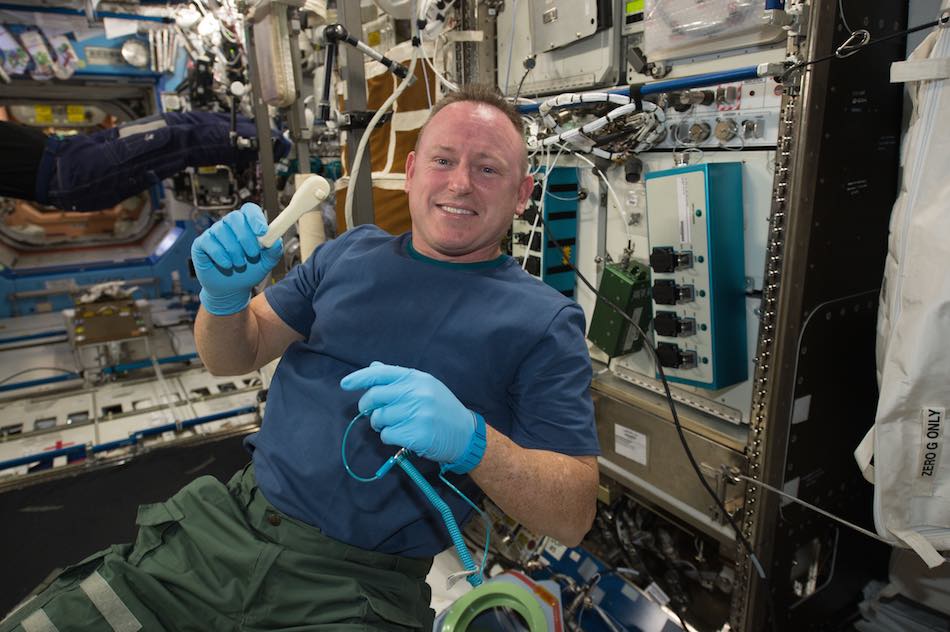
3D printing may be challenging in zero gravity, but the benefits outweigh any challenges. Made In Space continues to move forward with the technology by developing and operating larger scale microgravity production facilities.
One important project in progress is the manufacturing of optical fiber on the ISS. Terrestrially produced fiber suffers from certain glass impurities and microcrystal formations under the effects of gravity. Made In Space hopes that by removing gravity, it will improve both the response time and throughput advantage of traditional optical fiber currently in use for telecommunications. This could have huge implications for future space-to-Earth manufacturing.
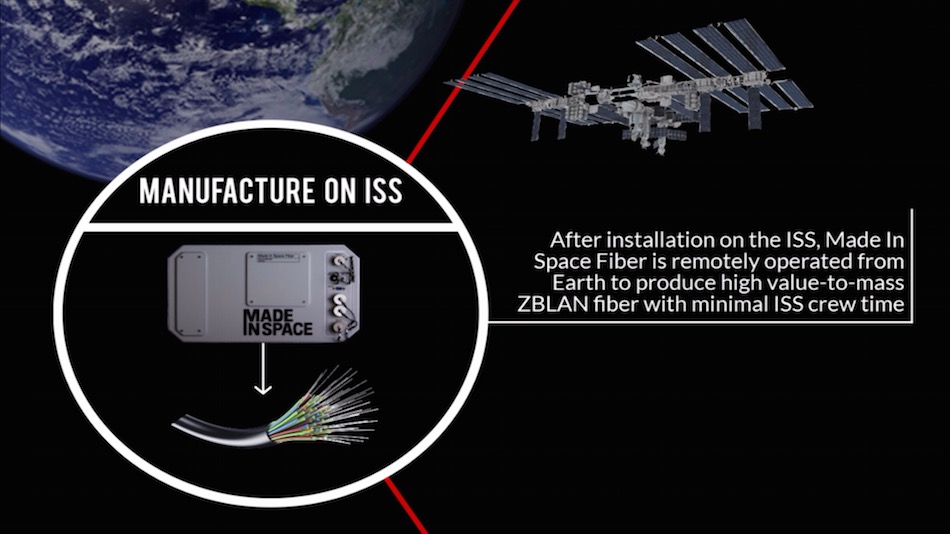
The Future of 3D Printing in Space
Rather than simply having a 3D printer on a satellite, imagine 3D printing the entire satellite. Tethers Unlimited is changing the way we build and deploy spacecraft, by enabling space systems to fabricate and integrate key components on-orbit.

Currently, the various components of a satellite—its antennae and solar panels, for example—have to be carefully designed to be foldable to fit inside a launch rocket. Once in orbit, those components have to unfold carefully and correctly, a hurdle that has tripped up many past missions.
With care, these issues can be avoided. But the limit on how much you can fold and pack into one mission is currently overcome primarily by building bigger rockets. Satellites that can be constructed in orbit would allow rockets to carry its material up in a very compact and durable form, allowing for more material to fit into each launch.
Tethers Unlimited is working on this and began by developing an architecture for a SpiderFab system, identifying the key capabilities required to fabricate large spacecraft components on-orbit. They developed two concept implementations of this architecture, one specialized for fabricating support trusses for large solar arrays (picture below), and the second a more flexible robotic system capable of fabricating many different spacecraft components, such as antenna reflectors and optical occulters.

The SpiderFab architecture is at a technology readiness level (TRL) of 3, which is a type of measurement system used to assess the maturity level of a particular technology. The scale goes from 1 to 9, where a TRL of 1 means scientific research is beginning, a 2 means the basic principles have been studied and practical applications can be applied, and a 3 means that active research and design have begun. During a TRL of 3, a proof-of-concept model is constructed, and both analytical and laboratory studies are required to see if the technology is viable and ready to proceed further through the development process.
On-orbit fabrication of spacecraft components can enable space programs to escape the volumetric limitations of launch shrouds and create systems with extremely large apertures and very long baselines in order to deliver higher resolution, higher bandwidth, and higher SNR data. Therefore, any space program/spacecraft will highly benefit from this technology.
The SpiderFab effort will radically change the way we build and deploy spacecraft, by enabling space systems to fabricate and integrate key components on-orbit.
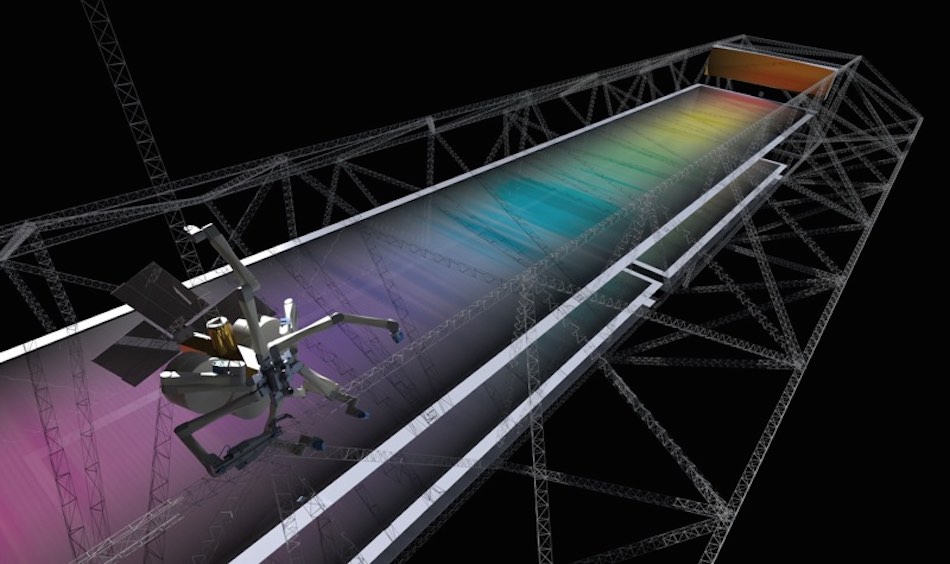
SpiderFab is not the only “build in space” concept: Made In Space has a competing idea on how to accomplish this goal, Archinaut, which will enable the first additive manufacturing, aggregation, and assembly of large and complex systems in space without astronaut extravehicular activity. We’ll start to see more competing ideas and products coming out in the next ten to fifteen years.
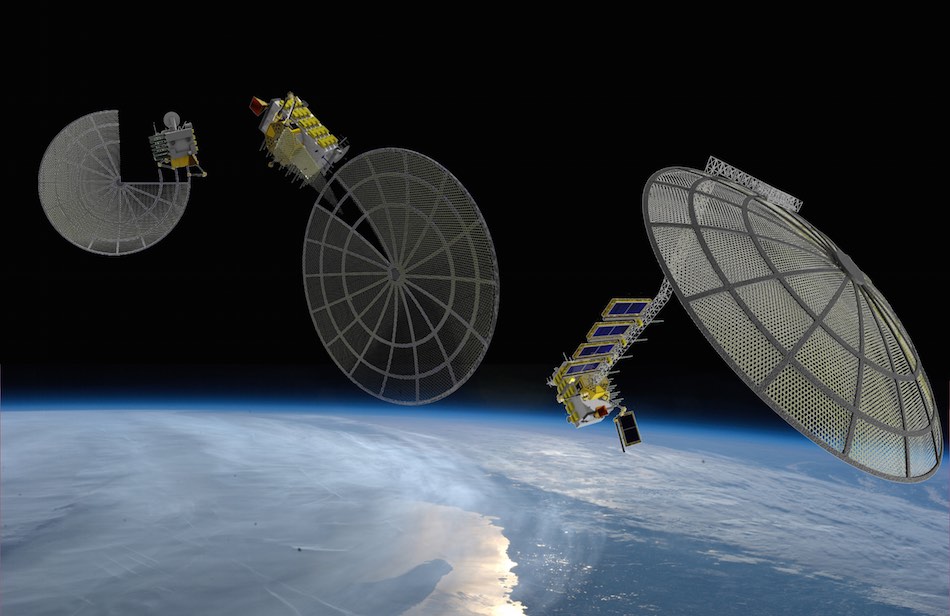
Parting Thoughts
It can take months or even years, depending on launch resupply schedules, to get equipment to the International Space Station (ISS), and that’s just too much time. For missions past low-Earth orbit (LEO), like Mars, re-supply from Earth may be impossible.
We have the technology to 3D print items as essential as utensils and bolts, so we must leverage that technology for space applications. From 3D printing a bolt inside the ISS to printing part of the ISS itself, 3D printing technology will change how we complete space exploration missions and the way science is conducted in space.