Time to read: 8 min
Titanium CNC machining can be challenging. Titanium, a chemical element, is stronger than industrial metals such as stainless steel. Yet titanium’s strength isn’t all that makes it difficult (but not impossible) to machine with CNC equipment.
Because titanium has low thermal conductivity, generated heat flows slowly through it. This means that the heat generated during CNC machining can build up quickly, causing tool wear and potential distortion of the workpiece. Titanium’s tendency to work harden and its chemical reactivity with cutting tools can further complicate machining operations.
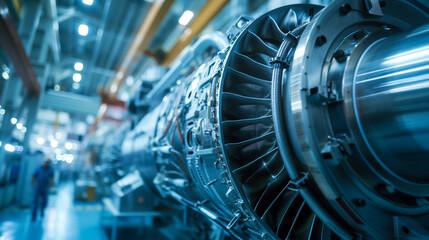
CNC-machined titanium parts are often used in aerospace applications.
Getting Started with Titanium CNC Machining
This article explains what you need to know about titanium, one of the many metals for which Fictiv provides CNC machining services. The article covers the advantages and applications for CNC titanium machining and provides expert tips about part design, material selection, machining, and surface finish.
Fictiv machines titanium parts at ridiculous speeds, and provides both instant AI and human design for manufacturing (DFM) feedback. If you’re ready to get started, create a free Fictiv account and upload your part for an instant quote.
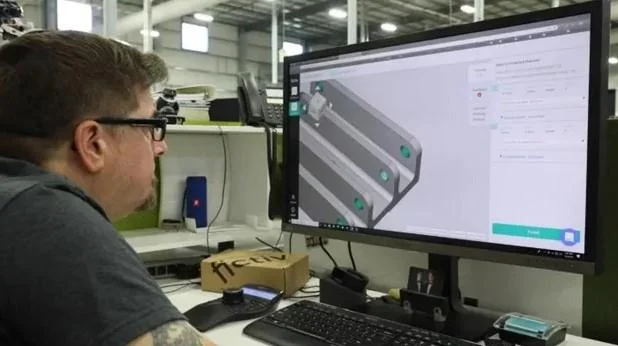
The Fictiv platform provides DFM feedback about your part.
Advantages and Applications for CNC Machining Titanium
CNC-machined titanium parts are exceptionally durable and titanium’s high strength-to-weight ratio, biocompatibility, and chemical/corrosion resistance make it an attractive material for the following applications.
- Aerospace is the primary consumer of titanium materials. Applications include aircraft seat components, shafts, turbine parts, valves, and oxygen generation system parts.
- Automotive manufacturers use titanium to reduce fuel consumption by reducing weight (i.e., lightweighting) by using titanium to replace heavier steel parts. Titanium is used in valves and valve springs, engine piston pins, retainers, and brake caliper pistons.
- Medical and Dental applicationsfor CNC machining titanium include screws (bone, dental, cranial, etc.), spinal fixation rods, femoral head implants, and orthopedic pins. Hip, knee, elbow, and shoulder joint replacements are also machined from titanium. Titanium is a good choice for the medical technology industry due to its biocompatibility and bioactivity produced with special surface treatments.
- Marine/Naval uses for machined titanium include seawater desalination propeller shafts, subsea resource extraction, rigging equipment, underwater robotics, and marine heat exchangers.
Economic Considerations
Titanium is more expensive than other metals because of its rigorous quality and control standards and growing market demand. Use the bulleted list below as a checklist for economic considerations.
- Compare titanium prices with other metals
- Determine your initial investment and the ongoing costs of tooling
- Analyze the factors affecting machining time
- Develop strategies for cost optimization
- Consider labor costs and the required expertise for operators
- Track energy consumption and identify strategies for reducing costs
- Calculate and optimize coolant and lubricant expenses
- Control waste management costs and pursue recycling strategies
- Identify long-term cost savings due to titanium’s durability
- Track current market demand and develop pricing strategies
- Calculate return on investment (ROI) a use a break-even analysis
Designing Parts for CNC Titanium Machining
Given that titanium is costlier than other metals, it’s crucial to design your parts meticulously. This involves using CAD/CAM software for part design and manufacturing, creating well-designed fixtures and jigs to support machining, and considering design for manufacturability (DFM) for efficient production.
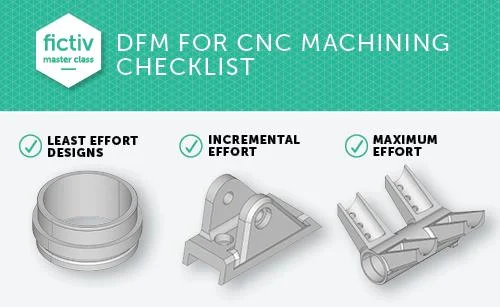
Fictiv’s DFM for CNC Machining Checklist is available for download.
CAD/CAM Software
Use computer-aided design (CAD) software to design your parts and computer-aided manufacturing (CAM) software to machine them. Then check your designs with analysis or simulation software like ANSYS. Proper part design can minimize machining time, improve part quality, and reduce waste.
CAM software uses your CAD models and assemblies to generate toolpaths. The tools themselves need to support titanium, which requires careful management of cutting forces and temperatures, as well as more rigidity.
Fixture and Jig Design
Titanium machining requires robust and well-designed fixtures and jigs. These supports must be rigid enough to handle machining stresses while preventing workpiece deflection and excess vibration. Proper fixture and jig design also ensures stability and accuracy, allowing for precise cuts while reducing the likelihood of tool breakage. As a part designer, it’s essential to understand how, why, and where these supports are used. This will help you design more economical, less complex parts.
Design for Manufacturability
Design for manufacturability (DFM) with titanium requires an understanding of the metal’s unique properties and machining challenges, including titanium’s lower thermal conductivity and higher required cutting forces. For more efficient production and better quality parts, simplify complex geometries and incorporate features that simplify machining operations. Examples include using larger radii, applying a uniform wall thickness, and avoiding deep pockets.
Fictiv provides DFM feedback along with your request for a quote, so create a free Fictiv account and upload your CAD file if you’re ready for CNC machining services.
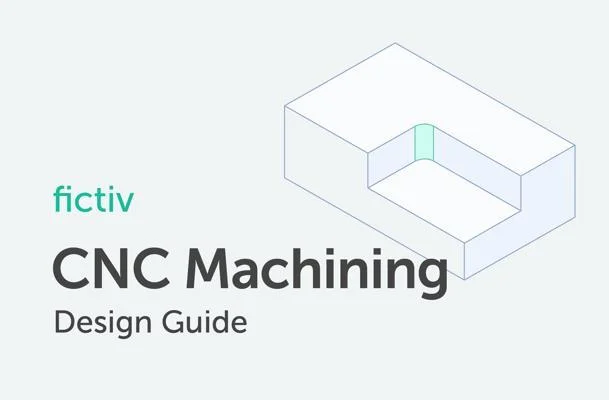
Fictiv’s CNC Machining Design Guide is available online anytime.
Selecting Titanium Alloys and Grades
Titanium is available in different grades, including commercially pure titanium (>99% Ti) (Grades 1 to 4) and titanium alloys (Grades 5 and higher). In the table below, you’ll find a description of these grades, their properties, and applications. This information can help you choose the right material for your titanium part design.
Table 1: Common Titanium Grades Used for CNC Machining
Grade | Description | Properties | Applications |
Grade 1 | Commercially pure Low oxygen content | Excellent corrosion resistance High impact toughness Easy to CNC machine Not as strong as some other titanium grades | Chemical processing Heat exchangers Desalination Automotive parts Airframes Medical |
Grade 2 | Commercially pure Standard oxygen content | Stronger than Grade 1 High corrosion resistance Good ductility High formability, weldability, and machinability | Airframes and aircraft engines Hydrocarbon processing Marine Medical Chlorate manufacturing |
Grade 3 | Commercially pure Medium oxygen content | More difficult to form than Grades 1 and 2 High strength and corrosion resistance Decent machinability | Aerospace Marine Medical |
Grade 4 | Commercially pure High oxygen content | Highest strength among the pure grades Excellent corrosion resistance Requires high feed rates, slow speeds, and high coolant flow Difficult to machine | Cryogenic vessels Heat exchangers Hydraulics Airframes and aircraft engines CPI equipment Marine Surgical hardware |
Grade 5 | Titanium alloy Ti6Al4V | High corrosion resistance Excellent formability Poor machinability | Airframe structures and aircraft engines Power generation Medical devices Marine and offshore Hydraulics |
Grade 6 | Titanium alloy Ti5Al-2.5Sn | Good weldability Stability and strength at high temperatures. Intermediate strength for titanium alloys | Liquid gas and propellant containment for rockets Airframe and jet engine applications Space vehicles |
Grade 7 | Sometimes considered pure, but contains small amounts of palladium Ti-0.15Pd | Superior corrosion resistance Excellent weldability and formability Lower strength than other titanium alloys | Production equipment parts Chemical processing |
Grade 11 | Sometimes considered pure, but contains small amounts of palladium Ti-0.15Pd | Excellent corrosion resistance, ductility, and formability Even lower strength than Grade 7 alloys | Desalination Marine Chlorate manufacturing |
Grade 12 | Titanium alloy Ti0.3Mo0.8Ni | High strength at high temperatures Great weldability and corrosion resistance. More expensive than other titanium alloys | Hydrometallurgical applications Aircraft and marine components Heat exchangers. |
Grade 23 | Titanium alloy T6Al4V-ELI | Great formability and ductility Fair fracture toughness Ideal biocompatibility Poor machinability Lower strength than other titanium alloys | Orthodontic appliances Orthopedic pins and screws Surgical staples Orthopedic cables |
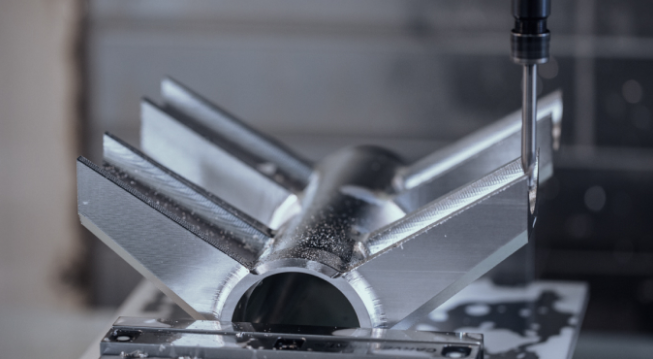
CNC machining supports design complexity, but titanium poses special challenges.
Tips for CNC Machining Titanium
Titanium can be machined with CNC milling, turning and lathing, drilling and boring, utilizing a multi-axis precision machine. Each process involves different operations and has benefits and challenges.
- Milling uses rotating tools to shape parts and requires managing speeds and coolant levels to prevent tool wear.
- Turning and lathing rotate the titanium workpiece while a stationary tool shapes it. It’s ideal for cylindrical parts but requires careful handling to avoid excessive vibrations and ensure a smooth finish.
- Drilling and boring are two similar processes. Drilling creates precise holes using sharp bits. Boring enlarges these holes and is used to meet tight tolerances.
- 5-axis machining is the most advanced process, allowing the titanium workpiece to move along five different axes. Because it can create intricate parts with fewer setups, it’s particularly useful in aerospace and medical applications.
Looking ahead, emerging technologies such as AI-driven toolpath optimization and smart machining systems are expected to revolutionize CNC machining. Additionally, the use of hybrid manufacturing—combining additive and subtractive methods—is expected to provide greater design flexibility.
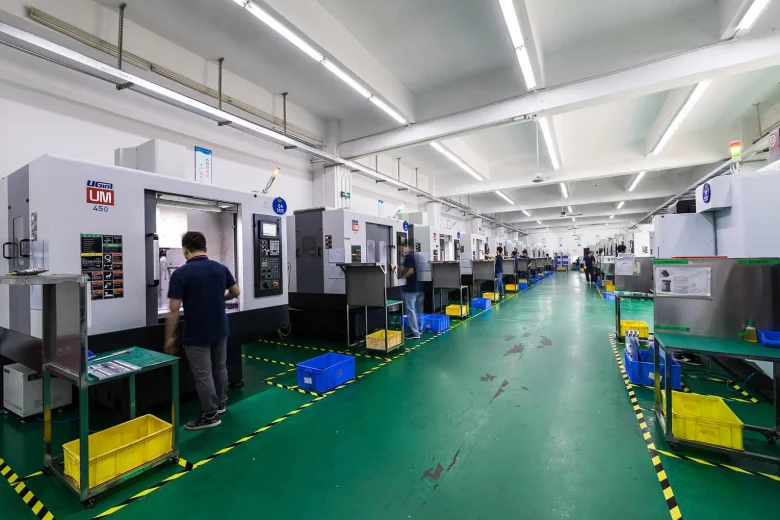
Fictiv uses high-precision CNC machining equipment to produce parts at amazing speeds.
Setting CNC Machining Parameters
Regardless of the CNC machining equipment you use, it’s important to fine-tune your machining parameters to achieve high-quality results. Cutting speeds and feed rates, machining tolerances, and coolant are important considerations.
Cutting Speeds and Feed Rates
Careful control of cutting speeds and feed rates help prevent workpiece overheating and tool wear. Lower cutting speeds paired with higher feed rates reduce heat buildup and maintain the integrity of the tool and the workpiece. If higher speeds are required, cutting tools coated with titanium aluminum nitride (TiAlN) or titanium carbo-nitride (TiCN) are recommended.
When CNC milling titanium, the ideal cutting speed varies depending on the specific type and grade of titanium, as well as the tooling and coolant used. A general guideline is a surface speed of approximately 60-100 feet per minute (FPM) or 18-30 meters per minute (MPM). It’s crucial to also consider other factors such as feed rate, depth of cut, and the machine’s power and rigidity.
Machining Tolerances
It’s difficult to achieve tight tolerances with titanium because of the metal’s sensitivity to heat and tendency to cause tool deflection. However, you can prevent excessive deflection by ensuring that parts are well-supported and secured. Shorter cutting tools also reduce deflection, while a well-stabilized setup minimizes vibrations that affect machining accuracy.
Coolant Use
Temperature control is critical when machining titanium. Directing a steady, high-pressure stream of coolant at the cut region cools both the workpiece and the cutting tool. A high-pressure coolant stream also removes chips that would otherwise stick to the tool. Adjust the volume and concentration of coolant to optimize usage and avoid waste.
To mitigate heat build-up, use a coolant with excellent lubricity and cooling properties. Coolants specifically designed for machining difficult materials, such as emulsion-based coolants with high lubricity, are recommended.
Additional Machining Considerations
Preventing overheating involves more than just coolants. Along with adjusting feed rates and spindle speeds, consider cutting strategies to improve efficiency and reduce heat. For example, increasing the axial depth of the cut while reducing radial engagement helps with thermal management.
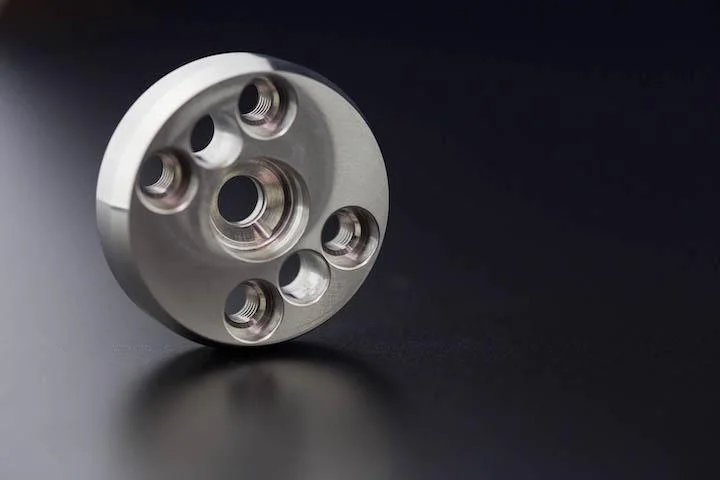
CNC-machined parts like this may require several surface finishing methods.
Following Safety Precautions and Best Practices
Safety is important in titanium CNC machining to reduce the risk of injuries to workers and damage to equipment. Machine crashes, electrical hazards, health hazards, and flying debris are all risk factors. Use the bulleted list below as a checklist for safety precautions and best practices.
- Understand the importance of safety in CNC titanium machining
- Wear recommended personal protective equipment (PPE)
- Follow safe handling and storage procedures for titanium materials
- Perform machine setup and regular maintenance checks
- Adhere to proper cutting tool selection, handling, and storage practices
- Handle and dispose of coolants and lubricants properly
- Implement fire prevention measures and response plans
- Safely remove and dispose of titanium chips and debris
- Use ergonomic workstation setups to reduce operator fatigue
- Implement training programs for operators on safe practices
- Develop emergency procedures and first aid measures
Surface Finishing CNC-Machined Titanium Parts
Titanium CNC machining supports the use of various surface finishing treatments for functional and aesthetic purposes. Often, finishing is used to reduce surface roughness and improve the appearance, durability, and performance of machined parts.
The surface finishing processes used with titanium include:
- Polishing
- Bead blasting
- Anodizing
- Chroming
- Brushing
- Painting
- PVD coating
- Powder coating
- Electrophoresis
Industry Standards and Certifications
There are several standards and certifications that apply to CNC machining titanium.They help ensure the quality and reliability of titanium parts produced through CNC machining, especially in critical applications like aerospace and medical devices.
Industry Standards
ASTM International, the International Standards Organization (ISO), and SAE international have published industry standards that apply to titanium CNC machining.
ASTM Standards
- ASTM B265: Standard Specification for Titanium and Titanium Alloy Strip, Sheet, and Plate.
- ASTM F136: Standard Specification for Wrought Titanium-6Aluminum-4Vanadium ELI (Extra Low Interstitial) Alloy for Surgical Implant Applications.
- ASTM F1472: Standard Specification for Wrought Titanium-6Aluminum-4Vanadium Alloy for Surgical Implant Applications.
ISO Standards
- ISO 5832-2: Implants for surgery – Metallic materials – Part 2: Unalloyed titanium.
- ISO 5832-3: Implants for surgery – Metallic materials – Part 3: Wrought titanium 6-aluminum 4-vanadium alloy.
SAE Standards
- SAE AMS 4911: Titanium Alloy Sheet, Strip, and Plate, 6Al – 4V Annealed.
Certifications
There are three certifications that apply to CNC machining titanium
- ISO 9001: Quality Management Systems – Requirements. This certification ensures that a company’s quality management processes meet international standards.
- AS9100: Quality Management Systems – Requirements for Aviation, Space, and Defense Organizations. This certification is crucial for companies manufacturing aerospace components.
- ISO 13485: Medical devices – Quality management systems – Requirements for regulatory purposes. This certification is essential for companies producing medical devices.
Choose Fictiv for CNC Machining Titanium Parts
Fictiv provides CNC machining services for titanium along with secondary processes such as surface finishing. Importantly, we also offer DFM assistance and produce orders quickly, reducing your time to market. Whether you need intricate components or high-volume production, Fictiv delivers exceptional results with fast turnaround times.
To get started, create a Fictiv account and upload your design today!