Time to read: 8 min
Threaded fasteners, such as bolts and nuts, are used in many applications, ranging from plastic toys to massive bridges. And all threaded fastener connections need to stay together when we want them to, but also come apart when needed. For example, the valve covers on an engine must remain in place while driving, but we also need them to be removable so we can service the engine components.
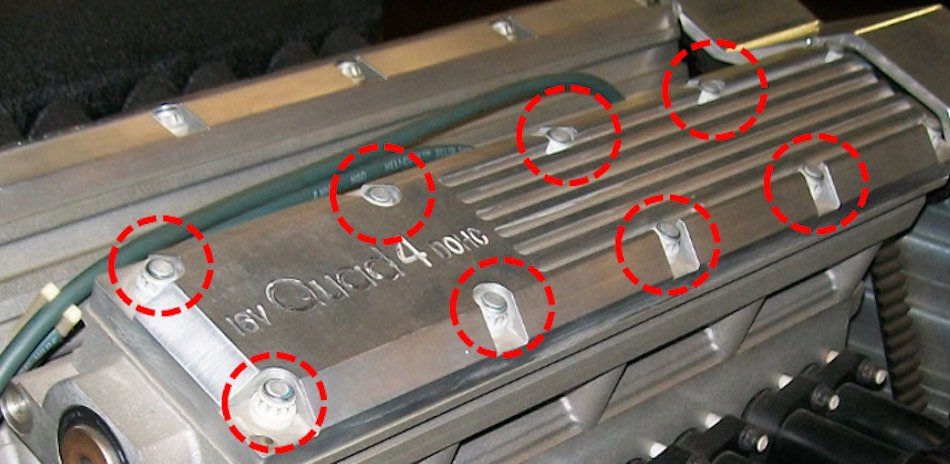
This article will explore different methods to ensure that these types of connections stay together when we need them to. The term “Thread Locking” is typically used for methods of ensuring the threads stay in place without loosening and will be used often in this article.
Threaded Fastener Connection Methods
There are many types of threaded fastener connections, but the primary types are as follows:Bolt, Nut (Washer Optional) – Seen below, this is the most common and low-cost type of threaded connection. It’s used in applications ranging from automobiles to cell tower antennas.
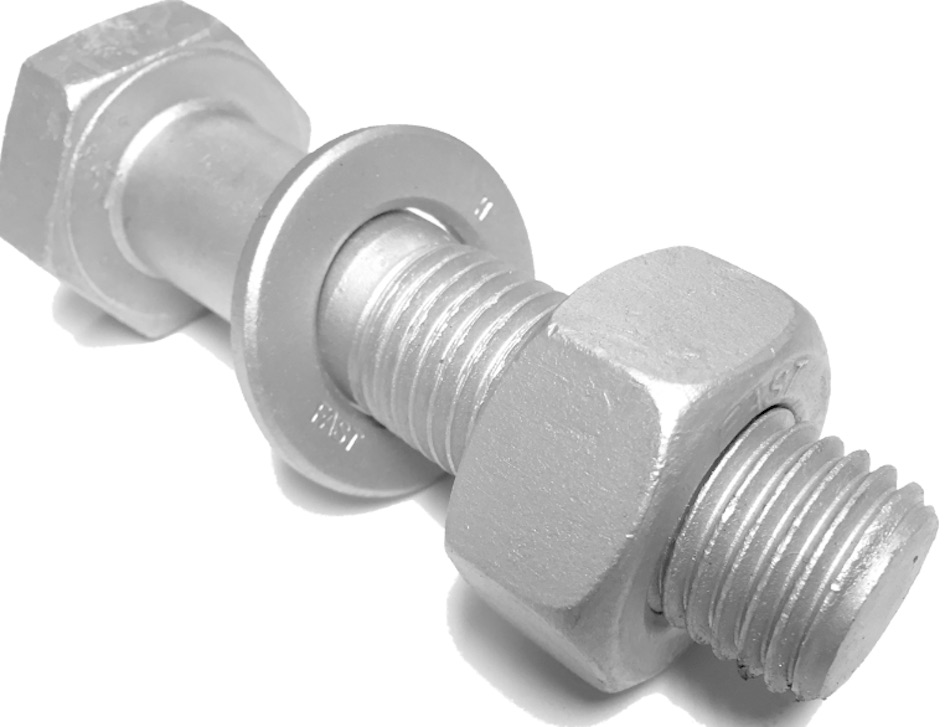
- Screw, Tapped Hole – With this type of connection, a screw is installed into a drilled and tapped hole in a housing or mechanical component. The most commonly recognized difference between a screw and a bolt is that screws typically go into threaded holes. In contrast, bolts go through 2 unthreaded components and fasten with a nut because screws have a tapered end and bolts have a non-tapered end.
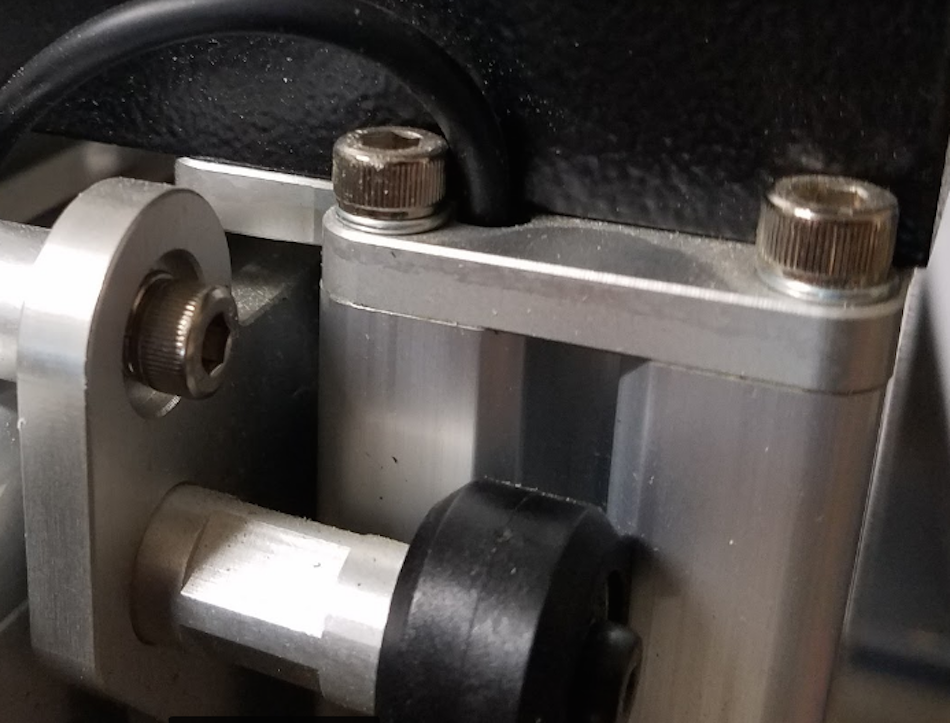
We can see three cap screws installed in tapped aluminum components. Screws are used instead of bolts for precision, ease of assembly, and increased component rigidity — or likely a combination of those factors.
- Threaded Components – These are most commonly shafts or housings (typically cylindrical) that have both been threaded to fasten together. A flashlight bulb and battery tube is a good example.
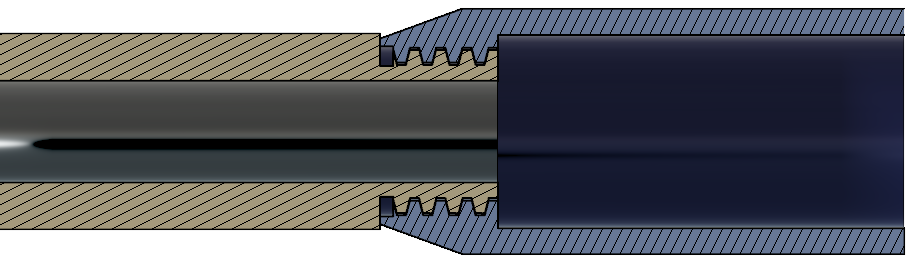
Diving Deeper: Physics of Threaded Connections
Now that we have reviewed the types of threaded connections, it’s time to go over some familiar terms: preload, torque, and stiffness. We will also cover some calculations to get you on the right path to choosing threaded fasteners.
Since the purpose of a bolt is to clamp two or more parts together, the applied clamping load stretches/elongates the bolt. This stretching or elongation is the preload or clamping force and remains after tightening the nut to near its elastic limit as long as the nut doesn’t loosen. This preload is axial and puts the bolt in tension while the members clamped together are in compression.
The torque required to create this preload is measured in units, such as in-lbs or N-m, but is always just a force acting to “twist” the components together. With threaded components, this torquing together creates an axial force (the preload). The image below illustrates a before and after picture of a bolt being tightened. The red lock washers are in the expanded state, but when the assembly is torqued together, the lock washers are compressed and behave as springs.
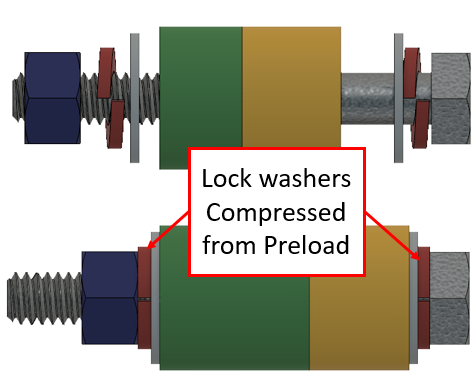
Pro-tip: when tightening a bolt/nut/washer connection, hold the bolt head stationary and apply torque to twist the nut tight; this prevents the bolt shank from fracturing due to thread-friction-induced torque.To calculate the required pre-load -Fi (the force that is applied while tightening the nut), and ensure that the bolt can withstand the applied tensile load P, us the following equations:
Fi = Preload
Ptotal=Total applied external tensile load on joint
P=Ptotal/number of bolts (N) = tensile load per bolt
Pb= portion of P applied to bolt
Fb= Pb +Fi =resulting load on bolt
Pm= portion of P applied to clamped members
Fm= Pm -Fi =resulting load on clamped members
C= stiffness constant of the joint
Assuming N bolts share the applied load equally and load P is in tension:
and
Pm=P-Pb=(1-C)*P
Load experienced by the bolt is:
Fb= Pb +Fi=C*P+Fi when Fm﹤0
And load experienced by the member is:
Fm= Pm -Fi=(1-C)*P-Fi when Fm﹤0
So, you can see how to solve for the preload needed to prevent failure of the bolt and clamped members for a threaded locking connection!
Pro-tip: Check out this textbook for more on bolt or other threaded locking method design.
In some cases, the frictional forces from this preload are enough to hold the fastener together. But in other cases — high vibration, expected stress relaxation (creep in plastics), and cyclic stresses — we need to use thread lockers.
Thread Locking Categories and Methods
Thread locking methods can be separated into two categories: mechanical methods and adhesives that prevent loosening and ensure you successfully secure bolts and screws:
Mechanical Hardware
Mechanical hardware includes physical components used to prevent threaded fasteners from loosening. These are some examples of common thread locking hardware:
- Lock Washers – There are a few styles of lock washers, but they’re all placed under the head of a bolt or screw with the intent of preventing it from loosening and maintaining a preload.

This type of washer acts as a spring when the bolt is tightened. That spring action maintains some preload, even if the screw relaxes a little. However, these components don’t work well in high vibration conditions.
Another type of lock washer is the Nord-lock, which relies on mechanical ramps and teeth to prevent loosening, as shown below:

The teeth bite into the bolt or screw head as well as the material under the washer, while the ramps are oriented so they “climb” in the direction that would loosen the fastener. In other words, to un-torque the bolt, you have to increase the preload, while overcoming the ramps. These are effective, but relatively pricey and typically used on larger hardware. There are also many other lock washer designs, so I encourage you to research additional options.
- Nylon Insert Lock (nylock) Nut – These have a circular nylon insert that locks the threads in place by deforming over the mating threads. These nuts may not hold the peak preload in all cases of vibration, but they typically retain the nut, even if it loses some preload.
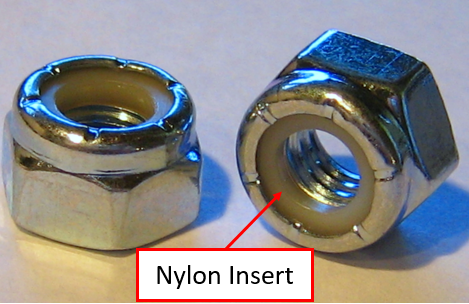
Nylock nuts are commonly used in high vibration environments on non-safety critical applications. For example, this type of fastener is used on my hitch mounted mountain bike rack, as shown below. In this application, there’s no immediate safety hazard if the preload is lost because the screw still supports the load in double shear.
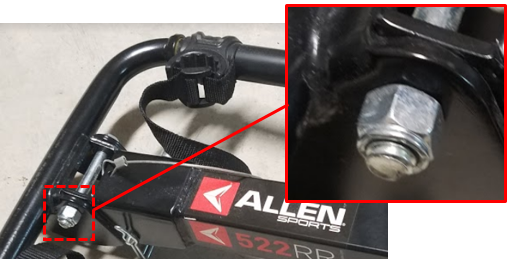
- Safety Wire – the use of safety wire is very common in aerospace, defense, and auto racing. It works by installing a steel wire through a hole in a screw, bolt, or nut and anchoring it to another item. For one nut to loosen, the other must be tightened because of the orientation of the wire. And that orientation is critical, because safety wire installed incorrectly is almost entirely useless. Safety wire is often applied between a series of fasteners to hold them all together, as seen below.
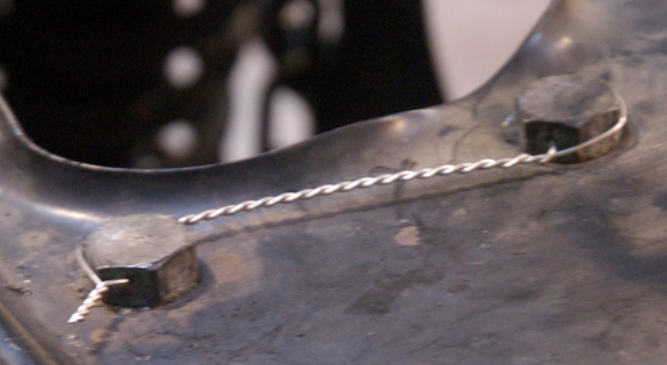
- Castle Nut/Safety Clip/Retainer Pin – There are several iterations of the castle nut, but they all behave in a similar fashion — a pin is placed through the threaded shaft or bolt to prevent a nut from backing off.
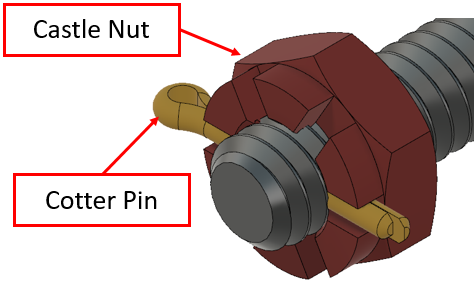
In this application, a hole is drilled in the bolt so the cotter pin can go through the slots in the castle nut. This prevents the nut from rotating in either direction to prevent loosening, but still allows for the pin to be removed and nut loosened if needed.
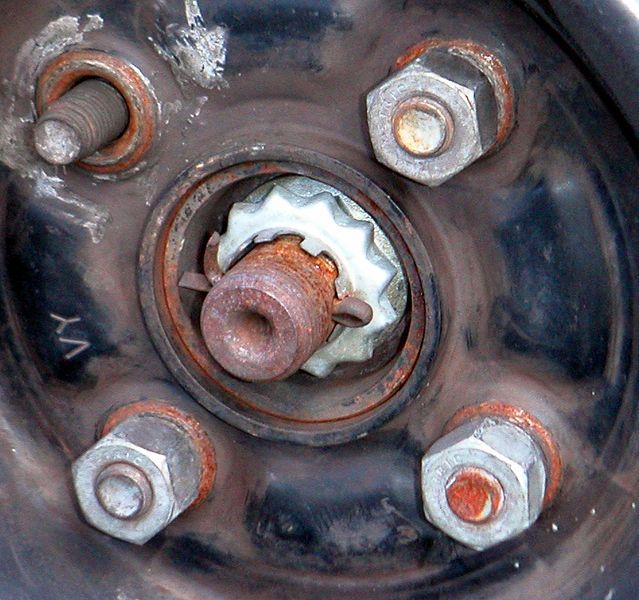
- One of the lesser known types of thread locking methods is the SpiralockⓇ (also known as the spiral locking technique) fastening system for heavy vibrations of challenging environments. This innovative locking system provides an angled shoulder that makes contact with the threads on a fastener’s shank and prevents them from loosening. The system reduces the stress concentration at the crest (peak) of the threads, and can provide a screw with a mating lock similar to a nut.
Adhesives
In many cases, adhesives are a commonly utilized thread locking method. They are even used in conjunction with the mechanical methods above in many instances. In the oil and gas industry, where the drilling environment sees extreme vibrations, it’s common to use a lock washer and an adhesive.
Such adhesives can be broken down as follows:
- Threadlockers (Loctite, Vibratite, i.e.) – These include a wide variety of adhesives that bond the threads in place. Loctite is the most widely known brand in the United States, but several alternatives exist. The image below shows an example of Loctite 242 (blue) applied to a bolt, but you can use Loctite for screw connections as well.
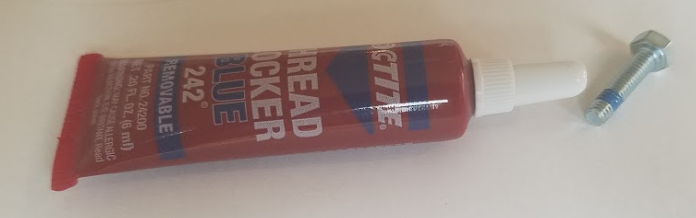
It’s important to note that Loctite comes in several grades, some of which are not intended to be removable — so ensure you’re using the correct grade for your application. You can also find the amount of loading each adhesive can sustain in the relevant technical data sheets.
- Dry Patch – This method uses a dry patch pre-applied to threads to act as a thread locker. In some instances, it’s a dry nylon, while in others it’s an active adhesive. The image below shows a dry patch of a combination threadlocker/sealant used to seal a pneumatic pressure relief valve. This is similar to PTFE tape you apply to plumbing threads.
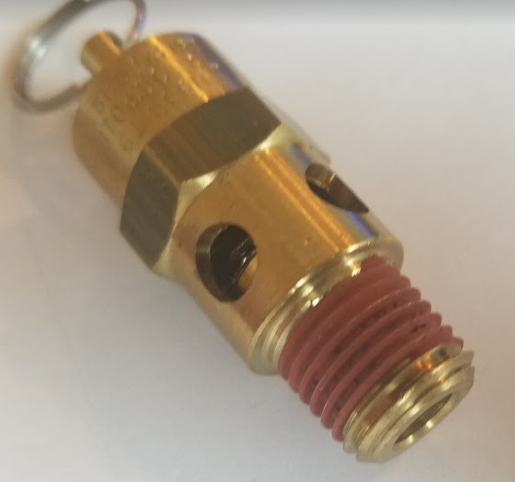
Dry patches are often used to eliminate the process variability associated with manually dispensing adhesive threadlockers. They also are used to improve the logistics of loose hardware that requires threadlockers. For example, I recently assembled some furniture that had dry patches on all the hardware. The manufacturer knew this would improve the reliability of the assembly and doesn’t require the end user to apply a liquid threadlocker.
Here’s a quick reference chart that will help you find the right thread locker for your next project:
Method |
Common Applications |
Relative Cost |
Split Lock Washer | Low to mid-vibration applications that target a maintained preload |
$ |
Nord Lock | High-vibration, heavy industrial applications that need to retain a preload |
$$$ |
Nylon Insert Nut | Low to mid-vibration assemblies or applications that need to retain the nut if preload is lost |
$ |
Safety Wire | Safety-critical applications, particularly aerospace, defense, and racing |
$$$ |
Castle Nut | Safety-critical applications where lost hardware is unacceptable, such as wheel hubs |
$$ |
Loctite |
High-vibration applications that need to retain preload and can tolerate adhesives |
$ |
Dry Patch |
Mid to high-vibration applications that want to eliminate the process step and variability of liquid adhesives |
$-$$ |
As we see above, there is a multitude of ways to prevent threads from coming loose under normal operations. However, it’s important to choose the right method for your application. While the chart above will help get you started, I recommend more research before deciding on your ultimate solution. When selecting your method, it helps to walk through these options with vendors and coworkers to match your application and get a close fit — then test a few different options to see what gives you the best blend of attributes.
Sourcing Simplified – Start Your Next Project With Fictiv
Whatever components you’re looking to secure, it’s likely they require some CNC machining to finish or produce in the first place. And Fictiv is your operating system for CNC machining that makes part procurement faster, easier, and more efficient. In other words, Fictiv lets engineers, like you, engineer. Create an account and upload your part to see what our instant quote process, design for manufacturability feedback, and intelligent platform can do for you.