Time to read: 5 min
UV-resistant plastics are specially formulated to withstand sunlight, a form of ultraviolet (UV) radiation. More specifically, these polymers resist UV degradation, a problem that can change a plastic’s physical appearance and mechanical properties. Visibly, the symptoms of UV degradation include yellowing, leaching, and bleaching. Mechanically, UV-degraded plastics exhibit brittleness and stress crack formation, and also have diminished strength, elasticity, and hardness.
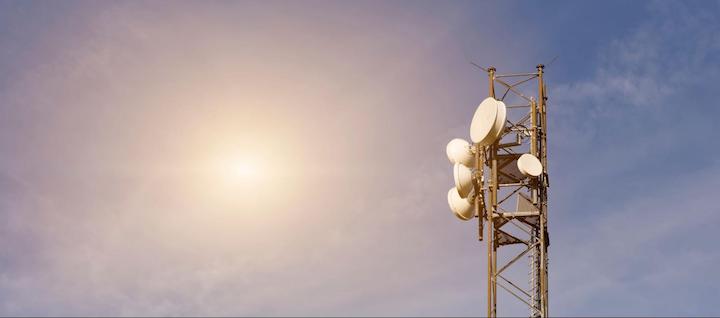
No plastic is 100% UV-resistant, but some have good UV stability in their natural state, while others require additives or coatings that impart UV resistance. There are two main types of UV additives: light stabilizers and UV absorbers, but carbon black, a fine black powder produced by the incomplete combustion of residues, is also used. Protective surface coatings such as paints or metallization can also provide UV protection, but they require secondary processes that add costs to materials and projects.
For part designers who need UV-resistant plastics, it’s crucial to balance UV stability against cost and to consider factors such as broader outdoor resistance and support for specific manufacturing processes. Whether you need UV-resistant plastics for 3D printing, injection molding, or CNC machining, Fictiv can help you with material selection and provides design for manufacturing (DFM) feedback along with your quote. Create a free Fictiv account if you’re ready to get started.
UV Resistant Plastics for 3D Printing, Injection Molding, and CNC Machining
Generally speaking, these are the top five UV-resistant plastics:
- Acrylonitrile Styrene Acrylate (ASA)
- High-Density Polyethylene (HDPE)
- Polycarbonate (PC)
- Polyamide-Imide (PAI)
- Polyvinylidene fluoride (PVDF)
The following sections describe each material’s properties and outdoor applications.
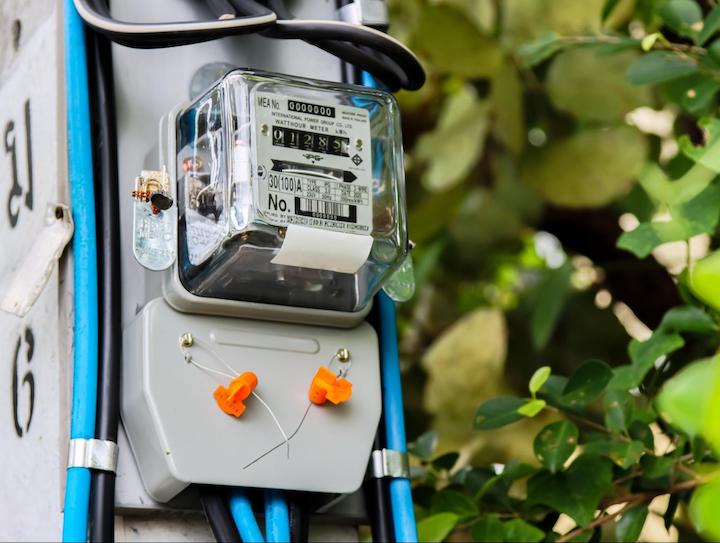
Acrylonitrile Styrene Acrylate (ASA)
ASA plastic is tough, strong, and resistant to impact, wear, and ultraviolet radiation. It also withstands weathering, heat, and weak acids and alkalis. ASA parts have glossy surfaces and retain their color, gloss, and mechanical properties even when exposed to outdoor environments. It’s easy to smooth layer lines after 3D printing, and this UV-resistant plastic is available as a resin for injection molding and as extrusions or co-extrusions that can be CNC machined. ASA’s main downside is that it absorbs moisture over time.
Applications for UV-resistant ASA include electrical housings, commercial siding, lawn furniture, sporting goods, and garden equipment. This UV-resistant plastic is also used in automotive applications ranging from exterior panels to side-view mirror housings. If you’re considering acrylonitrile butadiene styrene (ABS) plastic for your project, know that both ABS and ASA have similar mechanical properties — but without adding a UV stabilizer, ABS won’t resist ultraviolet degradation.
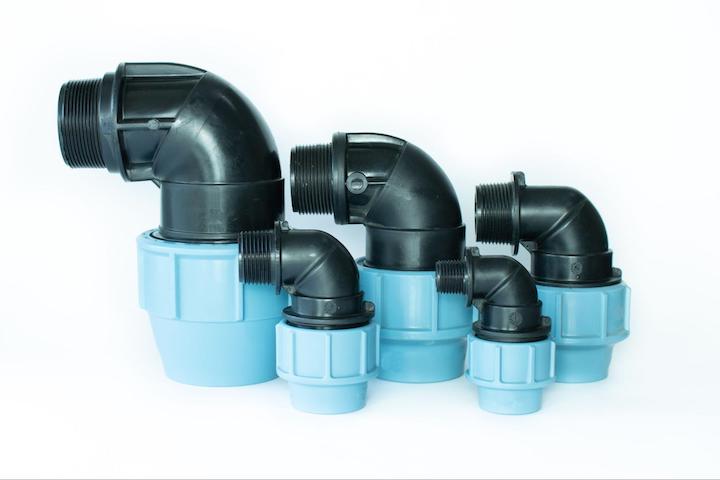
High-Density Polyethylene (HDPE)
HDPE plastic combines UV stability with strong and broad resistance to rain, wind, snow, and extreme temperatures. Unlike ASA, this UV-resistant plastic does not absorb water or moisture, which helps to prevent swelling, warping, or weakening of the material over time. Among its many advantages, HDPE is flexible, lightweight, and easy to recycle. Along with its excellent chemical resistance, HPDE provides exceptional impact resistance and can withstand mechanical stresses without breaking or cracking.
Applications for UV-resistant HDPE include playground equipment, outdoor furniture, agricultural containers, and water storage tanks. HDPE is also a popular construction material for outdoor structures and is sometimes called plastic wood, a product that has the appearance of natural wood without the risk of deterioration. Not all HDPE is designed for structural applications, however, so designers may need to consider flexural strength and compression strength along with UV resistance.
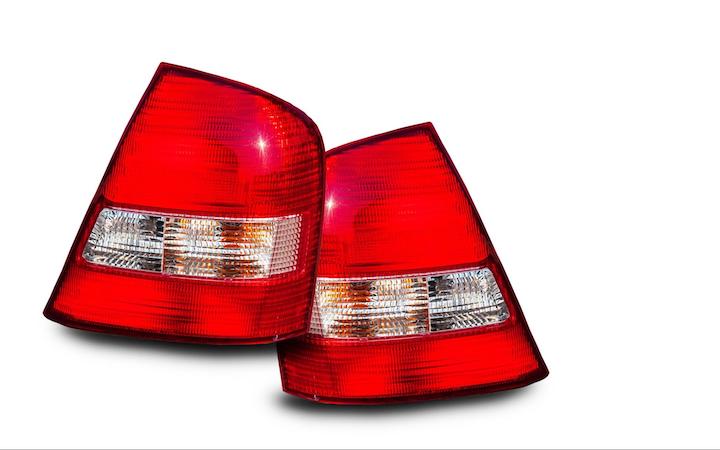
Polycarbonate (PC)
PC plastic provides greater impact resistance than HDPE and can withstand significant temperature changes. This UV-resistant material is also lightweight, easy to machine, electrically insulating, and fire-resistant. Although polycarbonate has a strength that’s 250 times greater than that of glass, PC is prone to scratching and is also more expensive than other UV-resistant materials. So, during material selection, part designers must balance polycarbonate’s UV stability against other considerations.
Applications for polycarbonate include outdoor signs and lighting systems. Special LED-diffusing grades of PC are designed to diffuse light from lamps that contain light-emitting diodes (LEDs). Structural applications for PC plastics include sunporches, carports, and other outdoor structures. With their excellent electrical insulation and ability to meet flammability requirements, polycarbonate materials are also used in electrical and electronic products, like outdoor switchgear in substations.
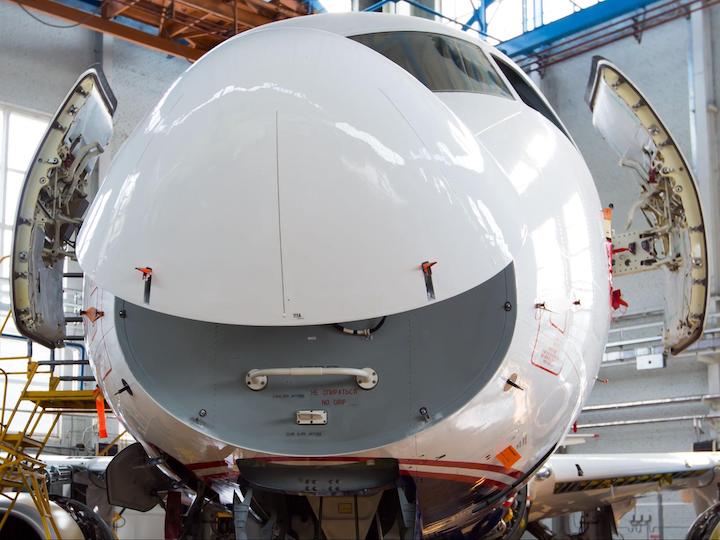
Polyamide-imide (PAI)
UV-resistant PAI combines UV stability with exceptional resistance to creep and wear. This high-performance plastic also has high levels of tensile strength and compressive strength for mechanical loading. Although PAI absorbs water and is mechanically rigid, it exhibits low thermal expansion and high thermal stability for dimensionally-stable components. PAI is used in 3D printing and has good machinability, but is relatively expensive and can be challenging to injection mold.
Applications for UV-resistant PAI include aerospace and automotive components and systems, electrical and electronic devices, and the green energy industry. In aerospace, PAI is used in fins, wings, antenna mounts, and radomes. Electrical and electronic applications include cables and connectors. In the green energy industry, PAI is used in large-scale battery power storage units that capture energy from wind or solar power for on-demand distribution.
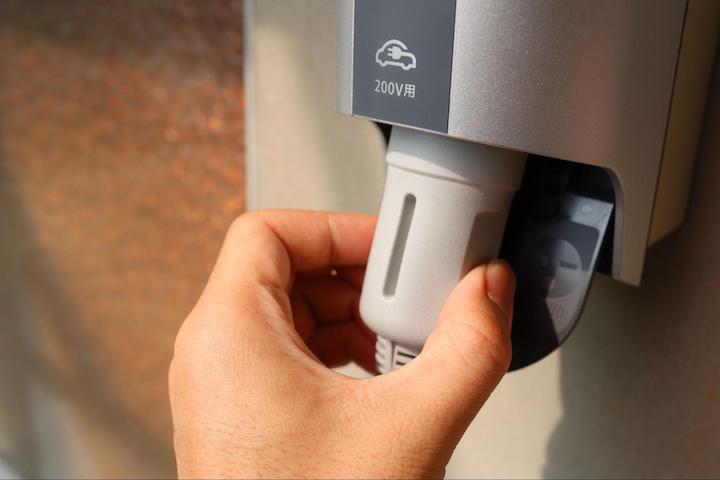
Polyvinyl Fluoride (PVDF)
PVDF is a high-purity plastic with excellent chemical resistance, flame resistance, and UV stability. There are two main types of PVDF plastics: homopolymer and copolymer. Homopolymer PVDF has greater stiffness and a higher heat deflection temperature than copolymer PVDF, which offers superior impact strength and stress crack resistance. Both types of material provide excellent thermal stability and have high fatigue resistance during cyclic loading.
Applications for UV-resistant PVDF include coatings for solar panels and outdoor building surfaces such as metal roofs, facades, and curtain walls. PVDF is also used in waterproof membranes, protective films, and outdoor electrical components for EV charging systems. Industries that use 3D printed, CNC machined, or injection molded PVDF include aerospace, automotive, sporting goods, petrochemical processing, and semiconductor equipment.
Fictiv Can Help You Choose the Right UV-Resistant Plastics
Here at Fictiv, our materials and manufacturing experts can help you pick the best plastic material for your next project. We work with a carefully vetted network of manufacturing partners who excel at 3D printing, CNC machining, injection molding, and urethane casting and are experienced working with a range of materials — which is especially important since some UV-resistant plastics are challenging to process. No matter how complex your design or the material you use, we’ll deliver the quality parts you need, fast. So, create a free Fictiv account and upload your part today to discover what our platform can do for you!