Time to read: 8 min
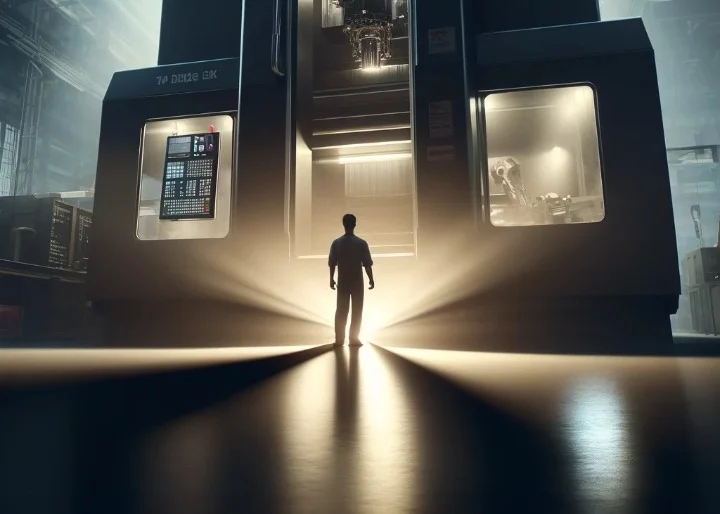
In the dynamic world of manufacturing, CNC machining stands at the forefront of innovation. This field is not just about shaping materials; it’s about shaping the future. As we delve into 2024 and beyond, the landscape of CNC machining is evolving rapidly, driven by technological advancements and industry demands.
Throughout this article, we’re using AI to help explore these exciting developments, highlighting their impact on various sectors, including robotics, healthcare, aerospace, automotive, and consumer products. We also spoke to several CNC manufacturing experts at Fictiv, who shared their own insights and experiences with specific advancements.
Present State of CNC Machining
Currently, CNC machining services are a critical backbone in manufacturing, known for precision, efficiency, and versatility. It’s a technology that has revolutionized how we produce mechanical parts, offering unparalleled accuracy and repeatability. As we navigate through a transformative era, CNC machining is not just keeping pace but setting new standards. It integrates with advanced technologies like AI and automation, paving the way for more intelligent, efficient, and sustainable manufacturing processes.
Navigating the Future Path of CNC Machining
As we look ahead to 2024 and beyond, the world of CNC machining is poised for remarkable transformation in the following areas:
- Innovative Advances: CNC machining is embracing a wave of technological advancements. Innovations in AI, automation, and data analytics are not just enhancing precision but also elevating the efficiency of manufacturing processes. These technological leaps promise to redefine the boundaries of what CNC machines can achieve.
- Materials and Tooling: The evolution in materials and tooling is a game-changer. We’re witnessing the adoption of stronger, lighter, and more sustainable materials. This shift is crucial for industries like aerospace and automotive, where material properties are pivotal.
- Sustainability and Environmental Considerations: The focus on sustainability is more pronounced than ever. CNC machining aligns with green manufacturing principles, minimizing waste and energy consumption. This commitment to the environment is a strategic business advantage.
Human-Machine Collaboration: The connection between human expertise and machine capabilities is strengthening. CNC operators are becoming more skilled in managing and optimizing these advanced machines, leading to enhanced productivity and innovation.
Each of these elements contributes to a more dynamic and efficient CNC machining landscape for industries that rely heavily on precision and innovation. Let’s take a closer look.
Pioneering Developments in CNC Machining
The latest technological advancements are reshaping CNC machining, from robotic automation to intelligent manufacturing, setting new benchmarks for precision and efficiency in the industry.
Automation and Robotics in CNC Machining: This advancement integrates sophisticated robotics with CNC systems, leading to automated tool changes and material handling. It significantly enhances production speed and reduces human error, making complex designs more feasible and efficient to produce.
Advances in Accuracy and Precision: Modern CNC machines incorporate high-resolution sensors and advanced control algorithms. This results in extraordinary precision, down to the micron level, which is essential in fields like medical device manufacturing, where minute details are critical.
Intelligent Manufacturing and IoT Integration: Internet of Things (IoT) integration allows CNC machines to be part of a connected network, enabling real-time data sharing and analysis. This connectivity ensures proactive maintenance, predicts potential issues, and optimizes operational efficiency, leading to smarter, leaner, and more adaptive manufacturing processes.
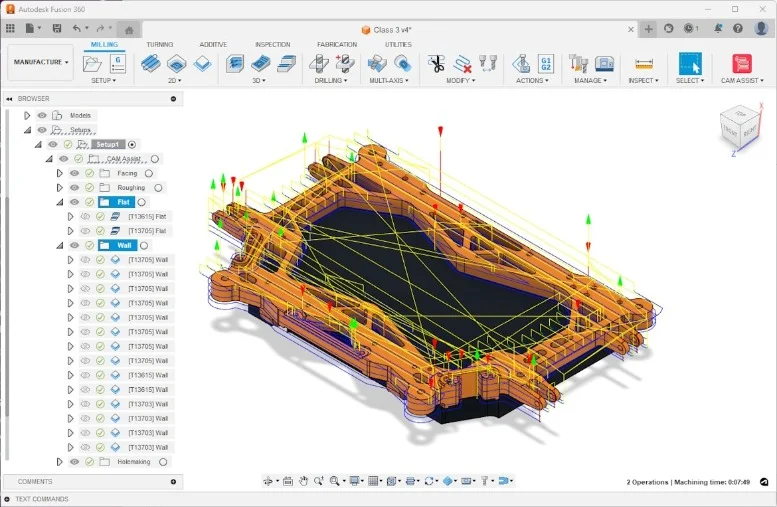
The CloudNC CAM Assist Automation Add-in for Fusion translates 3D models of 3-axis components into machining strategies in seconds. (Via Autodesk.)
Abhisek Das, a customer program manager at Fictiv, has witnessed the implementation and impact of AI in CNC manufacturing. “Specifically, AI co-pilots are being progressively used in computer-aided manufacturing (CAM) programs by machinists and for generative design in computer-aided design (CAD) packages by engineers.”
He points to Autodesk Fusion 360’s Generative Design, a powerful feature within the software that explores design alternatives based on specified constraints and objectives. Another example is CloudNC’s CAM Assist capabilities, which incorporate advanced algorithms and machine learning techniques to enhance the CAM process. It uses AI algorithms to automate and optimize the programming of CNC machine tools and analyzes 3D CAD models to generate efficient toolpaths, considering factors such as cutting forces, material properties, and machine capabilities.
“Innovations like these substantially reduce product development times and costs,” says Das. “They make design iterations shorter and the path to manufacturability smoother. They uncover solutions that may not cross an engineer’s mind, even with a first-principles approach, because the possibilities would literally be endless.”
Materials and Processes in CNC Machining
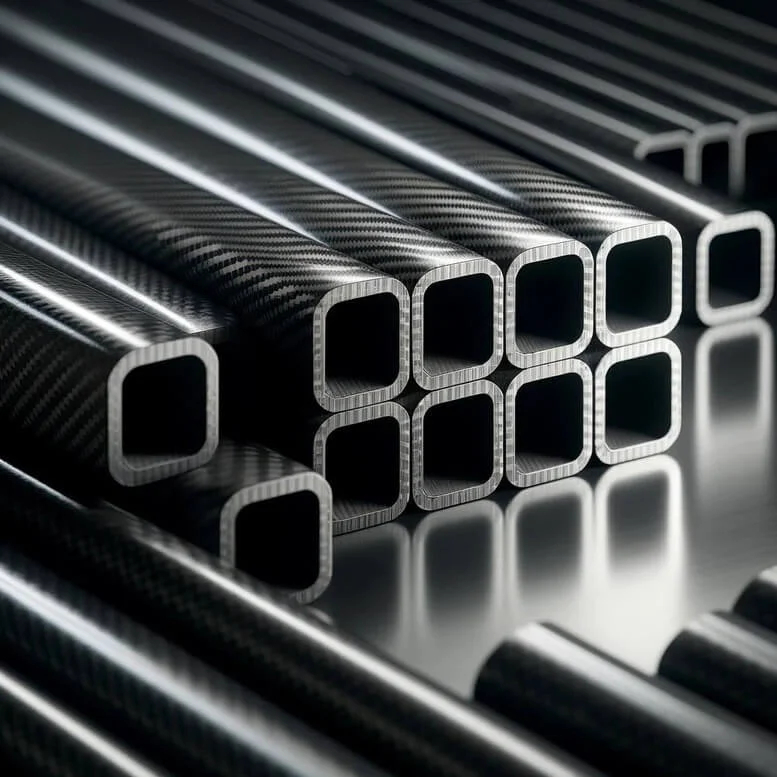
The future of CNC machining includes cutting-edge developments in materials and hybrid manufacturing processes that are setting new standards, heralding a new era of efficiency and innovation.
Advancement of Materials in CNC Machining: The inclusion of high-performance composites and advanced composite materials is a significant shift in CNC machining. Carbon fiber reinforced polymers (CFRP) and other fiber-reinforced composites are becoming increasingly popular due to their strength, lightness, and durability, making them ideal for demanding applications in aerospace, automotive, and robotics.
Tessa Axsom is the product marketing manager for Fictiv’s CNC machining services. She points out several advancements in CNC machining materials. “Society demands transportation that goes further, faster, and uses less energy,” she explains. “Materials scientists around the world have been tasked with designing or finding new materials that weigh less but are stronger. Superalloys are the sort of designer metal alloys that have improved creep and corrosion/oxidation resistance and have excellent mechanical properties when compared with traditional metal alloys. Superalloys like Hastelloy, Inconel, and A-286 have been increasingly popular in the aerospace, nuclear power, automotive, and chemical processing industries.”
Similar advancements are taking place in the aerospace and aeronautical industries, which have been pressured to remain competitive while reducing carbon emissions. “Superalloy metal matrix composites are basically metal alloys in a fiber matrix that have excellent thermal fatigue and corrosion resistance coupled with high strength. They can withstand high temperatures while staying lower on the density scale, making them perfect for applications like hot-end aerospace parts, naval ship components, and gas turbine engines,” Axsom explains. “However, here we have a situation where a material’s excellent performance properties make it difficult to machine. At high strength at high temperatures, these superalloy metal matrix composites are not good contenders for CNC machining, casting, or forging. So, many utilize them in 3D printing. My guess is that we will continue to see new innovations in materials as the pressure to be the lightest and fastest continues.”
Additive Manufacturing and CNC Hybrid Systems: This segment has seen remarkable growth with the integration of Laser-Based Additive Manufacturing, Directed Energy Deposition (DED), and Wire Arc Additive Manufacturing (WAAM). These technologies combine the precision of CNC machining with the versatility of additive manufacturing, enabling the creation of complex geometries that were previously unachievable. They offer improved material properties and the potential for significant cost and time savings in the manufacturing process.
Anup Kumar, a manufacturing engineer at Fictiv, is especially enthusiastic about conformal cooling through hybrid systems. “It’s particularly advantageous in the context of injection molding and forging die production,” he points out. It can improve cooling efficiency through intricate channel designs, reduce cycle times, and optimize part quality. This integration offers manufacturers greater design flexibility, material versatility, and cost-effectiveness in producing dies for these critical manufacturing processes.”
He’s also excited about the versatility and efficiency of hybrid systems, which are especially useful for parts repair. This enables manufacturers to quickly and cost-effectively restore damaged or worn-out components to their original functionality. Kumar explains, “By leveraging the strengths of both technologies, hybrid systems provide precise, high-quality repairs that meet the demanding requirements of modern industrial applications.”
Sustainability in CNC Machining
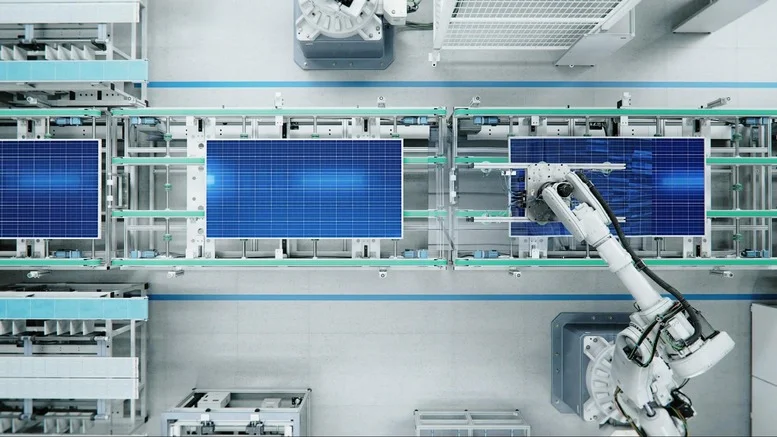
Sustainability is becoming a cornerstone in CNC machining as the industry shifts toward more eco-friendly practices. Let’s look at some of the latest sustainable initiatives and technologies.
Energy Efficiency in CNC Machines: Advanced motor technologies are being implemented for greater efficiency, while regenerative braking systems capture and reuse energy. Intelligent power management systems optimize energy use, reducing overall consumption and operational costs.
Waste Reduction and Recycling Initiatives: The industry is focusing on refining machining processes to reduce material wastage. Scrap material recycling is being prioritized, supporting circular economy practices and contributing to more sustainable production cycles.
Sustainable Materials and Practices: The shift to eco-friendly cutting fluids reduces environmental impact. Selection of sustainable materials for manufacturing and compliance with environmental certification standards are becoming increasingly important, reflecting the industry’s commitment to sustainable practices.
Fictiv’s Ashwin Kasirajan is a manufacturing engineer who notes that minimizing the usage and responsible disposal of coolant, as well as alternative and renewable energy implementations. “There are many advantages to implementing sustainable practices in CNC machining,” he explains. “Beyond the reduced environmental impact and regulatory requirements, these initiatives can help lower operating costs over time and enhance the company’s reputation with customers, investors, and other stakeholders.”
Challenges and Considerations in CNC Machining’s Future
In this section, we address the key challenges and considerations that are shaping the future of CNC machining:
Cybersecurity Concerns: The integration of CNC machines into digital networks raises concerns about data security, necessitating robust protective measures against cyber threats. Network vulnerabilities must be addressed to prevent unauthorized access and safeguard sensitive information. Additionally, protecting intellectual property in a digital landscape is vital to maintaining competitive advantages and industry integrity.
Skilled Workforce Shortages: The increasing technological complexity of CNC systems requires a workforce with specialized skills. This challenge is compounded by an aging workforce, emphasizing the need for targeted training and education programs to prepare a new generation of skilled workers.
Regulatory Compliance and Standards: Navigating the evolving landscape of quality standards, environmental regulations, and international guidelines is crucial. Adherence to these standards ensures product quality, environmental responsibility, and the ability to compete in global markets, making compliance a key factor in the industry’s future.
Each aspect presents unique challenges but also opportunities for innovation and advancement in CNC machining.
Market Outlook in CNC Machining
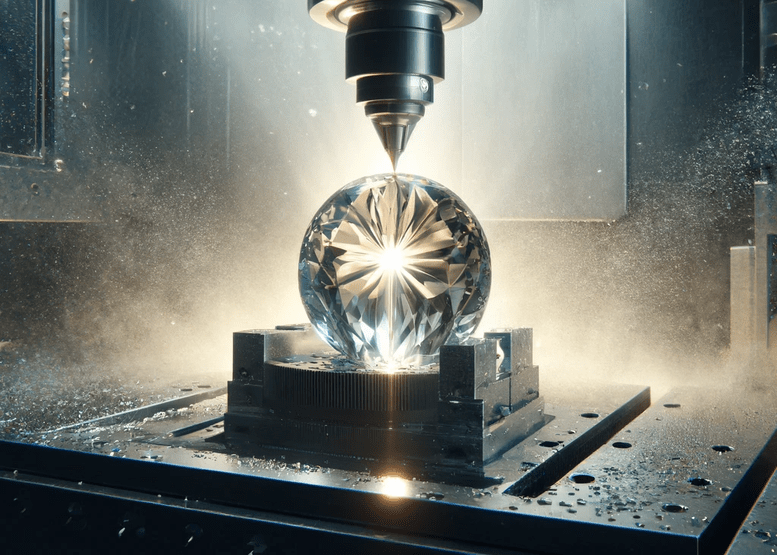
Let’s take a look at the impact of broader industry and economic trends on the future of CNC machining:
Growth Projections for the CNC Machining Industry: Anticipated continuous growth is driven by the industry’s eagerness to adopt cutting-edge technologies, enhancing efficiency and capabilities. This forward-looking approach positions CNC machining as a field ripe for ongoing development and innovation.
Emerging Markets and Opportunities: The aerospace and defense sectors are increasingly relying on CNC for precision parts, while the medical devices sector is turning to CNC for its demand for high-quality components. Additionally, the burgeoning electric vehicle market is presenting new opportunities for CNC machining, given its need for specialized parts.
Potential Disruptions and Major Advancements: The inclusion of additive manufacturing is set to revolutionize the industry, offering new ways to create complex parts. Quantum computing could drastically change manufacturing processes and efficiency. Furthermore, global supply chain dynamics are a pivotal factor, with shifts potentially impacting production strategies and market access.
Forging Ahead: Seize the Future of CNC Machining with Fictiv
We believe the future of CNC machining is vibrant and evolving, driven by technological advancements, sustainability efforts, and market dynamics. From automation and innovative materials to cybersecurity challenges and skilled workforce needs, CNC machining is at a pivotal point.
Partnering with Fictiv can help you navigate these changes. Our global manufacturing network, AI-powered technology, and broad capabilities, including CNC machining services, offer an ideal solution for companies looking to stay ahead in this dynamic industry. Working with Fictiv means embracing the future of manufacturing with confidence, innovation, and efficiency. Request an instant quote to get started.