Time to read: 5 min
PTFE, or Polytetrafluoroethylene, AKA Teflon®, is a unique material with a few physical properties that make it versatile enough for parts across various industries. One of these unique physical properties is a low coefficient of friction, which makes PTFE highly usefully in critical applications.
Understanding the coefficient of friction is fundamental knowledge that’s essential for engineers, designers, and manufacturers to optimize their processes, reduce wear and tear, and improve efficiency.
In this article, we will explore the significance of the coefficient of friction of PTFE in manufacturing, why PTFE has such a low coefficient of friction, and how PTFE’s unique properties make it an ideal material for various industrial applications.
Engineering Fundamentals Refresh: What is the Coefficient of Friction?
Here are all the facts you should know about the coefficient of friction if you’re designing for manufacturing or purchasing parts:
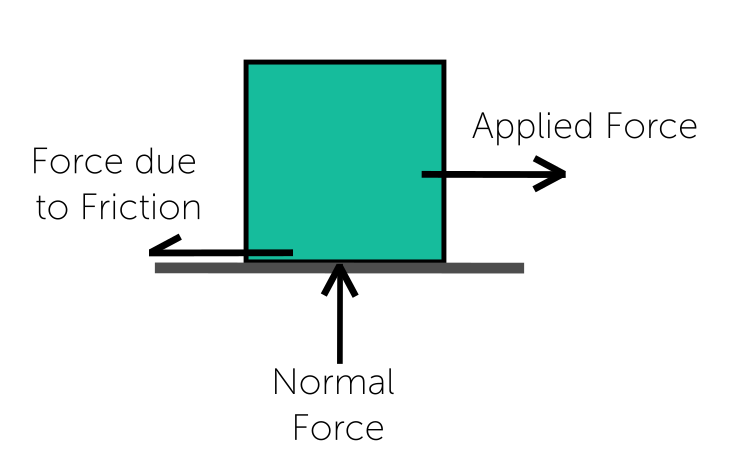
The force due to friction is one that opposes motion and occurs when two surfaces come into contact. This force is related to the weight of the object, the surface morphology, and texture of the two objects or surfaces in contact. This can be explained by the following equation (see previous image):
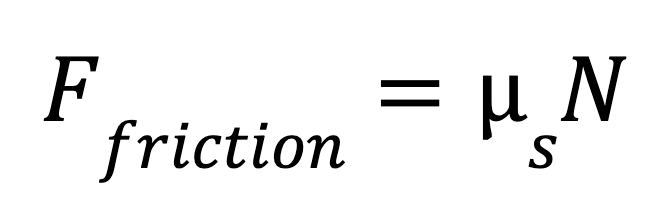
Whereby:
Ffriction is the force due to friction (force opposing the motion)
µs = static coefficient of friction (dependent on the two materials, dimensionless)
N = normal force that is equal to mass * force due to gravity (weight)
- The force due to friction is equal to the force you must put in to initiate movement of the object.
- The two types of friction are static and kinetic friction.
- Static friction is what you must overcome to initiate movement of an object on a surface where both objects or surfaces are at rest.
- Kinetic friction is the friction of movement between two surfaces that are in motion, with respect to each other.
- The value of the coefficient of friction depends on the nature of the two surfaces in contact and conditions such as temperature, humidity, and surface roughness.
You can (and should!) utilize the coefficient of friction of one material interacting with another to your advantage to either promote damage free movement or prohibit movement from occurring. Calculating the forces required to overcome friction is simple, and utilizing the correct material, surface treatment, or lubrication will go a long way to ensuring the longevity of your design.
A material with a low coefficient of friction will slide more easily over another material, because this lowers both the force due to friction and the force required to overcome it. PTFE has one of the lowest coefficients of friction of any known solid materials. In fact, it ranks number three for the lowest coefficient of friction — it’s slightly higher than diamond-like carbon, and double the coefficient for aluminum magnesium boride (the solid material with the lowest known coefficient of friction).
Why Does PTFE Have a Low Coefficient of Friction?
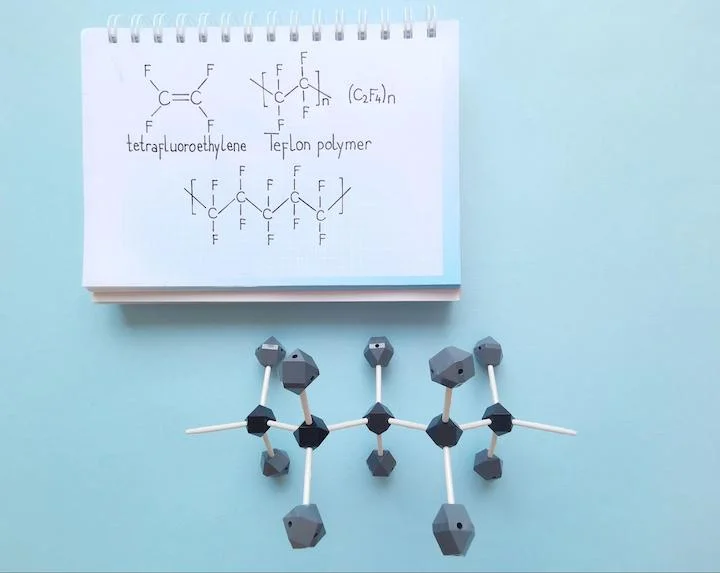
The reason why PTFE has such a low coefficient of friction can be found in its molecular structure. PTFE or Polytetrafluoroethylene is a synthetic fluoropolymer of tetrafluoroethylene, which means it is composed of carbon and fluorine atoms. The carbon and fluorine atoms form really strong bonds in the form of long chains, which makes PTFE resistant to thermal and chemical degredation.
The fluorine atoms in the PTFE compound completely surround the carbon atoms and form a protective barrier. Fluorine atoms are electronegative, which means that they work to repel any other atoms they come into contact with, which enables the sliding effect — and Teflon® is the only known surface to which a gecko cannot stick.
This sliding effect and electronegativity mean that Teflon® is also generally unreactive when exposed to chemicals. You can see scanning electron microscope images that show the long chains that make Teflon® so slick here.
Applications of PTFE Coefficient of Friction in Manufacturing
Logically, one of the most advantageous applications of PTFE is for CNC machined components that require a low coefficient of friction or must make contact with each other without degradation or wear and tear. The table below shows both the kinetic and static coefficients of friction for PTFE sliding on common surfaces:
Material Making Contact with a Teflon® Surface | Static Coefficient of Friction | Kinetic Coefficient of Friction |
Teflon® | 0.04 | 0.04 |
Teflon® with Grease | 0.04 | |
Steel | 0.05 – 0.2 | |
Wet Snow at 0C | 0.05 | |
Dry Snow at 0C | 0.02 | |
Nickel | 0.15 | 0.12 |
Aluminum | 0.19 | 0.18 |
Glass | 0.1 | 0.1 |
Titanium Vanadium (Ti-6Al-4V) | 0.23 | 0.21 |
PTFE in the Automotive Industry
Why is it used?
PTFE is commonly utilized in the automotive industry due to its thermal stability. long lifespan, leak-proofness, environmental resistance, and high temperature resistance for both interior and exterior components.
Common Automotive PTFE Components:
If you have a car, odds are that at least one part in that car is made of PTFE, including:
- braking system hoses, wear indicators, and clips
- interior weather stripping, fabric protection, and vents
- powertrain seals, head gaskets, and piston rings
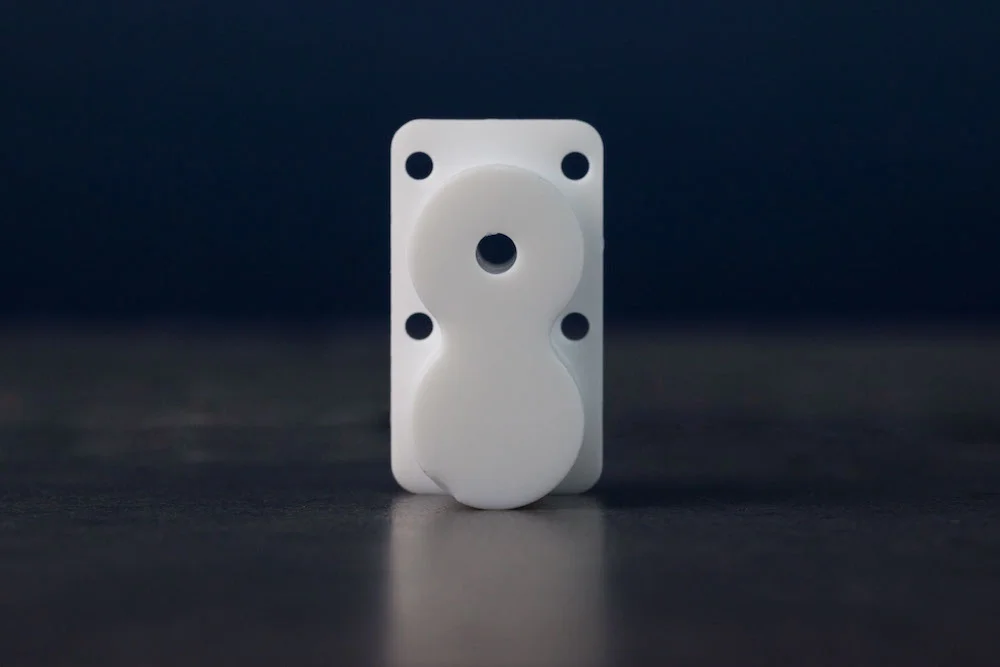
PTFE in the Electronics/Telecommunications Industry
Why is it used?
PTFE is commonly utilized in the electronics and telecommunications industries because it offers an improvement in electrical performance, chemical resistance, durability, and enhanced fire safety.
Common Electronics/Telecommunications PTFE Components:
PTFE is utilized for the following electronics/telecommunications parts:
- flexible circuit boards
- display screens
- wire and cable jackets
- cable insulation
- electro-wetting products
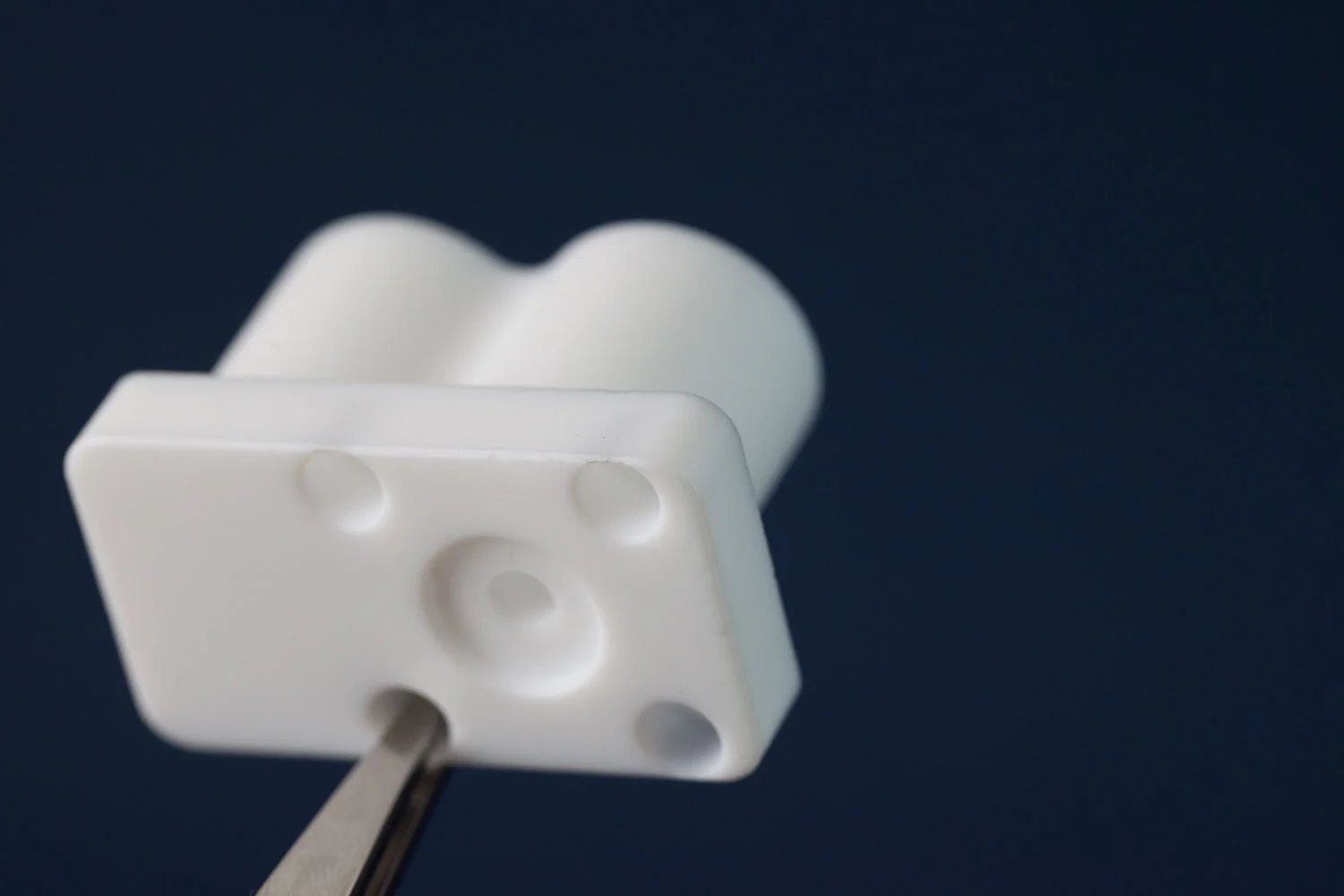
PTFE in the Medical Industry
Why is it used?
PTFE is commonly utilized in the medical industry because it is both biologically inert and biocompatible. With the development of PFOA-free PTFE, it is now safe to use versions of PTFE — such as ePTFE, a porous expanded PTFE — as medical implants.
Common Electronics/Telecommunications PTFE Components:
PTFE can be utilized for the following medical industry parts:
- implants
- syringe filters
- medical-grade fittings
- bulk tubing
- surgical instruments
- testing equipment
Other industries that utilize Teflon® components include:
- food and beverage
- construction
- chemical processing (like plating or surface modification)
- solar panel manufacturing
- packaging
Manufacturing PTFE Components with Fictiv
Now that you have a better understanding of the coefficient of friction and PTFE, we hope you’ll be able to confidently use the material in your next application — and Fictiv delivers quality PTFE components.
We commonly get requests for PTFE parts that are highly heat resistant and resist friction against solids — such as gears, gaskets, side plates, bearings — and for electrical components like connector assemblies. We can make PTFE parts in either white or black, and our network of manufacturing experts and machinists will ensure you get great results.
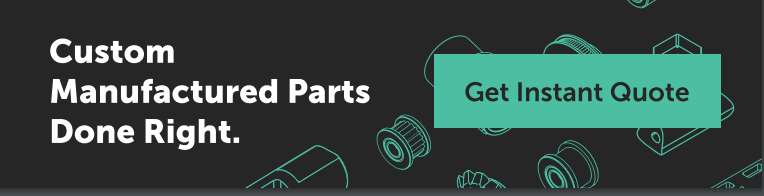
At Fictiv, we make custom manufactured parts at ridiculous speeds. Submit a part for an instant quote or create a free online account today!