Time to read: 7 min
As sustainability becomes a greater priority, the plastic manufacturing industry is undergoing a shift to adapt to the changing times. With mounting environmental pressures and a global push for greener solutions, sustainable plastic manufacturing redefines how we produce everyday goods.
At the center of this transformation lies injection molding, one of the most common manufacturing processes for mass-produced plastics. Sustainable plastics, designed to minimize ecological harm through renewable sourcing, recyclability, or biodegradability, are driving this change.
In injection molding, this means adopting eco-friendly materials such as biodegradable or recycled plastics and reducing waste. At the same time, these trends must ensure the production of high-quality products while advancing environmental integrity, with energy efficiency optimized through improved machinery and process design.
This article dives into sustainable plastic manufacturing, spotlighting advancements in eco-friendly injection molding and offering actionable insights for mechanical engineers, manufacturing professionals, product designers, and advocates eager to embrace innovative plastics and sustainability.
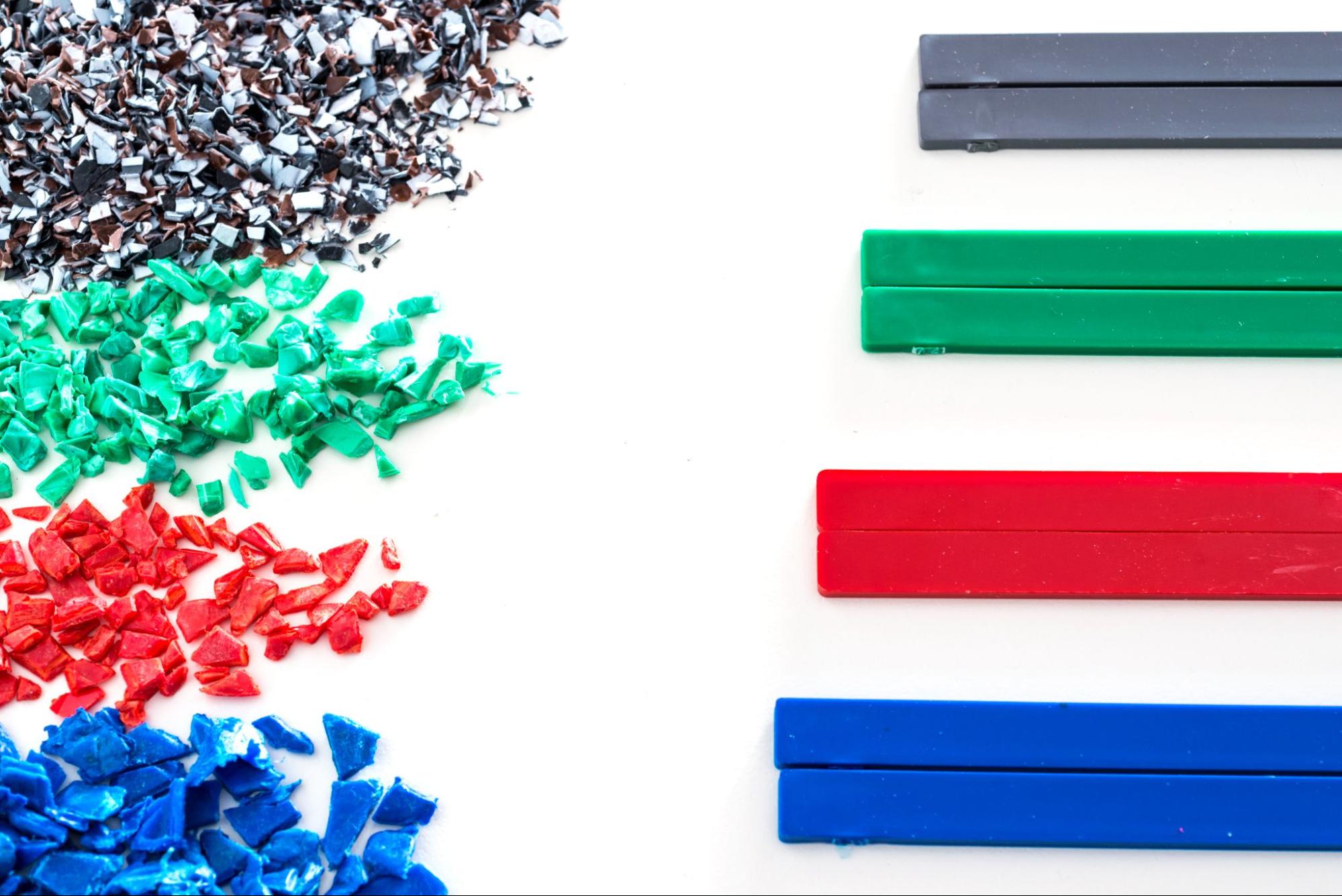
Key Strategies for Sustainable Plastic Manufacturing in Injection Molding
Sustainable plastic manufacturing in injection molding requires a strategic approach to minimize environmental impact while maintaining performance and efficiency.
Material Selection
Picking the right materials is the foundation of sustainable injection molding. Using recycled plastics, biodegradable options, or bio-based resins is key. Sustainable, high-surface-energy plastic adds strength for tough jobs while staying eco-friendly. Additives like biodegradable enhancers can also improve sustainability without lowering quality.
Process Optimization
Using less energy is a key part of sustainable plastics manufacturing. Modern machines with features like variable-speed drives and better heating systems can cut energy use by up to 30%. Ongoing innovation in material science leads toward sustainable plastics that can be molded at significantly lower temperatures. Optimizing cycle times and temperatures further cuts consumption, aligns cost savings with environmental gains, and makes injection molding a leader in eco-friendly production.
Waste Reduction
Reducing waste is a major goal in sustainable injection molding. While traditional thermoplastics can be reground—meaning scrap plastic is shredded and reused to keep it out of landfills—sustainable materials like post-consumer resins (PCRs) go a step further. These plastics incorporate waste that would otherwise go unused, helping to drive the circular economy.
Closed-loop systems take this to the next level by recycling waste back into the production process, creating a cycle that minimizes trash. This approach strengthens plastics and sustainability by maximizing material reuse.
Design for Sustainability
Designing parts with sustainability in mind can save materials without losing quality. For example, simpler designs use less plastic, and modular designs allow products to last longer. Using sustainable high-surface-energy plastic can also make parts more durable, reducing the need for replacements. These design choices support sustainable plastics manufacturing from the very start.
What Are Sustainable Plastics?
Sustainable plastics are materials crafted to lessen environmental impact, often derived from renewable resources or engineered for recyclability and biodegradability. Ideally, they are not created from petroleum byproducts.
Unlike traditional plastics, which often rely on finite fossil fuels and contribute to pollution, sustainable plastics aim to curb carbon emissions, conserve resources, and reduce waste. They encompass several types:
- Biodegradable Plastics: Materials like polylactic acid (PLA) and polyhydroxyalkanoates (PHA) decompose naturally, cutting down long-term pollution.
- Recycled Plastics: Post-consumer resins (PCRs) and plastic regrind (or reprocessed scraps from prior molding) reduce the need for virgin materials. Thermoplastics can be recycled and reused.
- Bio-Based Polymers: Sourced from plants like corn or sugarcane, these plastics offer a lower carbon footprint than petroleum-based counterparts.
Sustainable plastics in manufacturing help reduce plastic waste and lower the carbon footprint of production. By integrating these materials, manufacturers align with regulatory demands and consumer preferences for environmentally friendly products.
The non-biodegradable nature of traditional plastics leads to discarded products taking hundreds of years to decompose. During this period, the deteriorating integrity of the original plastic items leads to microplastic contamination, now known to be detrimental to humans and wildlife alike.
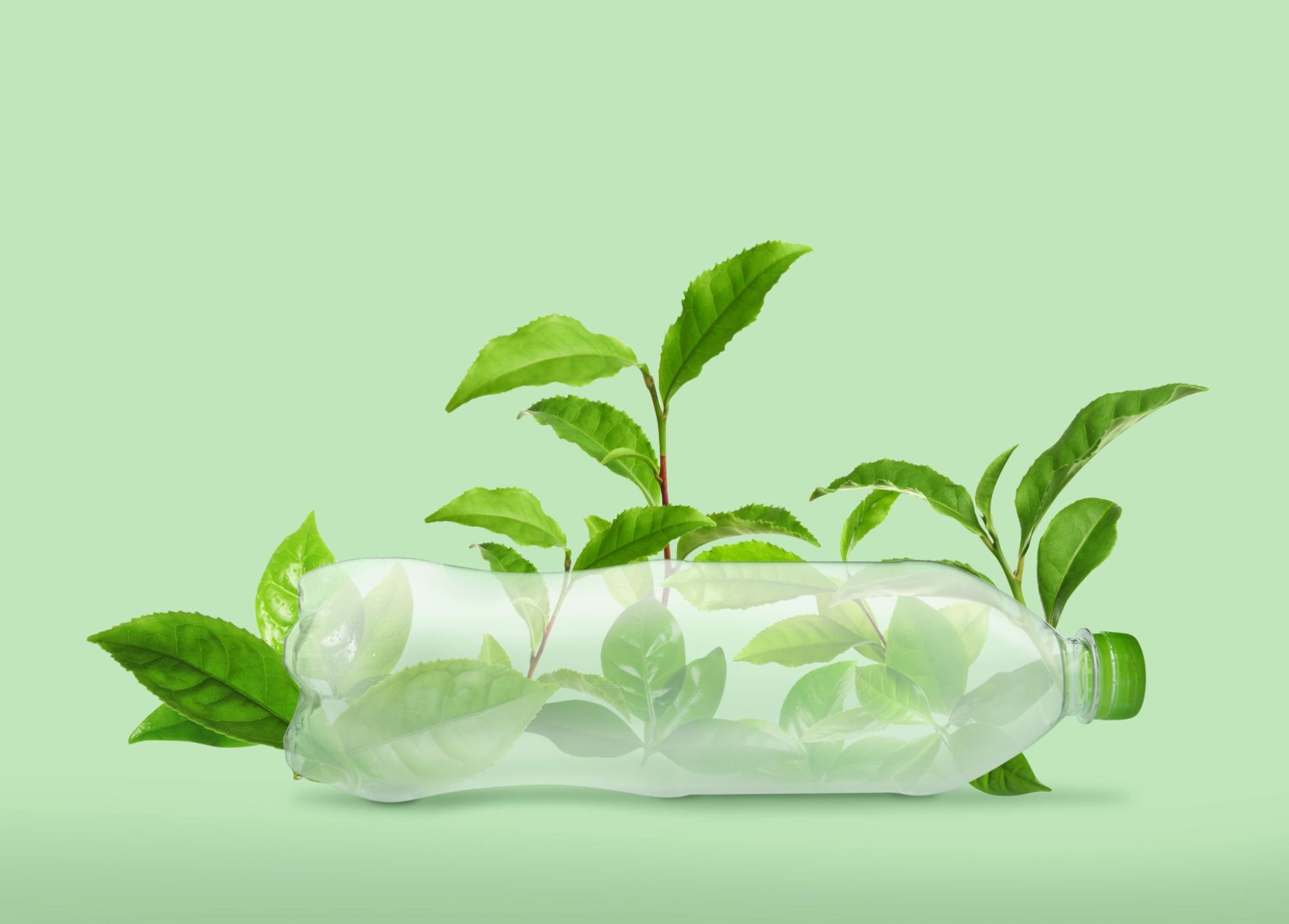
Sustainable Materials for Injection Molding
As the demand for eco-friendly solutions grows, manufacturers are using materials like biodegradable plastics and recycled resins in injection molding. These materials reduce waste and carbon emissions while maintaining product quality, paving the way for greener manufacturing.
Recycled Plastics and Post-Consumer Resins (PCRs)
Recycled plastics, including post-consumer resins (PCRs) and plastic regrind, are vital for sustainable manufacturing. PCR comes from used plastics like bottles or packaging, while plastic regrind is made from manufacturing scraps ground into pellets for reuse.
Unlike virgin plastics, which emit 2–3 kg of CO2 per kg during production, recycled plastics can reduce emissions by up to 60%, often to 0.8–1.2 kg of CO2 per kg. This reduction is achieved by minimizing raw material extraction and leveraging reprocessed materials, despite minor emissions from collection and sorting.
Additionally, biodegradable plastics like polylactic acid (PLA) can further cut energy use, requiring lower processing temperatures (160–180°C) compared to traditional plastics like polyethylene or polypropylene (200–250°C). Recycled polyethylene terephthalate (rPET) is used for bottles, while recycled polypropylene (rPP) can be used for containers, packaging, and even automotive parts.
However, ensuring consistency requires careful sorting to remove contaminants, as impurities can affect color or strength, posing challenges for quality control in injection molding. Nevertheless, recycled plastics lower costs and environmental impact, advancing plastics and sustainability.
Bio-Based Plastics
Bio-based plastics like polylactic acid (PLA) and polyhydroxyalkanoates (PHA) are derived from renewable sources such as corn or bacteria, reducing reliance on fossil fuels in sustainable injection molding. PLA production emits 50% less greenhouse gas than conventional plastics, while PHA can biodegrade in marine environments, helping curb ocean pollution.
Both are compostable, cutting landfill waste, but often require industrial composting facilities. PLA needs temperatures above 60 °C to break down efficiently, a challenge for widespread use. Production can also strain agricultural resources, with PLA requiring 0.5–1 hectare of land per ton, potentially impacting food security.
Blending bio-based plastics with recycled resins can improve flexibility or heat resistance, making them suitable for packaging, medical implants, or agricultural films. These materials support sustainable plastic manufacturing by offering an eco-friendly alternative to petroleum-based plastics.
Sustainable High-Surface-Energy Plastic
Sustainable high-surface-energy plastics improve adhesion and durability in injection molding. This makes them ideal for applications like automotive dashboards and medical packaging that require coatings or bonding. They are often derived from bio-based or recycled sources and support sustainability goals without compromising performance.
Their high surface energy enables strong bonds with paints or adhesives, reducing the need for energy-intensive surface treatments and extending product life by preventing wear and peeling. For instance, recycled polyethylene-based versions can cut emissions by 40–50% compared to virgin plastics.
However, achieving both high surface energy and toughness can be challenging, as increased brittleness may require additives. While sourcing these materials can be more expensive, their durability and environmental benefits make them a wise choice for sustainable plastic manufacturing.
Comparing the Environmental Impact of Different Plastics
A life cycle assessment (LCA) reveals key differences. Virgin plastics have a high carbon cost, while recycled plastics cut emissions by 60%. Bio-based plastics reduce fossil fuel use but may strain agricultural resources.
Sustainable high-surface-energy plastic offers a 40–50% reduction in emissions, balancing durability with eco-friendliness and guiding manufacturers in optimizing sustainable plastic production.
The Role of Injection Molding in Sustainable Plastic Manufacturing
Injection molding is a linchpin in plastic production, prized for its ability to efficiently create intricate, high-quality parts. Yet, traditional methods often depend on virgin plastics and energy-hungry machinery, leaving a hefty environmental footprint.
Sustainable plastic manufacturing can help alter this undesirable situation by optimizing injection molding with eco-friendly practices. A sustainable future for injection molding leverages materials like biodegradable plastics, recycled polymers, and bio-based resins, alongside ongoing strategies to improve energy efficiency and reduce waste.
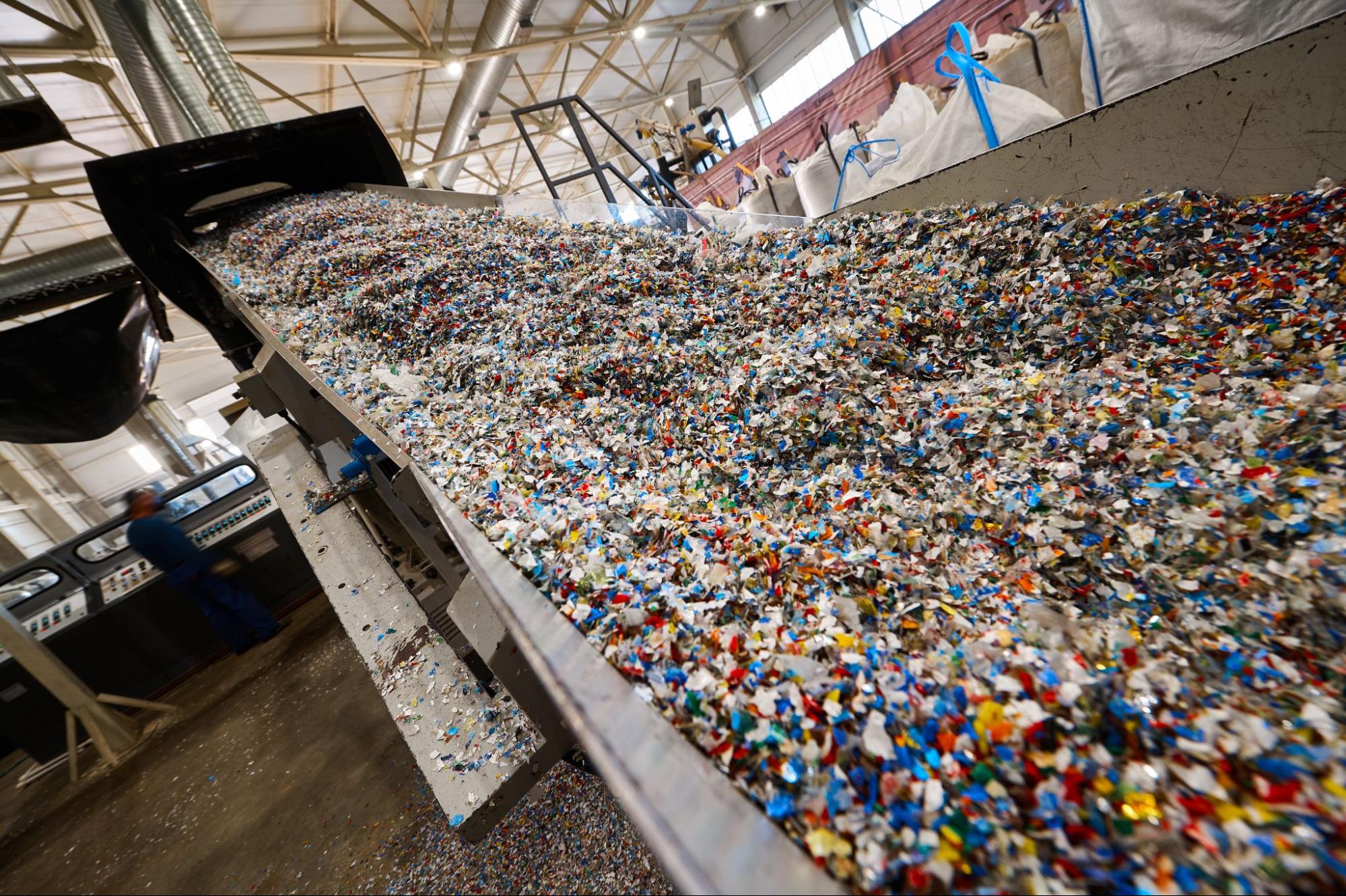
Challenges and Considerations in Sustainable Injection Molding
Below are some of the challenges and considerations in sustainable injection molding:
Cost Implications
Sustainable materials like bio-based resins or sustainable high-surface-energy plastics can carry higher upfront costs. Yet, long-term savings from energy efficiency and waste reduction—particularly with recycled plastics like post-consumer resins (PCRs) that repurpose discarded materials and reduce raw material expenses—often offset this. These savings are further bolstered by government incentives. Sustainable plastic manufacturing thus becomes a strategic investment with economic and ecological returns.
Performance Trade-Offs
Biodegradable plastics might not be as strong as traditional ones, so designs may need to be adjusted. Mixing sustainable and traditional materials can help, while sustainable high-surface-energy plastic offers a strong, eco-friendly option. These solutions ensure that sustainable plastics manufacturing meets industry standards.
Regulatory Compliance and Certifications
Compliance with standards like ISO 14001 validates sustainability efforts. These frameworks ensure market access and avoid penalties, though they demand thorough audits. Sustainable plastic manufacturing thrives under such scrutiny, meeting regulatory and consumer demands for eco-friendly products.
The Future of Sustainable Plastics and Injection Molding
The future of sustainable plastic manufacturing brims with potential. Compostable plastics are gaining traction, while low-energy machines reduce emissions, paving the way for greener production. Ongoing research into bio-based blends promises breakthroughs, and sustainable high-surface-energy plastics are expanding applications for durable, eco-friendly products.
Beyond technology, growing consumer demand for sustainable goods has heightened awareness of the environmental toll of microplastics, and the momentum of circular economy initiatives is driving change. As material science advances and regulatory frameworks evolve, potentially tightening around 2030, sustainable injection molding is poised to become an industry standard, advancing plastics and sustainability in tandem.
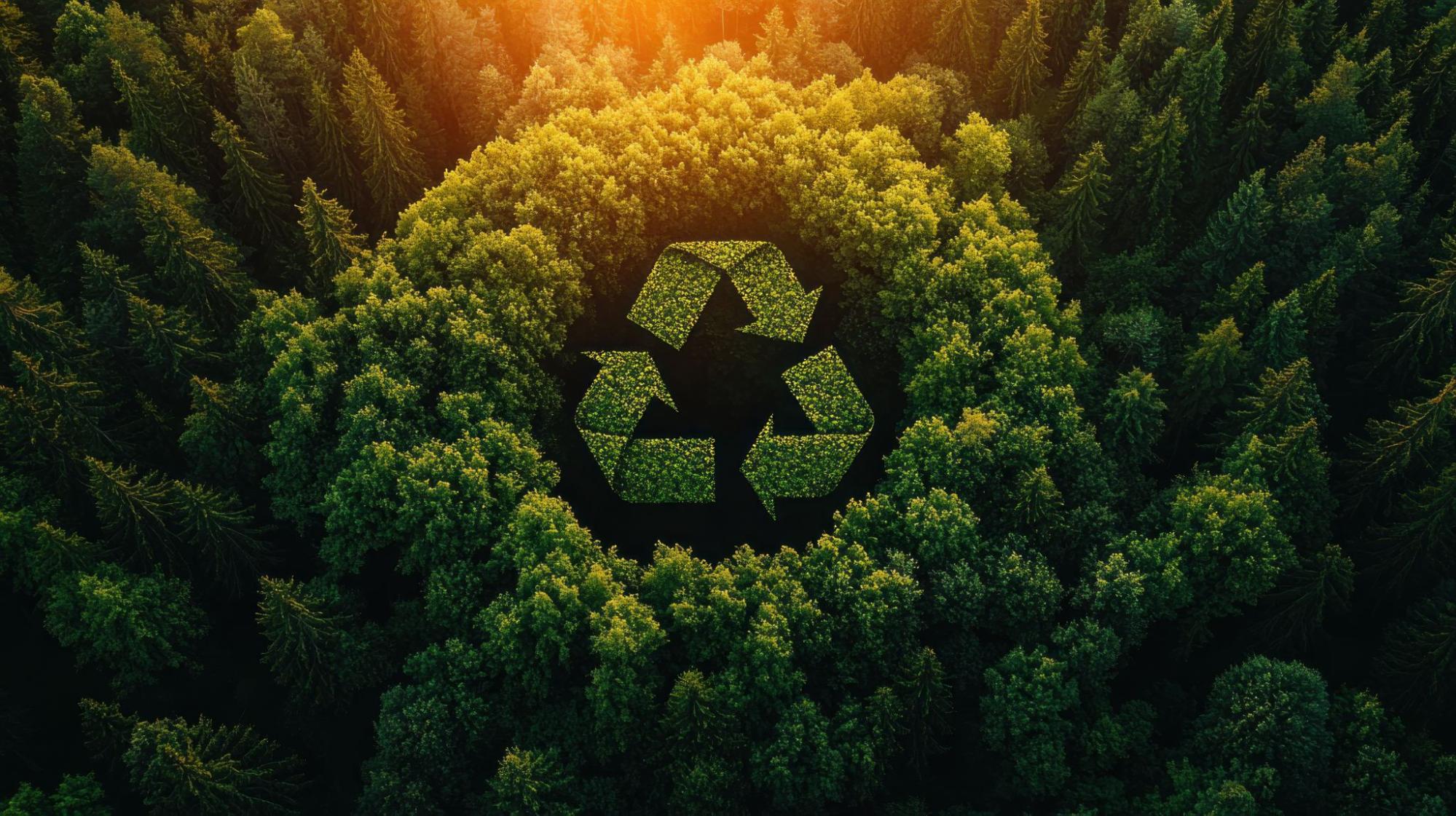
How Digital Manufacturing Supports Sustainable Plastics
Digital tools are making sustainable injection molding even better. Cloud-based systems support sustainable injection molding by optimizing shipping routes for eco-friendly materials, thereby reducing emissions tied to their transport.
AI tools help design parts that use less material from the start. Fictiv’s digital platform, for example, connects companies with suppliers who use eco-friendly materials and focuses on reducing waste, showing how technology can boost plastics and their sustainability.
Driving Sustainability in Injection Molding: Innovation Meets Responsibility
Sustainable plastic manufacturing bridges environmental stewardship with industrial prowess, especially via injection molding. The use of recycled plastics, bio-based resins, energy-saving processes, and smart designs shows that eco-friendly and profitable production is possible.
As plastics and sustainability take center stage, manufacturers adopting these practices will shape a greener, more responsible future. Fictiv supports this shift with digital solutions that optimize sustainable injection molding, offering a glimpse of what’s possible when innovation meets customer expectations.
Ready to green your plastic manufacturing process? Fictiv’s digital platform and network of experts support sustainable injection molding with recycled materials, optimized designs, and reduced waste. Get a quote today and see how we can help craft high-quality, sustainable plastic parts.