Time to read: 9 min
Globally, the medical device industry has a compound annual growth rate (CAGR) of 6.2% and is expected to reach sales of USD $1.025T by 2032. Medical device companies that streamline and scale production can meet growing demand while maintaining quality. Innovative technologies can help, but there are proven strategies that successful companies pursue.
This article describes these strategies and the role of artificial intelligence, machine learning, automation, robotics, and rapid prototyping in medical manufacturing. You’ll also find tips, trends, and some advice about picking the right partner. Keep reading to learn more.
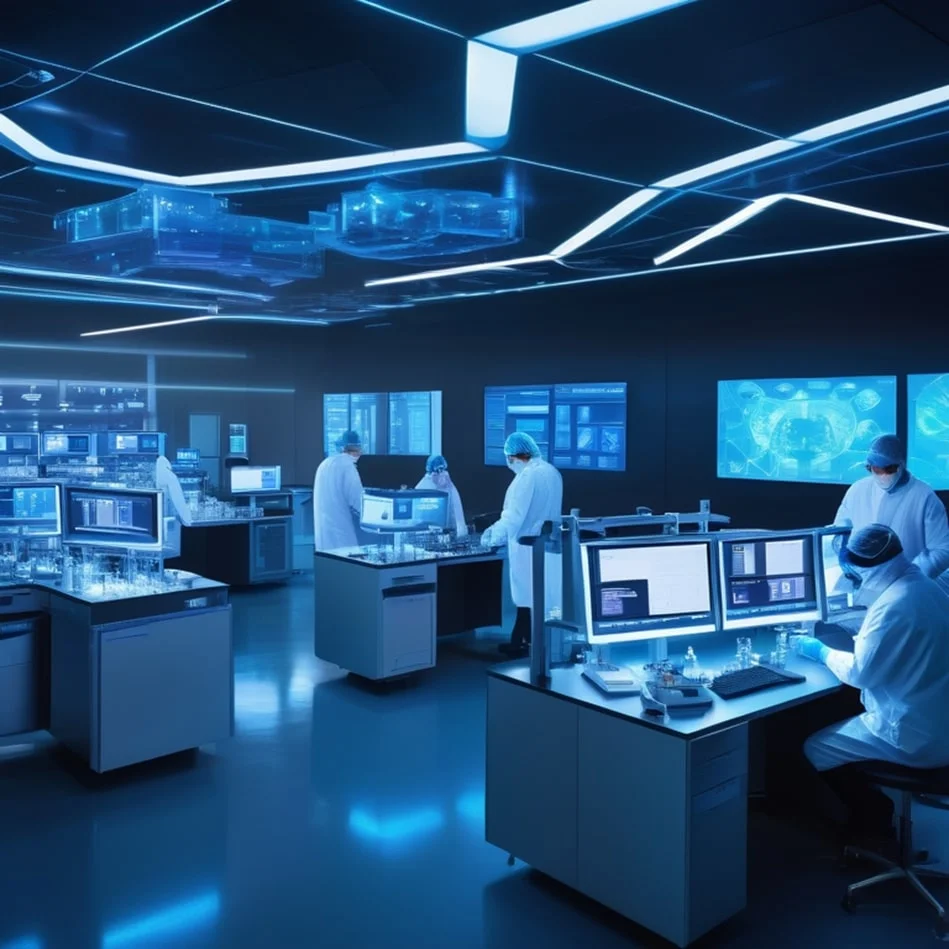
Streamlining vs. Scaling in Medical Production
Medical device companies that successfully streamline and scale production can control costs, optimize resources, produce units more efficiently, and introduce and iterate products more quickly than competitors. Streamlining and scaling are related concepts, but they’re not exactly the same.
Streamlining
Streamlining is the process of simplifying or optimizing production workflows to increase efficiency, reduce waste, and improve productivity. As part of this process, it’s important to implement quality control measures that identify and address defects early in the production process. Otherwise, rework and scrap can reduce your profitability.
Scaling
Scaling refers to how companies rapidly increase (or decrease) production in response to changing market demand. In the medical industry, scaling requires the design and implementation of systems and processes that can be adjusted without compromising quality. By streamlining production workflows, it’s easier to make these changes.

Medical Manufacturing Challenges
For medical device companies, there are two major challenges to consider during scale-up.
- Regulatory requirements
- Maintaining quality across higher volumes
The following sections explain.
Regulatory Requirements
The main challenge in scaling medical production is ensuring compliance with regulatory requirements while maintaining quality. Successful medical device companies navigate these complex regulatory frameworks while optimizing manufacturing and operations.
Regulatory requirements can be demanding and diverse. For example, a company that wants to sell its medical device in the United States must meet U.S. Food and Drug Administration (FDA) regulations. In the European Union, CE marking is required instead. The CE in CE marking stands for “Conformité Européenne,” which is French for “European conformity.”
Both the FDA and the EU’s Medical Device Regulation (MDR) divide medical devices into three numbered classes. Yet there are differences. For example, the EU MDR further divides Class II medical devices into medium-risk (Class IIa) and high-risk (Class IIb) devices.
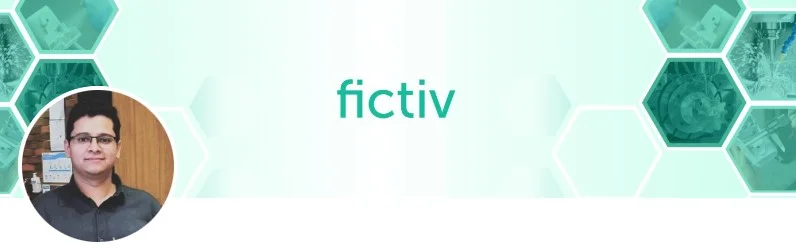
Managing Large-Scale Operations
As demand increases, medical device companies must ensure they can produce more products while maintaining the required level of quality. Variations in materials and processes, supply chain issues, and workforce challenges can all increase with expanded production.
High-volume manufacturing also generates large amounts of data, and managing and analyzing this information is essential for identifying and addressing quality issues. Inspecting and testing every product in a high-volume run may be impractical, but sampling could miss issues with untested units.
Additional Challenges
Depending on the manufacturing partner, medical device companies could face additional challenges.
- Low-volume manufacturers that can support you during product launch may not be able to grow with you as demand increases.
- High-volume manufacturers may not want to work with you while initial demand for your product is low.
- Domestic manufacturers are sometimes more expensive, and the part volumes you need may require higher cost, specifications-grade materials.
- Offshore manufacturers may cost less, but offshoring can raise concerns about quality, a lack of visibility, increased shipping costs, and tariff concerns.
Overcoming these challenges takes a combination of innovative technologies and strategies. It also helps to partner with Fictiv because we simplify sourcing and can support you from the back of the napkin sketch through prototyping, and from low-volume to high-volume production.
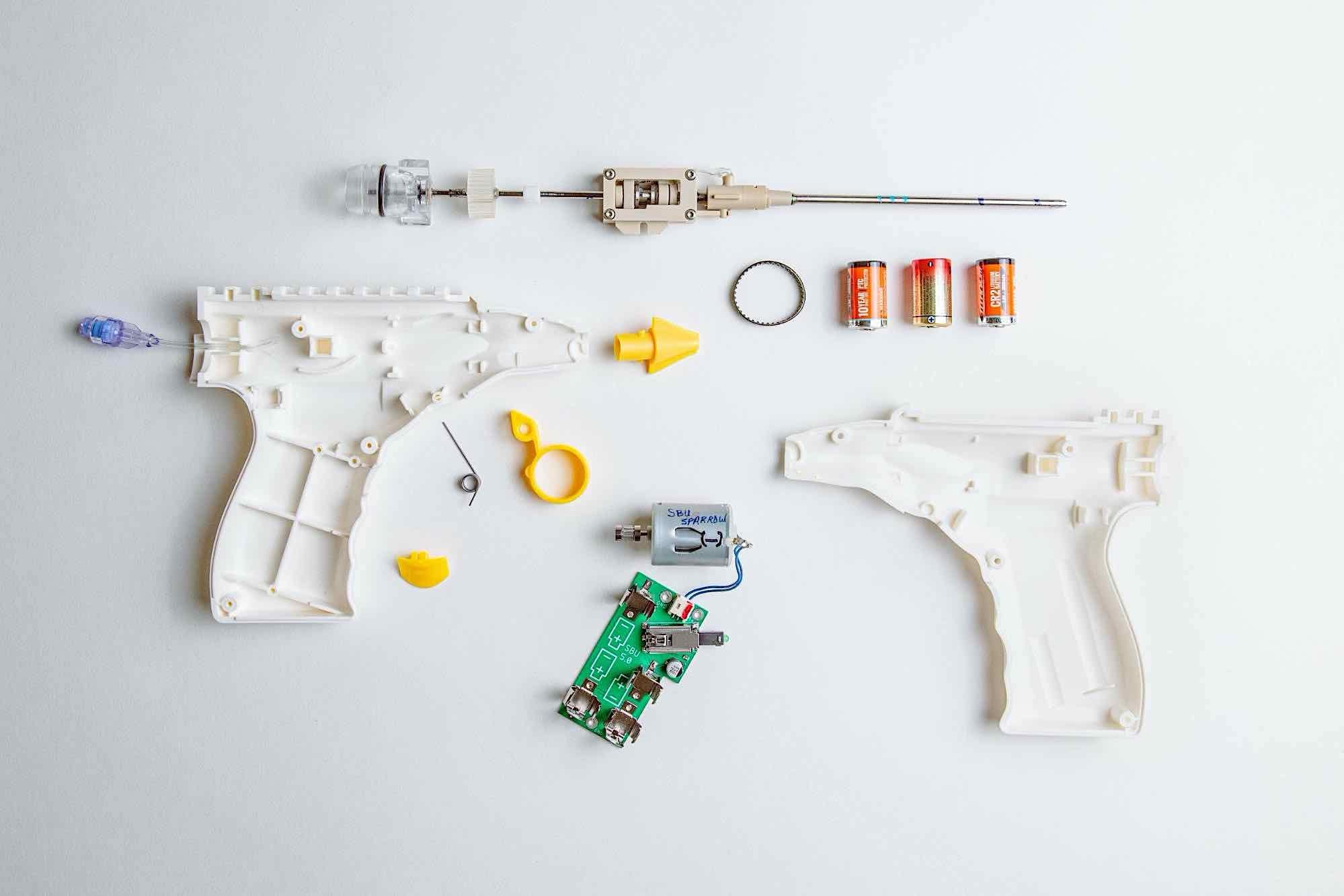
Customer Case Study: TransMed7
Transmed7 is a medical device company that needed a faster and more cost-efficient way to iterate its product designs. The Portola Valley, California firm also wanted a partner who could seamlessly scale to meet customer demand. Transmed7 leveraged Fictiv’s 3D Printing, CNC Machining, and Injection Molding capabilities.
As Gene Vetter, Co-Founder & CEO of TransMed7 said, “Fictiv enabled us to save millions of dollars in infrastructure, people, and time costs when compared to traditional development and supply chain strategies. Moreover, Fictiv helped Transmed save eight years of product development time on the company’s first two devices.
Innovative Technologies for Streamlining and Scaling
Medical companies like Transmed7 can face multiple challenges, but innovative technologies can help to streamline and scale production. Examples include:
- Artificial intelligence (AI)
- Machine learning
- Automation
- Robotics
- Rapid prototyping
The following sections explain.
Artificial Intelligence and Machine Learning for Data-Driven Insights
Today, medical companies are designing AI-powered diagnostic systems that can analyze patient data, detect patterns, and provide real-time insights. This enables faster, more accurate, and repeatable diagnoses, enhancing patient outcomes and optimizing healthcare costs. Adaptive machine learning algorithms help to improve diagnostic accuracy over time.
Yet AI and machine learning can also optimize medical manufacturing itself. By analyzing data and identifying patterns, medical manufacturers adjust processing parameters in real time. In addition, AI and machine learning support predictive maintenance for reduced downtime.
The table below describes some medical applications of AI and machine learning.
Application | Description |
---|---|
Diagnostic Imaging | AI algorithms analyze medical images, aiding in the detection and diagnosis of disease. |
Predictive Maintenance | Machine learning predicts equipment failures, helping to reduce downtime and optimize maintenance. |
Quality Control | AI-powered systems enable real-time quality checks, ensuring compliance with standards and reducing defects. |
Supply Chain Optimization | Machine learning algorithms optimize inventory levels, predict demand, and streamline logistics processes. |
Automation and Robotics
Automation and robotics also help medical device companies streamline and scale manufacturing. By reducing or eliminating the need for manual intervention, automation minimizes the risk of human error. Automated systems also perform repetitive tasks with greater accuracy, ensuring consistent part quality regardless of production volume.
Today, automated injection molding is used to produce plastic medical parts. Insert-loading robots place inserts into the mold before injection, part removal robots extract finished parts from the mold, and secondary operation robots handle tasks such as trimming, assembly, and packaging. Automated conveyors transport parts and materials within the factory.
Automated CNC machining also supports greater production efficiency and higher part volumes. For example, robotic arms are used to load and unload metal workpieces. Automated tool changers switch CNC tools during operations without human intervention. Pallet systems, conveyors, and automated retrieval and storage systems (AS/RS) are also used.
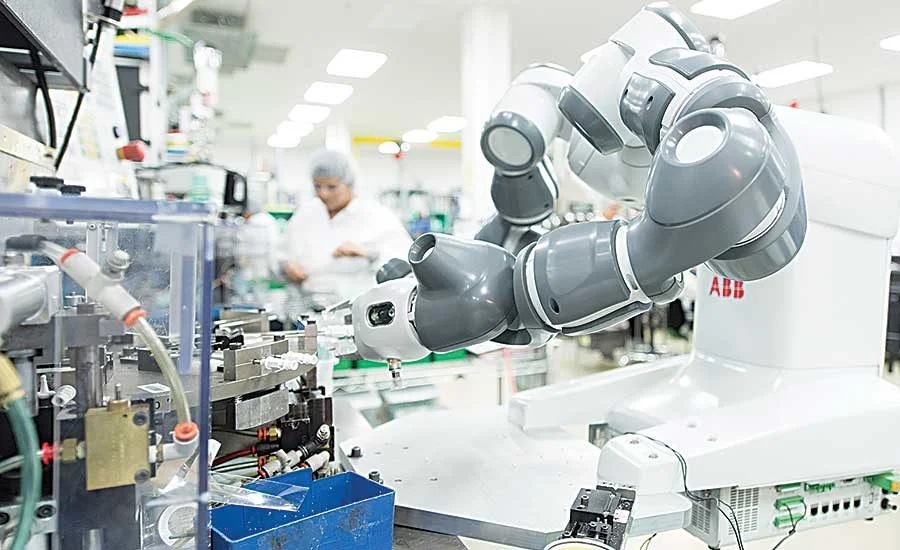
Rapid Prototyping
Rapid prototyping quickly fabricates a preliminary part from a three-dimensional (3D) design. Injection molding or CNC machining can be used, but 3D printing is usually associated with rapid prototyping instead. This form of additive manufacturing doesn’t require custom tooling such as injection molds, and 3D printing supports complex part geometries that are not achievable with traditional manufacturing methods like CNC machining.
With 3D printing, medical device designers support personalized healthcare for improved patient outcomes. For example, 3D printed dental products such as teeth aligners, crowns and bridges, and surgical guides. Biocompatible 3D printed materials are available, and designers have a choice of 3D printing processes.
Scaling can pose challenges, however. For medical products that aren’t patient-specific, medical device companies need a cost-effective way to mass-produce parts. There’s a crossover point at which injection molding or CNC machining becomes more cost-effective than 3D printing, and Fictiv can help you identify this quantity.
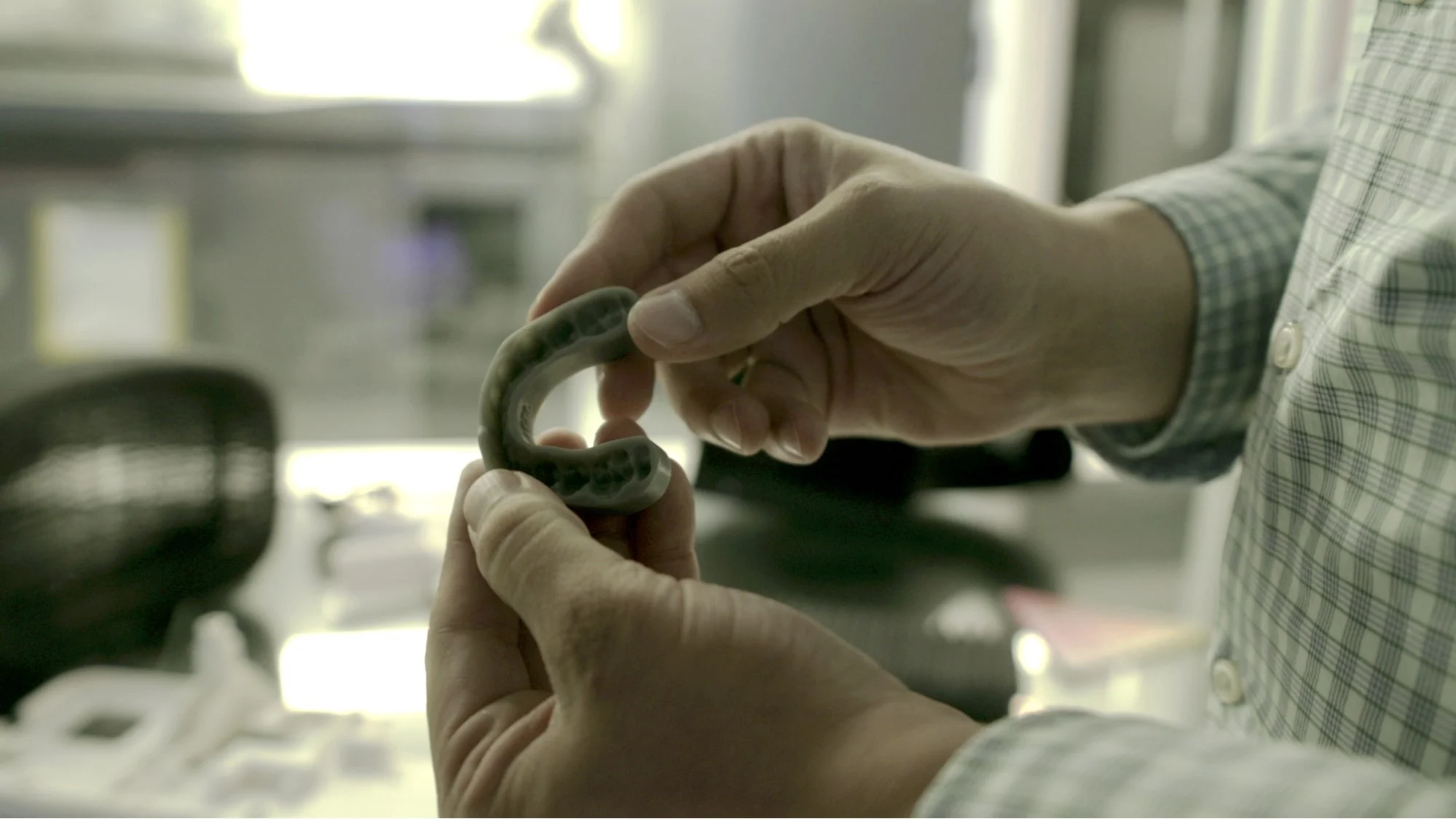
Strategies for Streamlining and Scaling Medical Production
Innovative technologies can support streamlining and scaling, but expanded medical production doesn’t end there. To be successful, medical device companies need to implement strategies that encompass quality management, supply chain management, and global market expansion.
Quality Management System (QMS)
A quality management system (QMS) documents the processes and procedures that a company must follow to achieve and maintain quality. In the medical industry, ISO 13485 is an international standard that outlines QMS requirements for the design, production, installation, servicing, and manufacturing of medical devices.
Supply Chain Management
Supply chain management provides a seamless flow of materials and components for production at any scale. Consider implementing the following strategies at your company.
- Embrace technology: Use software-based systems for inventory management, demand forecasting, and order processing. Automation and digitalization in supply chain processes can improve efficiency and reduce errors.
- Establish strategic partnerships: Choose reliable suppliers and logistics partners to ensure the smooth flow of materials and components. Build long-term relationships and maintain clear communication channels.
- Implement just-in-time inventory: Adopt just-in-time inventory practices to minimize inventory holding costs. This involves ordering materials and components in line with production schedules, reducing the need for excess inventory.
- Monitor and analyze data: Use data analytics tools to monitor key performance indicators and track supply chain performance. Look for ways to identify bottlenecks, optimize processes, and make data-driven decisions.
- Continuously improve processes: Review and optimize supply chain processes regularly. Implement lean manufacturing principles and encourage employee involvement in process improvement initiatives.
Global Market Expansion
Expansion into global markets is another obstacle that medical device companies face when scaling production. Understanding regulatory requirements, cultural differences, and market dynamics in different countries can help.
- Regulatory requirements: The standards that your medical device needs to meet vary by country and could change over time. Engage regulatory experts before and during product launch, as well as throughout your product’s life cycle.
- Cultural differences: Avoid practices that may influence product use or induce risks and hazards. The interpretation of colors and symbols varies, and the type of professional who operates a device in one country may not be the same as in another.
- Market dynamics vary not only by size, but also in terms of ease of access and rate of adoption. Local partners can provide insights that help facilitate market expansion.
- Streamlining and scaling are possible, and several trends make it more important than ever.
Future Trends in Scalable Medical Production
The following trends are shaping the future of scalable medical production.
- Personalized Healthcare: The demand for personalized healthcare solutions is driving the development of custom medical devices. To meet demand, 3D printing and other advanced manufacturing technologies will grow in importance.
- Internet of Medical Things (IoMT): IoMT devices can automatically collect health metrics like blood pressure, heart rate, and temperature from patients who aren’t in a healthcare facility.
- Advanced Drug Delivery Systems: New technologies will improve treatment efficacy, reduce side effects, and enhance patient compliance. Maintaining these systems will require consumables and service agreements.
- Sustainability and Eco-Friendly Manufacturing: Minimizing waste generation, using recyclable materials, and optimizing energy consumption will become an increasingly important part of sustainability efforts.
By understanding these trends, medical device companies can stay ahead of the curve, meet changing market demands, and maintain quality.
Why Medical Device Manufacturers Choose Fictiv
From startups to Fortune 500 firms, Fictiv partners with medical companies that want to streamline and scale production to meet growing market demand. With help from our engineering experts, you can go from idea to iteration, and from validation testing to mass production and continuous improvement. Whether you’re starting from a back of the napkin sketch, a prototype, or low volume production, we can help you scale-up for success.
Fictiv can also help you streamline your supply chain. Traditionally, scaling medical production meant dealing with multiple suppliers. That could be challenging if each supplier performed only certain processes and in certain quantities. There are unique challenges and opportunities during each stage of the product life cycle, but manufacturers who are locked into infrastructure, equipment, and geography have limitations.
Fictiv simplifies sourcing by providing 3D Printing, CNC Machining, Injection Molding (including liquid silicone rubber, or LSR, injection molding) and more—all in the quantities that you need. Our digital manufacturing platform also lets you leverage a seamlessly and intelligently connected network of 250 manufacturing centers in four regions across the globe.
You’ll get access to near-infinite capacity, capabilities, materials, and secondary processes – including assembly work. Managing your entire bill of materials (BOM) and bill of process (BOP) can be a real headache, but Fictiv’s supply chain is ready to support you throughout the entire product life cycle and deliver benefits at each stage.
Why settle for supply chain limitations when you get what you need at the right time and with the right capabilities for the best outcomes and a competitive advantage? Take the first step toward streamlining and scaling your manufacturing. Create your free Fictiv account today.