Time to read: 4 min
Specialty plastics for injection molding have material and performance properties that meet the requirements of more demanding applications. These include engineering plastics and resins for medical, automotive, aerospace, electronics, and other applications. Polymer blends — mixtures of two or more polymers that form new materials with different properties — are also used to meet tougher requirements.
Specialty plastics and polymer blends cost more than the commodity plastics produced in high volumes used in many consumer, commercial, and industrial applications. They provide an alternative to copolymerization and use mixing instead of chemical processes. Polymer blends still require attentive processing, and plastic injection molders must carefully monitor the concentration of blended materials, viscosity ratio, molding temperature, and clamping pressure.
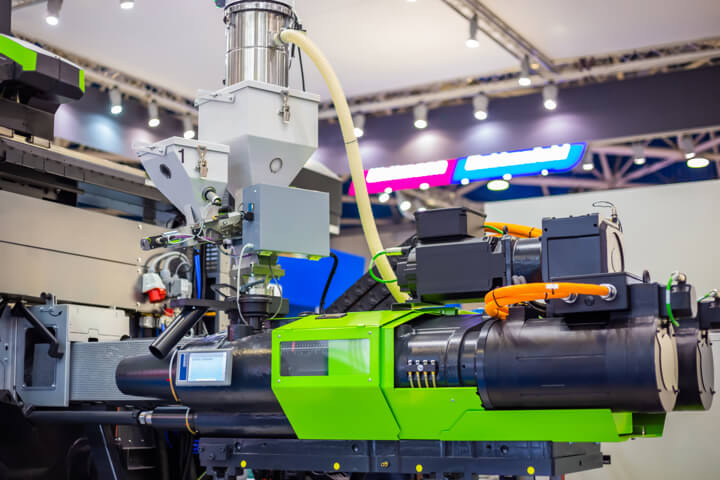
Specialty Plastics for Injection Molding
There are many types of specialty plastics, but these are the five most commonly used in injection molding.
- Liquid crystal polymers (LCPs)
- Polybutylene terephthalate (PBT)
- Polyether ether ketone (PEEK)
- Polyetherimide (PEI)
- Polyphenylsulphone (PPSU)
The following sections provide an overview of each specialty plastic that includes their material properties, comparisons with other materials, and sample applications.
Liquid Crystal Polymers (LCPs)
LCPs are used for injection molding thin-walled parts and small components. They also resist gamma radiation, steam autoclaving, and most chemical-sterilization methods. In addition to medical devices, these specialty plastics are used for injection molded sockets for integrated circuits (ICs). LCPs require drying before processing, however, which adds costs.
Polybutylene Terephthalate (PBT)
PBT has a low melt viscosity, which makes it an excellent plastic material for injection molded parts with thin cross sections. PBT also has excellent resistance to creep, which is the tendency of a material to slowly deform over a long period of exposure to high levels of stress. Applications for injected molded PBT include keyboards, switches, and distribution boxes.
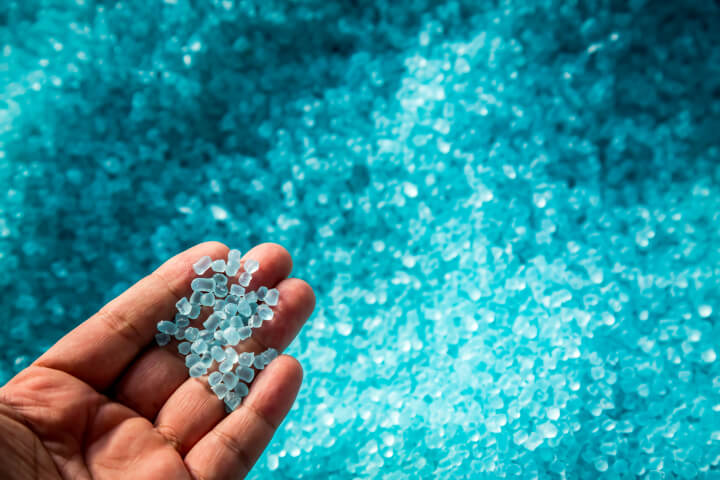
Polyetherimide (PEI)
PEI is a heat-resistant thermoplastic that combines stiffness and stability with low flammability and low smoke production. Its environmental resistance and high impact strength make it a good choice for medical components and automotive transmissions and lighting systems. PEI is similar to PEEK plastic but generally costs less. Ultem® is a leading brand name.
Polyether Ether Ketone (PEEK)
PEEK is an engineering plastic that is used in medical applications because it resists gamma radiation and autoclaving, both of which are used for sterilization. PEEK has excellent mechanical properties, resists chemicals and thermal degradation, and withstands long-term liquid submersion. PEEK is relatively expensive and can be filled with glass for greater stiffness and tensile strength.
Polyphenylsulfone (PPSU)
PPSU is a transparent, heat-resistant plastic with high toughness, high flexural and tensile strength, and good resistance to chemicals and heat. Applications include pipe fittings, battery containers, medical device parts, and sterilizable products for medical applications. In the automotive and aerospace industries, PPSU is used when exceptional thermal and mechanical properties are required.
Polymer Blends for Injection Molding
There are three main polymer blends used in plastic injection molding.
- Polycarbonate/acrylonitrile butadiene styrene (PC/ABS)
- Polycarbonate/polybutylene terephthalate (PC/PBT)
- Polyphenylene ether/polystyrene (PPE/PS)
The following sections provide an overview of each of these blended plastics along with information about material properties, comparisons, and sample applications.
Polycarbonate/Acrylonitrile Butadiene Styrene (PC/ABS)
PC/ABS is one of the world’s most widely used engineering thermoplastics. It’s strong, stiff, and heat resistant with high impact resistance, even at low temperatures. During processing, this polymer blend has low shrinkage which results in fewer injection molding defects. PC/ABS is used in the automotive industry for glove boxes and in the electronics industry for laptop monitor enclosures.
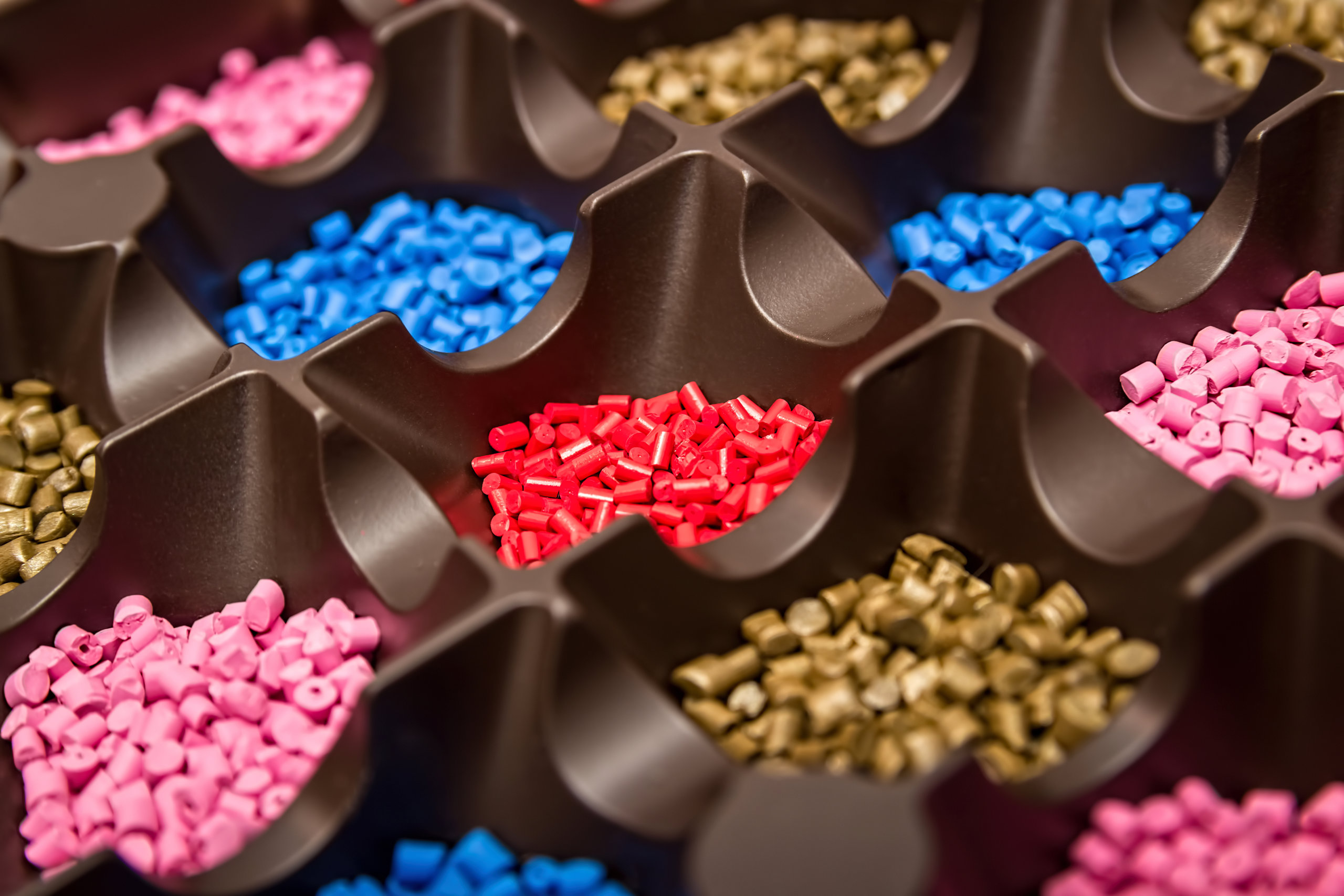
Polycarbonate/Polybutylene Terephthalate (PBT)
PC/PBT offers a good combination of chemical resistance, temperature resistance, and mechanical strength. It retains its toughness at low temperatures and provides long-term durability. This blended polymer’s properties can be further enhanced by additives that provide flame or UV resistance. Unlike PC/ABS, however, it has high mold shrinkage. Applications include electrical insulation.
Polyphenylene Ether/Polystyrene (PPE/PS)
PPE/PS provides excellent dimensional stability, low mold shrinkage, low water absorption, and outstanding stability in both hot and cold water. It also provides high impact strength and temperature resistance. Applications include instrument panels for electrical equipment, smoke detectors, speaker housings, and reusable medical devices.
Plastic Injection Molding Materials and More
Hundreds of different resins can be injection molded, so it helps to have an expert’s advice before choosing a molding material – especially an expensive one – for your project. The most common injection molded materials tend to cost less, but some applications require a specialty plastic or a polymer blend. Fictiv can give you guidance on selecting the right resin and also provides design for manufacturing (DFM) assistance.
For all your custom injection molded part manufacturing needs, Fictiv has you covered. We simplify custom plastic part sourcing with intelligent, streamlined, automated workflows — in short, Fictiv is your operating system for custom manufacturing that makes part procurement faster, easier, and more efficient.
In other words, Fictiv lets engineers, like you, engineer.
Create an account and upload your part to see what our instant quote process, expert guidance, and intelligent platform can do for you. Our injection molding service can deliver T1 samples in as little as 2 weeks!