Time to read: 4 min
Both soft and hard tooling are used in plastic injection molding, and soft tooling is also used in urethane casting, a separate manufacturing process. For product designers, these different uses of the term “soft tooling” can be confusing. Terms like “hard” and “soft” are relative, of course, as the metal tooling used in injection molding can be categorized as hard or soft depending on the type of metal and its grade.
It’s critical to understand the differences between soft tooling and hard tooling in injection molding, as well as the differences in soft tooling between injection molding and urethane casting. There are pros and cons to every type of tool, and it’s good to have a selection of mold materials. In this article, we’ll discuss the specific tooling choices that affect material selection, costs, quantities, and quality.
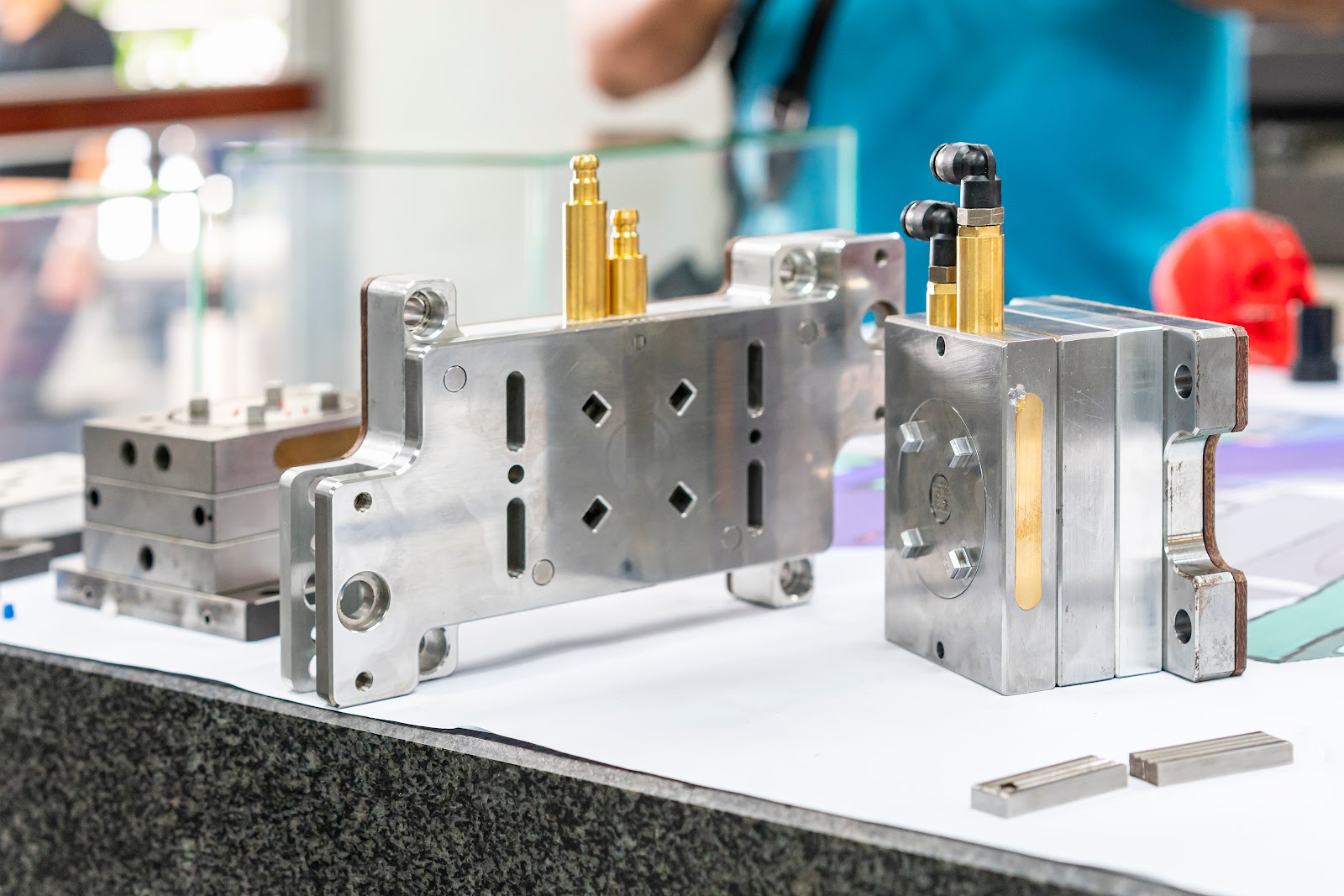
What is soft tooling?
In plastic injection molding, soft tooling usually refers to metal molds that have aluminum cores and cavities, as opposed to steel. Aluminum is softer than steel, and can’t be hardened to the same extent that steel can. Some aluminum molds have inserts made from steel, but these are usually pre-hardened steels in lower grades. It’s also worth noting that while 3D printing can be used to produce soft mold features such as cavities, the mold itself still requires a metal frame.
In urethane casting, the soft tooling isn’t machined from aluminum. Instead, it’s made from silicone, carbon fiber or fiberglass. These tools begin with a master pattern that is milled, machined, or 3D printed. This master pattern, a replica of the end-use part, is then used to produce molds for parts production. In urethane casting, soft tooling is used in a manual, pour-and-cure process. By contrast, soft tooling for injection molding is used in machine-based manufacturing.
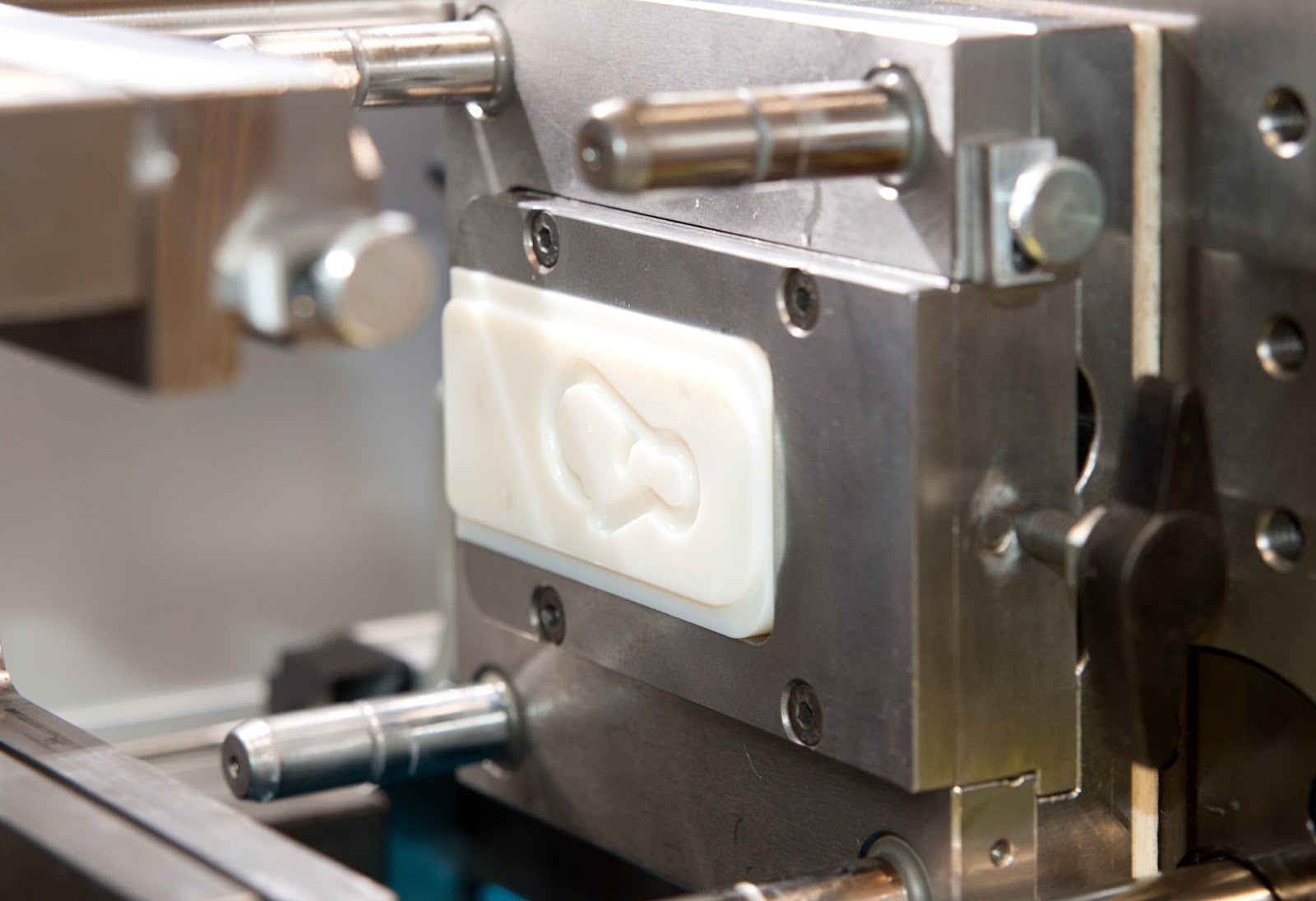
What are the advantages and disadvantages of soft tooling?
Injection Molding
The main advantage of aluminum injection molds is that they cost less and take less time to produce. Steel molds can be priced competitively, however, and Fictiv can supply them in less time than you might think. Yet, speed and costs aren’t the only considerations.
Aluminum molds can’t withstand as many injection molding cycles, and aluminum has more limited support for mold changes. Plus, softer tooling may deform under the high clamping pressures associated with injection molding and cause flash, a type of surface defect. And, aluminum molds can’t hold the tight tolerances that are achievable with steel molds.
Because of their limited wear resistance, aluminum injection molds are not a good choice for abrasive materials such as glass-filled nylon. Plastic materials that require high temperatures, such as PEI and PEEK, also don’t mold well in aluminum because it’s difficult to maintain the required temperature. Corrosive grades of plastic, such as PVC or POM, are problematic because they can degrade the aluminum itself.
Urethane Casting
With urethane casting, the relationship between soft tooling and material selection is less important because the molding process only supports the use of castable polyurethanes, additives, and curatives.
Durability is also an important consideration. The silicone molds in urethane casting can withstand about 25 shots per cavity. These molds are easier to make and are less expensive to produce than aluminum injection molds — but silicone molds can’t produce as many parts, nor do they support the same degree of precision or complexity as metal molds.
Still, the soft tooling that’s used in both molding processes can support prototyping, bridge production, and low-volume manufacturing. The volumes in urethane casting are generally lower (1 to 100), however, and designers can’t create parts or prototypes in the end-use plastic material.
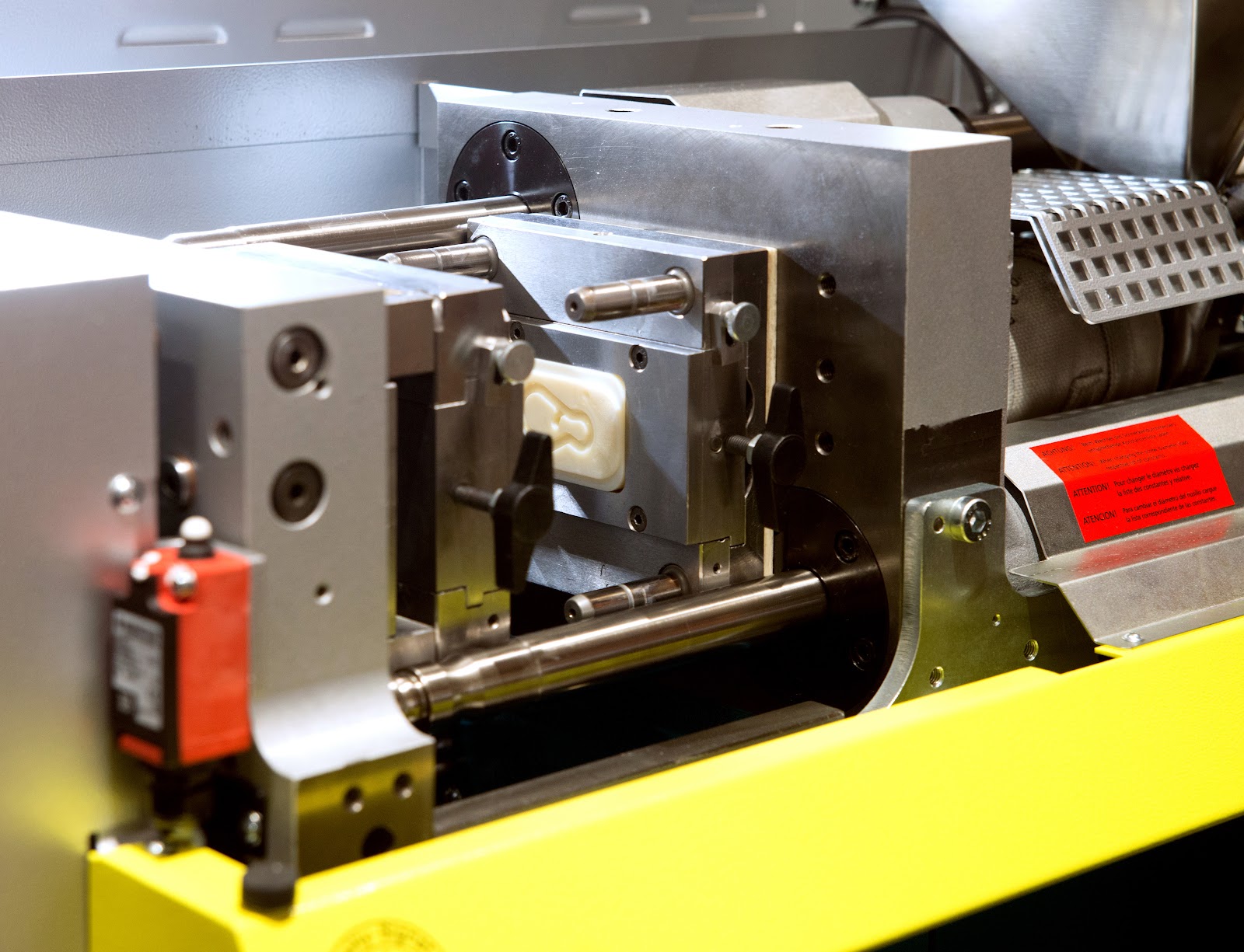
What is hard tooling?
Hard tooling for plastic injection molding is made of steel, an alloy consisting of iron and carbon with small amounts of other ingredients. Steel is harder than aluminum, but heat-treated steel is even harder and provides greater durability and wear resistance. Most P20 steel is not hardened, but it’s still significantly harder than aluminum, and has a tooling life that is five to ten times longer. NAK80, a semi-hardened tool steel, has an even longer tooling life and polishes well for the production of optically clear parts.
Hardened steels for injection molds include H13 and S136. H13 steel is used commonly for high-volume production and has a tooling life between 500,000 and 1 million shots. It’s a good choice for molding glass-filled nylon and can achieve tighter tolerances than aluminum. S136 is a stainless steel with a typical tooling life of 1 million or more shots. It can resist the corrosive chemicals in PVC or POM materials and supports superior polishing, so can create parts with high optical clarity.

What are the advantages and disadvantages of hard tooling?
Because there’s more than one type of steel tooling, designers should carfully compare hard tooling and soft tooling. In medical injection molding, for example, less expensive and faster-to-machine steels are used for pilot prototypes and low-volume production. For higher-volume production, hardened steel molds may be used instead. H13 and S136 steels are more expensive than P20 and NAK80 steels, but hard tooling – regardless of a steel’s grade – always lasts longer. Steel molds can also be refurbished and modified.
Conclusion
Injection molding isn’t your only option for parts production, but it can help accelerate time-to-market while improving designs and controlling costs. Plastic injection molding offers designers a wider choice of materials than urethane casting can provide, and offers higher production volumes.
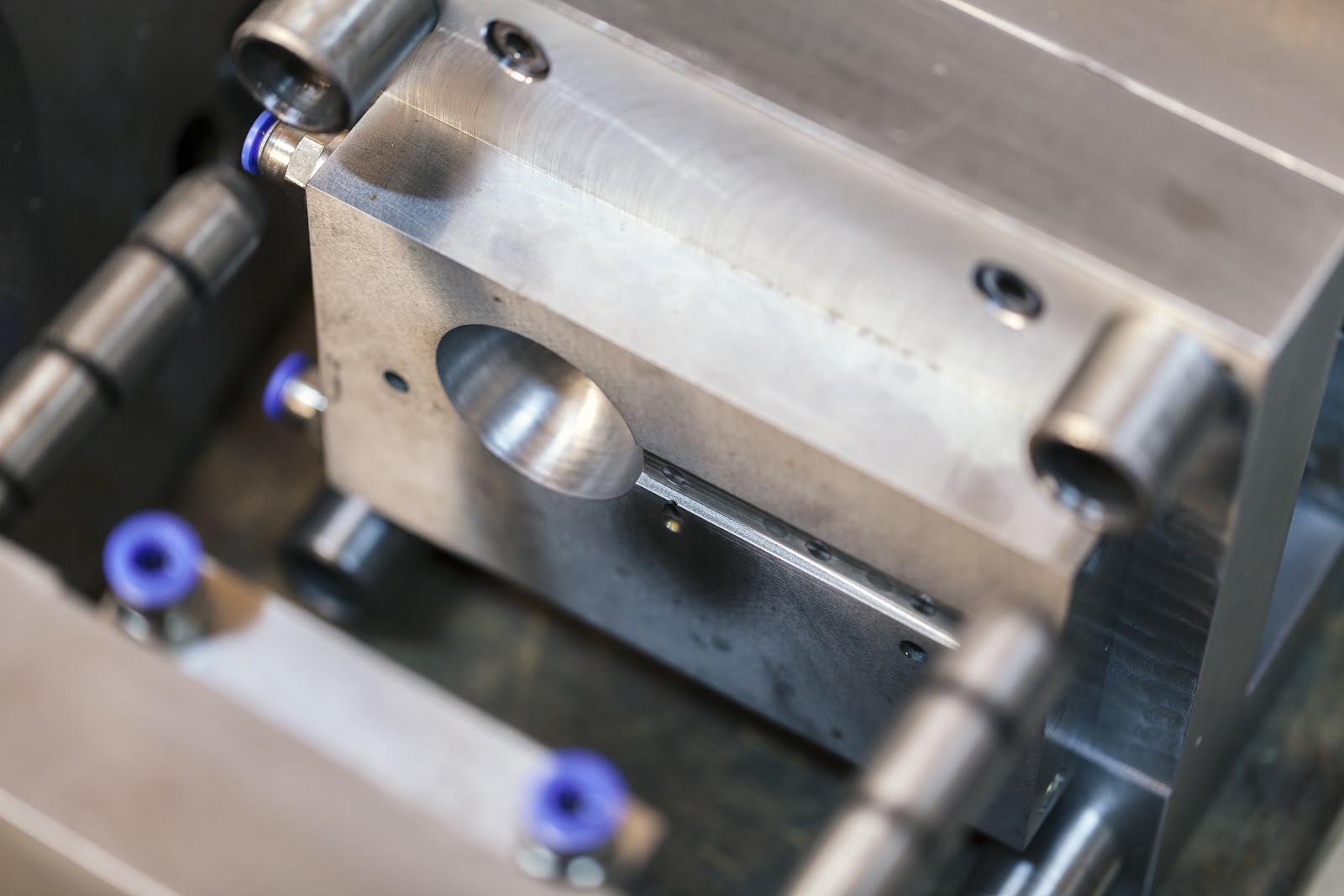
Fictiv is your operating system for custom manufacturing, and no matter where you are in the design process, we have the resources, know-how, and manufacturing network to make your next project a success. Learn more about our injection molding services and create an account to get a quote today.