Time to read: 6 min
Silicone elastomers are synthetic materials containing silicon, oxygen, carbon, and hydrogen atoms. These thermoset resins have various uses and benefits, but not all silicones are the same. For example, the general-purpose silicone that’s used to seal bathtubs and windows isn’t suitable for medical devices or cooking utensils.
This article from Fictiv provides an overview of silicone rubber, starting with chemistries and curing systems. You’ll then learn about the different types of silicone materials, their advantages over other elastomers, and how silicones are fabricated and used in a wide range of applications. If you’re designing a silicone part, create a free Fictiv account and upload your CAD file for a quote. We produce complex parts at amazing speeds!
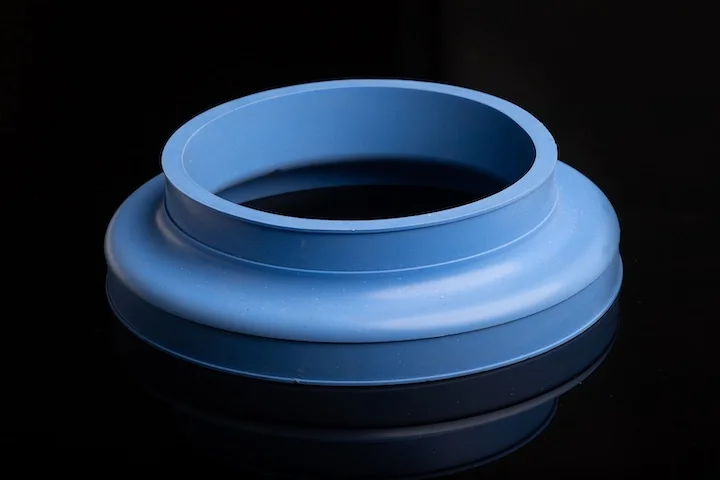
Silicone parts like this can be compression molded for low-volume production.
Silicone Chemistries
Chemically, silicones consist of alternating silicon and oxygen (Si-O) bonds. This inorganic Si-O backbone is what makes silicones’ physical and chemical properties different from polymers (such as thermoplastics) that have an organic carbon (C-C) backbone.
Most silicones have a polydimethylsiloxane (PDMS) chemistry where each silicon atom is bonded to two oxygen atoms and two methyl (CH3) groups. PDMS production depends upon the specific type of methyl group that’s attached to the silicon atom.
Silicone Curing Systems
Curing is a chemical process that transforms a material from a liquid state into a solid form. In the context of elastomers, curing is also known as vulcanization. This chemical reaction causes cross-linking between polymer chains, typically with covalent or ionic bonds.
There are many types of curing systems, but these four are the most common.
- Condensation
- Platinum
- Peroxide
- Ultraviolet light (UV)
The following sections explain how each curing system works and some common applications.
Condensation Curing
Condensation curing uses tin-based catalysts such as tin salts or tin oxides to initiate crosslinking. The atmospheric moisture that’s used during curing releases byproducts such as alcohol and acetic acid. Post-curing or post-baking, a process that involves heating silicone in an oven, may be required to remove residue. Applications for condensation-cured silicones include molds, architectural components, and special effects production.
Platinum Curing
Platinum curing uses platinum-based catalysts to initiate crosslinking. These silicones are less sensitive to atmospheric moisture, and platinum curing does not release byproducts such as volatile organic compounds (VOCs) that require post-baking for removal. Because of their greater cleanliness and purity, some platinum-cured silicones are used in medical applications. For example, platinum-cured USP Class VI silicones are used with medical wearables.
Peroxide Curing
Peroxide-cured silicones use organic peroxide catalysts that decompose during curing. They can also be cured at lower temperatures. Peroxide-cured silicones aren’t as transparent as platinum-cured silicones, but peroxide curing is less expensive. Applications typically include silicone tubing and O-rings, but food-grade materials can be used with dishware.
UV Curing
UV cured silicones react to ultraviolet (UV) light to initiate crosslinking. In other words, these silicones cure with light instead of heat. Sometimes, however, a secondary curing method is needed to reach shadowed areas. UV curing is rapid, but it also allows for greater control over curing time. Often, UV cured silicones are used in electronics and medical applications.
“There are also military applications for silicones, both at the asset and weapons system levels. For example, silicone components are used in military aircraft, naval vessels, tanks, and submarines.” – Metallurgical Grade Silicon Metal and Silicone Rubber: A Matter of National Security, Rubber World magazine, November 2023
Type of Silicone Materials
There are four basic types of silicone materials.
- Room temperature vulcanizing (RTV)
- Liquid silicone rubber (LSR)
- High consistency rubber (HCR)
- Fluorosilicones
The following sections describe them.
Room Temperature Vulcanizing (RTV) Silicones
As their name suggests, room temperature vulcanizing (RTV) silicones cure at room temperature without the need for additional heat. These materials exhibit minimal shrinkage during curing and remain flexible over a wide temperature range. RTV silicones are available in one-part formulations that cure with exposure to moisture in the air, and in two-part formulations that consist of a base and a curing agent. Applications include RTV molds.
Liquid Silicone Rubber (LSR)
Liquid silicone rubber (LSR) starts as a liquid and cures into a flexible elastomer. With their low viscosity, LSRs can be 3D printed or injection molded to produce parts with intricate and complex shapes. Applications for liquid silicone rubber include medical devices such as catheters and asthma inhalers, and medical equipment seals and gaskets.
High-Consistency Rubber (HCR)
High-consistency rubber (HCR) has a thick, putty-like consistency prior to curing. Although HCRs are designed for heat curing, extended periods of time at room temperature will allow for partial curing using either peroxide or platinum agents. HCRs support the use of compression molding for parts such as gaskets, but these silicone materials can also be extruded into tubes and calendared into silicone sheets.
Fluorosilicones
Fluorosilicones are silicone elastomers that contain fluorine in their molecular structure. The fluorine replaces some or all methyl groups, and the degree to which this replacement occurs determines the elastomer’s properties and cost. Compared to general-purpose silicones, fluorosilicones provide greater resistance to fuels, chemicals, and oils. Fluorosilicones have limited physical strength, however, and they aren’t recommended for dynamic sealing applications.
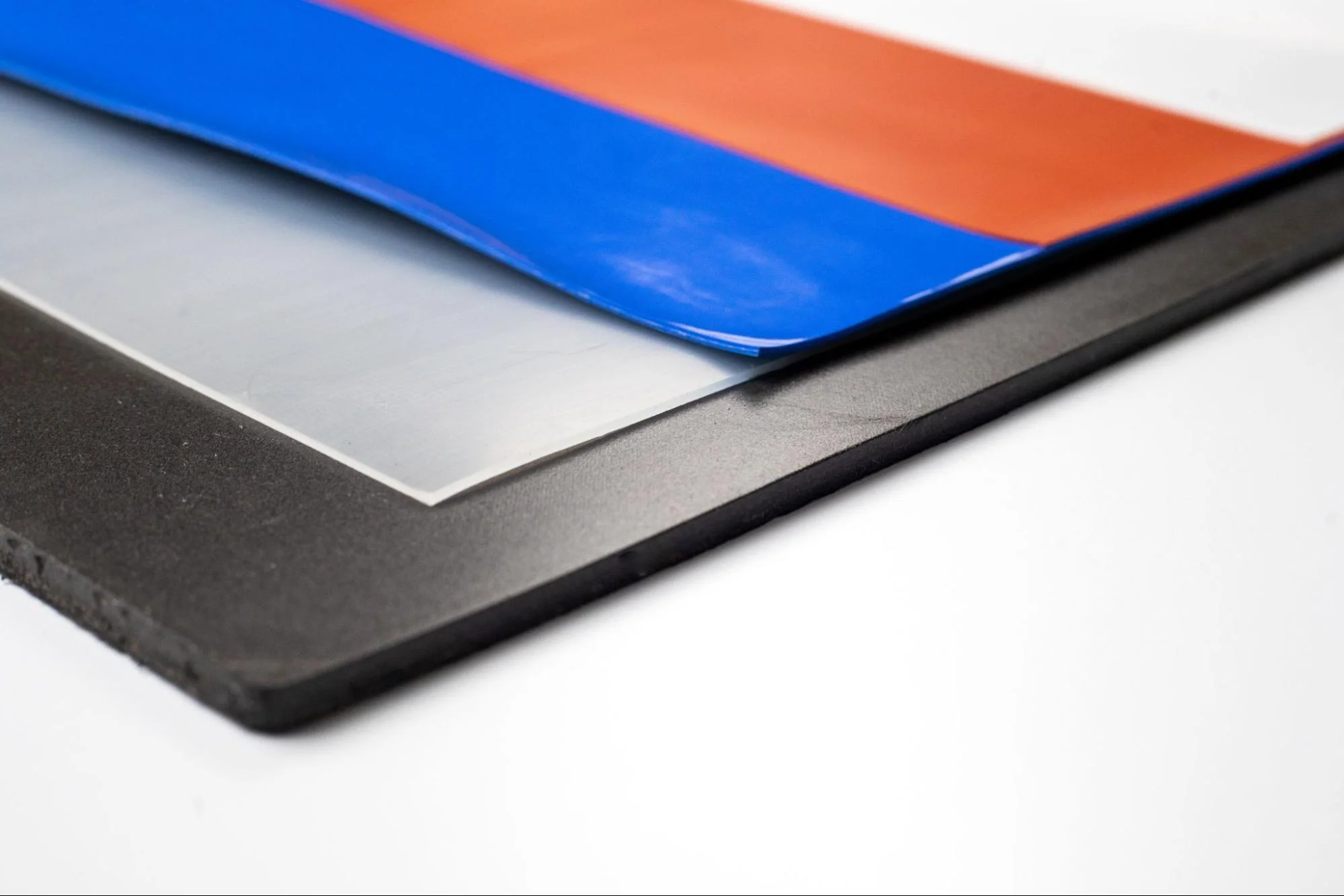
Silicones and fluorosilicones are also used in military and aerospace applications. Image Credit: Specialty Silicone Products
Silicone Benefits
Silicone elastomers provide the following benefits.
- Temperature range and thermal stability
- Flexibility and elasticity
- Compression set and stress relaxation resistance
- Chemical and environmental resistance
- Electrical insulation
- Microbial resistance
- Customization and versatility
- Fabrication methods
The following sections explain.
Temperature Range and High Thermal Stability
Silicones resist a wide range of temperatures without a significant loss of physical properties. Specific temperature ranges vary by type and formulation, but most silicones remain functional at temperatures as low as -60°C to -100°C (-76°F to -148°F). Most silicone materials can also withstand elevated temperatures between 200°C and 300°C (392°F to 572°F).
Flexibility and Elasticity
Silicones maintain their flexibility over a wide temperature range, but they’re also known for their elasticity: the ability of a material to return to its normal shape after being stretched or compressed.
- Stretching occurs when a material is subjected to a force that pulls it apart and causes it to elongate.
- Compression occurs when a material is subjected to a force that pushes it together and causes it to shorten.
Silicone parts such as pads and gaskets are often subject to both types of deformation.
Compression Set and Stress Relaxation Resistance
Silicones’ ability to resist compression set and stress relaxation makes them an excellent choice for applications that require long-term performance under mechanical stress.
- Compression set refers to a material’s permanent deformation under a compressive force, such as a closed door.
- Stress relaxation is the gradual decrease in stress under a constant strain over time.
Because of their stress relaxation resistance, silicones retain their sealing capability over time when deformed continuously.
Chemical and Environmental Resistance
Silicone materials provide broad chemical and environmental resistance. They resist:
- Weak acids
- Bases and alkalis
- Common solvents like ketones, esters, and hydrocarbons
- Aqueous salt solutions
Importantly, silicones do not degrade or swell in the presence of moisture. They are inherently hydrophobic (i.e., water-repellent) and withstand oxidation, ozone, and ultraviolet light (UV), all of which are factors in many outdoor applications.
Electrical Insulation
Silicones are excellent electrical insulators that combine high dielectric strength with low electrical conductivity.
- Dielectric strength is the maximum voltage required to cause an insulating material to break down under an electric field. The higher the dielectric strength, the higher the voltage before breakdown occurs.
- Electrical conductivity is a measure of a material’s ability to conduct an electrical current. The lower the electrical conductivity, the greater the resistance to the flow of current.
With their unique combination of properties, silicones are well-suited for dielectric elastomer actuators (DEA) and can support 3D printing with UV curing.
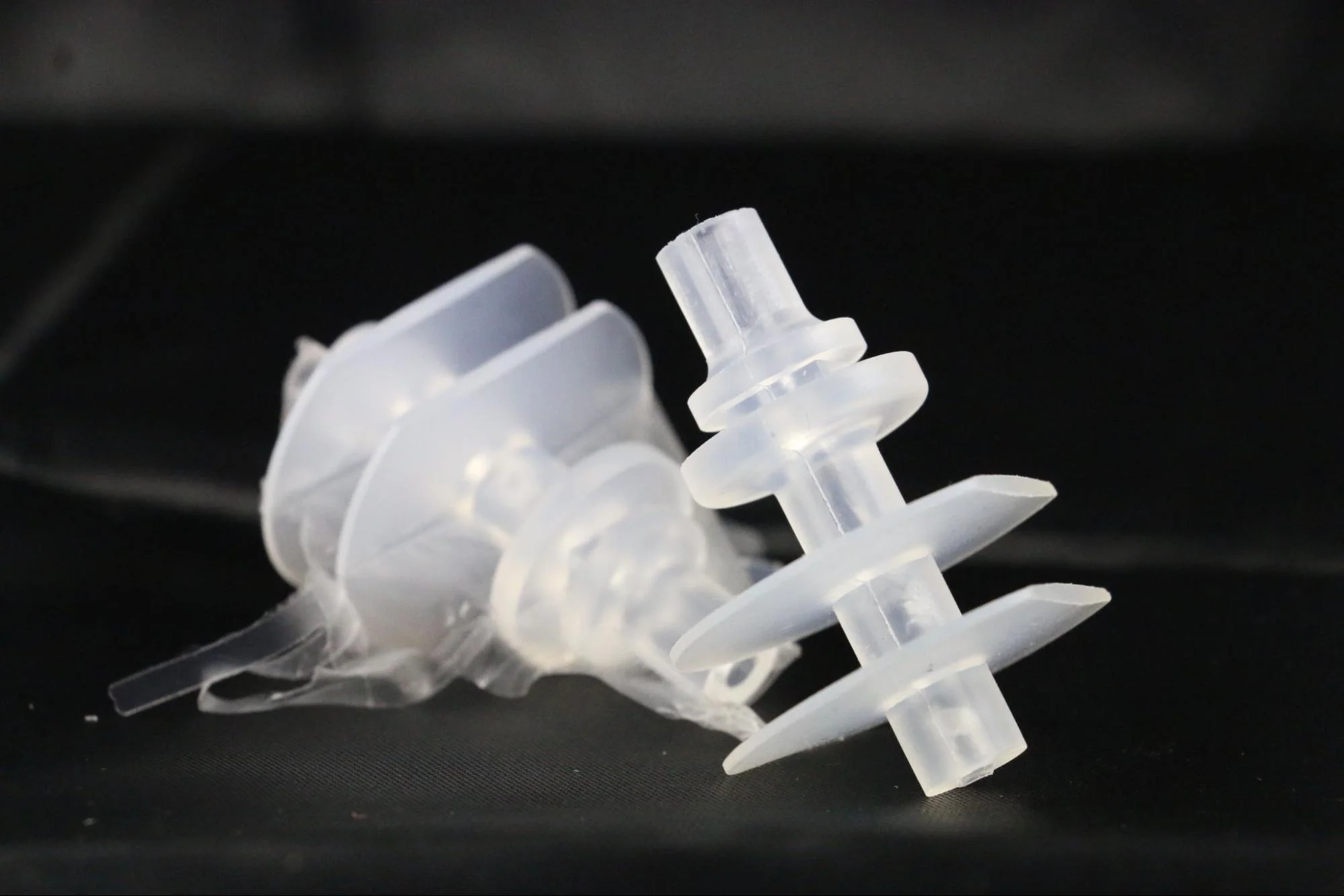
This silicone medical valve was injection molded and then cryogenically deflashed. Image Credit: Nitrofreeze
Microbial Resistance
Microbes are microscopic organisms that include bacteria, viruses, and fungi. Because silicones are chemically inert and water repellent, they do not provide a nutrient source for microbes and help to prevent the accumulation of moisture, which is required for microbial growth.
With their smooth surfaces, silicone materials are also relatively easy to clean. Surface treatments and the use of antimicrobial additives can enhance silicones’ microbial resistance for food and medical applications.
Customization and Versatility
Silicones are also customizable and support the use of additives, fillers, and pigments. Examples include compounds that are electrically conductive because they contain metal particles and silicones that are formulated for flame-resistance. Some products combine UL 94 V0 flame resistance with shielding against electromagnetic interference.
Fabrication Methods
As previous sections in this article have explained, silicone elastomers support 3D printing, injection molding, and compression molding. They also support urethane casting and can be extruded or calendered. Depending on their material properties, some silicones can be CNC machined. With injection molding and compression molding, silicone can also be used as an overmold material.
Silicone Fabrication and Fictiv
Fictiv can help you with your silicone manufacturing needs through our network of global partners. Importantly, we also provide design for manufacturing (DFM) assistance that can help you reduce costs and optimize the performance of your part designs. When you request a quote from us, you’ll generally receive a response within 24 hours.
Companies that work with Fictiv can access silicone-related services, including:
- 3D printing
- Injection molding
- Compression molding
- CNC machining
- Urethane casting
Are you designing a silicone part? Create a free Fictiv account and upload your CAD file.