Time to read: 10 min
Sheet metal prototyping is a proven method for evaluating a part’s form, fit, and function before full-scale production. Modern advancements in fabrication tools and digital workflows have made the process faster, more precise, and closely aligned with production intent—allowing teams to iterate quickly and reduce time to market without compromising quality.
Prototype fabrication uses standard production techniques such as bending, cutting, punching, and welding, resulting in functional parts that replicate key attributes of the final design. These prototypes support real-world testing for performance, durability, and assembly, enabling engineers to identify and resolve issues early.
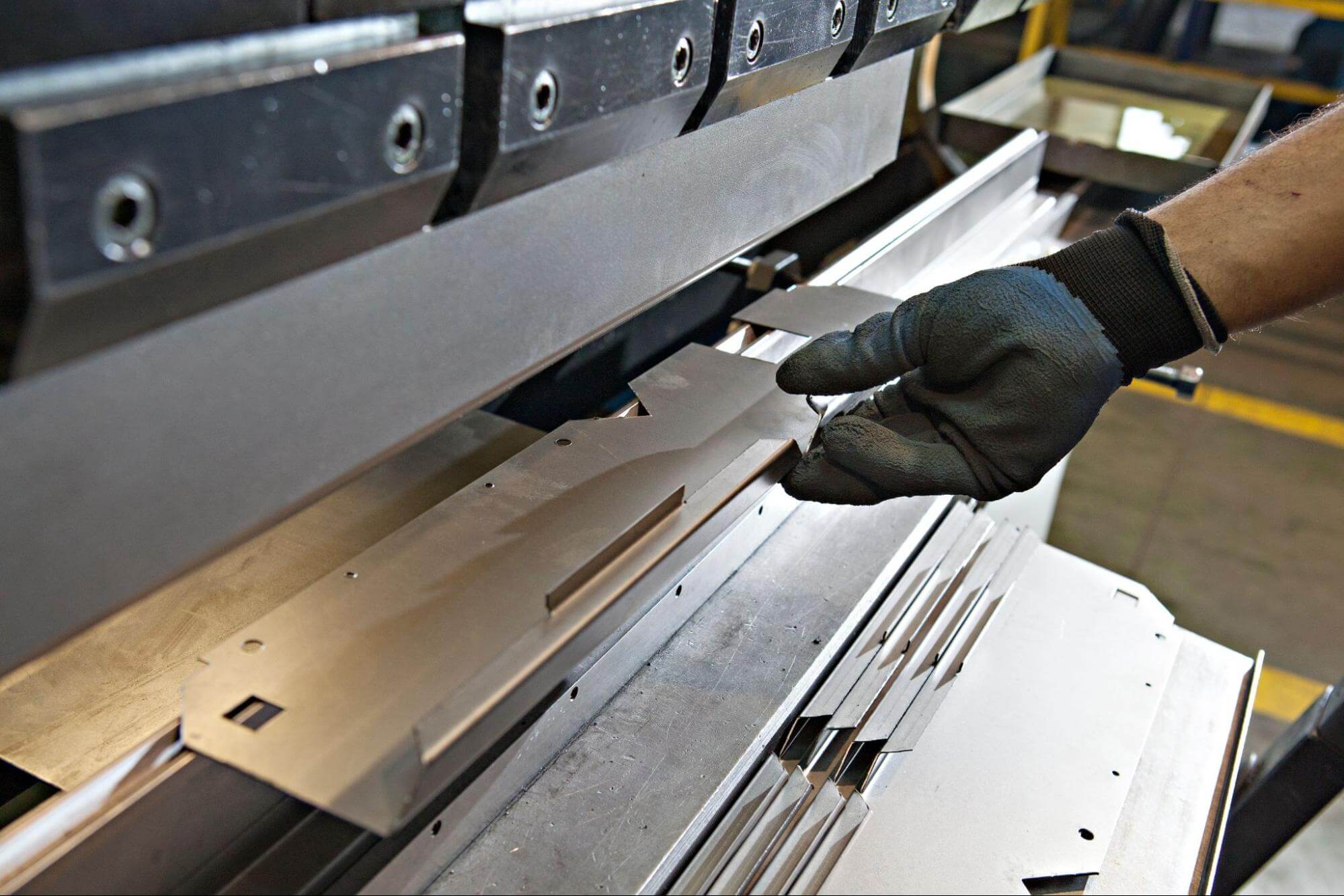
A press brake is used for bending in sheet metal prototyping
Today’s sheet metal prototyping methods allow for rapid design changes and fast feedback, helping improve overall product quality. Industries such as automotive, aerospace, consumer electronics, and medical devices rely on this approach to develop accurate, optimized, and robust components.
This article discusses the process and advantages of sheet metal prototyping, key techniques, and how it can accelerate product development in various industries.
The Sheet Metal Prototyping Process
Prototyping allows engineers and manufacturers to test and refine designs before committing to full-scale production. Sheet metal prototyping uses one or more fabrication methods to create functional metal parts quickly and efficiently.
By using advanced fabrication techniques, prototype sheet metal parts can be produced with high accuracy and minimal lead time, enabling faster product development cycles. Key steps in sheet metal prototyping include:
Design and CAD Modeling
Design and computer-aided design (CAD) modeling begin with creating a detailed 3D model using CAD software. Beyond visualization, CAD tools enable precise control over dimensions and tolerances, helping engineers identify potential interferences, simulate mechanical stresses, and avoid costly design flaws early.
CAD ensures the prototype aligns closely with design intent and production requirements and is ready for efficient manufacturing. Many CAD programs have a sheet metal tool built in, which further improves sheet metal design and makes it easier to transition to flat patterns.
Materials Selection
Material selection is critical in sheet metal prototyping, as it directly affects strength, durability, and functional performance. Aluminum, stainless steel, and mild steel are common choices, offering a balance of manufacturability and structural integrity. Other options include brass, bronze, copper, and titanium. If your production material falls outside these, it may be best to explore other prototyping methods—substituting materials may mislead functional testing and compromise design validation.
Cutting
Cutting methods, such as laser, waterjet, and plasma cutting, are used to achieve precise shapes and dimensions. Laser cutting offers high accuracy, while waterjet cutting is ideal for heat-sensitive materials. For simpler shapes or blanking, a guillotine shearing press is a more cost-effective choice. By using CAD models to generate G-code, these processes eliminate the need for expensive dies, reducing production time and costs while enhancing the speed and precision of sheet metal prototyping.
Forming and Bending
After cutting the sheet metal blank to size, shaping is done using a press brake, rollers, or prototype stamping dies. This process forms the complex angles and contours needed for the final part geometry. The ability to shape metal accurately from a precisely cut blank ensures a higher level of design fidelity and part functionality.
Assembly and Finishing
Finally, the prototype is assembled using welding, riveting, or other fastening techniques. Surface treatments such as powder coating, anodizing, or chem film are applied to enhance durability and aesthetics.
Learn more about the sheet metal fabrication process by downloading our sheet metal manufacturing guide.
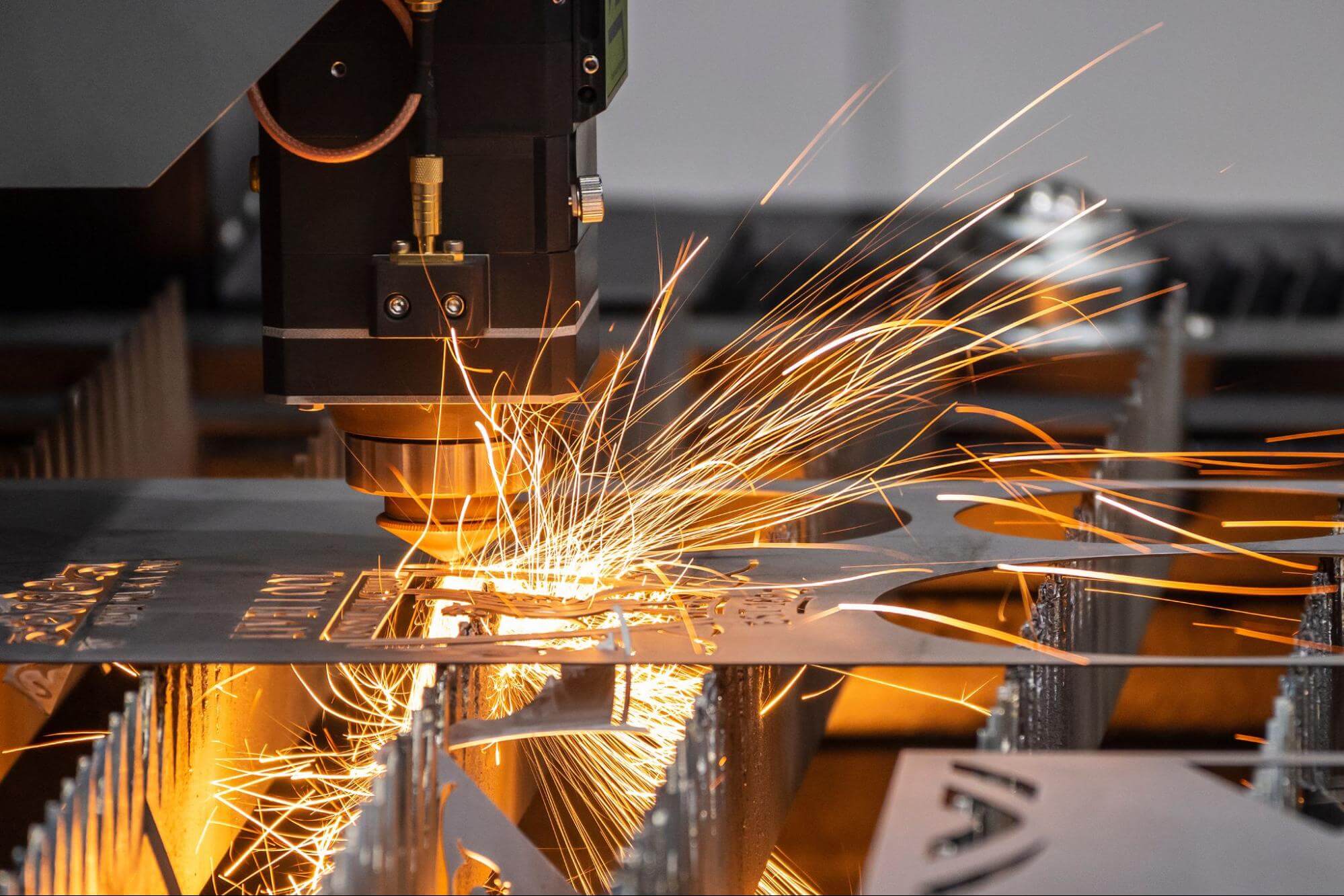
Advantages of Sheet Metal Prototyping
Sheet metal prototyping offers several key advantages that can significantly accelerate product development and improve design accuracy—particularly for parts suited to metal forming—though its effectiveness depends on the specific application:
Fast Turnaround for Product Development
Rapid sheet metal prototyping significantly reduces the time required to develop and test new designs. With advanced fabrication methods like laser cutting and automated bending, prototype sheet metal parts can be produced within days, allowing engineers to identify design flaws early and make adjustments quickly. This accelerates the overall product development cycle and shortens the time to market.
Cost-Effective for Low-Volume Production
When enough prototypes are made, the line between prototyping and small-batch production starts to blur. Sheet metal prototyping eliminates the need for complex, expensive tooling, making it a practical and affordable option for low-volume production after final design approval. This delivers high-quality results without the financial burden of traditional fabrication methods.
Use of Planned Production Materials for Functional Testing
Prototyping with actual production-grade materials allows for accurate performance testing. This ensures that the final product will meet structural, thermal, and mechanical requirements, reducing the risk of failure during full-scale production.
High Accuracy and Repeatability for Custom Designs
Advanced fabrication techniques provide tight tolerances and consistent results, even for complex or custom designs. This level of accuracy ensures that the prototype closely matches the final product, allowing for more realistic testing and validation.
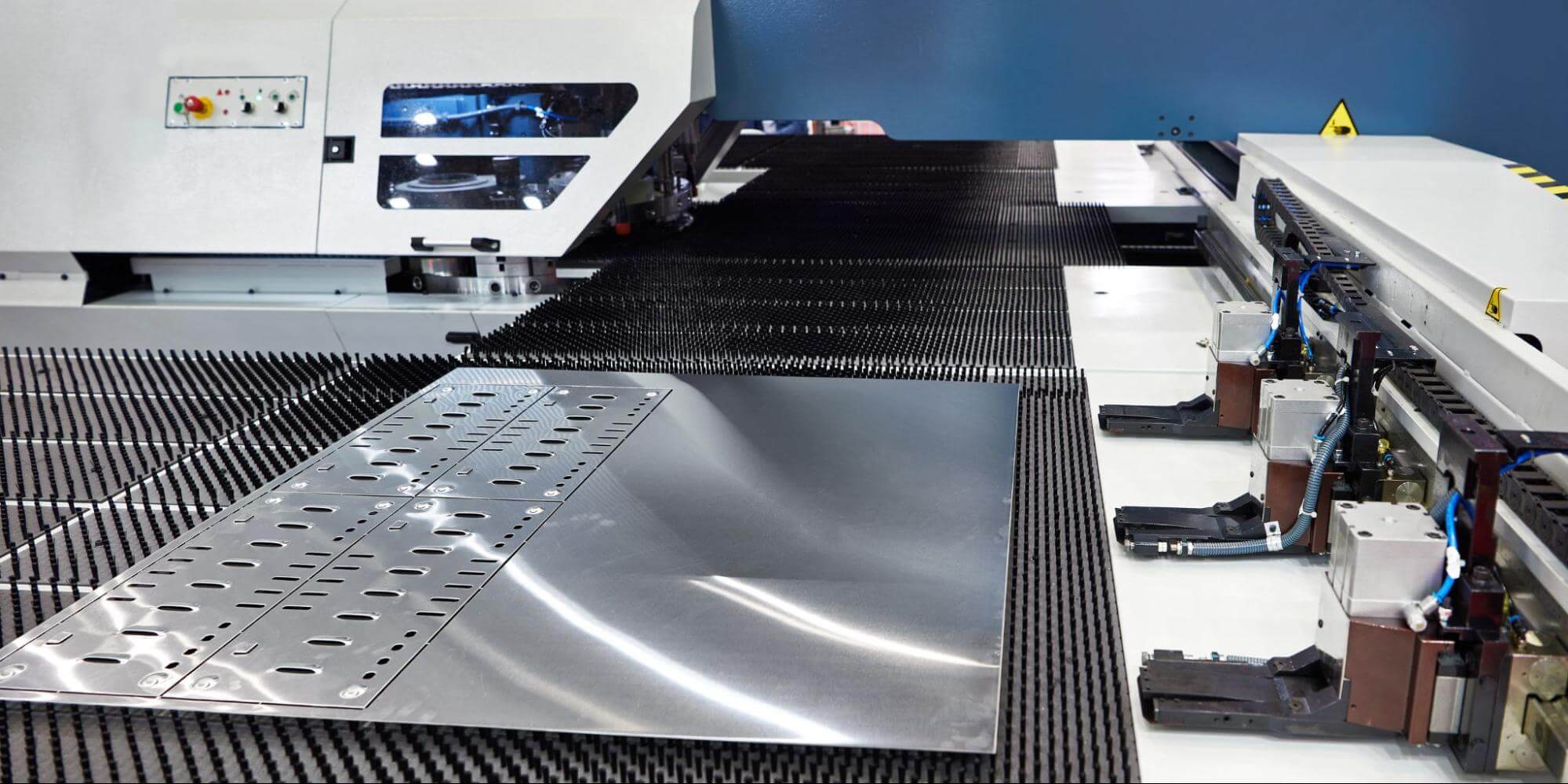
A coordinate turret punch press is used to create hole patterns in sheet metal
Common Techniques Used in Sheet Metal Prototyping
Sheet metal prototyping relies on a range of precise fabrication techniques to quickly create high-quality prototypes. These methods ensure that prototype sheet metal parts meet design specifications and functional requirements, allowing for efficient testing and refinement:
Laser Cutting & Waterjet Cutting
Laser cutting uses a high-powered beam to achieve tight tolerances in intricate sheet metal shapes, while waterjet cutting employs a high-pressure stream of water mixed with abrasives to cleanly slice through materials without generating heat, which is ideal for heat-sensitive metals and thicker sheet materials. Both methods offer fast and accurate shaping and can minimize material waste when paired with an efficient nesting layout, making them well-suited for rapid prototyping and short-run production.
CNC Turret Punching
Turret punching uses computer-controlled machinery to rapidly produce holes, slots, and cutouts with exceptional accuracy and repeatability. Beyond simple perforation, CNC technology supports complex patterns and integrated features in sheet metal parts. While often used for punching, CNC systems also play a key role in other fabrication steps—such as cutting, bending, and forming—making them a versatile tool throughout the prototyping process.
Sheet Metal Bending & Forming
Sheet metal bending and forming use press brakes, rollers, and sometimes inexpensive stamping dies to shape metal into custom geometries. These processes enable the creation of complex angles, curves, and contours. While press brakes and rollers offer flexibility for small runs, stamping with simple dies can be a cost-effective option for higher-volume parts, providing consistency and precision.
Welding & Joining
Techniques like MIG, TIG, and spot welding are commonly used to assemble multiple components into a single part, offering precision and strong bonds. Riveting, bolting, and other fastening methods are also frequently employed in prototyping — not for added strength, but for their cost-effectiveness, ease of assembly, and ability to facilitate quick disassembly—ideal for testing, refining, and iterating designs without committing to permanent joins.
Surface Finishing
Processes such as powder coating, anodizing, or chem film can be applied to enhance the durability and appearance of prototype sheet metal parts. Part surfaces can also be polished using various methods, including vapor and hand polishing.
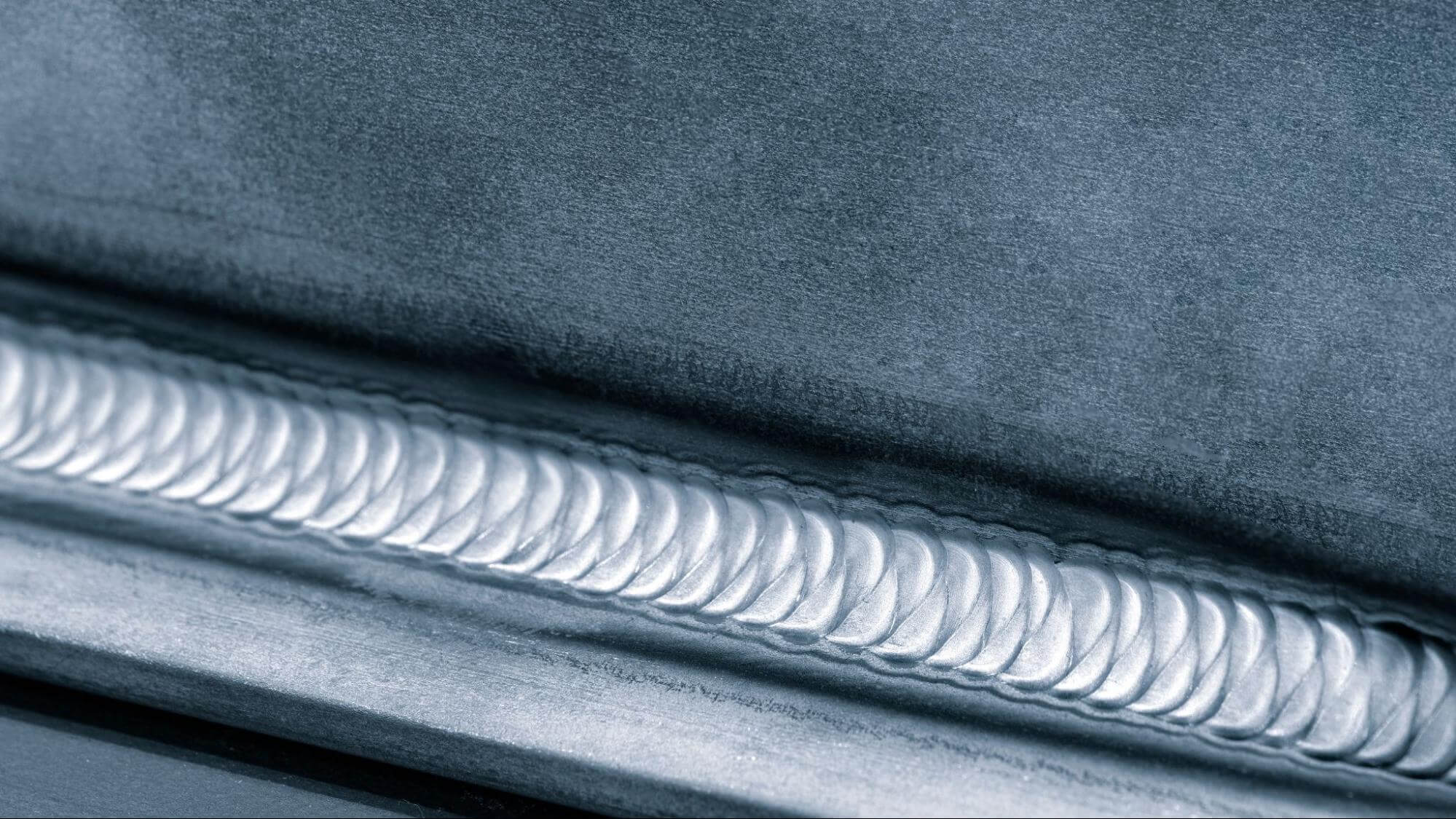
A welding seam on an angled sheet metal joint
Material Selection for Sheet Metal Prototypes
Choosing the right material is essential to ensure your prototype accurately reflects production intent. For functional testing, it’s best to match the production material—or a close equivalent—in terms of strength, weldability, formability, corrosion resistance, and conductivity.
Environmental conditions and manufacturing methods should also guide your selection, though limitations in the prototype phase may require compromises. For mock-ups or visual models, more affordable or easily formed materials may suffice, but they won’t provide reliable performance insights. The closer your prototype mimics the final part, the more accurate your testing will be—and the fewer surprises you’ll have during production.
Here are some materials that can be used for building prototypes:
Aluminum
Aluminum is ideal for prototypes requiring low weight and high corrosion resistance. Certain grades, like 5052-H32, have great formability, making them suitable for complex designs and high-performance applications.
Steel & Stainless Steel
Steel is commonly chosen for its high strength and affordability, making it suitable for applications requiring load-bearing performance. Stainless steel adds resistance to corrosion and oxidation, which is critical in harsh or high-moisture environments. When selected and formed appropriately, both materials can meet demanding mechanical and environmental requirements for functional prototypes.
Copper & Brass
Copper offers superior electrical and thermal conductivity, making it ideal for electronic components. Brass combines conductivity with a polished finish, making it suitable for decorative and functional applications.
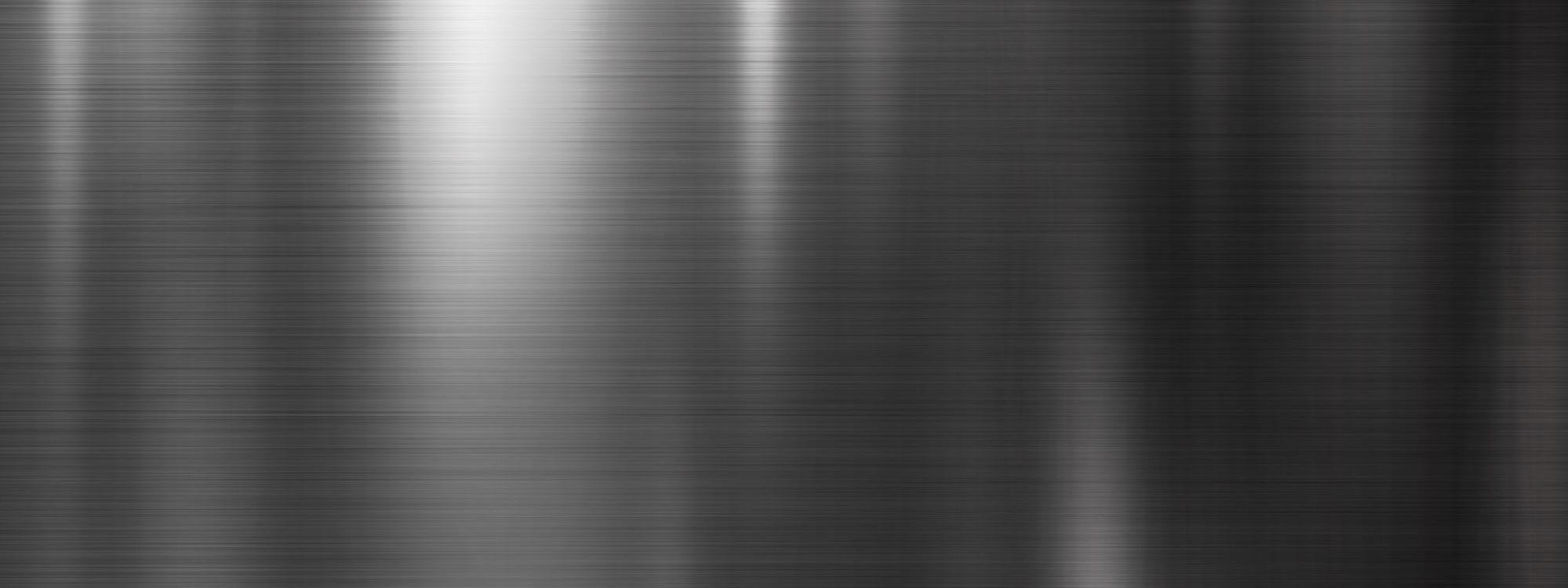
Applications of Sheet Metal Prototyping
Sheet metal prototyping is widely used across various industries to create precise, functional parts for testing and development. Sheet metal prototyping has many applications, including:
Automotive
Sheet metal prototyping plays a crucial role in automotive manufacturing, enabling the production of brackets, panels, and housings integral to vehicle assembly. By utilizing rapid prototyping techniques, automotive manufacturers can test new designs for performance, durability, and fit before committing to full-scale production. This approach not only accelerates the design validation process but also helps reduce development time and costs, ensuring that only the most reliable and cost-effective components move forward in production.
Aerospace
In aerospace, lightweight, high-strength components are crucial for performance and safety. Sheet metal prototyping enables the creation of structural components, such as frames, engine parts, and protective panels that meet stringent weight, durability, and safety requirements. This process allows manufacturers to test and refine designs early in development, ensuring components can withstand the demanding conditions of aerospace applications without compromising performance.
Medical Devices
In the medical industry, sheet metal prototyping is essential for creating a range of components, including surgical instruments such as forceps, scalpel handles, and clamps, as well as equipment enclosures and diagnostic tools. The ability to rapidly produce custom metal parts helps streamline the development process, ensuring these devices meet stringent regulatory approvals and performance standards required for patient safety and reliability.
Consumer Electronics
Custom enclosures and casings for smartphones, laptops, and other devices are often produced through sheet metal prototyping. This process allows manufacturers to create durable, high-quality enclosures that effectively protect sensitive electronics. Techniques like die stamping and corner stamping are used to form precise, robust shapes. These methods ensure the casings have both structural integrity and the necessary design features, such as reinforced corners, to withstand everyday wear and provide optimal protection for internal components.
Industrial Equipment
Sheet metal prototyping is commonly used to fabricate machine guards, electrical boxes, and structural supports, allowing manufacturers to test designs for strength and functionality in demanding industrial environments. While electrical boxes are a typical use case, machine guards and structural supports, often made of sheet metal, offer vital protection and stability. For instance, custom supports might be used to reinforce heavy machinery or maintain structural integrity in complex equipment, providing solutions tailored to specific industrial needs.
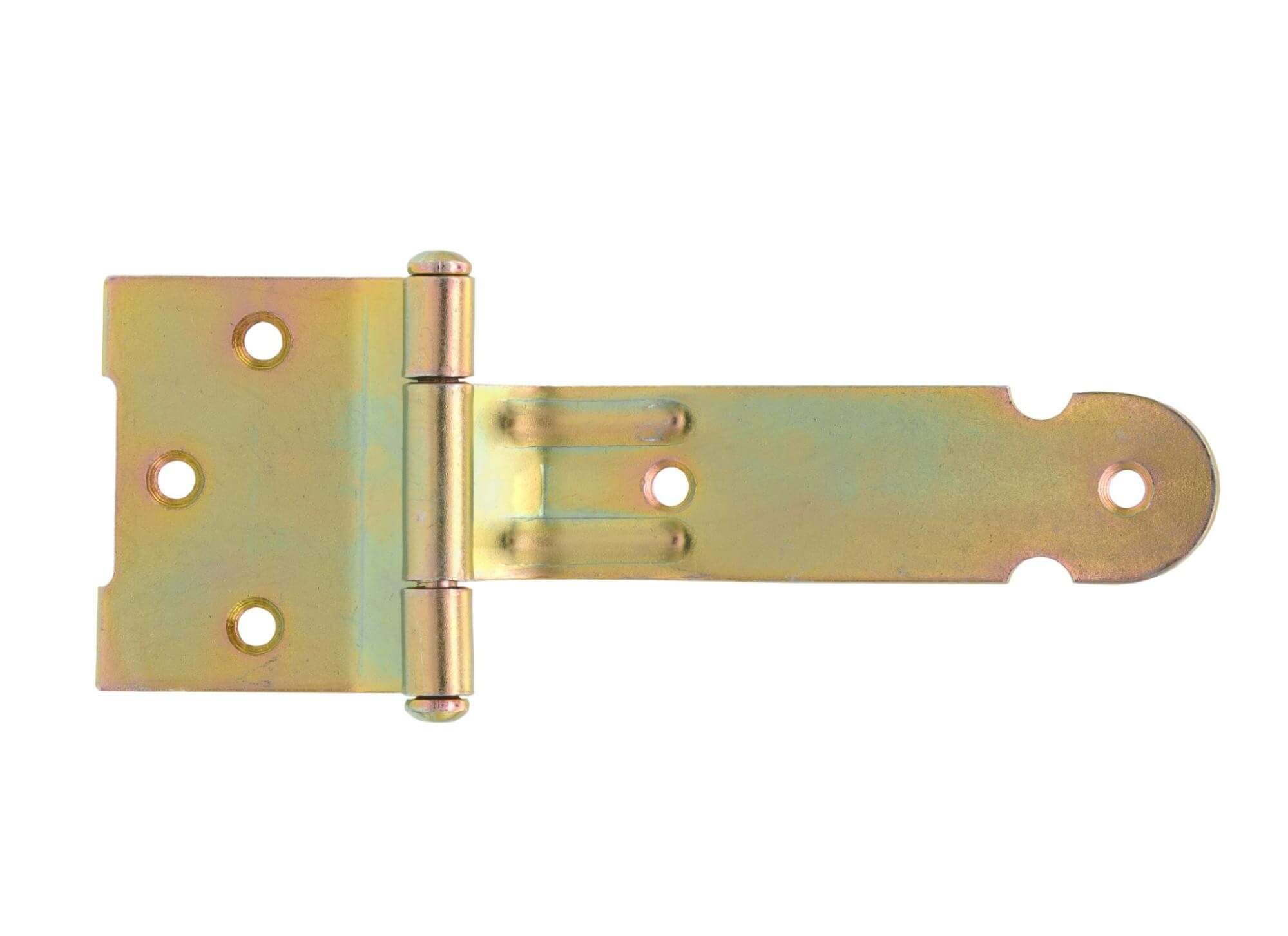
Hinge with sheet metal components
Sheet Metal Prototyping vs. 3D Printing vs. CNC Machining
When deciding which prototyping method to use, it’s important to consider key factors like speed, cost, material properties, and the specific needs of your project. The table below compares these three processes in these critical areas:
Sheet Metal Prototyping | 3D Printing | CNC Machining | |
Speed | Fast turnaround for metal parts | Very fast for plastic/resin; slower and more costly for metal | Slower due to precise milling and cutting |
Cost | Cost-effective for low–medium volumes; minimal tooling required | Low cost for small plastic parts; high cost for metal parts | Higher setup/tooling costs |
Material Compatibility | Uses real production metals (e.g., steel, aluminum) | Primarily for polymers, but can do metals and composites | Excellent for metals; high precision |
Sheet Metal vs. CNC vs. 3D Printing
Opt for sheet metal prototyping when your final part will be made of sheet metal, or when you need to test a design with similar material properties. This method is ideal for structural components, brackets, and enclosures where strength and durability are critical.
How To Optimize Your Designs for Sheet Metal Prototypes
Focus on manufacturability, material compatibility, and the intended production process. While it’s important to consider factors like temperature, corrosion, and strength, avoid over-optimizing for the prototype alone. The goal is to create a prototype that closely mirrors the final part in shape, size, and performance, without deviating from production realities.
Design for Manufacturability (DFM) Principles for Sheet Metal
Apply DFM principles early to ensure both prototype and final production run smoothly. Use consistent bend radii, minimize tight tolerances, and avoid overly complex geometries. Align holes, cutouts, and bends with standard tooling. These practices reduce rework and ensure a smoother manufacturing transition.
Avoiding Mistakes and Optimizing for Cost with Sheet Metal Prototypes
To streamline sheet metal prototyping and reduce production costs, avoid these common pitfalls and follow best practices:
- Avoid Sharp Internal Corners: Use generous radii to reduce stress concentrations and prevent cracking.
- Choose the Right Material: Match materials to the intended environment and stress conditions (e.g., temperature, corrosion resistance, strength).
- Provide Adequate Clearance: Ensure sufficient spacing between parts to avoid assembly or movement issues.
- Use Standard Material Thicknesses: This reduces cost and simplifies manufacturing.
- Simplify geometry: Minimize the number of welded or joined parts to cut down on labor and tooling costs.
- Align With Final Production Intent: Design prototypes to reflect the actual production setup, avoiding costly redesigns later.
- Collaborate With Your Prototyping Partner: Work together to identify material or cost-saving opportunities before moving to production.
Learn more about how to optimize your designs for sheet metal with our sheet metal design guide.
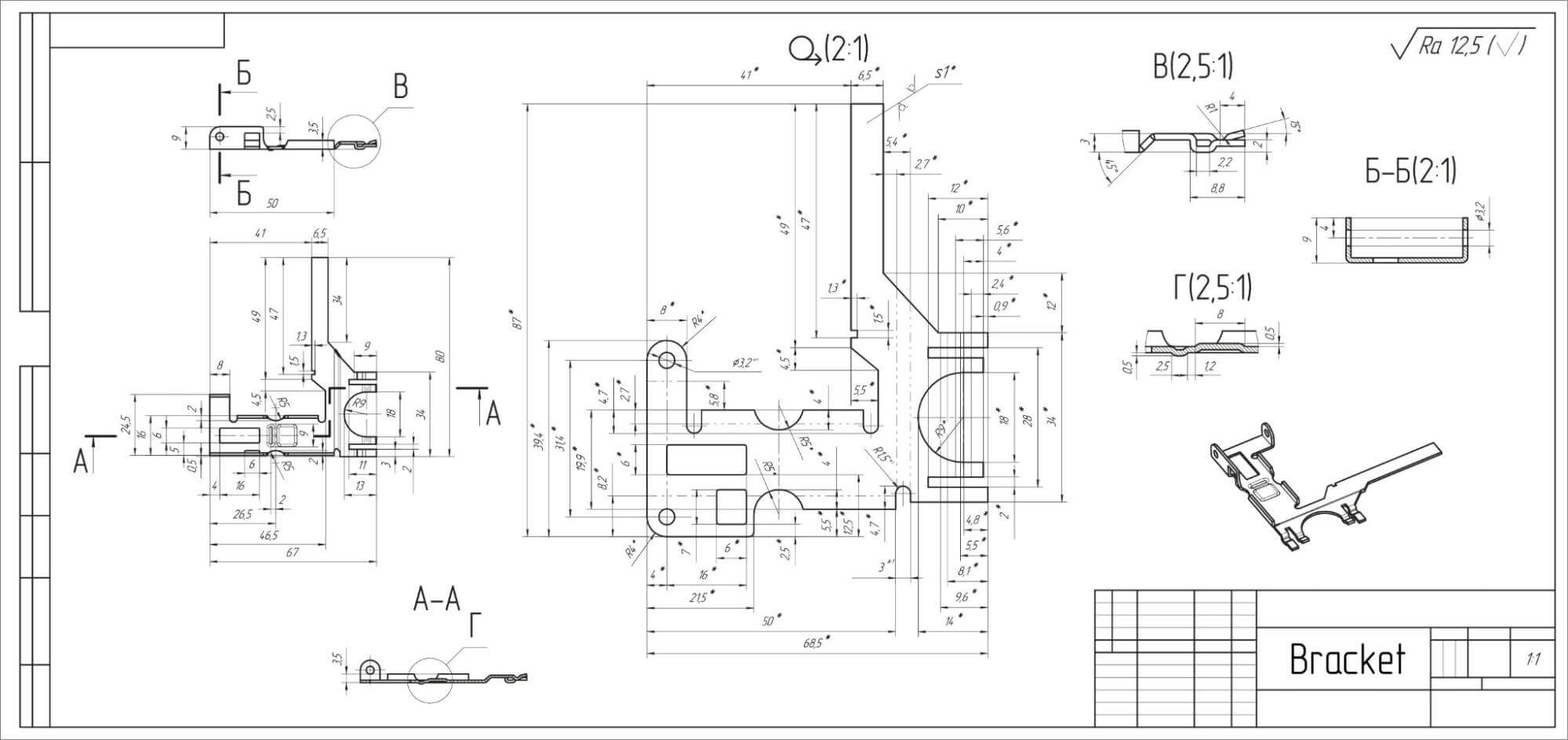
Sheet metal 2D drawing showing flat pattern and dimensions
How Fictiv Supports Sheet Metal Prototyping
Fictiv streamlines sheet metal prototyping by combining digital tools with expert support. Its platform simplifies the transition from design to production, helping teams move faster, reduce risk, and maintain high quality throughout the product development cycle.
Fast Quoting and Production for Rapid Turnaround
Fictiv’s digital manufacturing platform streamlines the quoting and ordering process, enabling engineers to move from design to prototype quickly. With instant quotes and automated order processing, teams can reduce lead times and accelerate iteration cycles.
DFM Feedback and Expert Support for Optimal Design
Fictiv provides design for manufacturability (DFM) feedback during the quoting process, helping you optimize designs not just for prototyping, but for final production as well. This early insight enables better performance, reduced costs, and fewer downstream issues. Their team of manufacturing experts offers guidance on material selection, cutting methods, and assembly techniques—ensuring your prototype is both high-quality and aligned with the requirements of full-scale production.
End-to-End Manufacturing Capabilities
From prototype to full-scale production, Fictiv’s network of manufacturing partners handles all stages of the process. Whether you need rapid sheet metal prototyping or large-scale production, Fictiv ensures consistent quality and fast turnaround times, helping you bring products to market faster.
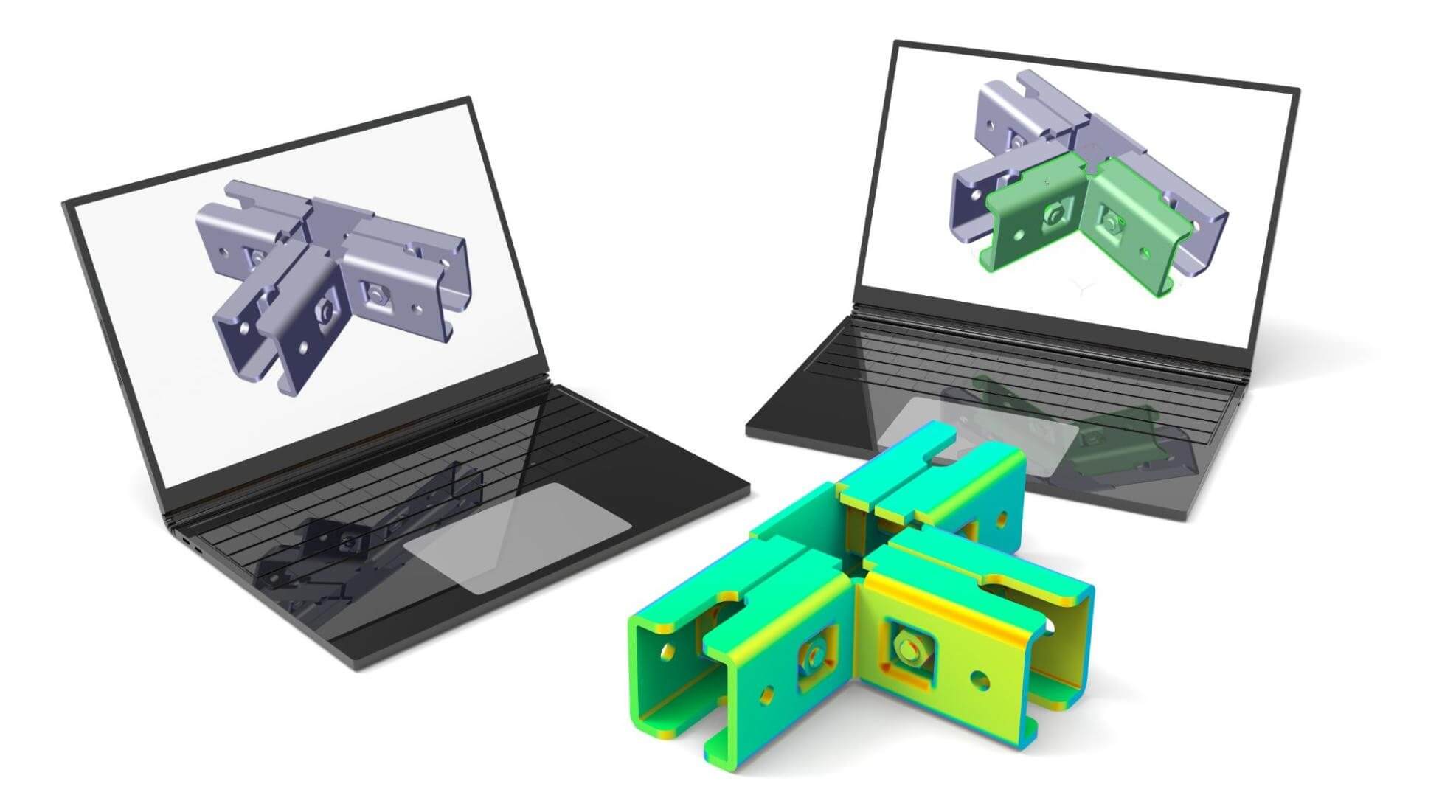
Sheet metal CAD and FEA
Accelerate Product Development With Rapid Sheet Metal Prototyping
Whether you need complex custom parts or simple functional components, Fictiv’s advanced manufacturing network and design feedback help you achieve the best results. From design to production, their streamlined process ensures cost-effective and efficient outcomes.
Get an instant quote today and accelerate your product development with Fictiv’s reliable sheet metal prototyping services!