Time to read: 9 min
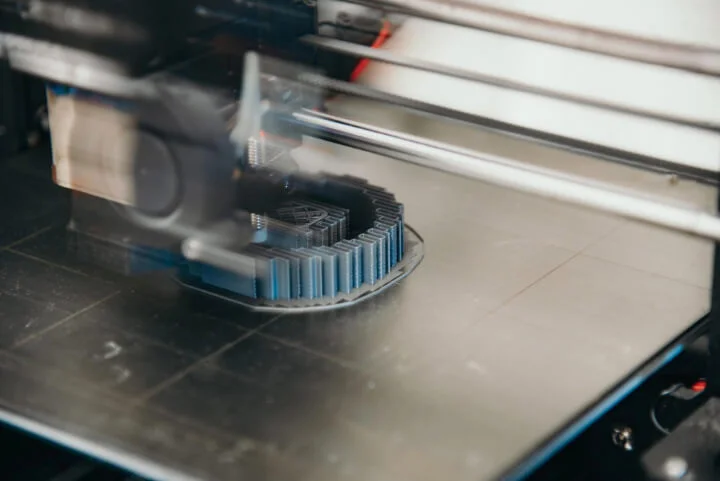
Rapid prototyping is a crucial tool for developing a new product or enhancing an existing one. It can be used to make, test, and refine different design choices at speed. Since the process is iterative, it provides an accelerated path to the best design solution. This saves product designers a lot of time by testing preliminary versions and making adjustments before full-scale development.
This article focuses on 3D printing as a rapid prototyping technique: what it is, how it works, and how it can be used to reduce time to market and costs, benefits, applications, as well as different methods of 3D printing rapid prototyping.
What Is Rapid Prototyping?
Rapid prototyping is a quick and iterative process of creating a preliminary version of a product in order to test and validate design concepts, functionality, and user interactions. It involves rapidly building and refining prototypes to gather feedback and make informed decisions before committing to full-scale development. In other words, when designing a physical product, rapid prototyping lets you try out materials, sizes, shapes, and colors to test their impact on fit, form, and function. The insights gained from these experiments can then be used to improve the final product — refining its design and performance. Going through different versions of the product improves the final product.
What Is 3D Printing?
3D printing, also called additive manufacturing, is a process of creating 3D objects by layering materials based on a digital model. It allows for the precision production of complex and customized objects made from plastics or metals.
What Is 3D Printing Rapid Prototyping?
Since rapid prototyping typically uses additive fabrication methods instead of subtractive methods, 3D printing has become a very popular option. Rapid prototyping in 3D printing involves using 3D printing technology to design and create physical models at a rapid pace, which helps get products to market faster. 3D printing produces a high-fidelity prototype that closely resembles the final product. While other methods like casting and CNC machining are used for rapid prototyping, many industries prefer 3D printing for proof of concept.
What Are the Different Types of 3D Printing Rapid Prototyping?
There are several 3D printing processes on the market. The most widely used methods for rapid prototyping are fused deposition modeling (FDM), stereolithography (SLA), selective laser sintering (SLS), Multi Jet Fusion (MJF), Digital Light Synthesis (DLS), and PolyJet. Other 3D printing technologies include binder jetting, digital light processing, laminated object manufacturing (LOM), and selective laser melting (SLM).
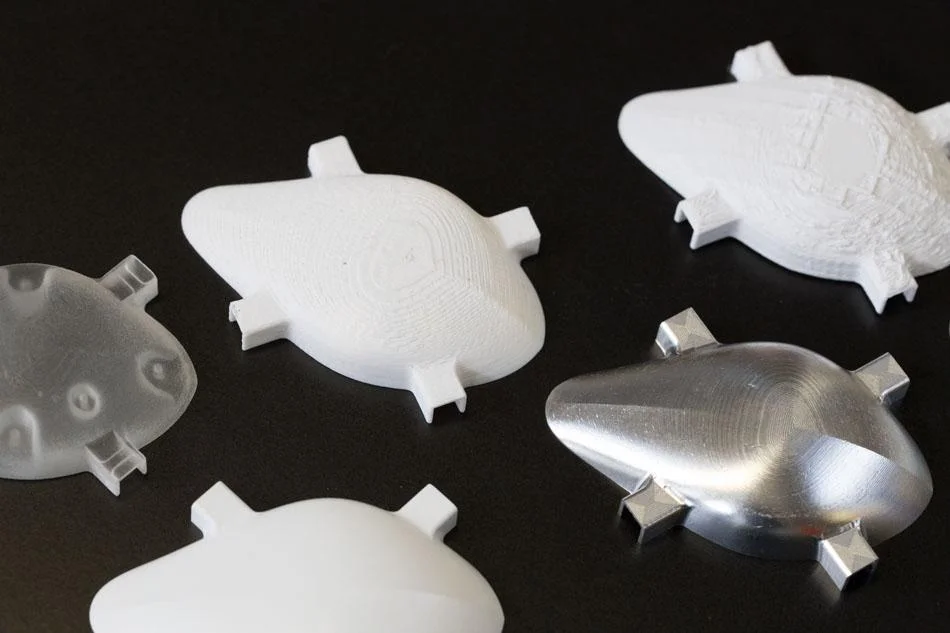
Listed and discussed below are some of the most popular 3D printing methods used for rapid prototyping:
Stereolithography (SLA)
SLA is a fast and economical method with cost-effective material options for producing rapid prototypes. This printing technology utilizes a bath of photosensitive liquid, from which a part is solidified layer by layer through computer-controlled UV light. It is ideal for creating prototype parts that seamlessly integrate into larger assemblies and offers several advantages. These include the ability to generate smooth surfaces, ensure accurate dimensions, and facilitate easy post-processing such as painting. SLA prototypes exhibit resistance to moisture and heat, ensuring their suitability for long-term use.
Selective Laser Sintering (SLS)
SLS makes use of a powder bed to construct models layer by layer, utilizing a laser to heat and sinter powdered materials. This versatile process is suitable for building both metal and plastic prototypes. SLS parts generally exhibit superior-strength properties compared to those produced using SLA. While the surface of SLS-finished products may be rough, this can be addressed through secondary finishing treatments. Opting for SLS is advantageous for stronger and more durable prototypes or project components. The benefits of SLS include enhanced mechanical properties in rapid prototypes, streamlined manufacturing times by eliminating unnecessary processes, reduced use of plastic materials, optimal results with post-processing effects like coloring and dyeing, and the absence of support structures during the prototyping phase.
Fused Deposition Modeling (FDM)
FDM is a cost-effective and user-friendly 3D printing process. FDM utilizes a thermoplastic filament melted inside a printing nozzle barrel, with the liquid plastic deposited layer by layer to form the final product. This method is known for its speed, affordability, large build volumes, and vast range of available materials, making it an excellent choice for product development and rapid prototyping. Key benefits of this technology include the efficient use of materials and the minimization of waste in the process. Another advantage is the ability to apply multiple colors to prototypes during a single production phase.
Multi Jet Fusion (MJF)
MJF is a cutting-edge 3D printing technology known for its speed and precision. MJF uses an inkjet array to apply fusing and detailing agents across a bed of powdered material, which is then fused by a heat source. This technology is ideal for functional prototypes and end-use parts with excellent mechanical properties and surface quality.
MJF offers several advantages, including high production speeds and the ability to produce complex geometries without the need for support structures. The process yields parts with consistent strength and dimensional accuracy. Additionally, MJF produces parts with fine details and smooth surface finishes, making it suitable for both prototyping and production runs. Key benefits of MJF include reduced production times, high material efficiency, and the ability to create parts with intricate details and uniform mechanical properties.
Digital Light Synthesis (DLS)
DLS is an advanced 3D printing technology developed by Carbon. DLS uses digital light projection, oxygen-permeable optics, and programmable liquid resins to produce high-quality parts. The process involves projecting UV light through an oxygen-permeable window, curing the resin layer by layer. This method is known for its ability to create isotropic parts with excellent mechanical properties and surface finishes.
DLS is particularly advantageous for producing functional prototypes and end-use parts with complex geometries. The technology supports a wide range of materials, including elastomers, rigid plastics, and high-temperature resins. Key benefits of DLS include the production of parts with smooth surfaces, high resolution, and excellent mechanical properties. Additionally, DLS enables rapid production times and uniform strength and durability.
PolyJet
PolyJet is a versatile 3D printing technology known for its ability to produce high-resolution parts with multiple materials and colors. The process involves jetting photopolymer droplets onto a build platform, where they are cured layer by layer using UV light. PolyJet is ideal for creating detailed prototypes, molds, and intricate models with complex geometries.
PolyJet offers several advantages, including the ability to produce parts with fine details and smooth surface finishes. The technology supports the use of multiple materials and colors within a single print, enabling multi-material and multi-color prototypes. This versatility makes PolyJet suitable for a wide range of applications, including medical models, consumer products, and intricate mechanical components. Key benefits of PolyJet include high-resolution printing, the ability to combine multiple materials and colors, and the production of parts with excellent surface quality and detail.
What Are the Steps of 3D Printing Rapid Prototyping?
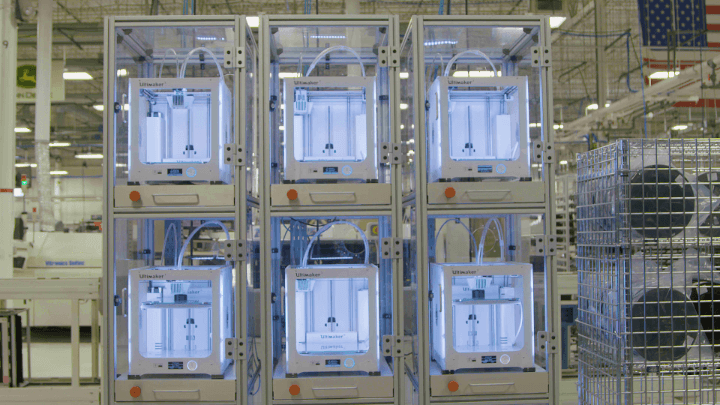
3D printing rapid prototyping, or prototyping in general, only uses five steps to create the prototypes. These are as follows:
Step 1: CAD Solid Modeling
The rapid prototyping process begins with a valid, solid computer-aided design (CAD) model representing the part design. Designers can use existing CAD files or create new ones, making adjustments if needed to support prototyping purposes. This step establishes the foundation for the physical prototype.
Step 2: Model Conversion to STL
To ensure consistency across different CAD packages, the solid model is converted to the STL format, which is the standard in the rapid prototyping industry. This format represents an object’s 3D boundary geometry using triangular facets.
Step 3: STL Model Slicing
The STL model is brought into proprietary slicing software, typically provided with the printing machine. This software allows users to adjust the size, location, and orientation of the model. The slicing program then divides the STL model into thin layers, ranging from 0.001 in. (0.0254 mm) to 0.01 in. (0.254 mm) thick, depending on the build technique. The software also generates tool patterns for both build and support areas for each layer.
Step 4: Model Fabrication
With the sliced STL model, physical prototypes are fabricated using various build techniques such as polymers, wax, ABS filament, liquid resin, or ceramic and metal powders. The machines construct the prototype one layer at a time, with minimal intervention required. The build orientation is crucial as it impacts both part properties and build time.
Step 5: Post-Processing
The final step involves post-processing, in which the fabricated prototype is removed from the machine. Supports are detached, and, if necessary, photosensitive or thermalsensitive materials are fully cured before use. Some cleaning and surface treatment may be required, including sanding, sealing, and painting, to enhance the model’s appearance and durability.
What Are the Prototyping Applications of Rapid Prototyping 3D Printing?
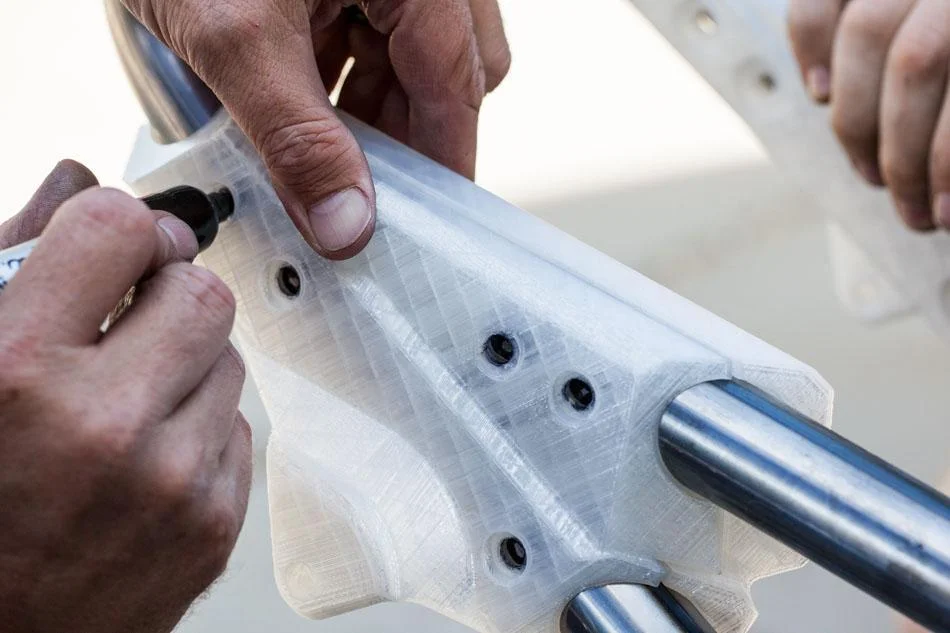
3D printing in rapid prototyping has diverse applications, including:
- Proof-of-Concept Prototypes: Rapid prototyping starts with proof-of-concept (PoC) prototypes or concept models, enabling designers to test or validate ideas and assumptions with minimal risk. These prototypes, developed in the early stages, exhibit minimal functionality necessary for validating assumptions before progressing to subsequent development phases. They are there to quickly explore and communicate concepts, utilizing 3D printing tools that facilitate the quick generation of physical models.
- Functional or “Works-Like” Prototypes: Engineering teams work on functional prototypes to test, iterate, and refine mechanical, electrical, and thermal systems. The idea is to validate the functions of a product, with a focus on demonstrating its operational capabilities. While these prototypes may differ in appearance from the final product, they involve core technologies and functions crucial for development. Critical core functions are often developed and tested in separate subunits before integration into a single product prototype.
- Visual or “Looks-Like” Prototypes: Looks-like prototypes provide abstract representations of the final product’s appearance, allowing designers to validate user interfaces, ergonomics, and overall user experience. These designs demonstrate and validate the visual aspects of a product, such as shape, size, color, and texture. Beginning with sketches or foam or clay models and progressing into CAD modeling, these prototypes facilitate iterative design cycles. Throughout these iterations, industrial designers aim to manufacture looks-like prototypes accurately resembling the final product, incorporating its colors, materials, and finishes.
- Pre-Production or Engineering Prototypes: These prototypes integrate findings from previous prototypes to create near-finished products for showcasing to stakeholders, investors, customers, and manufacturers.
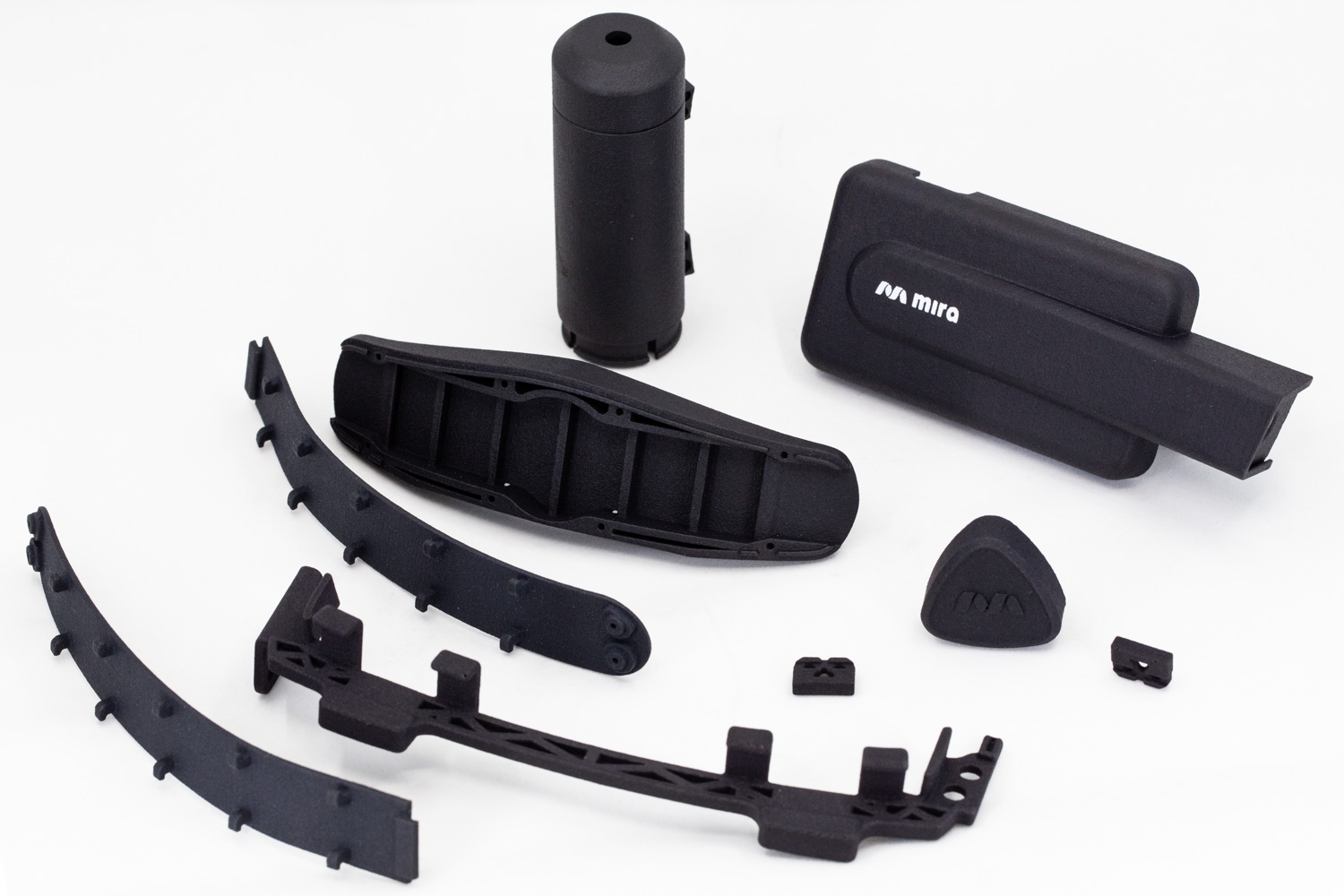
What Are the Advantages of Rapid Prototyping 3D Printing?
Rapid prototyping using 3D printing offers numerous advantages that contribute to its widespread adoption in various industries. Some key benefits include:
- Rapid prototyping significantly reduces the time required for product development cycles. Design iterations can be quickly translated into physical prototypes, allowing for faster design validation and refinement.
- Traditional prototyping methods can be expensive and time-consuming. 3D printing allows for cost-effective production of prototypes, eliminating the need for expensive molds or tooling.
- 3D printing enables the creation of complex and intricate designs that may be challenging or impossible with other traditional manufacturing methods. This design flexibility is especially beneficial for producing customized or intricate parts.
- Designers and engineers can rapidly prototype and test multiple iterations of a product. This iterative testing process helps identify design flaws, improve functionality, and enhance overall product performance.
- Traditional or subtractive manufacturing processes often leave behind a significant amount of material waste. In contrast, the additive process of 3D printing, with material deposited layer by layer, provides greater design opportunities to avoid waste.
Fictiv Simplifies Rapid Prototyping
Now that you know how rapid prototyping with 3D printing works, it’s time to transform your product ideas into reality with Fictiv. Simply create your account and upload your design files to gain access to industry-leading expertise, instant quotes, and high-quality custom parts delivered fast.
Frequently Asked Questions
Is 3D Printing the Same as Rapid Prototyping?
No, 3D printing is not the same as rapid prototyping. 3D printing is a broader term that involves various additive manufacturing processes used to create three-dimensional objects layer by layer from digital models. It includes applications beyond prototyping, such as manufacturing end-use products and creating models for artistic purposes. 3D printing is also not the only rapid prototyping method. Other methods like CNC and vacuum casting also form part of a suite of rapid prototyping technologies.
Is 3D Printing Good for Prototyping?
Yes, 3D printing is not only good for prototyping, but it can be used for rapid prototyping, which allows for quick design iterations through CAD (computer-aided design) software. It is also the preferred prototyping method for proof-of-concept prototypes due to its close resemblance to the final product.