Time to read: 15 min
Looking for a high-precision, cost-effective solution for medical device manufacturing? Injection molding delivers accuracy, regulatory compliance, and scalability for healthcare innovations.
It is a process used to manufacture a wide range of medical devices, from catheters and syringes to surgical instruments and implantable components. This highly precise and efficient method is essential for producing parts that meet the stringent requirements of the healthcare industry, including biocompatibility, sterility, and durability.
In this guide, we’ll provide a brief overview of medical injection molding and discuss the selection of common materials used, regulatory compliance, applications, and the latest advancements in the field.
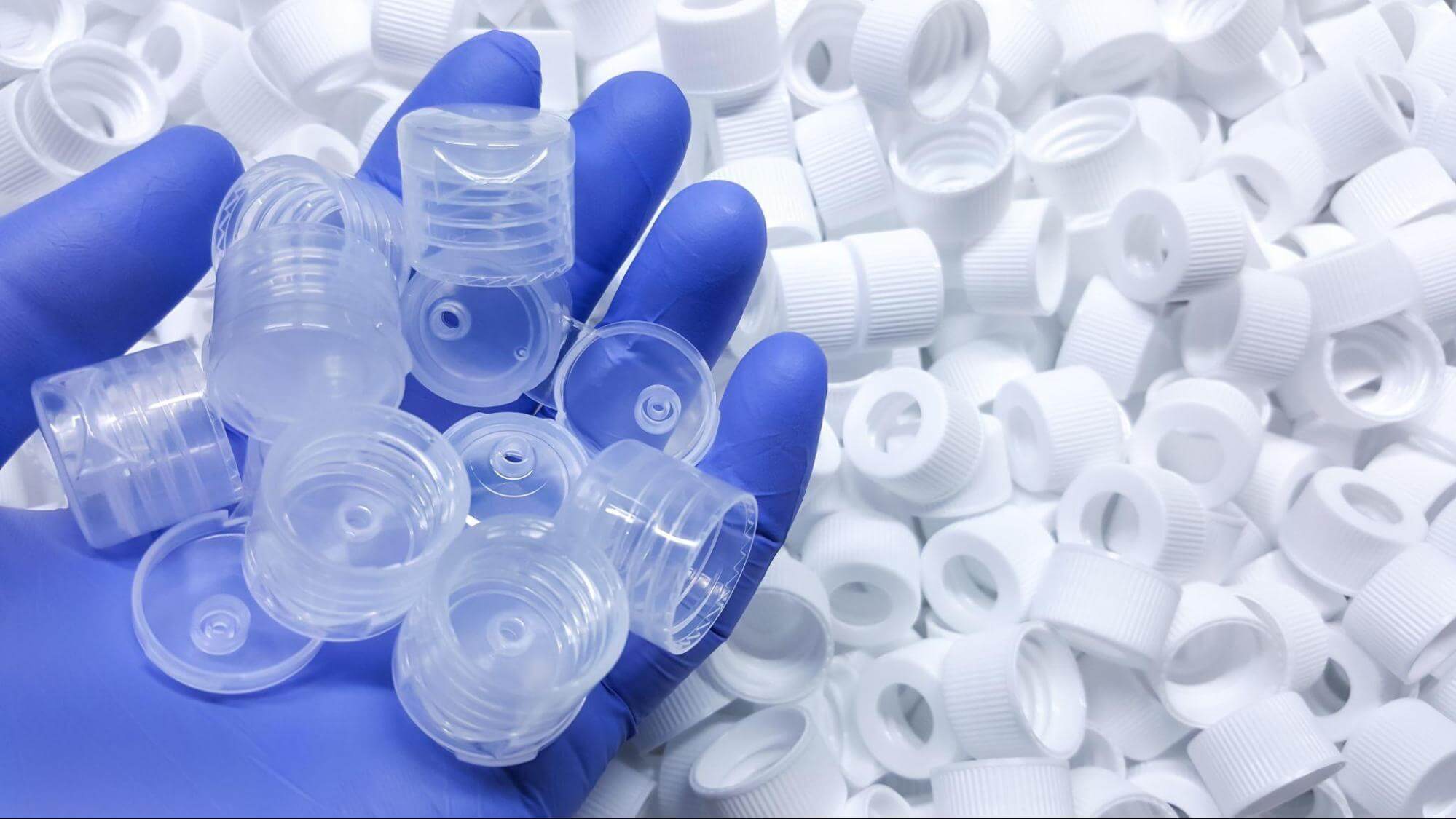
What Is Medical Injection Molding?
Medical injection molding is a manufacturing process used to produce precision plastic components for the healthcare industry. It is capable of consistently producing complex, high-volume components.
The process of creating medical devices through injection molding involves injecting molten medical-grade plastics into molds to shape the plastic into parts that adhere to strict tolerances, are biocompatible, and are durable. The molding process typically includes these four stages:
- Clamping: The mold is securely closed under high pressure.
- Injection: Molten plastic is injected into the mold cavity.
- Cooling: The material solidifies into the desired shape.
- Ejection: The finished part is removed from the mold.
Injection molding of medical components usually takes place in a controlled environment, also known as a clean room. This minimizes the chances of contamination, which is crucial to avoid in a medical setting. Clean rooms must adhere to strict standards to produce components that will not compromise patient safety.
All medical device components must meet stringent regulatory standards, including ISO 13485 and FDA (Food and Drug Administration), and undergo detailed quality control processes. These processes include precise documentation, real-time monitoring, and validation at every production stage, ensuring full traceability of materials, processes, and personnel involved.
Why Medical Injection Molding Is Essential in Healthcare
The healthcare industry has unique demands, and medical devices must meet stringent requirements while still being cost-effective to produce. Medical injection molding meets these demands by offering:
- Accuracy: Tight tolerances ensure that components are precisely sized and fit together as intended.
- Sterility: Cleanroom environments and biocompatible materials prevent contamination, ensuring products meet FDA and ISO standards.
- Cost Efficiency: Automated processes and high-volume production reduce costs, helping to make healthcare more accessible.
- Durability: Medical-grade plastics can withstand repeated sterilization, chemicals, and wear. They should also be able to withstand mechanical loading and be temperature resistant.
Common Medical Injection Molding Applications
Examples of the various products manufactured with medical injection molding are listed and discussed below.
Implantable Devices
Injection molding is used to manufacture implantable devices, such as knee and hip joints, dental implants, and other types of surgical implants. These products must be durable and compatible with human tissue.
Surgical Tools
Injection molding is also widely used to produce high-precision surgical tools, such as scalpel handles, forceps, clamps, and retractors. Materials used in molding surgical tools are selected for their strength, biocompatibility, and resistance to repeated sterilization processes, such as autoclaving.
Consumable and Disposable Medical Products
Many single-use medical products are injection molded, including:
- Syringes
- Test tubes
- Petri dishes
- Drip chambers
Laboratory Equipment
Medical research and testing frequently use injection-molded medical devices, such as containers, instrument handles, and microplates.
Medical Device Housings and Enclosures
Many medical devices and test equipment components require enclosures to help maintain their sterile condition and protect them from the environment. These are often made by injection molding.
Sterile Packaging Solutions
Beyond manufacturing the devices, injection molding is also used to create medical-grade packaging for them, such as blister pack components, vials and containers.
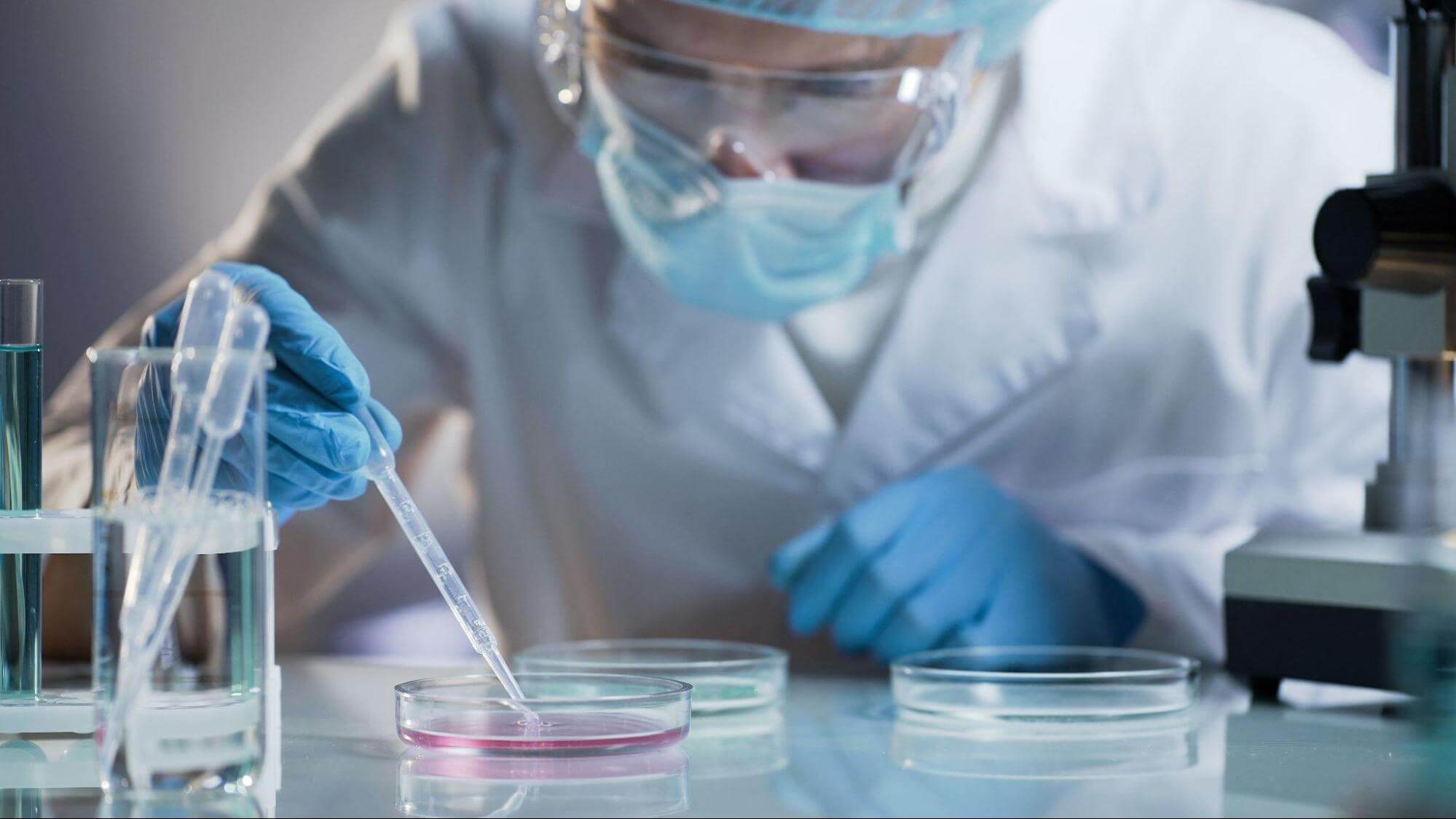
Key Techniques in Medical Injection Molding
A variety of injection molding techniques can be used to create medical components such as:
- Thin-wall molding
- Gas-assisted molding
- Insert molding
- Overmolding
- Metal Injection
- Liquid silicone molding
Thin-Wall Molding
Thin-wall injection molding is a manufacturing process used to create lightweight and durable parts with wall thicknesses typically less than 1 mm. It is especially suited for producing small, complex components that require a high degree of precision.
Since this method uses less material per part, it can be more cost-effective than conventional injection methods. This makes thin-wall molding ideal for high-volume production runs. A common application of this technique is the creation of compact enclosures for medical devices.
Gas-Assisted Molding
Gas-assisted injection molding is a low-pressure process that combines the precision of traditional injection molding with the added benefits of using pressurized gas, usually nitrogen or carbon dioxide. The gas is used to push the molten injected plastic into every nook and cranny of the mold. This creates hollow sections in parts with thicker walls while using less material. Once the molding process is complete and the part is completely cooled, the gas is vented. Then, after minor post-processing, such as trimming off flash, the part is ready to go.
Typically used for parts with large surface areas that demand detailed textures and superior surface quality, gas-assisted molding results in a smoother surface finish, better structural integrity, and no visible sink marks. This is because the pressurized gas evenly distributes the molten plastic against the mold walls, eliminating inconsistencies and reducing surface imperfections.
The gas also helps maintain uniform pressure throughout the cooling process, which minimizes internal stresses and enhances the part’s structural integrity. Additionally, sink marks are avoided by supporting the material from within, ensuring that the outer surface remains smooth and defect-free.
Insert Molding
Insert molding involves molding a secondary component over a pre-formed component, or insert. The existing part or inner part, which is usually metal but can also be plastic or ceramic, is placed into the mold before injecting molten plastic around it. This single-step process creates a strong molecular or mechanical bond between the two parts.
Molecular bonding occurs when the insert material is the same or similar to the encapsulating resin, creating a strong, leak-resistant joint. For example, molding a polyurethane bifurcation (a Y-shaped joint) to a polyurethane catheter achieves excellent results. The polyurethane resin and insert share identical or closely matched chemical properties, allowing their polymer chains to entangle and create a homogeneous interface. This eliminates the need for adhesives or mechanical fasteners, which reduces the risk of leaks or failure points.
Mechanical bonding, on the other hand, relies on the resin of the outer layer shrinking around the insert as it cools or locking onto surface irregularities on the insert, such as knurls, flares, or a rough, sandblasted finish. While shrinkage always occurs, it’s often insufficient to ensure strong or leak-proof joints. For dissimilar materials, mechanical retention features on the insert are essential to achieve the desired strength and performance.
Insert molding is widely used to produce medical devices such as insert-molded needle hubs, threaded fasteners, encapsulated electric components, luer fittings, and bifurcations.
Overmolding
Overmolding layers a polymer, such as silicone or thermoplastic elastomer (TPE), over a substrate to create a single, integrated part, with the benefit of eliminating the need for assembly once the part is done. Bonding occurs through both chemical and mechanical means—chemical bonds form at the molecular level, while mechanical bonds rely on the physical geometry of the interface between the two molded layers.
Insert molding differs from overmolding in that it involves molding over an inserted part that was pre-made and commonly metal, while overmolding involves molding one material over a molded part, often using two different materials in sequential steps. This means that overmolding molds two different parts in succession using the same machine, same cycle, same tools, etc. Only insert molding is compatible with metals, so if you require a plastic handle over a metal component, you’ll need to opt for insert molding, not overmolding.
Overmolding can be done in a continuous, automated two-shot molding process ideal for high-volume production or by pick-and-place molding, a manual or semi-automated method better suited for prototyping or low-volume needs. This technique is popular for making ergonomic handles for surgical instruments.
Metal Injection Molding
Metal injection molding (MIM) is an advanced manufacturing process that starts with a combination of powdered metal and thermoplastic binder. The mixture is heated, injected into a mold, and then cooled to form a part. After ejection, the binder is removed, and the part undergoes sintering—a high-temperature process that fuses the metal particles, creating a strong, dense, precise component.
Commonly used for surgical instruments and implants, MIM is ideal for high-volume production of complex, small-to-medium-sized medical parts. It offers superior strength, excellent surface finish, and tight tolerances. It can be a cost-effective alternative to CNC machining, especially for difficult-to-machine metals like stainless steel, cobalt-chromium, and titanium alloys.
Liquid Silicone Molding
Liquid silicone molding is used to manufacture medical products such as respiratory masks, tubing, and implants. Silicone is inherently biocompatible, which makes it ideal for medical applications.
The process uses liquid silicone rubber (LSR), a two-part elastomer that cures through a chemical process called crosslinking. During liquid silicone injection molding, the mixture is pushed into the mold under high pressure and cures in about 30 seconds. The process requires a controlled, hygienic environment to prevent contamination from dust, moisture, or ambient air, which could compromise the integrity of the final product.
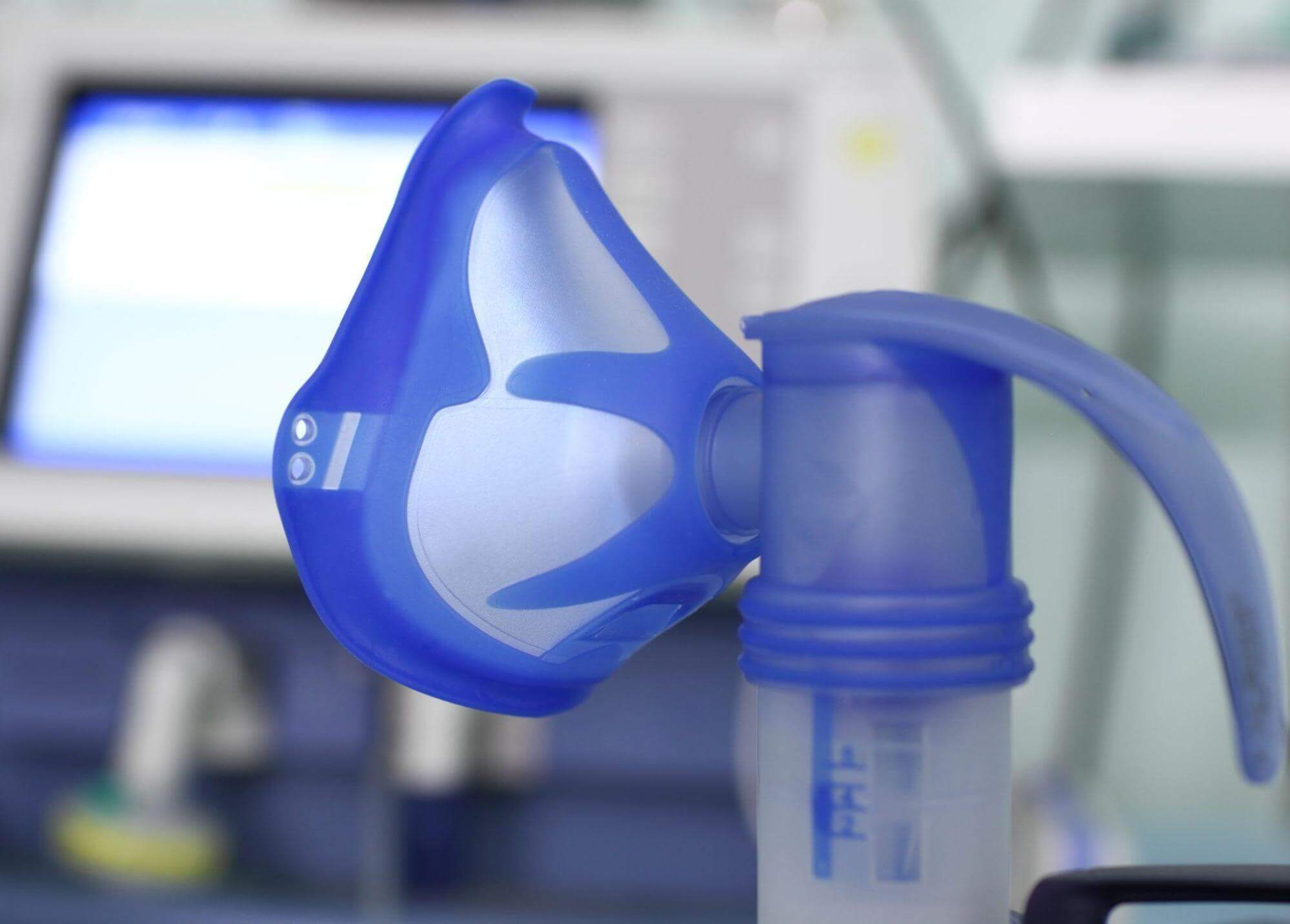
Plastic Materials Used for Medical Injection Molding
Injection molding uses different materials, including thermoplastic and thermosetting plastics. However, the primary option for medical devices is thermoplastic polymers, which can be heated, molded, and remelted several times without compromising their structural integrity. This is what makes them ideal for medical devices; their ability to be remelted and reshaped.
In medical device manufacturing, the thermoplastic materials are pushed into molds in a molten state, where they then cool and dry into the desired shape. Molds can have simple open-and-shut designs or more complex configurations, depending on the specific part requirements.
Thermoset plastics, however, are not as ideal for medical device injection molding. These plastics have strong covalent bonds between polymer strands, which results in useful mechanical properties: high melting points, chemical resistance, and mechanical strength.
The downside of thermosetting materials is that once cured, they cannot be remelted or reshaped like thermoplastics. Their lack of recyclability makes them less ideal for the medical industry. These materials are usually better suited for adhesives, protective coatings, or high-heat applications.
The following are descriptions of some of the most common medical-grade plastics for injection molding:
Polyethylene (PE)
This medical-grade plastic has impressive stiffness and tensile strength. It can withstand harsh environmental conditions and is highly compatible with human tissue. Common applications for PE in the medical industry include tubing, connectors, prostheses, and containers. There are different types of PE:
- High-Density Polyethylene (HDPE): This PE variant is rigid and moisture-resistant. It is ideal for pharmaceutical products such as medicine bottles, prescription vials, caps and closures, syringe components, medical device packaging, laboratory bottles and jars, and ointment tubes.
- Low-density polyethylene (LDPE): This translucent and flexible material is often used for squeezable bottles and medical tubing.
- Ultra-High Molecular Weight Polyethylene (UHMW): Offers exceptional wear resistance and is ideal for applications such as orthopedic implants.
Polypropylene (PP)
PP offers exceptional strength and is more resistant to moisture and gases than PE. It’s also resistant to impact, cracking, temperature degradation, wear and tear, and radiation. Another key feature of this material is that it is suitable for storing fluid drugs. Critical components such as knee and hip replacements, syringes, and connectors are all made from PP. For knee and hip replacements, injection molding is used to create the plastic components, like liners and spacers, that minimize metal-on-metal contact and improve the implant’s performance and longevity.
Polycarbonate (PC)
This naturally transparent, solid material exhibits excellent mechanical properties. Fexible, tough, and resistant to impact breakage, temperature degradation, and abrasion, PC is also highly compatible with biological tissue. It is ideal for medical equipment including protective gear, clear masks, and oxygenators.
Polyetheretherketone (PEEK)
PEEK is exceptionally resistant to harsh environments, including high temperatures, chemicals, radiation, and wear and tear. This high-quality thermoplastic offers excellent dimensional stability, even after exposure to stress. Common uses for PEEK include orthopedic implants and prosthetics.
Polystyrene (PS)
This material is not as flexible as the others described here, but it still offers exceptional mechanical properties and is compatible with human tissue. It also displays great dimensional stability. Polystyrene is often used for medical components such as culture trays, Petri dishes, gloves, vials, pipettes, implants, and some diagnostic components.
Perfluoroalkoxy (PFA)
This fluoropolymer has very high thermal resistance, excellent creep resistance at elevated temperatures, and resists a wide range of chemicals.
Fluorinated ethylene propylene (FEP)
This fluoropolymer has low friction, good impact resistance, and excellent chemical resistance. FEP is also flexible, transparent, and considered to be biocompatible.
Thermoplastic Elastomers (TPEs)
TPEs have a unique balance of thermoplastic’s processability and rubber-like elasticity. They are ideal for overmolded components or catheters.
Silicone
Silicone, while technically not a plastic, is a rubber-like material with excellent mechanical properties for medical devices. It is compatible with body tissue, offers flexibility, and can be used to create a variety of devices, including tubing, connectors, and catheters.
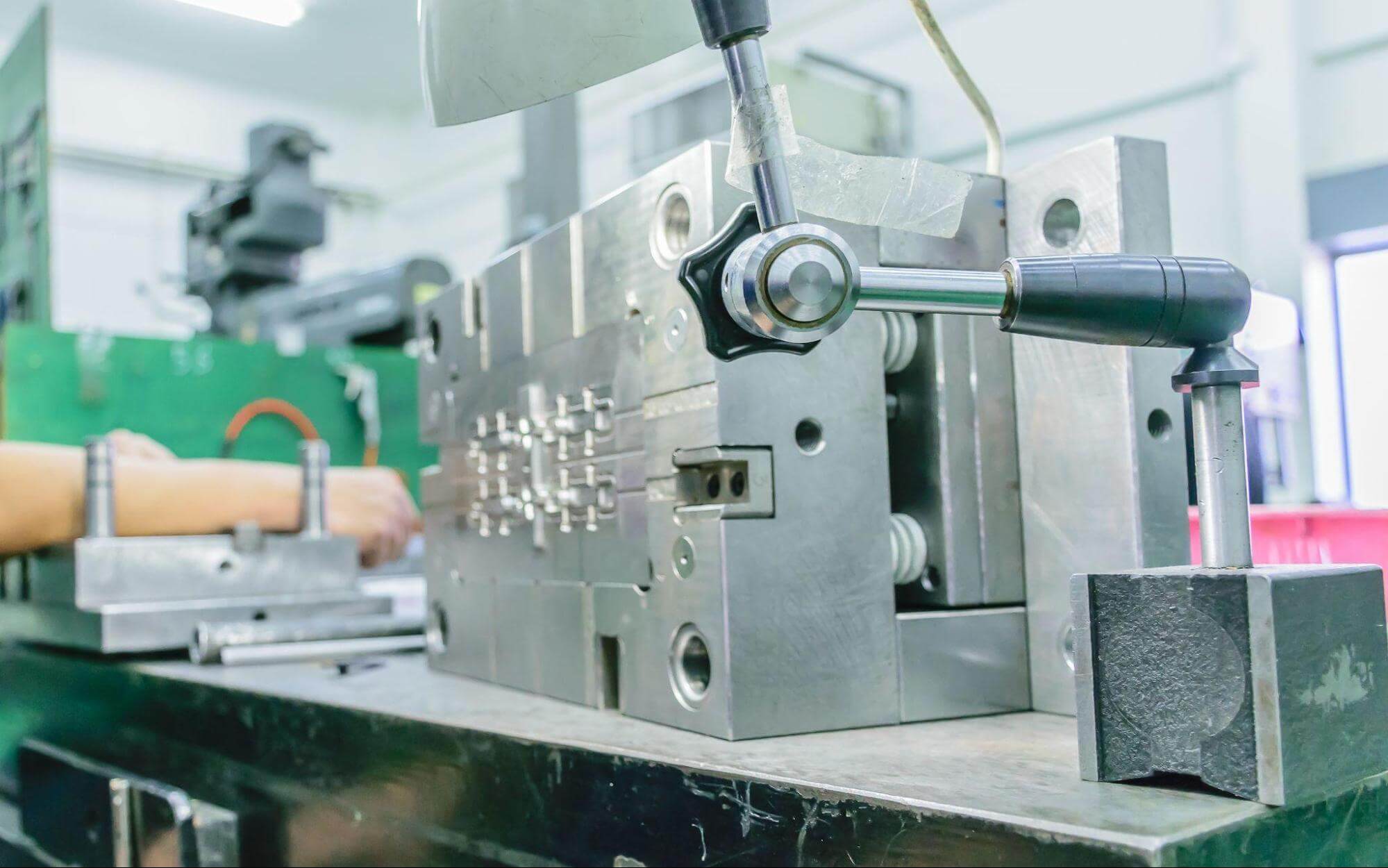
Medical Injection Molding Standards and Requirements
Medical plastic molding is a highly precise and critical process with little room for error. The materials chosen must meet stringent requirements to ensure safety, functionality, and reliability of medical devices. Below are the essential factors to consider in medical plastic molding:
Regulations and Compliance
Compliance with regulatory standards is compulsory when manufacturing injection-molded parts and products for the medical industry. The medical sector is one of the most heavily regulated industries, and any components produced—whether through injection molding or other methods—must meet stringent requirements set by the FDA (Food and Drug Administration) and be ISO (International Organization for Standardization) certified. These regulations ensure that medical devices are safe, effective, and reliable for patient use.
FDA Regulations
The FDA enforces rigorous standards to guarantee the cleanliness, sterility, and overall safety of medical devices. These regulations apply to many products, including implantable devices, surgical instruments, and other medical components. Key considerations include:
- Material Suitability: The materials used in medical devices must be capable of withstanding sterilization processes such as autoclaving, gamma radiation, or ethylene oxide treatment without degrading. They must also be biocompatible, meaning they do not cause adverse reactions when in contact with human tissues or fluids.
- Manufacturing Process: The injection molding process itself must meet FDA guidelines. This often involves audits to ensure that production facilities adhere to good manufacturing practices (GMP) and maintain a cleanroom environment to prevent contamination.
- Documentation and Traceability: Manufacturers must maintain detailed records of materials, processes, and quality control measures to demonstrate compliance during FDA inspections.
Failure to meet FDA regulations can result in product recalls, legal penalties, and damage to a company’s reputation. Therefore, it is essential to work with materials and manufacturing partners with a proven track record of FDA compliance.
Medical Device Classes
Medical devices are classified according to their potential for causing harm to patients, the general public, or to other personnel who use or operate the medical device. This classification determines the degree of required regulatory oversight.
The U.S. FDA (Food and Drug Administration), and the EU MDR (Medical Device Regulation) both divide medical devices into three classifications, where Class I refers to the lowest-risk medical devices and Class III refers to the highest-risk. The EU MDR further breaks down Class II devices into two subcategories: IIa and IIb.
Class I medical devices are not intended to support or sustain life and will not present an unreasonable risk of illness or injury to a patient. Examples include wheelchairs, glasses, hospital beds, and test tubes.
Class II encompasses any medical device for which general controls are deemed insufficient to provide reasonable safety and effectiveness. Examples include contact lenses, syringes, and pregnancy tests. The EU MDR adds two subcategories:
- Class IIa refers to devices that present a medium risk.
- Class IIb refers to devices that pose a high risk.
Class III medical devices are usually designed to sustain or support life and may present an unreasonable risk of injury or illness. Examples include pacemakers, defibrillators, and implanted prostheses.
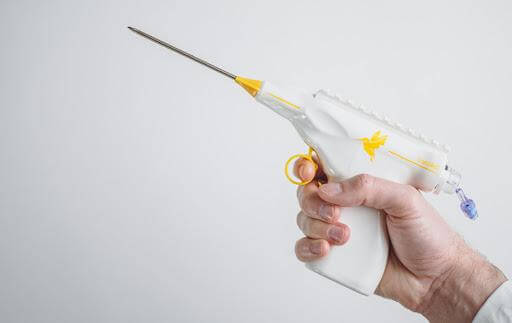
ISO Certification
The medical device industry is tightly controlled to ensure patient safety. Listed below are some of the common standards that affect manufacturing, including plastic injection molding.
- ISO 13485 – Medical Devices
- ISO 10993 – Biological Evaluation of Medical Devices
- ISO 14644 – Cleanrooms & Associated Controlled Environments
ISO 13485 – Medical Devices
ISO 13485 outlines the requirements for a quality management system (QMS) when producing medical-grade products. It is the most common standard used in medical device manufacturing. ISO 13485 is not limited to plastic injection molding but rather covers the general requirements for all manufacturing technologies that are used to produce medical equipment. This standard was developed to ensure that consistent quality is maintained and that medical devices and equipment are produced in a safe and effective manner.
To achieve these goals, ISO 13485 outlines processes and procedures to manage risk and regulatory compliance while providing mechanisms to continuously improve the QMS whenever a gap or potential for improved performance is noted. The standard defines best practices for documentation, training, traceability, research and design, production, and how to handle non-conformances. For both the part designer and the injection molders, there are well-defined responsibilities.
The QSR (Quality System Regulations), also referred to as 21 CFR part 820, as outlined by the FDA, has many parallels with ISO 13485. In the United States, the QSR may be used as a supplement or replacement for the ISO 13485 standard.
ISO 10993 – Biological Evaluation of Medical Devices
ISO 10993 focuses primarily on the biocompatibility requirements for medical devices. It encompasses products that are designed to come into direct or indirect contact with the body. The goal of ISO 10993 is to reduce the risk of adverse effects on patients when exposed to materials that include, but are not limited to, injection molded plastics. ISO 10993 compliant materials are non-toxic, do not affect the immune system, or do not potentially cause cancer.
The ISO 10993 standard consists of 23 parts or subsections. This includes processes and procedures for animal welfare requirements, tests for carcinogenicity, reproductive toxicity, in vitro cytotoxicity, and various sterilization techniques. USP (United States Pharmacopeia) Class VI covers similar biocompatibility requirements for plastics and, as such, is sometimes used in place of ISO 10993 or as a supplement. For designers, this standard can play an important role in material selection.
ISO 14644 – Cleanrooms & Associated Controlled Environments
ISO 14644 regulates the use of cleanrooms during medical device manufacturing. It defines the various cleanroom classes from Class 1 to Class 9, where Class 1 has the most stringent cleanliness requirements.
In cleanrooms, the amount and size of airborne particles are carefully controlled to reduce the chances of exposing sensitive medical components to these particles. ISO 14644 also outlines specific requirements for designing, manufacturing, and maintaining cleanrooms for optimal performance. Designers may need an injection molder with a Class 7 or Class 8 cleanroom to limit the potential for contamination during manufacturing.
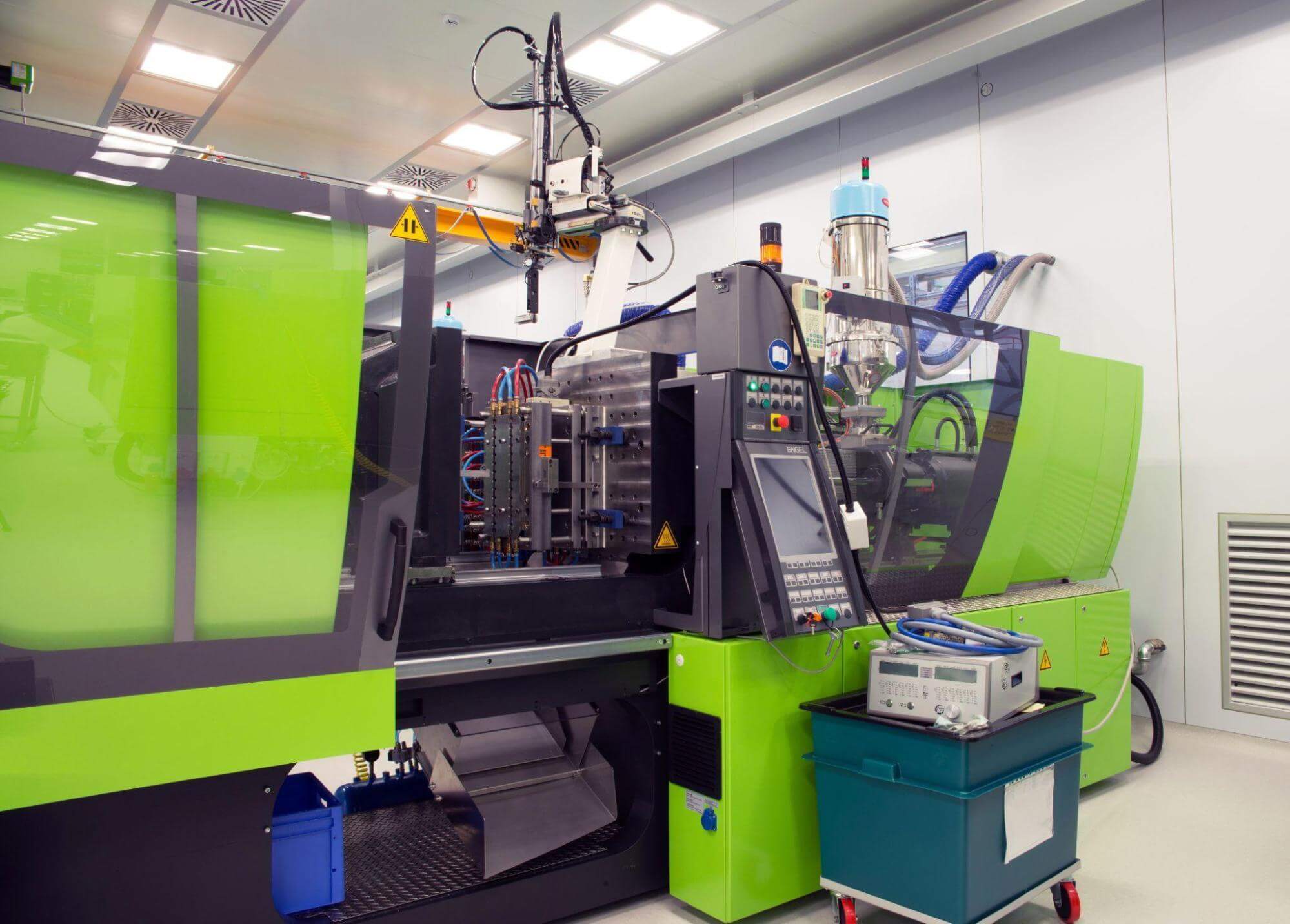
Withstanding Sterilization Processes
Sterilization is a non-negotiable requirement for medical devices. Any part that comes into contact with the human body must be contaminant-resistant and capable of enduring sterilization methods like autoclaving, gamma radiation, or chemical treatments without damage.
Operational Environment
Medical devices often operate in challenging conditions, exposing them to heat, chemicals, liquids, vibration, and physical stress. Materials must be reliable and durable to perform consistently under these adverse conditions. Plastics used in medical molding are typically selected for their ability to handle such demands without compromising performance.
Durability and Strength
Using breakable or weak materials in the medical field is unacceptable, especially for components like implants and surgical tools. Each selected material must have a high durability index and exhibit excellent tensile strength to minimize the risk of biohazards.
Recent Advancements and Future Innovations in Medical Injection Molding
Medical injection molding is undergoing a rapid evolution, driven by cutting-edge technologies and emerging trends that are transforming how medical devices are designed and manufactured. These advancements are not only improving the precision and efficiency of the process but also enabling the creation of more complex, customized, and sustainable medical solutions. Here’s a look at the key innovations shaping the future of medical injection molding:
Scientific Molding and AI Optimization
The demand for highly accurate and consistent medical devices has led to the development of scientific molding, a data-driven approach that optimizes the injection molding process. This method uses real-time monitoring and advanced analytics to ensure every part meets exact specifications.
One of the most exciting advancements is the integration of artificial intelligence (AI) into molding processes. AI algorithms continuously adjust molding parameters, such as temperature, pressure, and cycle time, to improve product quality and reduce material waste. This enhances manufacturing efficiency and also supports more sustainable practices by minimizing resource consumption.
Integration of 3D Printing
3D printing is revolutionizing the prototyping and production of medical devices. By combining 3D printing with traditional injection molding, manufacturers can accelerate the development of prototypes and create highly customized components. This hybrid approach allows for faster design iteration and the production of patient-specific devices, such as implants and prosthetics.
For example, 3D-printed injection molds can be used to test new designs before committing to expensive tooling, reducing development time and costs. This innovation is particularly valuable in creating complex geometries that were previously difficult or impossible to achieve with traditional methods. It also makes it possible to cater to patient-specific needs in the health sector.
Biocompatible Materials for Advanced Applications
Innovations in materials science are enabling the development of new polymers that are not only biocompatible but also offer enhanced properties such as improved strength, flexibility, and heat resistance. These materials are expanding the possibilities for medical device design, particularly in applications like implantable devices and minimally invasive surgical tools.
Sustainability and Eco-Friendly Practices
Scientists are also working hard to ensure the future environmental sustainability of the medical injection molding industry. Research efforts are focused on environmentally friendly materials that can be composted or recycled. Additionally, advancements in energy-efficient molding equipment and processes are helping to minimize waste and lower carbon footprints.
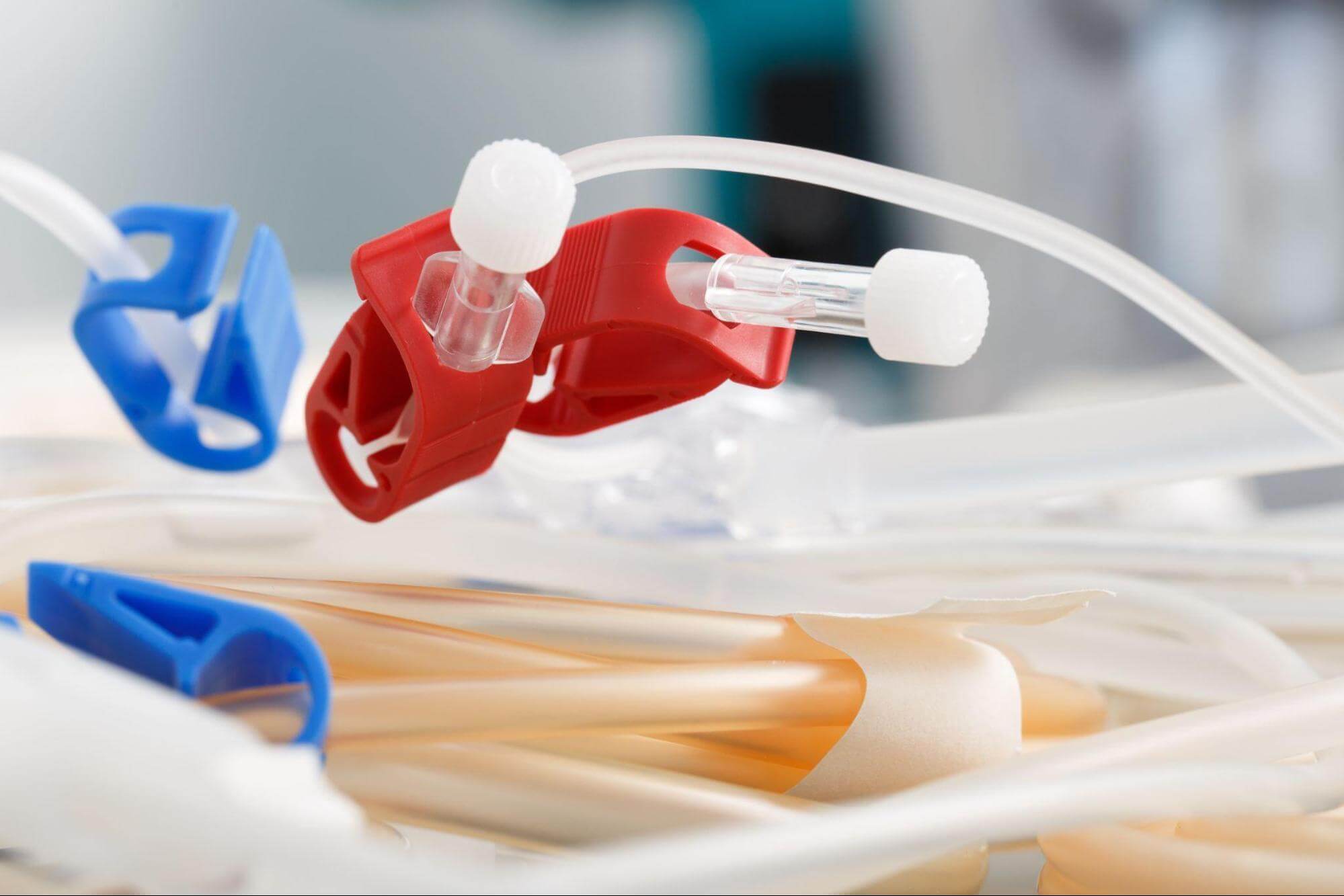
Fictiv As Your Partner Company for Medical Injection Molding
Injection molding is a precise, cost-efficient manufacturing method that produces high-quality parts capable of meeting the strict standards of the medical industry. While there are countless applications for injection molding in healthcare, not all materials are suited for every situation. Consider working with an injection molding expert to ensure that your design is paired with the right material and meets regulatory requirements.
At Fictiv, our expert engineers can help you refine your design and select the right material for your component. By uploading your designs, you can also access instant design for manufacturability (DFM) analysis to identify potential issues, reduce production slowdowns, and lower your cost-per-part.
Need precision-molded, FDA-compliant medical parts? Get a quote today and bring your design to life with Fictiv’s expert network of injection molders.