Time to read: 2 min
The Challenge: Manufacturing Process Tradeoffs for Medical Product Development
Plastic injection molding (IM) is ideal for high-volume manufacturing, but not all medical injection molders can provide tooling that is cost-effective for functional prototypes and low-volume production (LVP.) As a result, medical product designers may be forced to use another process during these stages of the product development cycle. That’s a lost opportunity for identifying and eliminating problems that could occur during high-volume production, sometimes with costly consequences.
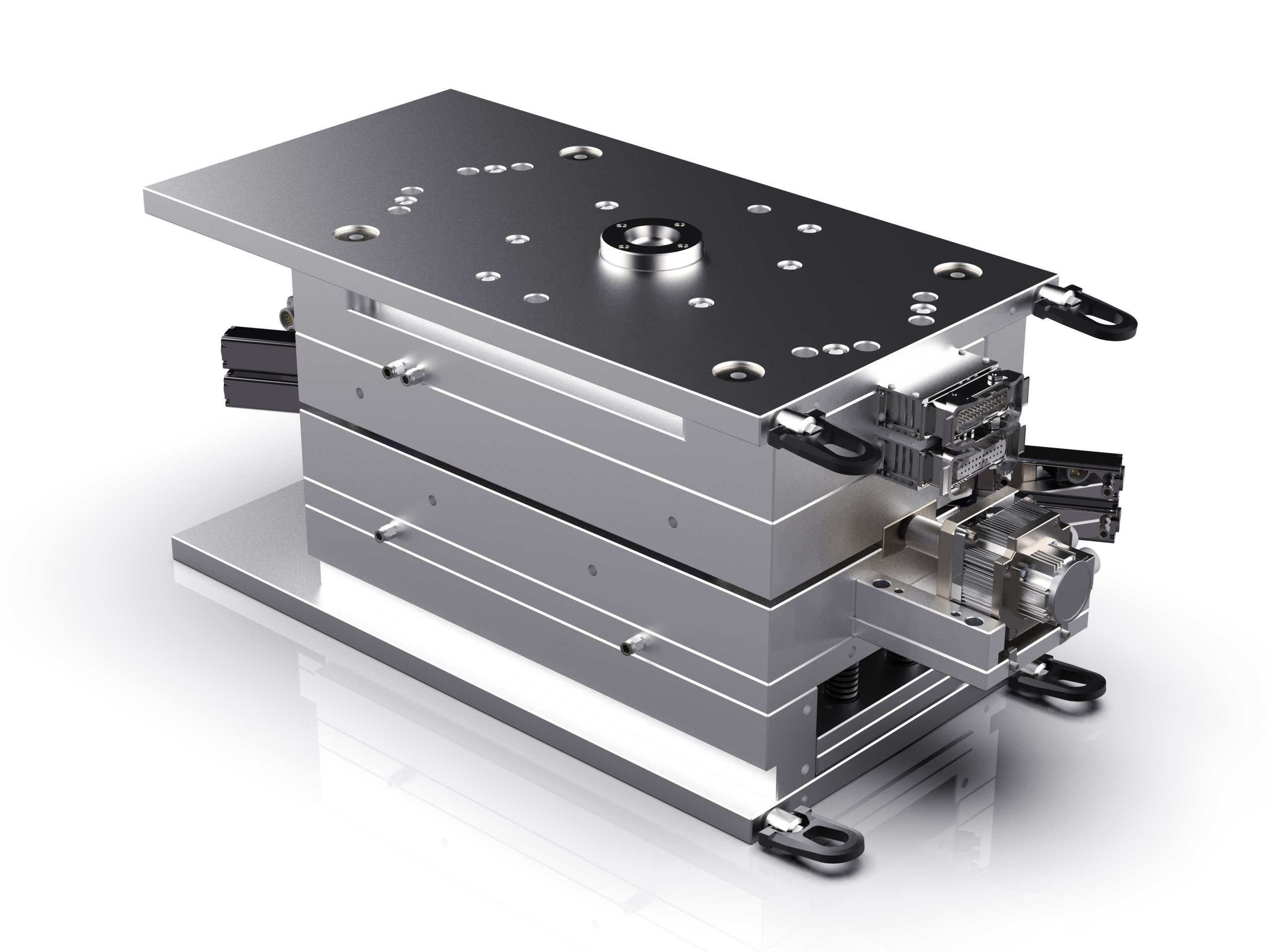
The Solution: IM for Medical Prototypes and Low-Volume Production
Fictiv provides cost-effective injection molds for prototyping and low-volume production. Molds that are made with aluminum or steel can be used with a master unit die (MUD) and frame that includes sprues and runners, leader pins, water lines, and ejector pins. Medical companies that pay only for the mold cavity and the core details save money, but that’s not the only way to control costs. With family molds, cavities for different iterations of the same part can support comparisons.
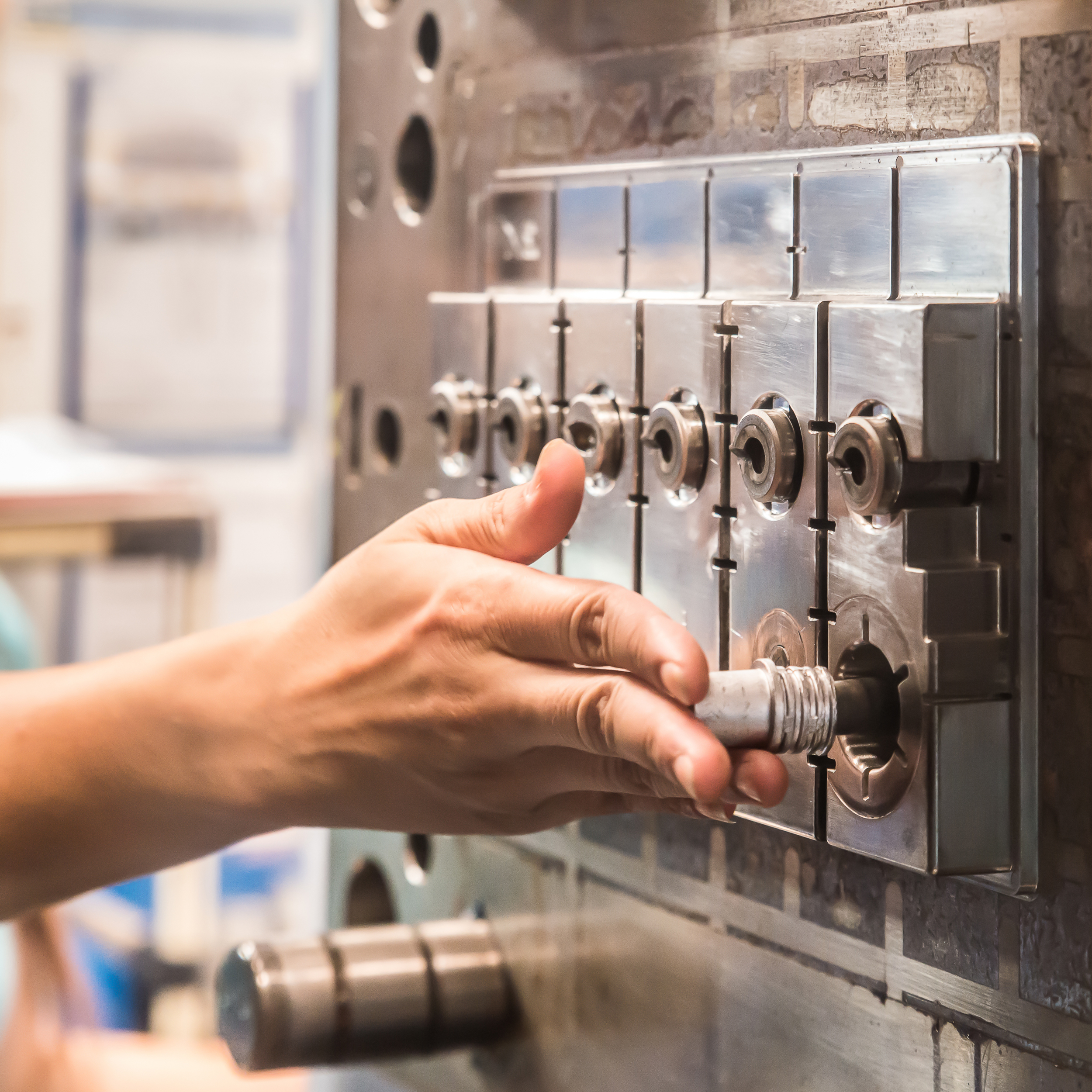
The Impact: Cost Control and Streamlined Medical Product Development
Partnering with Fictiv provides designers with access to medical injection molding that uses mold simulation and analysis software for higher quality parts, optimized cycle times, and fewer tooling trials. Simulating the fill and packing phase, optimizing gate locations and sizes, and improving specific process conditions before high-volume production begins also avoid common problems like warping and shrinking. In addition to tooling that costs less, designers can reduce waste downstream.
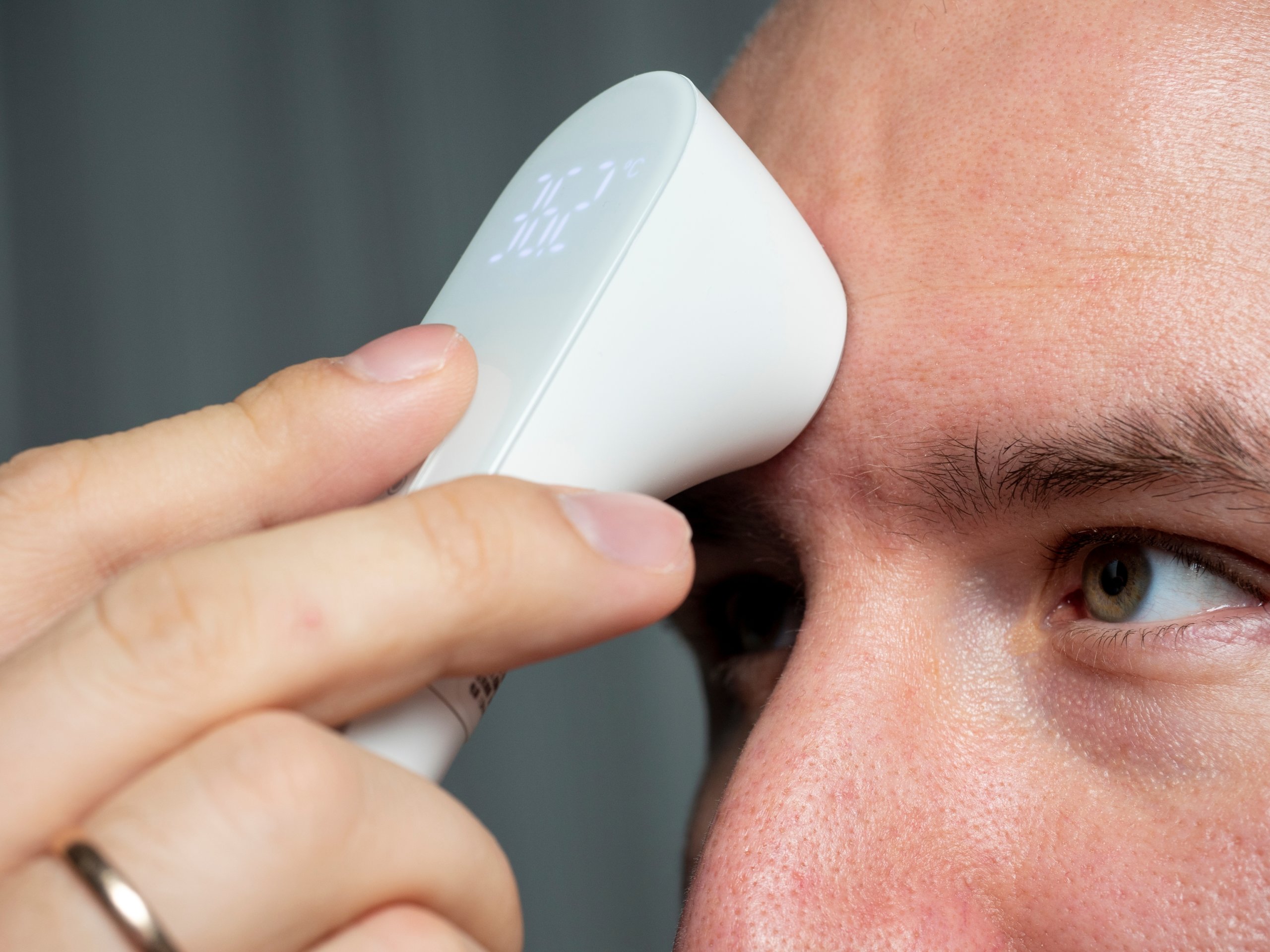
At Fictiv, we have the resources, know-how, and manufacturing network to deliver the plastic injection molding products that you need. Learn more about our injection molding services and create an account to get a quote today!