Time to read: 5 min
Polyphenylsulfone (PPSU) is an injection-molded plastic that resists high temperatures and harsh chemicals. Injection-molded PPSU parts are also tough, dimensionally stable, and impact-resistant. They can withstand steam autoclaving, hot water with detergents, and other demanding conditions. Filled and reinforced grades of this material are also available.
Because it’s a specialty plastic, PPSU costs more than commodity materials like polycarbonate, which often competes with PPSU. Applications for PPSU include medical devices, baby bottles, automotive parts, and electrical components. PPSU injection molding resins are available under various trade names, including Radel®, Ultrason®, TECASON®, and Sultron®.
If you’re considering polyphenylsulfone for your injection molding project, keep reading to learn more about this engineering plastic, including:
- Advantages
- Disadvantages
- Applications
- Properties
- Design guidelines
- Processing requirements
Fictiv works with a carefully vetted network of PPSU injection molders who can produce complex PPSU parts at amazing speeds. When you request a quote for our plastic injection molding services, you’ll also receive design for manufacturing (DFM) assistance from our engineering experts. Create your free Fictiv account to get started.
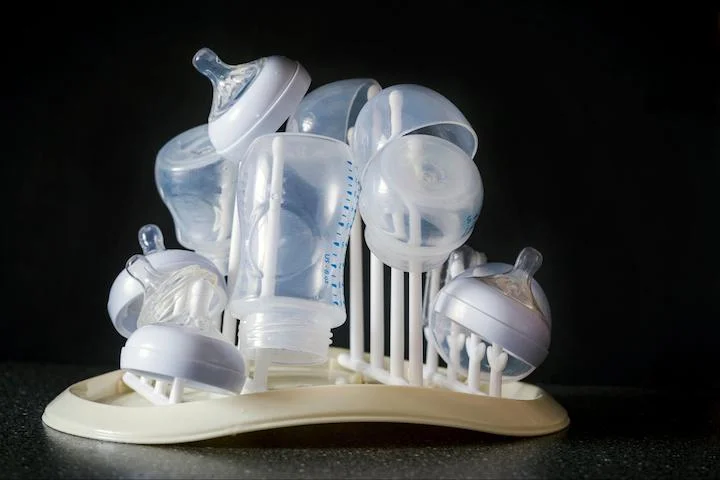
Advantages of PPSU
The advantages of injection molded PPSU include its high heat resistance, chemical resistance,
dimensional stability, impact strength, and biocompatibility. PPSU is also electrically insulating.
High Heat Resistance
PPSU maintains its performance properties and dimensional stability at continuous use temperatures up to 260ºC. That’s part of the reason this specialty plastic is a good choice for applications involving hot water and steam.
Chemical Resistance
Injection-molded PPSU resists a wide range of chemicals, including the aggressive disinfectants and cleaners used in healthcare environments. Most commodity plastics can’t match this performance.
Dimensional Stability
Injection-molded PPSU parts maintain their size and shape even when exposed to moisture or temperature variations.
Impact Strength
Because of its exceptional impact strength, PPSU is extremely durable. It’s also a good choice for applications where resistance to mechanical stress is critical.
Biocompatibility
PPSU’s biocompatibility supports its use in medical and healthcare applications. This engineering plastic can be sterilized repeatedly without significant degradation.
Electrical Insulation
Injection-molded PPSU is a good electrical insulator. This makes it a good choice for electronic connector housings.
Disadvantages of PPSU
PPSU isn’t the best choice for some types of injection molded parts. In addition to its high cost, it has a complex chemistry that can raise processing issues.
Cost
PPSU is more expensive than engineering thermoplastics such as ABS and nylon. Therefore, part designers need to balance PPSU’s cost vs. the application’s requirements.
Processability
Injection molding PPSU resins have a high melting point and require precise temperature control. Once melted, PPSU has a high viscosity (i.e., resistance to flow). Specialized additives can improve PPSU’s moldability.
Applications for Injection Molded PPSU
Injected molded PPSU is often used to produce these types of parts:
- Medical devices
- Dental parts
- Surgical instruments
- Appliance components
- Electrical connector housings
- Plumbing components for hot water service
Properties of Injection Molded PPSU
Before deciding to use injection molded PPSU, designers need to consider its physical, mechanical, and processing properties, which are listed in Table 1 below.
Value | ||
Physical | Density | 1.29 g/cm3 |
Water Absorption at Equilibrium 23 °C/50% r.h | 0.3–0.6% | |
Mechanical | Hardness | 122 Rockwell R |
Tensile Strength | 70–75 MPa | |
Young’s Modulus | 2.51 GPa | |
Elongation | 7% | |
Flexural Strength | 102 MPa | |
Flexural Modulus | 3.6 MPa | |
Impact Strength (IZOD) Notched | 3.83 J/cm | |
Thermal | Heat Deflection Temperature | 217 °C |
Vicat Softening Point | 216 °C | |
Thermal Expansion Coefficient | 55 µm/m°C | |
Melting Point | 218–220 °C | |
Electrical | Electrical Resistivity | 6.10E+15 ohm-cm |
Dielectric Constant | 3.46 | |
Dielectric Strength | 55 kV/mm | |
Chemical | Resistance to acids/bases | Good |
Resistance to organic solvents | Fair |
Design Guidelines for PPSU Injection Molding
PPSU parts that are poorly designed can exhibit injection molding defects. Fictiv’s injection molding experts can help you refine your designs so that you get great results, and you should download our free “Injection Molding Design Guide” to use as a reference for your next project.
Download the Injection Molding Design Guide
The following sections examine some PPSU-specific design considerations.
Wall Thickness
The recommended wall thickness for PPSU injection molded parts ranges from 0.76 to 2.92 mm. To avoid potential part defects, apply a uniform wall thickness. If thicker walls are required in some areas, make the transition gradual. Avoid excessively thick walls because they tend to cause internal voids and sink marks.
Rounded Corners and Fillets
Use rounded corners and fillets instead of sharp corners to reduce stress concentrations, minimize the risk of cracking, and facilitate material flow during injection molding.
Draft Angles
Apply a draft angle, or taper, to the walls of injected molded PPSU parts so that it’s easier to eject them from the mold. Generally, 1° to 2° of draft is sufficient for both the inside and outside walls. Textured finishes increase draft requirements by a minimum of 1 degree per side for every 0.001 inch of the texture depth.
Bosses
Although PPSU has excellent dimensional stability, some part designs include bosses for extra stability and to support the use of fasteners. Make the thickness of a boss less than 60% of the wall thickness. This will help to prevent sink marks from shrinking as the plastic cools.
Ribs
Ribs enhance structural integrity and increase load-bearing capacity. If your design uses these features, incorporate fillets at the bottom of the ribs and apply a radius of 0.25T-0.5T (where T is the nominal wall thickness). To help prevent sink marks, limit rib height to 2.5T.

PPSU Material Processing
PPSU injection molders need to follow specific processing guidelines for best results. Because adherence to these guidelines is beyond a part designer’s immediate control, it’s important to work with an experienced injection molder like the ones in Fictiv’s carefully vetted network.
Moisture
Prior to injection molding, dry PPSU at a maximum temperature of 165°C for approximately 4 hours. If necessary, PPSU resins can be dried for a longer period but at a lower temperature. Regardless of duration, use a desiccant bed dryer with a dew point maintained below -30 °C.
Temperature Control
PPSU requires very high temperatures because this amorphous plastic is difficult to melt. Typically, the temperature of the injection barrel is 360°C. To achieve a similar pressure in the mold, special heaters may be required.
Injection Speed
Use a moderate injection speed. For best results, this speed should be fast enough to achieve melt homogeneity but slow enough to avoid shear burning. For unfilled grades, PPSU fill times are typically 2 to 5 seconds. Faster injection rates support more uniform solidification and a good surface finish, especially with glass-reinforced PPSU grades.
Succeeding With PPSU Injection Molding
PPSU is an injection molding plastic with exceptional properties, but a manufacturing-ready design and a skilled production partner are critical. Fictiv has the engineering experts and global manufacturing network you need to get quality injection-molded PPSU parts. From prototyping through production, we’re here to help you succeed.
Create your free Fictiv account and request an injection molding quote today — we mold complex parts at high speeds!