Time to read: 9 min
The Production Part Approval Process (PPAP) is a critical quality control procedure used in the manufacturing sector, especially by automotive and aerospace companies, to ensure that a supplier’s parts meet specified requirements before mass production begins. By providing a structured approach to evaluating new or revised parts, it aims to reduce the risk of defects, enhance part reliability, and ensure consistency throughout the supply chain.
PPAP is an integral part of Advanced Product Quality Planning (APQP), a framework that focuses on ensuring product quality through proactive planning and validation. While APQP outlines the broader product development process, PPAP focuses on the final stage before production to ensure that parts are ready for series production.
This article will cover the production part approval process, different submission levels, and specific requirements that must be met at each stage.
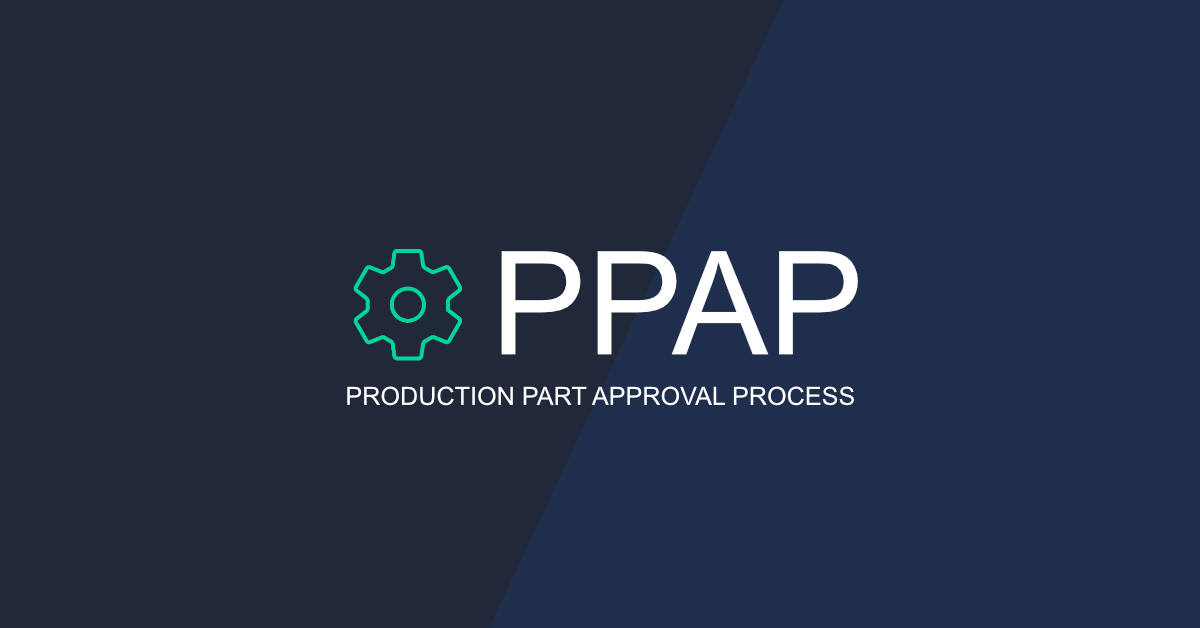
PPAP provides proof that you’re getting quality parts. Image Credit: ChainTraced
Important: Fictiv supports PPAP, but we also provide quality parts outside of this framework. If your project requires PPAP, select it as an additional service when you request a quote for Injection Molding, CNC Machining, or one of our other services.
PPAP Definition and Meaning
PPAP is a standardized process established by the Automotive Industry Action Group (AIAG) that manufacturers use to ensure that a supplier’s parts and subassemblies meet all engineering specifications and quality requirements. It is especially essential for industries where the parts are subjected to strict quality, safety, and performance standards, such as automotive, aerospace, medical, and consumer electronics.
Thorough documentation and process validation requirements, PPAP minimizes the risk of defects, rework, and production delays. The Part Submission Warrant (PSW) is a key document that summarizes the entire submission and formally confirms that the product meets all customer requirements before production.
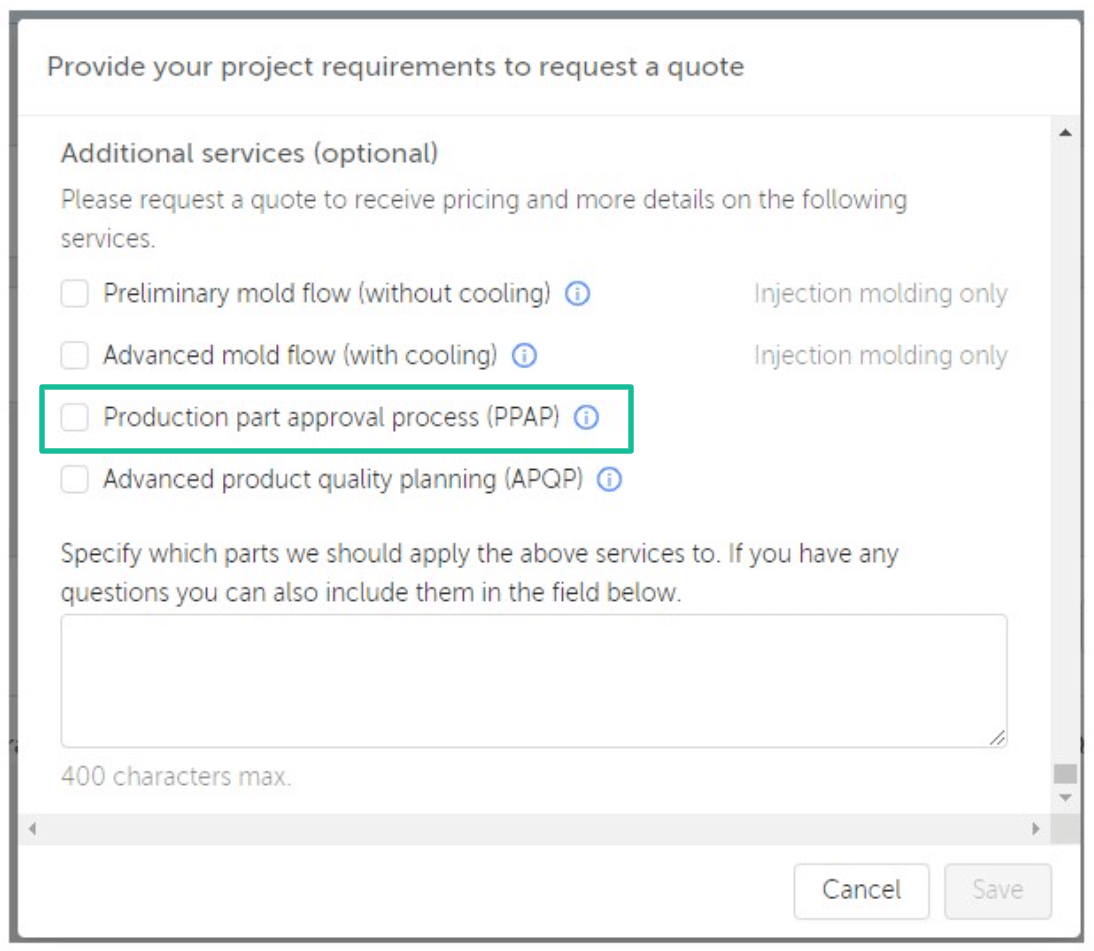
You can specify PPAP when you request a quote from Fictiv. An additional fee applies.
When is PPAP Required?
- New product or component introductions
- Changes in supplier or manufacturing location
- Changes to materials or processes
Benefits of PPAP in Manufacturing
The Production Part Approval Process brings several key benefits to manufacturers, suppliers, and OEMs:
- Consistent Quality: The process helps to ensure that the parts supplied meet consistent quality standards over time, minimizing the risk of defects or production issues.
- Reduced Risk: By validating parts before mass production, PPAP reduces the risk of failures or defects in the final product, which can be costly and damaging to the brand.
- Improved Supplier Relationships: It promotes collaboration between OEMs and suppliers, fostering trust and clear communication regarding expectations and requirements.
- Regulatory Compliance: Following the established process ensures that parts comply with safety standards and regulations, which is particularly important for industries like the automotive and aerospace sectors.
- Cost Savings: Applying the PPAP standards and suggested methods can help reduce costly rework, delays, and recalls by ensuring that all parts meet specifications before series production begins.
The PPAP Process: Step-by-Step Breakdown
The PPAP process is designed to systematically validate that a supplier is capable of producing a part that meets the specified design and quality requirements. The process consists of several key stages, each involving specific documentation and testing.
Here’s a breakdown of the typical steps involved:
Part Submission and Initial Review
The supplier submits the part for review, along with necessary documentation such as engineering drawings, material certifications, and process flow diagrams. The OEM then reviews the submission and confirms that the part matches the design dimensional requirements and design specifications. Next, if any discrepancies or issues are found, the supplier is required to make corrections before proceeding further.
Design and Process Validation
Design validation ensures that the part meets all functional, performance, and regulatory requirements as outlined in the design specifications. The prototype is used to design the process to ensure that the process meets all requirements.
The next step is process validation. This involves confirming that the manufacturing process can produce pilot parts that meet the design requirements consistently and reliably. This step may include pilot runs or “initial production runs” to evaluate process stability.
The next step is to conduct testing and inspection, such as capability studies (e.g., CpK analysis), to demonstrate that the process is capable of producing parts within acceptable tolerances.
Production Trial Runs
A trial production run is performed to simulate actual production conditions. During this stage, parts are produced in larger quantities to test the scalability of the manufacturing process. The goal is to validate the consistency of production output, identify any issues that could arise during full-scale production, and ensure the parts meet all quality standards.
Part Approval or Rejection
Based on the results of the design and process validations, the part is either approved for mass production or sent back to the supplier or project team for further improvement. If the part is approved, a Part Approval Certificate is issued, signifying that the part is ready for large-scale production.
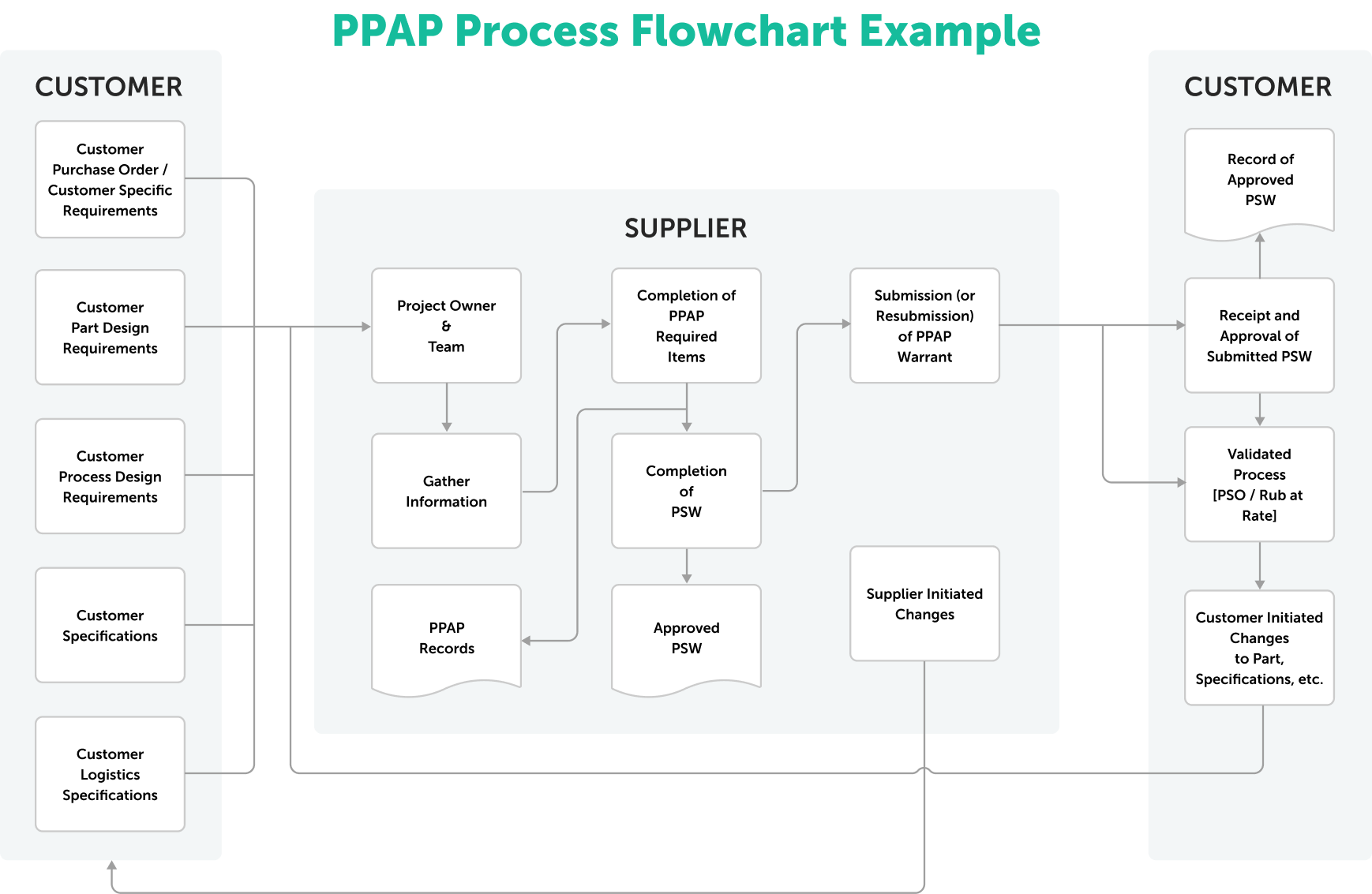
Following a process like this example is necessary, but creating a flowchart is not a PPAP requirement.
Understanding the 5 PPAP Submission Levels
There are five levels of PPAP submission. Each represents a different level of required part approval and validation documentation. The appropriate level is determined by the OEM based on factors such as the complexity of the part, the history of the supplier, and the risk level associated with the part.
All PPAP levels require a Part Submission Warrant (PSW), a formal declaration that the supplier has completed all PPAP requirements and that the production process is capable of consistently producing parts that meet all specifications.
PPAP Submission Levels and Their Requirements
PPAP Level | Documentation Requirements | When to Use It |
Level 1 | Part Submission Warrant (PSW) only | For minor changes |
Level 2 | PSW + limited supporting documents | Low-risk components |
Level 3 | Full PPAP package | Standard industry requirement |
Level 4 | Customer-defined requirements | Custom/critical parts |
Level 5 | Full documentation + on-site review | High-risk or safety-critical parts |
Here is a detailed explanation of the submission requirements for each level:
- PPAP Level 1: Part Submission Warrant (PSW) Only: At this level, the supplier submits a PSW, a document confirming that the part meets all specifications. No additional documentation or samples are required. Level 1 is typically used for low-risk, low-complexity parts for which there is a history of consistent quality performance by the supplier.
- PPAP Level 2: PSW With Limited Documentation: The supplier submits the PSW along with some supporting documentation, such as design records, material certifications, and process flow diagrams. This level is appropriate for parts that are moderately complex or when there are minor changes to an existing design.
- PPAP Level 3: PSW With Full Documentation: The supplier submits the PSW along with a comprehensive set of documentation, including engineering drawings, process flow charts, capability studies, and test results. A full set of sample parts submitted at PSW level must also be provided. Level 3 is the most commonly used level for new parts or significant design changes. It provides the OEM with a complete picture of the part’s design, manufacturing process, and quality control measures.
- PPAP Level 4: PSW With Special Requirements: This level requires the PSW and additional documentation specific to the part. Special requirements could include unique testing or process certifications. The OEM may request additional samples or more detailed documentation. Level 4 is typically used for parts that require special handling, such as high-risk components, critical safety parts, or parts that must meet unique regulatory requirements.
PPAP Level 5: PSW With Complete Submission: The highest level of submission, Level 5 includes the PSW and all documentation from Level 3, along with any special requests made by the OEM. This submission will include extensive data to demonstrate that the part meets all requirements under real-world conditions. Level 5 is used for parts that are critical to the final product’s safety or functionality, or where the risk of failure is high. It involves a full-scale audit of the supplier’s capabilities.
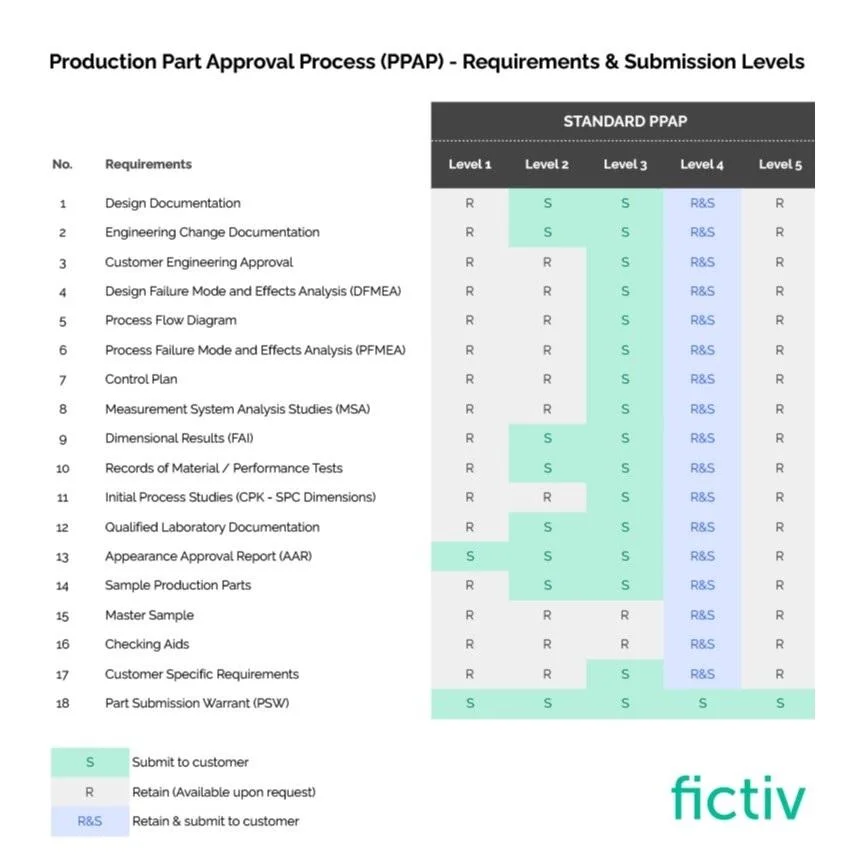
Chart of PPAP Requirements and Submission Levels
Why PPAP Is Critical for Quality Manufacturing
PPAP plays a critical role in ensuring that manufactured parts meet design specifications and can be produced reliably at scale. It does this by validating part quality before mass production ever begins—an early check that helps prevent defects and reduce variation.
This upfront diligence ensures consistent results across production runs. In highly regulated industries like automotive and aerospace, where even the smallest deviation can have serious consequences, that consistency is non-negotiable. PPAP also confirms whether a supplier can sustain that level of quality over time, helping to avoid disruptions caused by nonconforming or unreliable parts.
But PPAP isn’t just about quality; it’s about control. It compels suppliers to prove that their processes are stable, repeatable, and well-documented. The ripple effect is significant: fewer delays, fewer recalls, and far less wasted cost. For manufacturers, suppliers, and OEMs, PPAP is more than a quality checkpoint. It’s a strategic investment in reliability, trust, and long-term risk reduction.
As Lisa Wang, Deputy General Manager and Head of Quality for Fictiv in China, explains:
“Through PPAP, the supplier and customer agree upon the requirements needed to obtain approval of the supplier-manufactured parts. By providing a consistent approval process, PPAP also helps to reduce delays and non-conformances.”
Common Challenges and Best Practices in PPAP Implementation
Implementing PPAP can present several challenges. However, understanding these hurdles and applying best practices can improve the process.
Here are some of the common issues encountered and best practices for how they can be resolved:
- Incomplete Documentation: Standardize submission templates to ensure that all required documentation is provided upfront, avoiding delays and incomplete submissions.
- Long Approval Times: Improve communication between suppliers and manufacturers to ensure that any issues are quickly identified and resolved, helping to reduce approval times. Make sure a cadence or schedule is put in place to implement approval processes.
- Inconsistent Measurement Results: Regular calibration of measurement tools and ongoing staff training can help ensure accurate and reliable measurements. Implement a stand operating procedure (SOP) for inspection, testing, and measurement.
- High Resource Dependency: Implementing PPAP can require significant upfront investments in quality control, testing, and documentation. Managing the documentation and data that’s involved can be time-intensive and may require dedicated personnel.
- Complexity: PPAP can involve a large number of documents and steps, which adds complexity to the internal processes of suppliers and their customers.
- Rigidity: PPAP has a formalized structure that may seem overly rigid to companies that are not part of the automotive or aerospace industries.
Key Documentation Requirements for PPAP
The PPAP process requires several key documents and records to demonstrate that the parts meet the necessary quality standards. Below are the critical requirements:
- Part Submission Warrant (PSW): The PSW is a document signed by the supplier that confirms that the part has been manufactured according to specifications and is ready for approval.
- Design Records: These include engineering drawings, CAD files, and design specifications that outline the part’s dimensions, materials, tolerances, and performance requirements.
- Engineering Change Documents: If applicable, these include any engineering change orders (ECOs) that affect the part’s design or specifications.
- Design FMEA (Failure Modes and Effects Analysis): DFMEA is a proactive analysis tool that identifies potential failure modes in the part and their effects on the final product. Performing this analysis before production starts helps lower product risk early in the design phase.
- Process Flow Diagram: This is a detailed flowchart showing the complete manufacturing process, from raw material procurement to final inspection. This diagram identifies key production steps, quality control checks, and critical processes.
- Process Control Plan: A process control plan document outlines the control measures that will be used during production to ensure part quality, such as in-process inspections, testing, and tooling requirements.
- Measurement System Analysis (MSA): This includes studies to verify that measurement tools and systems are accurate and reliable for testing parts during production.
- Capability Studies (CpK or Cp): These studies assess the capability of the manufacturing process to produce parts within the specified tolerances. A CpK value of greater than 1.33 is commonly required to ensure a process meets acceptable performance levels. This corresponds to a defect rate of less than 64 parts per million (PPM).
- Production Samples: A batch of parts produced under normal production conditions for evaluation and approval. These samples are tested for functionality, appearance, and compliance with specifications.
- Material Certifications: Documentation verifying that the materials used in production meet the required standards and specifications.
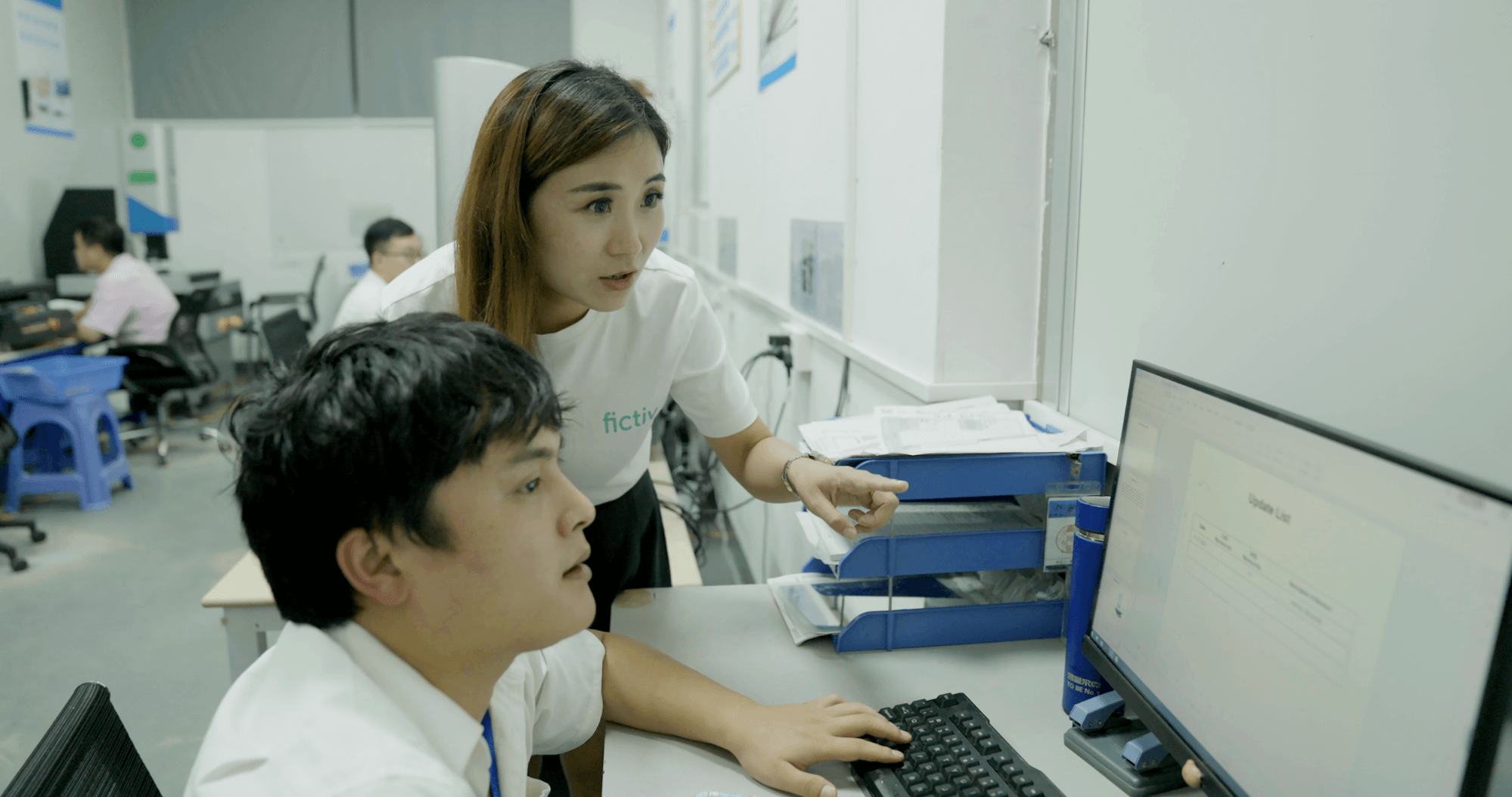
Cross-functional teams and clear communications strengthen PPAP.
Ensure Part Quality and Supplier Consistency with Full PPAP Compliance in Manufacturing
PPAP is a foundational quality control process that ensures that parts meet customer requirements and are consistently manufactured to high standards. It plays a critical role in reducing defects and improving part reliability and supplier consistency. For both OEMs and suppliers, PPAP is key to building a resilient, high-performing supply chain.
Adhering to PPAP ensures that parts meet stringent industry standards before full-scale production. But its value goes beyond compliance. PPAP fosters collaboration, transparency, and a culture of continuous improvement between manufacturers and suppliers. Whether for simple or complex, safety-critical parts, it provides a structured, data-driven framework to validate designs, materials, and processes.
Focus on building—leave PPAP to us. With Fictiv, you can get high-quality parts backed by complete PPAP documentation, plus rapid prototyping and AI-powered DFM. We handle compliance and quality control, so you can move forward with confidence. Get started today—if you need PPAP, you can request it in your quote.