Time to read: 7 min
The next time you stop to admire the quality of your sleek blue bicycle or bright red grill, you may have powder coating to thank. It’s commonly used to enhance the appearance and longevity of products all around us.

This article will discuss powder coating, the steps involved in the process, its benefits and drawbacks, and how it differs from other coatings.
What Is Powder Coating and How Does It Work?
Powder coating is a highly effective surface treatment and finishing method used across various industries for its durability and performance. Unlike traditional liquid paints that rely on wet application, powder coating involves dry powders that are electrostatically charged and cured with heat. This process creates a tough, high-quality finish that resists corrosion, chipping, and fading, making it a superior alternative to conventional coatings.
Compared to other options, powder coating is often the best choice due to its excellent finish, durability, and environmentally friendly nature. It is also more efficient and reduces waste while avoiding the use of hazardous solvents. Powder coating is an excellent option for CNC-machined, sheet metal, or die-cast parts.
Powder coating is a cost-effective method that can be applied to various materials beyond metal, including plastic, making it highly beneficial for industries such as automotive, aerospace, construction, and consumer goods. Additionally, with a wide range of available colors, powder coating allows customized finishes to meet aesthetic requirements.
If you need powder coating for your parts, sign up or log in to the Fictiv platform to get started!
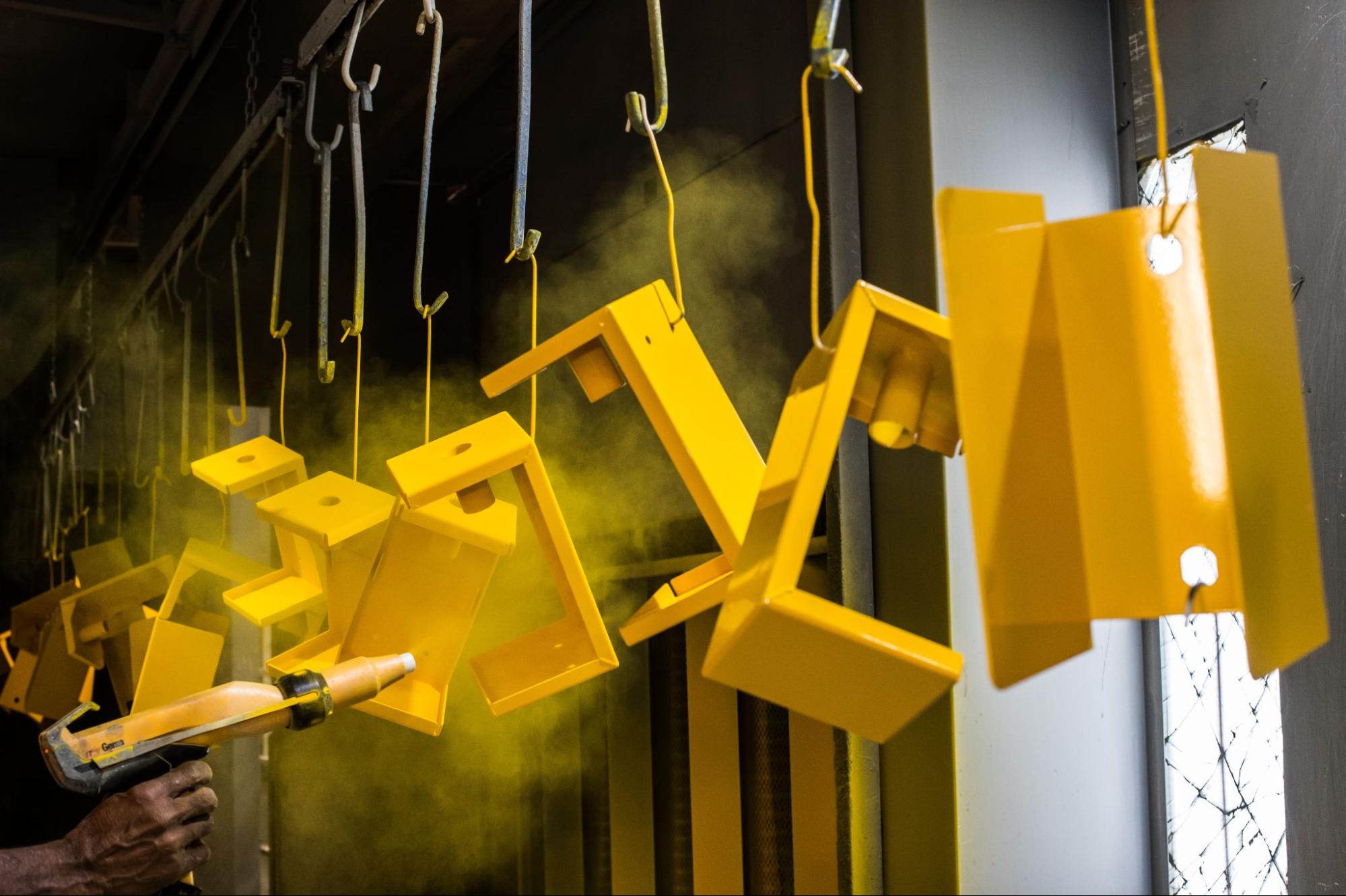
The Powder Coating Process
Surface Preparation
Proper surface preparation is crucial for a successful powder coating application. Before applying powder coating, the substrate must be thoroughly cleaned to remove dirt, grease, and other contaminants. This step, which typically involves washing and degreasing to eliminate oils or residues, is essential to ensure proper powder adhesion..
Then, the substrate may also undergo surface finishing to create a rough profile, ensuring better powder coating adhesion. This can include shot blasting, grit blasting, or sandblasting, which increases the surface area and enhances the mechanical bond between the coating and the substrate, resulting in a stronger, more durable finish. However, this surface preparation is not always necessary, as the chemical cleaning process and a preliminary bake are usually enough to remove debris.
Application Process
The two primary methods for applying a powder coat are Electrostatic Spray Deposition (ESD) and Fluidized Bed Coating.
In ESD, the most common method, electrically charged powder particles are sprayed onto grounded metal surfaces. This process ensures even coverage and strong adhesion. However, certain factors must be carefully controlled, including voltage settings, film thickness, and the shape of the part being coated. Automated voltage adjustments help maintain a consistent surface finish, while spray techniques may need to be modified for complex geometries to ensure proper coverage.
For batch processes, the Fluidized Bed Coating method is used. In this process, preheated parts are immersed in a fluidized bed of powder. Upon contact with the hot surface, the powder melts, forming a thick and uniform coating. This method is particularly effective for applications requiring high-impact resistance, as it produces coatings of 10+ mils, providing enhanced durability.
Curing Process
The curing process transforms the applied powder coating into a hard, durable finish. This is commonly done through thermal curing, during which coated parts are heated in ovens. Standard curing temperatures range from 325–450 °F (163–232 °C), with curing times varying between 10–30 minutes, depending on the material and coating thickness. As the powder melts, it forms a smooth, protective film that bonds permanently to the substrate.
Alternatively, UV-cured powder coatings require lower temperatures, making them suitable for substrate materials that cannot withstand high heat. In this process, the powder is applied and then exposed to ultraviolet light, triggering a rapid chemical curing reaction. While not suitable for all applications, UV curing significantly reduces processing time while still providing durable protection similar to thermal curing.
Advantages of Powder Coating
Among the many advantages of powder coating, durability stands out as the primary benefit. Powder-coated surfaces are highly resistant to scratches, chips, corrosion, and chemicals. Additionally, they meet strict performance standards, such as pencil hardness (ASTM D3363) and salt spray resistance (ASTM B117), ensuring long-lasting protection.
Beyond durability, powder coating offers exceptional versatility in color, texture, and gloss. Custom finishes can be achieved to suit various design needs, including matte, satin, gloss, metallic, and textured coatings.
From an environmental perspective, powder coating is a sustainable choice. It contains no solvents, produces minimal hazardous waste, and features a high transfer efficiency of nearly 98%, thanks to reclaimable overspray. This not only reduces material waste but also improves cost efficiency, as less product is needed compared to liquid paint. Additionally, its durability lowers long-term maintenance costs.
Powder coating is not just for aesthetic purposes; it is widely used in industrial applications as well. It can be customized to match Pantone and Reichs-Ausschuss für Lieferbedingungen (RAL) color standards, including metallic, textured, and transparent finishes.
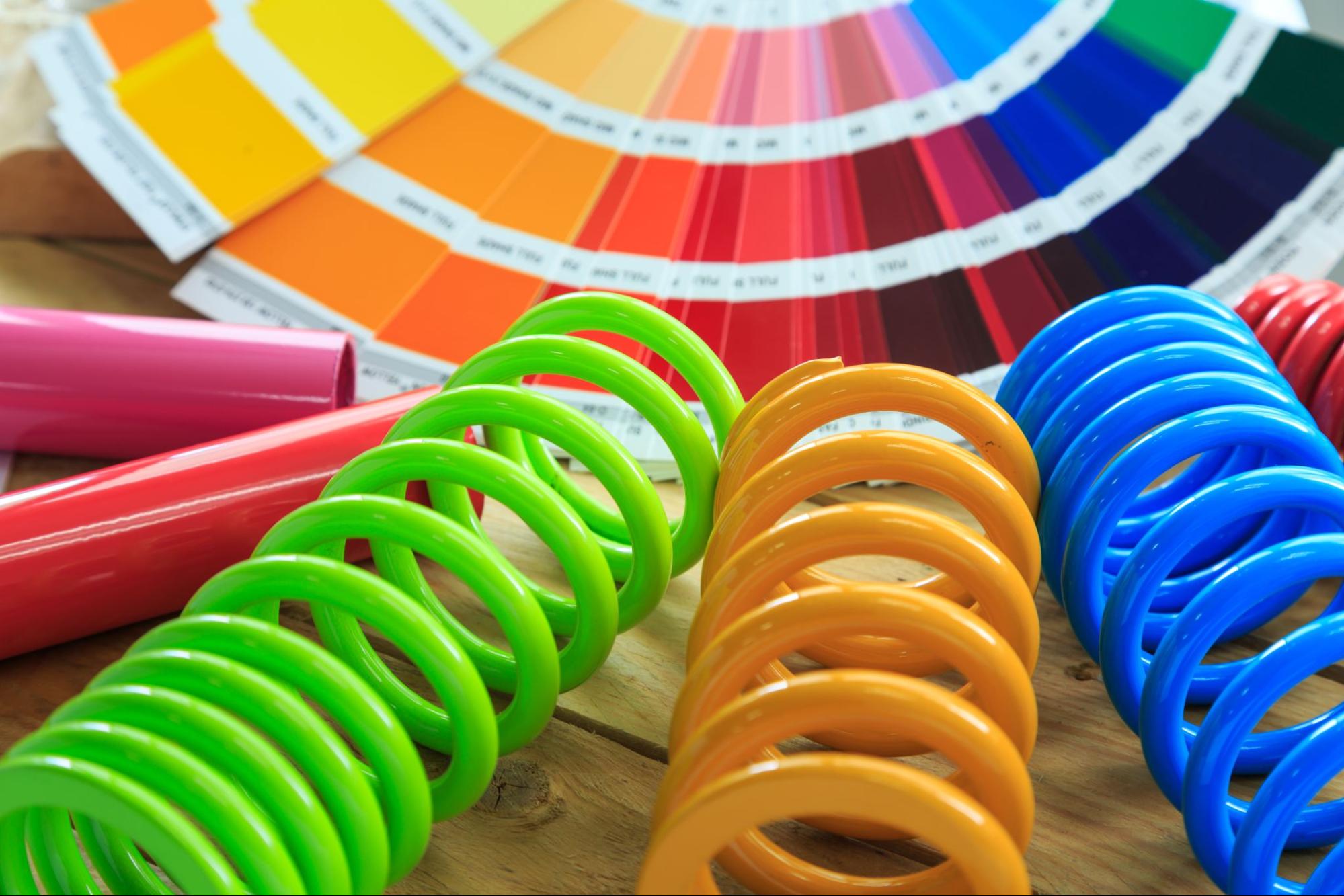
Limitations and Challenges of Powder Coating
While powder coating offers many benefits, it also has some drawbacks. One challenge is controlling the coating thickness, which should ideally be between 2–6 mils (.002–.006 in). Applying too much coating can create an orange peel effect, which is a rough, dimpled texture resembling the skin of an orange. This can also occur from high humidity, extreme temperatures, or faulty equipment.
Material selection is another limitation. Some polymers and composites cannot withstand the high curing temperatures required for powder coating, making alternative coating methods necessary. Additionally, certain metals require pretreatment to improve adhesion and coating performance.
Another concern is chipping in high-impact areas. Unless the coating formulation is specifically designed for high-impact resistance, severe impacts can cause the finish to chip. However, this issue can be addressed by selecting the correct powder coating formulation for the intended application.
To overcome these challenges, careful consideration of the substrate material, application method, and end use is essential. Despite these limitations, powder coating remains a highly versatile and beneficial finishing solution for a wide range of industries.
Industry Applications of Powder Coating
Highlighting its versatility and other beneficial properties, powder coating is a necessity in a number of industries:
- Medical Technology: Antimicrobial powder coatings are used on medical devices and hospital apparatus to alleviate the spread of infective microorganisms
- Climatic Technology: Provides corrosion protection to enhance both durability and efficiency for heavy-duty equipment like solar panels, wind turbines, and energy storage systems
- Automotive: Extensively used with rims, engine parts, chassis, and almost all other parts of cars exposed to high temperatures and chemicals
- Aerospace: Used to coat the frames and interiors of aircraft, which require an extreme strength-to-weight ratio to withstand severe conditions, ensuring a durable finish
- Industrial Machinery: Used with armor-grade protective measures like gear and cases that can corrode over time
- Consumer Goods: Aesthetic and long-lasting finishes for bicycles, fitness tools, and electronic appliances
- Architectural and Construction: Erosion protection and added designs for railings and window frames
- Retail Displays and Advertising: Signs, display stands, and store fixtures that are eye-catching and able to withstand the elements with unparalleled strength and aesthetics
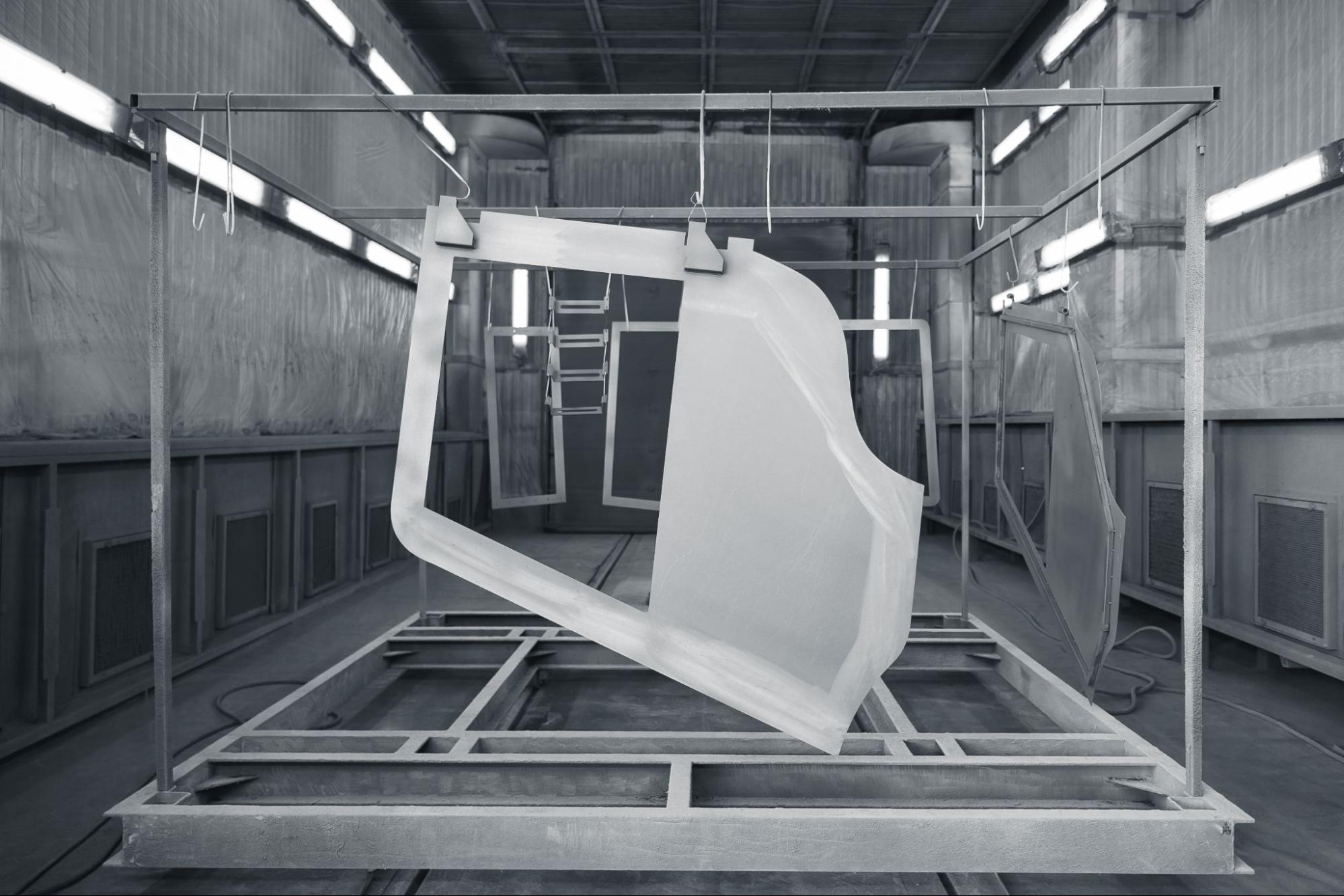
Comparing Powder Coating to Other Common Finishing Options
The choice of coating depends on the desired outcome and material. Below are some common alternative options to powder coating, though this list is not exhaustive:
- Anodizing: Ideal for aluminum surfaces that require protection from scratches and color fading, but is limited in its range of color and finish options
- Chemical conversion coatings: Primarily for corrosion resistance on aluminum and magnesium but lack color versatility and aesthetic appeal
- Liquid Paint: Achieves various cosmetic requirements on designed plastics and other surfaces but requires longer drying times than powder coating and can release volatile chemicals into the air
Finishing Process | Advantages | Disadvantages |
Powder Coating | – Durable and resistant to corrosion, chemicals, and UV radiation – Environmentally friendly (low VOCs) – Provides a thick, uniform coating | – Requires high curing temperatures – Difficult to repair or touch up – Adds thickness to the part |
Anodizing | – Excellent corrosion resistance Increases surface hardness – Provides electrical insulation – Can be dyed for aesthetic purposes | – Limited to aluminum and a few other metals – Cannot cover welds or defects well – Brittle and prone to chipping under impact |
Chemical Conversion Coatings | – Thin coating improves corrosion resistance and paint adhesion – Low-cost and easy application – Can be conductive (depending on type) | – Lack of color versatility – Limited standalone protection (often used as a base for paint) – Provides less wear resistance – May contain hazardous chemicals |
Liquid Paint | – Wide range of colors and finishes – Can be applied to various substrates – Easy to repair and touch up | – Requires solvents for application with longer drying times – Less durable than powder coating and anodizing – Higher VOC emissions (environmental concerns) |
Comparing Powder Coating to Other Common Finishes
Enhance Your Product Quality With Fictiv’s Powder Coating Solutions
Powder coating is not only cost-effective and visually appealing but also environmentally friendly. Many industries prefer it as a finish option because it provides a durable finish that meets both mechanical and cosmetic requirements. By using powder coating, companies can significantly improve their operational efficiency.
Get in touch with us today for a quote and see how we can help you with powder coating for your prototype or production parts. You can also use Fictiv’s online quote tool for quick estimates—simply add a finish while quoting and select a color option from the dropdown list.
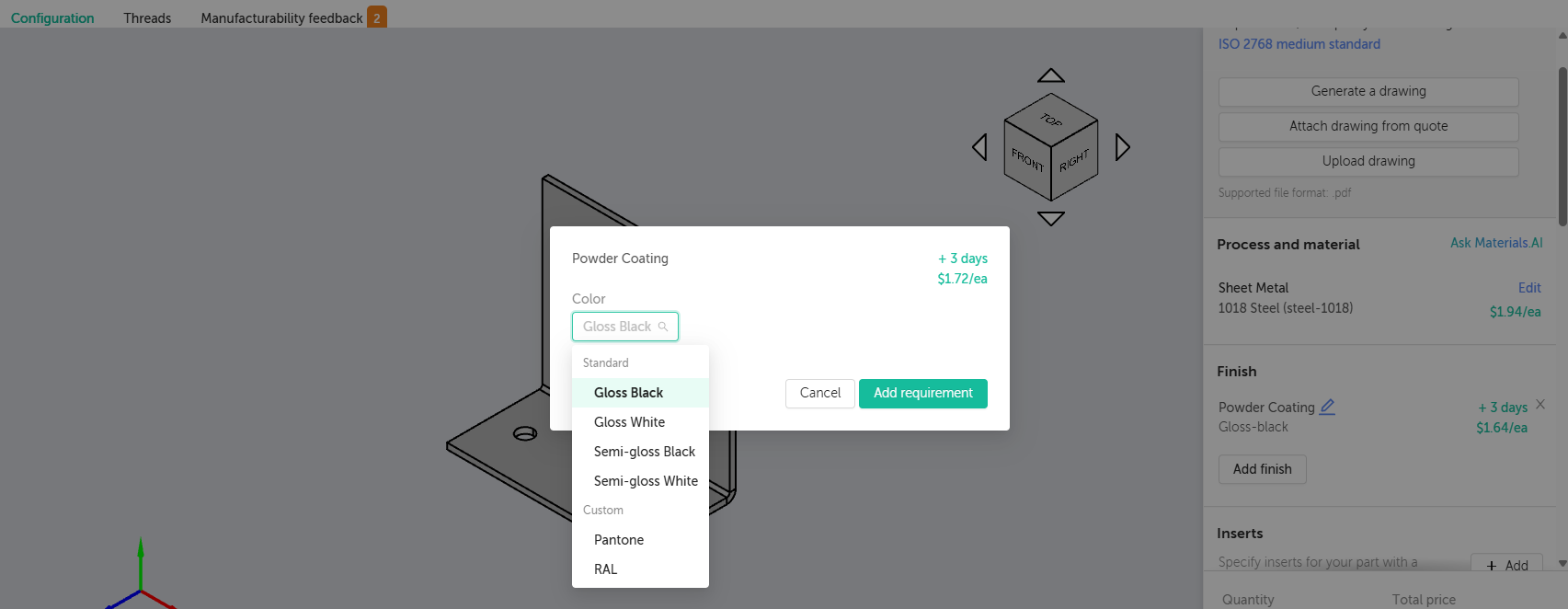