Time to read: 7 min
Polyamide and nylon are frequently utilized interchangeably, as they belong to the same class of engineered polymers. These materials are increasingly utilized due to their excellent mechanical properties, toughness, and adaptability. Nylon is a type of polyamide polymer (polyamides encompass a large group of materials), so they cannot be utilized interchangeably.
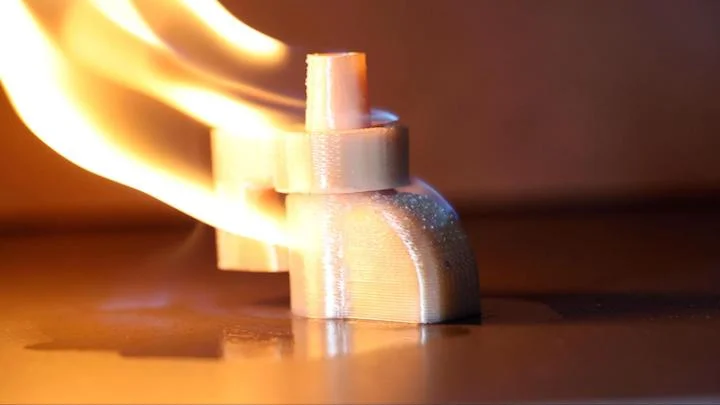
This comparison guide will delve into the nuanced contrasts between polyamide and nylon. We will examine their compound structures, dig into their properties, and compare their common uses. Keep reading to learn how these materials are utilized in different industries.
Polyamide vs. Nylon Composition and Structure
All plastics are carbonaceous polymers, giving them a similar composition and structure. However, plastics are diverse in composition, structure, and properties. Here are some of the differences between polyamides and nylon:
Polyamide
Polyamide encompasses manufactured polymers, and is defined by the presence of amide (NH-CO) linkages in their sub-atomic design. These linkages present remarkable properties, including high elasticity, versatility, and protection from impact resistance. In simpler terms, polyamides are polymers with repeating units fused with amide links. An amide group is one with a chemical formula CONH2. These repeating units are called monomers and vary based on the type of polyamide, and they may be amides themselves. For example, the monomer for the Kevlar polyamide is benzene.
Well-known polyamides in this category include nylon, Kevlar, and Nomex, which are known for their outstanding strength and dimensional stability.
Nylon
DuPont coined the term nylon during the 1930s. Nylon is a specific type of polyamide with carbon and hydrogen monomers that form chains with the amide groups through a process known as “condensation polymerization” (hence the name polyamide). This is a process by which water is lost between two of the monomers. Its formation includes a buildup polymerization response between a dicarboxylic corrosive and a diamine. The reasonable selection of monomers and exact handling conditions yield different types of nylon.
Common Properties of Polyamides and Nylon
1. Tensile Strength and Durability
Both polyamides and nylon possess striking rigidity, making them appropriate for applications requiring materials to withstand high stress or impacts. This property has contributed to their far-reaching use.
2. Protection from Wear and Impact Resistance
One of the most striking qualities of polyamide and nylon is their astounding protection from wear and impact resistance. This element makes them ideal material choices for applications that include steady friction and contact with harsh surfaces, like pinion wheels, orientation, and transport lines.
3. Chemical Resistance
Polyamides, by and large, display excellent protection from different synthetic compounds, oils, and solvents, albeit the degree of this obstruction shifts depending upon the particular kind and exposure duration. This property has propelled their use in assorted modern settings where openness to cruel synthetic compounds is desirable.
4. Water Resistance
While nylon and polyamides possess good water resistance, nylon demonstrates higher water ingestion, in contrast with different polyamides. This can be beneficial in specific applications, though it might present difficulties in others. For instance, nylon fishing lines are designed to absorb water and perform better when they do absorb water; they lose their buoyancy so they can sink.
5. Melting Point
Different types of polyamides and nylons generally have varying melting points depending on their specific chemical compositions. That being said, some types of nylon may have a lower melting point than certain polyamides due to differences in the length of their molecular chain. For example, nylon-6 has a lower melting point than nylon-6.6 due to its shorter molecular chain length. However, other types of polyamide may have lower melting points than some types of nylon. Ultimately, a given polymer’s melting point is determined by various factors, including its molecular weight, crystallinity, and chemical structure.
Polyamide and Nylon for 3D Printing – Common Uses
Polyamide and nylon are excellent 3D printing materials because of their dimensional stability, durability, high impact strength, excellent impact resistance, and versatility. Among the top polyamide and nylon materials for 3D printing are PA12, Nylon 12, PA12 Glass Beads, Nylon 6, Nylon 11, Nylon 11 Flame Retardant, and Nylon 12 Glass-Filled. Here are some common uses of the most common 3D printing nylon and polyamide materials.
3D Printing Polyamide 12 (PA 12)/Nylon 12 for 3D Printing
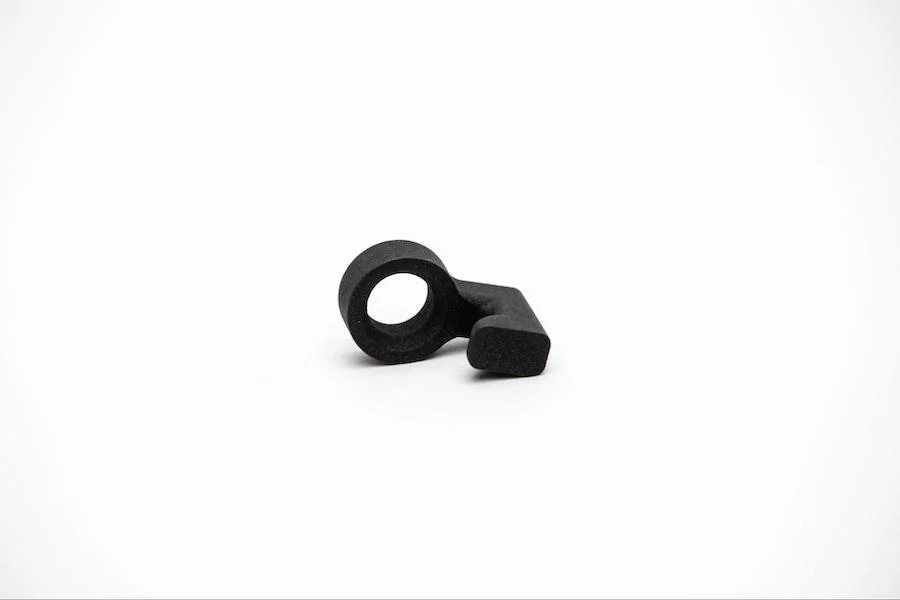
Polyamide 12 (PA 12) is a Multi Jet Fusion (MJF) 3D printing material with excellent durability and strength. It also has excellent chemical resistance, with the ability to withstand chemical, oil, and solvent exposure without significant material degradation. The 12 in PA 12 is present because of the 12 carbon atoms in the monomer, which happens to be laurlactam (a cyclic amide).
MJF PA 12 is an excellent material to use for functional prototypes, professional 3D printed parts, end-use parts, complex assemblies, and even the most complex geometries. Its chemical resistance makes it an excellent choice for industries such as oil and gas, automotive, medical devices, food packaging, and chemical processing.
PA 12 is often called Nylon 12, especially for Selective Laser Sintering (SLS) and Fused Deposition Modeling (FDM) 3D printing. Nylon 12 SLS 3D printed parts are constructed from a laser-heated and fused nylon powder layer by layer, allowing for complex geometry and intricate feature formation. Nylon 12 SLS 3D printed parts are strong, chemically resistant, durable, and flexible, making them excellent choices for aerospace, medical, and automotive industry parts.
Nylon 12 FDM is a filament-based 3D printing technology that utilizes a heated extruder to melt and deposit nylon filament layer by layer to create a part. Nylon 12 FDM is easy to use, affordable, and compatible with a wide range of 3D printers. Nylon 12 FDM is ideal for creating functional parts that require good strength and flexibility at a reasonable cost. Its strength and flexibility make it ideal for functional parts, such as gears, hinges, and snap-fit components. Nylon 12 FDM is commonly used in the automotive, consumer goods, and electronics industries. Some examples of Nylon 12 FDM parts are brackets, housings, bicycle frames, phone cases, electrical connectors, and gears.
3D Printing Polyamide 12 With Glass Beads (PA 12 GB)
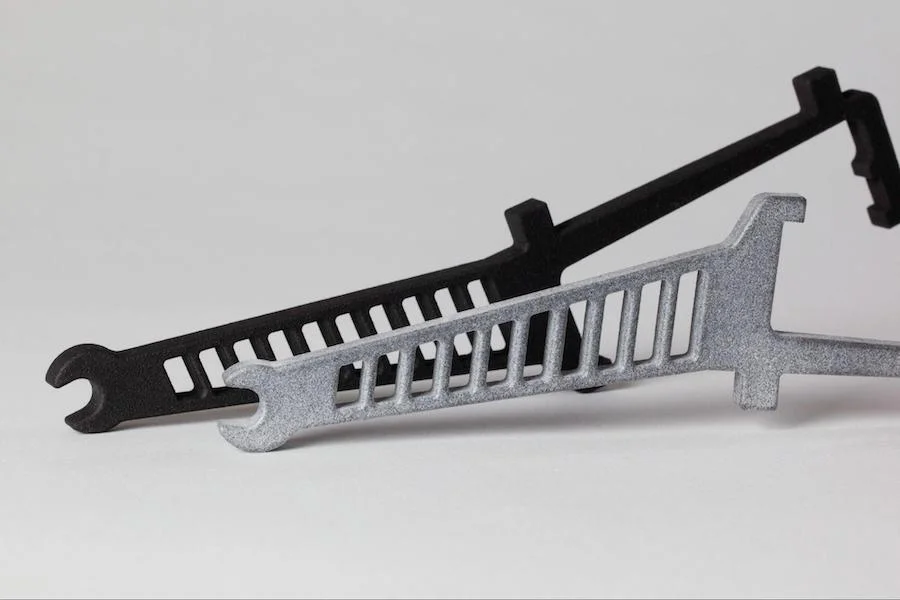
Glass beads reinforce the PA 12 material, enhancing the dimensional stability, rigidity, and stiffness of 3D printed parts. PA 12 with glass beads (PA 12 GB) material is strong and smooth, offering the strength coupled with the smooth touch you need for products that people interact with.
PA 12 GB is a material utilized with the Multi Jet Fusion (MJF) 3D printing process. Industries that favor PA 12 GB 3D printed parts are electronics, aerospace, tooling/fixturing, oil and gas, and marine. Some common MJF 3D printed PA 12 GB parts are jigs, fixtures, tooling, injection molds, conveyor system parts, brackets, connectors, and automotive housings.
3D Printing Nylon 6
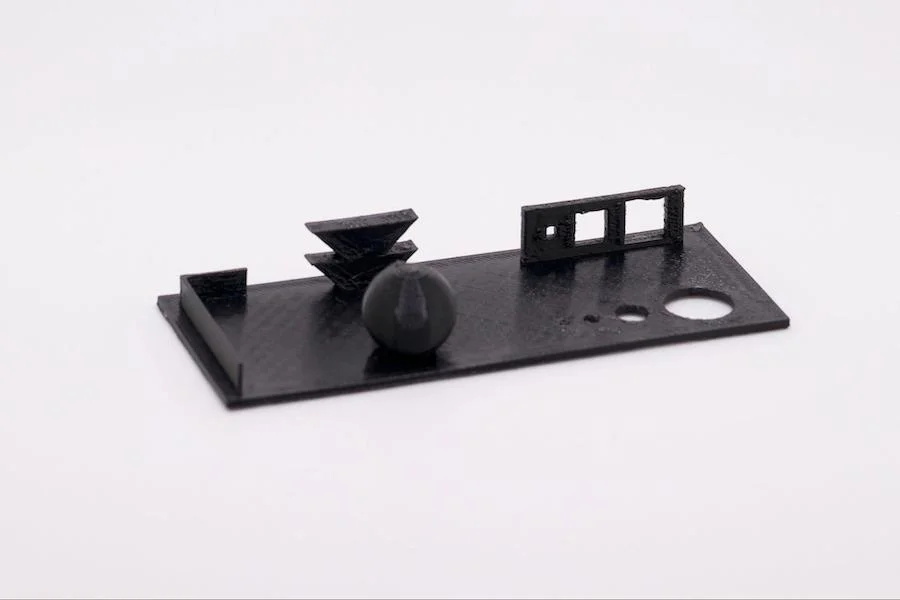
Nylon 6, FDM 3D printing material, is so named because of the 6 carbon atoms that comprise the monomer ε-caprolactam, a cyclic amide. Nylon 6 is strong, durable, and has good heat and chemical resistance. Nylon 6 is a versatile and popular material for 3D printing because of its high strength, durability, and resistance to wear and impact. It is also known for its excellent temperature resistance and ability to retain its shape even when exposed to high temperatures.
There are many applications for Nylon 6. It is commonly used for functional prototypes, mechanical parts, and end-use products. Its ability to be easily machined, drilled, and tapped makes it a popular material for parts that require post-processing. Additionally, Nylon 6 is often used to produce gears, bearings, and other parts that require high strength and durability.
3D Printing Nylon 11 and Nylon 11 Flame Retardant
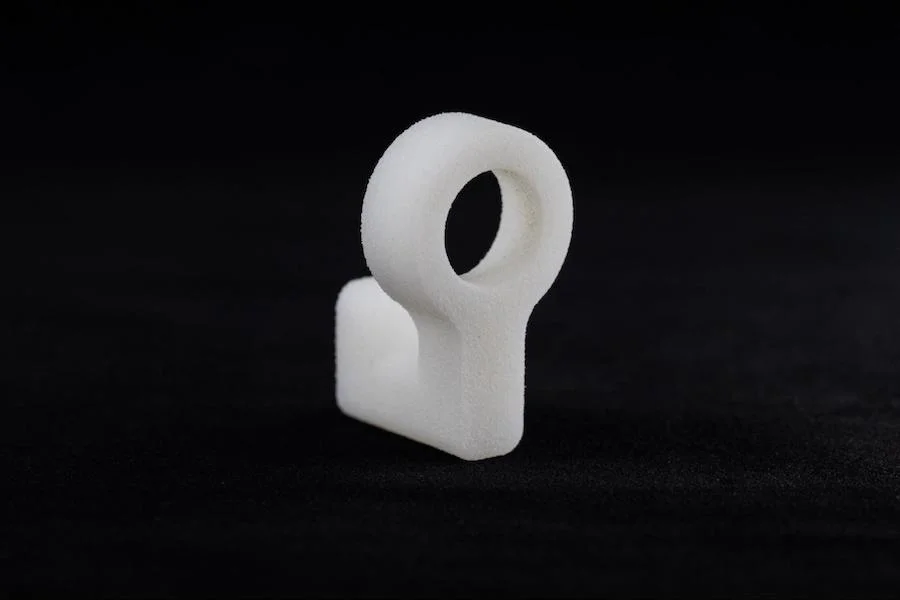
Nylon 11 is a Multi Jet Fusion 3D printing bio-based material with good ductility and impact resistance. It also boasts excellent dimensional accuracy coupled with low density and eco-friendly properties. Nylon 11 is widely used in the automotive, aerospace, electronics, and consumer goods industries. Its ability to withstand harsh environments and extreme temperatures makes it a popular choice for parts that need to perform well under challenging conditions. Common parts made from 3D-printed Nylon 11 include snap-fit components, clips, clamps, fears, prosthetics, fuel lines, connectors, and housings.
Nylon 11 Flame Retardant is a Selective Laser Sintering (SLS) 3D printing material that has added fillers such as molybdenum trioxide, alumina trihydrate, or antimony trioxide to further enhance the natural fire resistance of Nylon 11 and improve its smoke suppression properties. The required fire resistance determines the amount and type of filler used. It is also a heat-resistant material. Nylon 11 Flame Retardant is often utilized in electronics, automotive, aerospace, industrial equipment, and medical industries. Some common parts printed with Nylon 11 Flame Retardant material include engine covers, electrical connectors, switches, pump components, and medical diagnostic components.
3D Printing Nylon 12 Glass-Filled
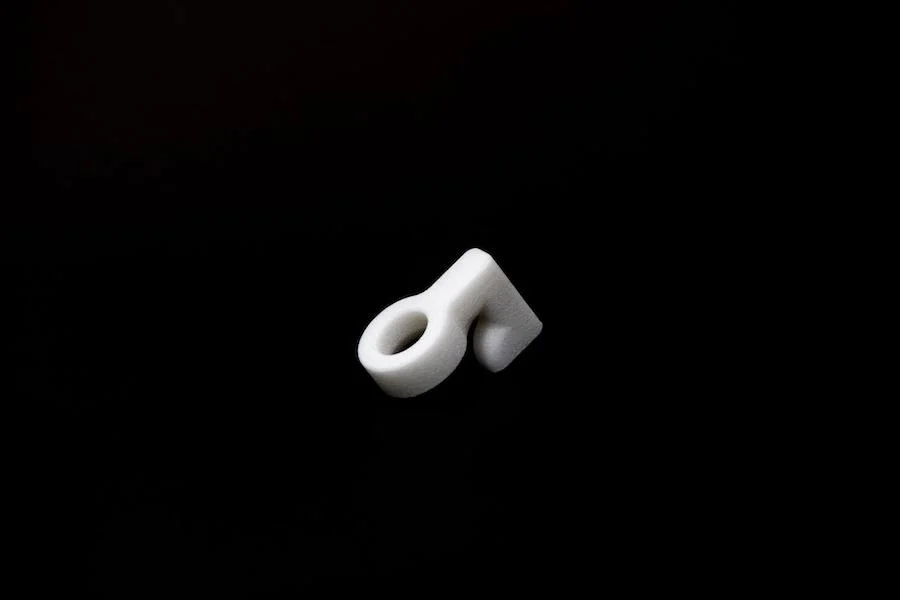
Nylon 12 Glass-Filled is an SLS 3D printing material with high strength, stiffness, and durability. Nylon 12 glass-filled is known for its excellent mechanical properties, making it a popular choice for various applications. Nylon 12 Glass-Filled has a unique structure made by combining Nylon 12 resin with glass fibers, resulting in a composite material that is both lightweight and strong.
The glass fibers embedded in the Nylon 12 matrix create a structure similar to reinforced concrete, giving it exceptional strength and stiffness. Like reinforced concrete, the fibers act as reinforcement, helping distribute mechanical stress throughout the material and preventing it from cracking or breaking under pressure.
In addition to its excellent mechanical properties, Nylon 12 Glass-Filled is highly resistant to heat, chemicals, and wear. This makes it an ideal material for use in various industrial applications, including automotive, aerospace, and consumer goods. Nyon 12 Glass-Filled is excellent for durable prototypes or functional end-use parts, such as Housings, enclosures, consumer sporting goods, gears, and medical equipment.
Conclusion
In conclusion, the differences between polyamide and nylon relate to specific characteristics within the broader category of manufactured polymers. The common amide linkages they share give them exceptional mechanical properties, making them suitable for a wide range of industries. Understanding the subtle variations between these materials allows designers and engineers to make informed decisions about material selection.
Whether used in materials, auto parts, designing plastics, or athletic gear, the remarkable properties of polyamide and nylon continue to drive progress and innovation in various fields. With the advancement of technology, we can anticipate even more sophisticated specifications and applications for these versatile materials, further expanding their reach and impact on modern industry. The enduring legacy of polyamide and nylon is a testament to human ingenuity and our ability to harness the power of science to shape the world around us.
Consider Fictiv for all your nylon and polyamide 3D printing needs. Check out our 3D printing capabilities page to learn more about the specific polyamides we offer or upload a design for an instant quote today.