Time to read: 6 min
For this week’s Hardware Spotlight, we’re chatting with Alex Neskin, the CTO at Petcube, an innovative product that connects owners with their pets using remote wireless camera streaming, 2-way audio, and a built-in laser pointer.
Often the greatest lessons are born out of challenges encountered and Alex Neskin, CTO at Petcube, relates to this sentiment all too well.
One Saturday morning last May in Hong Kong, Alex woke to a distressed voice on the other end of the phone. When the words finally came out they began with, ‘I feel broken hearted… so very sorry..” It was a representative of the Chinese factory he had been working with who called to regretfully inform him a subcontractor of theirs had been been shut down, the workers arrested, and all their tooling molds confiscated.
This call came just days before the tooling was to be finished. So after months and months of difficult preparation and tens of thousands of dollars spent, there was nothing else to do but start over.
In this exclusive interview Alex shares the lessons he learned as a result of this unfortunate experience which helped him navigate the complicated process of working with manufacturing vendors in China.
Choose Wisely
The key to choosing a factory in China all comes down to trust. Alex suggests there are three factors to consider when deciding which factories can be trusted.
1. Reputation
A key factor in choosing a trusted manufacturer in China is to look at reputation. The problem, however, is that the factories with the best reputation as known and trusted partners are generally more difficult to win the attention of as a smaller startup with small production quantity. The key here, Alex says, is two-fold and similar to the principles of successful job-hunting:
- Get an introduction. You might trust the factory, but they don’t trust you yet. You need to either scrape your own network to find an introduction or seek out the help of a partner program like HAXLR8R which can facilitate introductions on your behalf. Alex found his introduction to a large factory, Yitoa, through a colleague at a large Ukrainian company called PocketBook.
- Sell yourself. After an introduction there is still work to be done. You have to convince the factory that to work on a new product with small production quantity, which requires more research and time, is a positive investment. “I spoke with the manager and told him we were going to heavily promote our product at CES,” Alex shares. “Moreover, I stressed we would have larger quantities in the future and that for them, to work on a completely new product would show they had the capability to make new and innovative products.”
Manufacturing in China is a challenge for your body and for your mind
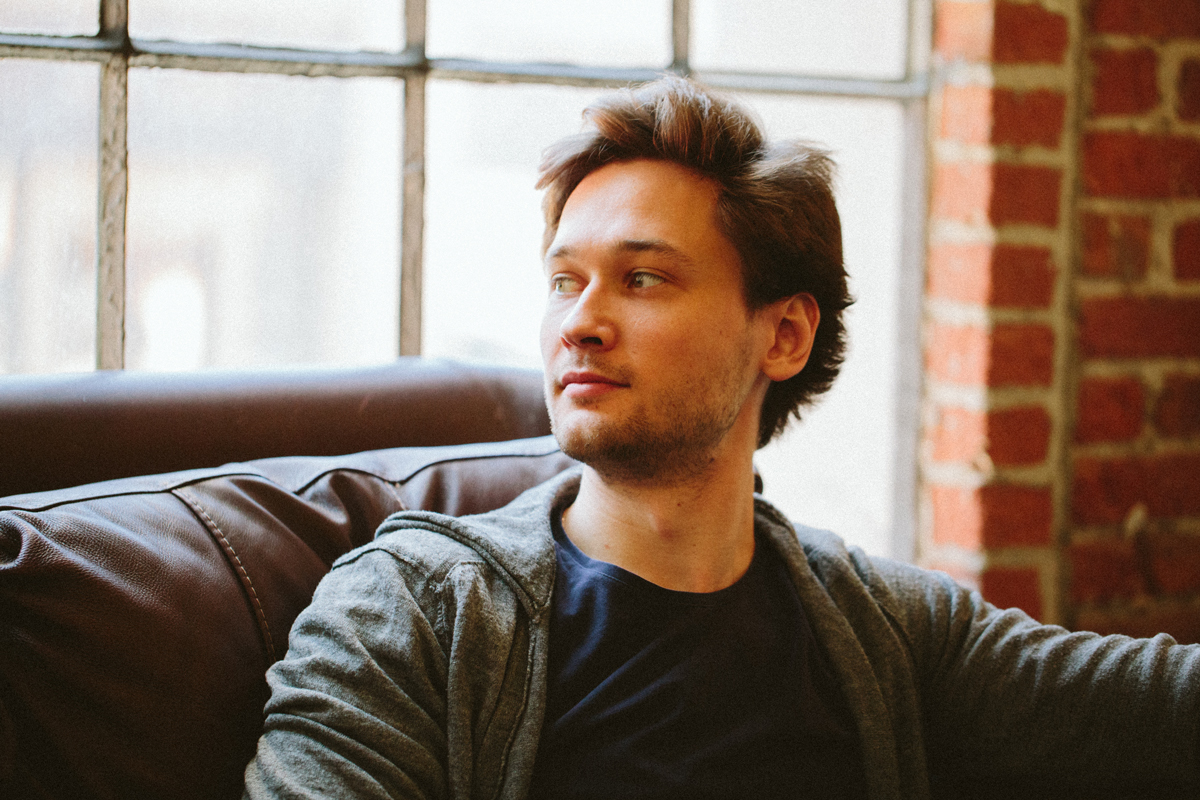
2. Mood
Another factor to consider when choosing a factory is the mood of the workers. “The best advice I received during my time in HAXLR8R’s program was to assess the mood of a given factory by checking out the restroom used by the factory workers,” Alex says. “When you’re visiting, ask the manager if you can use the worker’s restroom and then look for anything written on the walls. If it’s clear and clean then the mood is most likely positive. But If there’s writing on the walls then pay attention, take a picture, and ask someone to translate it afterwards. Writing on the walls can be a good indicator of discontent in the factory, which is a bad sign.”
3. Turnover
Alex also suggests to be wary of high turnover rates. One of the factories Alex worked with before Yitoa had a large number of younger people working in the factor and, thus, a very high turnover rate. So he would show up one day to explain the assembly process to a group of workers and then four days later there would be new workers making the same errors which would have to be corrected once again. Alex recommends looking for a factory just outside of the city center where the worker population is not quite as young.
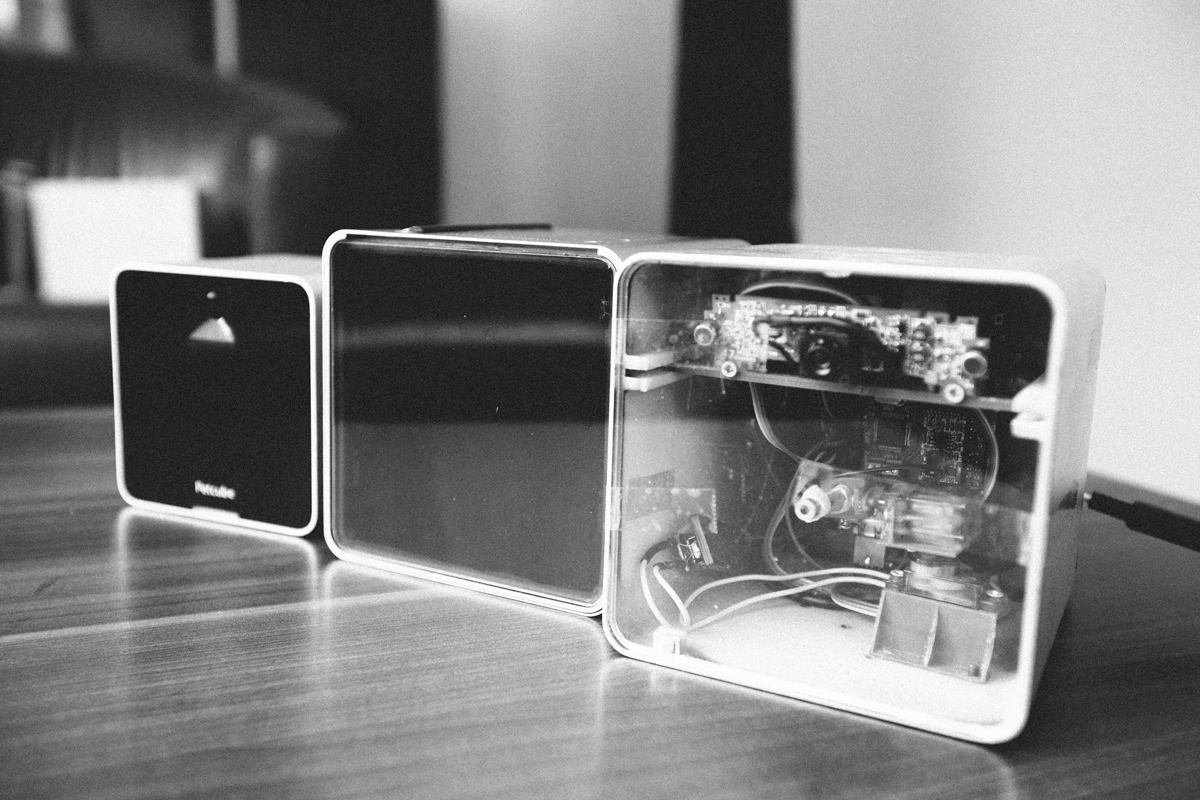
Be Present
Once you’ve chosen a factory Alex says it’s critical to be present on the assembly line floor to control the process. “No one knows your product as well as you do,” Alex stresses, “so the only way to make sure the process is going smoothly is to be there on the assembly floor to make sure no errors are being made. Control everything.”
An example of such an error Alex found was with the product casing. One day Alex went to his factory to check out the aluminum casing just shipped in by another vendor and when he took it in his hands and swiped his fingers along the edges his finger was sliced.
“I asked why it was like this,” Alex recalls, “because we had designed the casing with a 0.5 mm edge so it would be safe and the vendor said he thought it was for pets so he disregarded the specific edge dimensions.”
This is just one example of a series of problems which arose from miscommunication during the production process. The best way to assess and control all stages of production is to be there at the factory communicating in person with your manufacturing partners.
If you can see beyond any miscommunication or misfortune that crosses your path along the way, you can see opportunity on the other side
Test Everything
Before it was time to ship the product to the team’s Kickstarter backers, Alex had a strange dream. In the dream hundreds of Petcubes in palates on a ship at sea were caught in a violent storm, causing them to shake and ultimately be destroyed.
“I woke up from this dream and immediately thought, ‘I need to do a shaking test,’” Alex recalls. That same day he went to the factory and asked if a shaking test had been done. It had not. So he set one up and, low and behold, one of the mechanical parts was unstable.
From this point on Alex knew he would have to take the initiative to effectively test and analyze each of the products’ components.
Another test conducted was an aging test for which he placed the device in a fridge at a very low temperature, below -20 degrees Celsius, and also in a hot box with a temperature above 40 degrees Celsius. The device passed the cold test, but in the hot box the camera overheated and failed.
The only way to solve problems with your assembly line is to study the vulnerabilities and correct them gradually
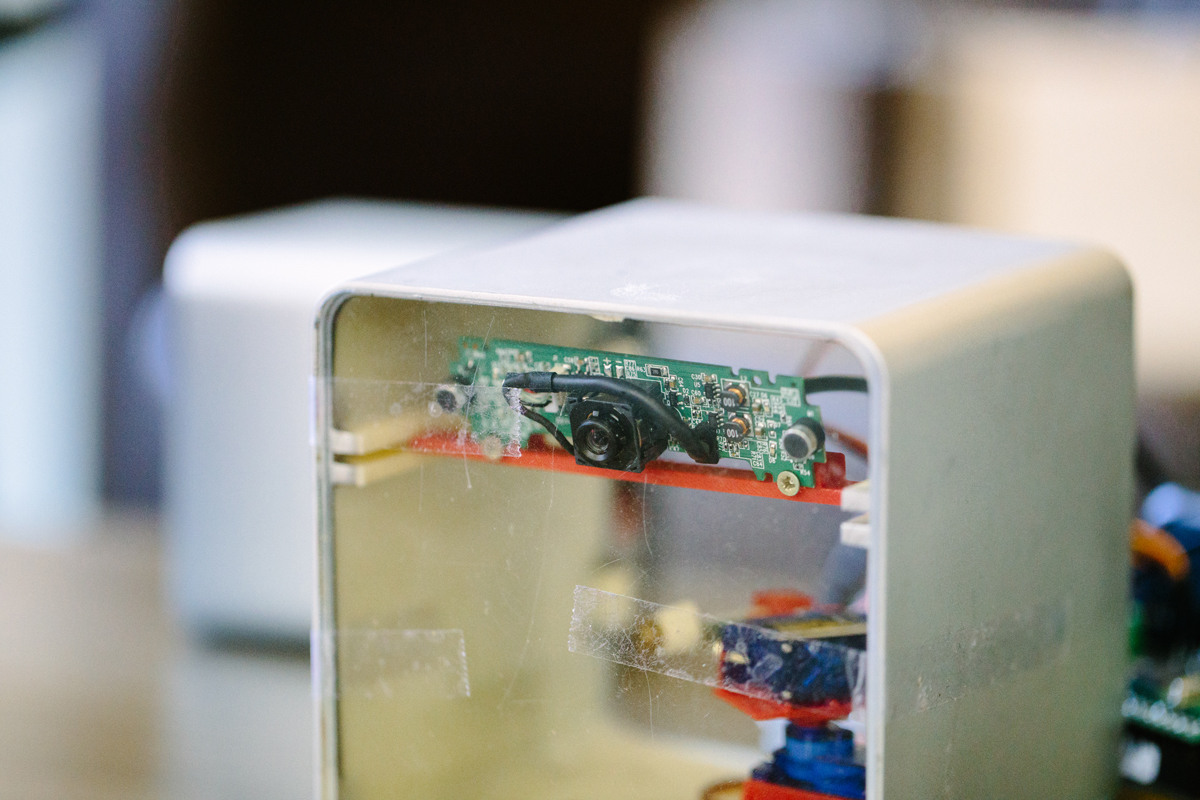
With each problem that arose Alex halted the assembly line until a proper solution was found. “I think I stopped assembly maybe 5 or 6 times during this phase of production so we could solve problems and start again,” Alex says.
It’s important to note that Alex had to take the initiative to undergo each of these tests – the factory manager did not initiate them on his behalf. “When you are working with a larger factory and producing small quantities you have to be in charge of everything,” Alex adds.
Alex also had to work with the factory manager to test and measure the efficiency of the factory assembly line. “We divided the assembly line into three stages and at each stage measured the speed, efficiency, and number of errors,” Alex shares. “We then rearranged people accordingly to improve the efficiency of the assembly line.”
Alex has a very thoughtful and reflective nature and speaks with metaphors to describe how he visualizes the perfect assembly line. “The only way to solve problems with your assembly line is to study the vulnerabilities and correct them gradually,” Alex offers. “Just like the water moves through the creek, you need to make the flow clean, stable and smooth.”
Be Resilient
Production may not always go according to plan. Scratch that – it will not always go according to plan. But the main takeaway for Alex is that resilience is the quality you must hold tight to in order to look past the many frustrations and complications one will inevitably encounter to get to final production.
“A certain level of positivity had to be present for me throughout this process,” Alex reflects. “Manufacturing in China is a challenge for your body and for your mind but if you can see beyond any miscommunication or misfortune that crosses your path along the way, you can see opportunity on the other side.”