Time to read: 7 min
Polybutylene terephthalate (PBT) has many electrical, medical, and food processing applications and comes in filled, unfilled, flame retardant, reinforced, and lubricated grades. Brands include Celanex®, a family of branded PBT materials that provides high strength and rigidity in thin-walled parts. PBT injection molding is used to produce plastic parts with good dielectric strength and resistance to creep, heat, and ultraviolet (UV) light.
Because of its exceptional properties, injection molded PBT is a specialty plastic rather than a commodity material. PBT’s rapid crystallization during injection molding speeds cycle times, but PBT can crystallize before the mold is filled, resulting in part defects. During cooling, PBT parts may deform because of internal stresses.
If you’re considering PBT for your injection moded parts, read on to learn all about this injection molding material, including:
- advantages
- disadvantages
- applications
- properties
- design guidelines
- processing requirements
- potential alternatives
Fictiv works with a carefully-vetted network of PBT injection molders who can minimize the risk of part defects during prototyping and production. When you request a quote for our plastic injection molding services, you’ll also receive design for manufacturing (DFM) assistance from our engineering experts. Create a free Fictiv account to get started.
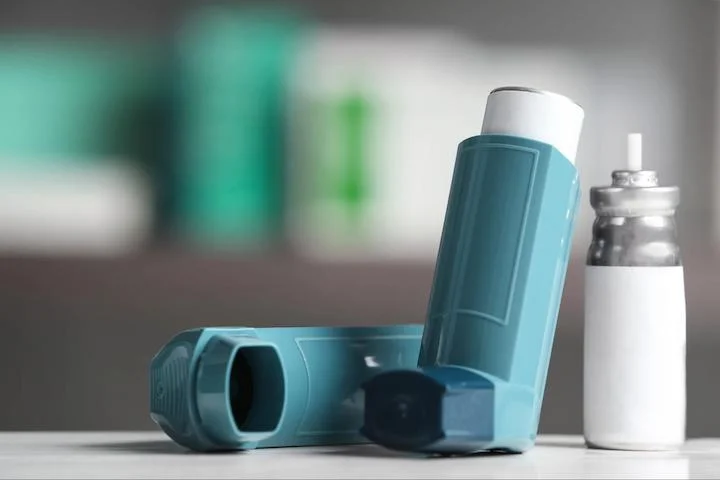
Advantages of PBT
The advantages of polybutylene terephthalate (PBT) for injection molding include UV resistance, availability in FDA compliant grades, heat resistance, and dielectric strength.
UV Resistance
PBT exhibits excellent UV resistance and retains its strength, impact resistance, and other mechanical properties when exposed to sunlight. The addition of fillers such as carbon black can further improve its UV resistance.
FDA Compliance
Not all grades of PBT meet U.S. Food and Drug Administration (FDA) requirements, but some materials are FDA compliant. For example, Celanex® PBT grades with an MT designation comply with FDA 21, CFR177.1660 for food contact substances (FCS).
Heat Resistance
Injection molded PBT can resist long-term exposure to heat. It has a continuous service temperature between 80ºC and 140ºC, depending on the grade and whether a glass filler is added for higher-temperature support. PBT’s heat deflection temperature, the temperature at which a sample deforms under a specified load, is 150ºC (@ 0.45 MPa).
Dielectric Strength
A material’s dielectric strength refers to its ability to act as an electrical insulator, and Polybutylene terephthalate has a dielectric strength of 23.7 kV/mm, which is considered to be good. The higher the dielectric strength, the greater the voltage the material can withstand before its insulating properties break down.
Disadvantages of PBT
PBT isn’t the best choice for some types of injection molded parts. In addition to rapid crystallization and deformation during cooling, its disadvantages include notch sensitivity, warping, and low hydrolysis resistance.
High Notch Sensitivity
PBT’s high notch sensitivity means that this specialty plastic tends to crack when there are stress concentrations. By adding reinforcing fillers such as glass fibers, however, cracks and their propagation can be reduced.
Warping
Stress imbalances can cause injected molded PBT to warp as it cools. Glass-filled PBT helps to reduce potential defects, but injection molders still need to carefully control processing variables like mold temperature and injection molding speed to get good results.
Low Hydrolysis Resistance
PBT can be degraded by long-term exposure to hot water, diluted acids, or strong mineral acids, so shouldn’t be used for applications with extended exposure to these substances.
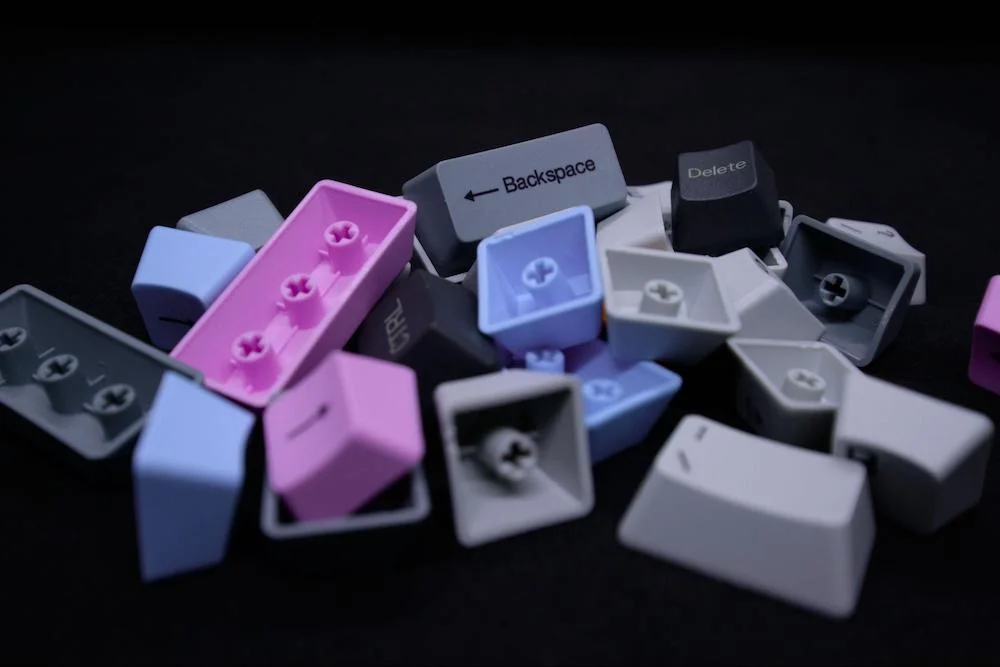
PBT Injection Molding Applications
Injection molded PBT has many electrical, medical, and food processing applications.
Electrical Applications
Electrical applications for PBT include:
- Electrical equipment housings
- Electrical connectors
- Terminal blocks
- Cable sheathing
- Circuit breakers
- Switchgear
- Keyboard caps
Medical Applications
Medical applications may require FDA-compliant PBT, and include:
- Medical, drug deliver, and lancing devices
- Injection pens and autoinjectors
- Dry powder inhalers and dose counters
- Asthma inhalers
- Patch pumps and wearable pumps
- Fluid handling and filtration
Food Processing Applications
Food processing applications for food contact safe PBT include:
- Machinery parts
- Bushes, bearings and pistons
- Valve and manifolds
Properties of Injection Molded PBT
Before deciding to use injection molded PBT, designers must consider its physical, mechanical, and processing properties, which are listed in Table 1 below. Note the differences between unfilled PBT and injection molded PBT with a 30% glass fill.
Unfilled PBT | 30% Glass-Filled PBT | ||
---|---|---|---|
Physical | Density (g/cm3) | 1.31 | 1.55 |
Shrinkage Rate (%) | 0.5–2.2 | 0.2–1 | |
Rockwell Hardness (R) | 117 | 116 | |
Mechanical | Tensile Strength at Yield (MPa) | 65.2 | 118 |
Elongation (%) | 43.1 (@ Break) | 3.76 (@ Break) | |
Flexural Modulus (GPa) | 4.53 | 8.5 | |
Flexural Strain (%) | 7 (@ Yield) | 3.42 (@ Yield) | |
Injection Molding | Drying Temperature (°C) | 118 | 120 |
Drying Time (hrs) | 2–4 | 2–4 | |
Melt Temperature (°C) | 251 | 250 | |
Mold Temperature (°C) | 78.7 | 80.1 |
Table 1: Properties of PBT
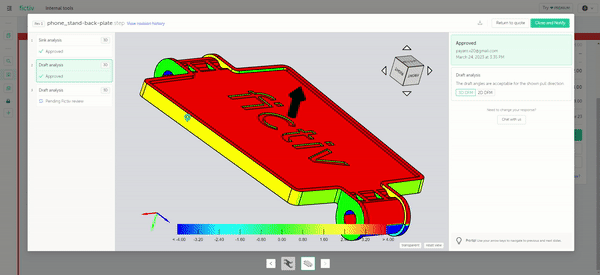
Design Guidelines for PBT Injection Molding
PBT parts that are poorly designed can exhibit injection molding defects. Fictiv’s injection molding experts can help you refine your designs so that you get great results, and you should download our free Injection Molding Design Guide to use as a reference for your next project.
Download the Injection Molding Design Guide
The following sections examine some PBT-specific design considerations.
Wall Thickness
Because PBT has a low melt viscosity, it supports injection molded parts with thinner walls and cross sections. For smaller parts, a minimum wall thickness of 0.7 mm is achievable, and for larger parts, walls as thin as 1.5 mm are possible.
Regardless of part size, wall thickness should be kept consistent, and if thicker walls are required in some areas, make the transition gradual. Also, avoid excessively thick walls because they tend to cause internal voids and sink marks. The maximum wall thickness is 12.7mm, but it’s better to use cores to reduce the effective thickness.
Shrinkage
To ensure the dimensional accuracy of your parts, consider shrinkage during part design. Compared to other polymers, PBT has a relatively high shrinkage rate and shrinks at different rates in different directions, which can cause warping. The shrinkage rate for unfilled PBT is between 0.5% and 2.2%, but the inclusion of glass fillers up to 30% volume by weight can reduce PBT shrinkage to 0.2% and 1%.
Radii
PBT’s high notch sensitivity requires the use of large radii on all corners — sharp corners will reduce part life and risk potential part failure. Apply a radius that is equal to between 25% and 60% of the adjacent wall thickness. And for the root of threaded features — a common failure point for notch-sensitive materials — use a radii between 0.127 mm and 0.254 mm.
Draft Angle
Applying a draft angle, or taper, to the walls of parts makes it easier to eject them from the injection mold. In general, mold cavities with deeper depths require larger draft angles. In many cases, a draft angle as low as 0.5° is possible; however, 1° provides the best results with injection molded PBT.
Part Tolerance
Injection molding tolerances are affected by the grade of material and type of injection mold. Unfilled PBT has different tolerances than glass-filled PBT, and steel injection molds can achieve tighter tolerances than aluminum injection molds. There are also differences between commercial and fine tolerances, and tighter-tolerance molds come with a higher cost.
Threads
PBT injection molding supports the creation of threads, though coarse threads are preferred over fine threads, and threads with a pitch finer than 28 are not recommended. Designs should round the root and crest of threads, and apply a radius between 0.1 mm and 0.3 mm to reduce stress concentrations.
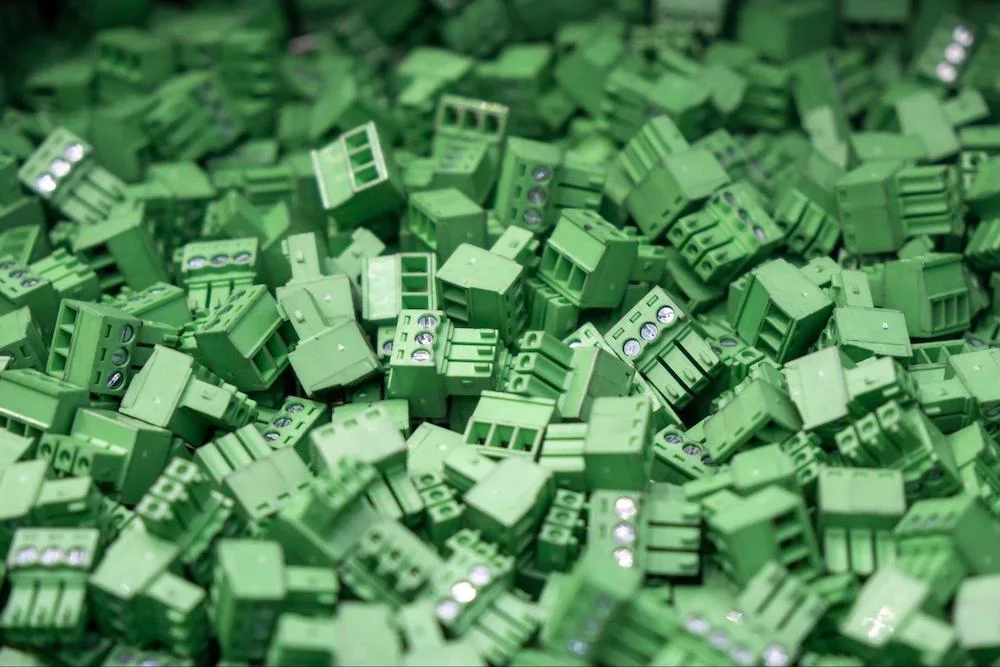
PBT Processing Guidelines
PBT injection molders need to follow specific processing guidelines for best results. Because adherence to these guidelines is beyond a part designer’s immediate control, it’s important to work with an experienced injection molder like the ones in Fictiv’s carefully-vetted network.
Moisture
PBT is not very hygroscopic at room temperature;, but it’s particularly sensitive to moisture at higher temperatures. Therefore, this thermoplastic material should be dried at 120ºC for between 2 and 4 hours prior to injection molding to prevent the appearance of part defects, which can appear as dark spots..
Temperature Control
PBT’s injection molding temperature is between 240ºC and 280ºC, as parts will turn a darker color if they are heated to the point of thermal decomposition. Mold temperature varies by PBT grade, but is generally around 80ºC. PBT’s rapid crystallization reduces cycle times, but injection molders must balance mold temperature against injection pressure and speed.
Injection Pressure
With its low melt viscosity, PBT flows easily during injection molding, so lower injection pressures can be used. In general, an injection pressure between 60 MPa and 90 MPa is recommended. Glass-filled grades of PBT require slightly higher injection molding pressures of between 80 MPa and 100 MPa.
Injection Speed
Injected molded PBT cools quickly, so it’s critical to keep the injection speed high enough to prevent the plastic from solidifying before the mold has been completely filled — otherwise, weld lines and sub-optimal surface finishes may result.
Potential Alternatives to PBT
If PBT isn’t the right material for your injection molding project, polypropylene (PP) and polyethylene (PET) are potential alternatives given their properties — so we’ve provided information about them below to see if they’re right for your application.
Fictiv’s plastic injection molding service offers all three materials, and many others that are suitable for a wide range of applications.
Polypropylene (PP)
Compared to PBT, polypropylene has better hydrolysis resistance and impact resistance, but PP is softer than PBT.
PET (Polyethylene Terephthalate)
Compared to PBT, PET has a slightly higher glass transition temperature along with greater mechanical properties and better high-temperature performance. PBT has a higher impact resistance, however. Both of these materials have poor hydrolysis resistance.
Succeeding With PBT Injection Molding
PBT is a popular injection molding plastic, but a manufacturing-ready design and a skilled production partner are critical. Fictiv has the engineering experts and global manufacturing network you need to get quality injection-molded PBT parts. From prototyping through production, we’re here to help you succeed.
Create your free Fictiv account and request an injection molding quote today — we mold complex parts at ridiculous speeds!