Time to read: 6 min
Manufacturing supply chain management (SCM) is critical in ensuring that design, materials, processes, and logistics are seamlessly coordinated to deliver high-quality products efficiently. Effective SCM optimizes resource allocation, minimizes waste, enhances production efficiency, and strengthens supplier relationships.
By incorporating lean manufacturing principles, companies can refine their operations further to reduce inefficiencies and maximize value creation. Additionally, adopting emerging digital technologies such as artificial intelligence (AI), blockchain, and automation significantly enhances supply chain visibility and decision-making.
In today’s competitive and fluctuating global market, manufacturers must balance cost control, efficiency, and risk mitigation to maintain profitability and operational resilience. This article explores key aspects of manufacturing supply chain management, including its core functions, challenges, best practices, and future trends.
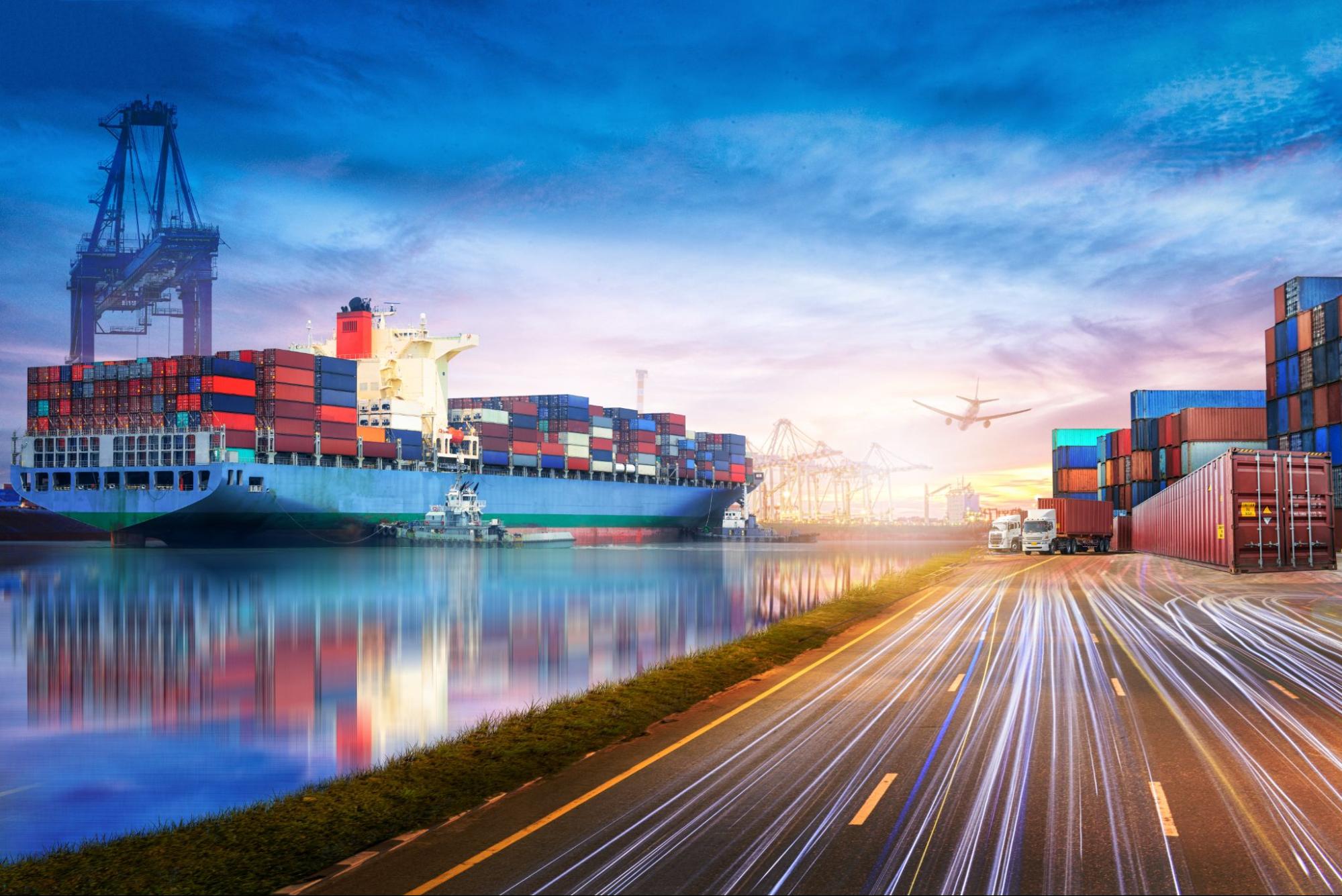
What Is Manufacturing Supply Chain Management?
Manufacturing supply chain management encompasses the comprehensive coordination of resources, processes, and logistics necessary to produce and deliver goods efficiently. It integrates multiple functions to ensure seamless operations, reduce inefficiencies, and maintain product quality throughout the production life cycle.
Here are some of the key components of manufacturing SCM:
Sourcing
Sourcing involves identifying, selecting, and managing suppliers that provide raw materials, components, and essential goods needed for production. Effective sourcing strategies focus on quality control, negotiating raw material costs, and finding reputable and reliable suppliers.
Production
The production component of SCM involves converting raw materials into finished products through various manufacturing processes. Ensuring production efficiency involves optimizing workflows, reducing downtime, and maintaining high-quality product standards.
Logistics
This function covers transportation, warehousing, and handling of materials and finished goods. Efficient logistics management ensures timely deliveries, minimizes transportation costs, and prevents supply chain disruptions.
Inventory Management
This process balances supply and demand by maintaining optimal stock levels to prevent shortages or excess inventory. Techniques such as demand forecasting, just-in-time (JIT) inventory, and automated tracking systems help improve inventory efficiency.
Distribution
This final stage ensures that finished products reach customers promptly and efficiently. A well-structured distribution network improves customer satisfaction, reduces delivery times, and optimizes supply chain costs.
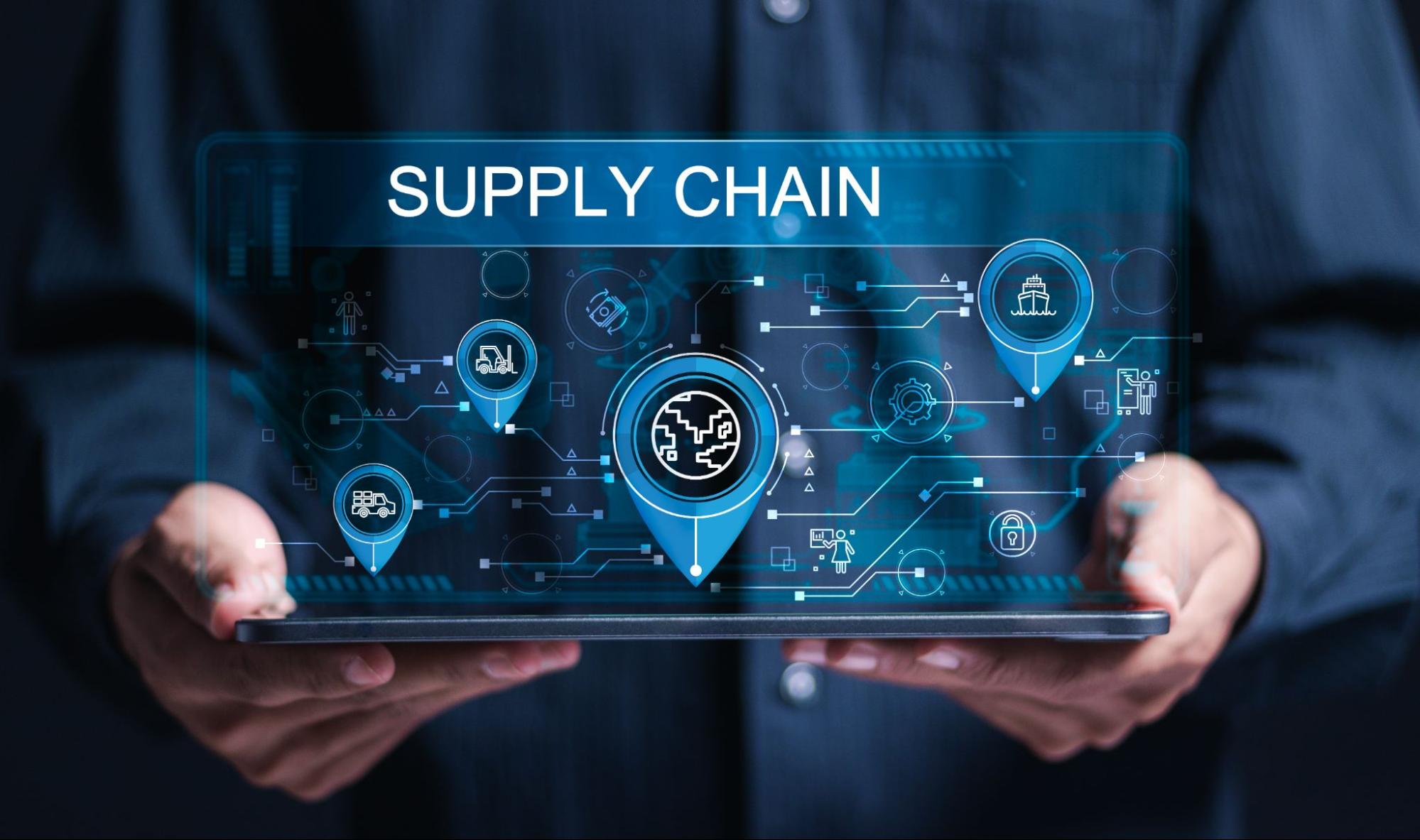
The Importance of Supply Chain Management in Manufacturing
An optimized supply chain is essential for achieving business success in manufacturing. Effective supply chain management provides several of the following key benefits that directly impact a company’s profitability and market competitiveness:
Cost Reduction and Waste Minimization
Implementing efficient procurement, production, and distribution strategies significantly lowers operational costs. Additionally, lean manufacturing techniques, such as minimizing excess inventory and reducing production waste, further enhance cost savings.
Production Efficiency and Faster Time-to-Market
By improving coordination between sourcing, production, and logistics, manufacturers can accelerate production cycles and respond more quickly to market demands. This is often accomplished through the use of enterprise resource planning (ERP) software, which ultimately leads to faster delivery times, improved customer satisfaction, and market competitiveness.
Enhanced Supplier Relationships and Risk Mitigation
Managing the manufacturing supply chain can help companies develop strong supplier partnerships while also ensuring consistent material availability, better pricing negotiations, and collaborative problem-solving. Additionally, implementing risk management strategies—such as supplier diversification and predictive analytics—helps manufacturers anticipate and mitigate potential supply chain disruptions.
Common Challenges in Manufacturing Supply Chain Management
Despite its benefits, SCM faces several challenges that can impact operational performance. Some of those challenges are described below:
Supplier Disruptions and Global Logistics Issues
Geopolitical tensions, trade restrictions, and natural disasters can disrupt supply chains, causing delays and shortages in the delivery and supply of raw materials and products.
Demand Forecasting and Inventory Optimization
Inaccurate demand predictions can lead to excess inventory or stockouts, both of which can affect profitability and customer satisfaction.
Cost Fluctuations in Raw Materials and Labor
Market volatility and economic shifts can result in unpredictable changes in material costs and wages, directly impacting manufacturing budgets.
Managing Complexity in Multi-tier Supply Chains
Coordinating multiple suppliers, third-party logistics providers, and distributors increases the complexity of managing supply chains effectively, which may require advanced data analytics and communication tools.
Tariffs and Trade Policy Uncertainty
Tariffs and shifting trade policies can significantly increase the total landed cost of imported materials, components, and finished goods. These unexpected expenses can erode profit margins and force companies to re-evaluate sourcing strategies, including location. Navigating tariff classifications, compliance requirements, and policy changes adds an administrative burden and demands close collaboration between supply chain, legal, and finance teams.
Lean Manufacturing and Supply Chain Optimization
Applying lean principles to manufacturing supply chain management leads to enhanced efficiency, cost savings, and waste reduction for manufacturers. Key lean manufacturing strategies and how they synergize with supply chain optimization are discussed below:
Just-in-Time (JIT) Manufacturing
JIT focuses on producing only what is required, precisely when it is needed. This helps reduce excess inventory, which allows manufacturers to lower overall storage costs, minimize waste, and respond more effectively to fluctuations in demand.
Waste Reduction
A key concept of lean manufacturing is waste reduction. Waste reduction strategies prioritize eliminating non-value-adding activities such as overproduction, excessive and unnecessary transportation of materials and products, and limiting machine downtime. Manufacturers can achieve sustainable cost savings by identifying inefficiencies and implementing continuous improvement initiatives.
Real-time Tracking and Automation
Leveraging digital manufacturing tools such as Internet of Things (IoT) sensors, artificial intelligence (AI), and blockchain technology can further enhance a manufacturer’s capability to manage its supply chain. For example, smart sensors can track inventory in real time and alert manufacturers when supply is low.
At the same time, machine learning algorithms can analyze historical sales data and market trends to predict future inventory needs. By implementing digital manufacturing tools, manufacturers can effectively and efficiently monitor inventory, forecast demand with higher accuracy, and optimize decision-making for greater efficiency.
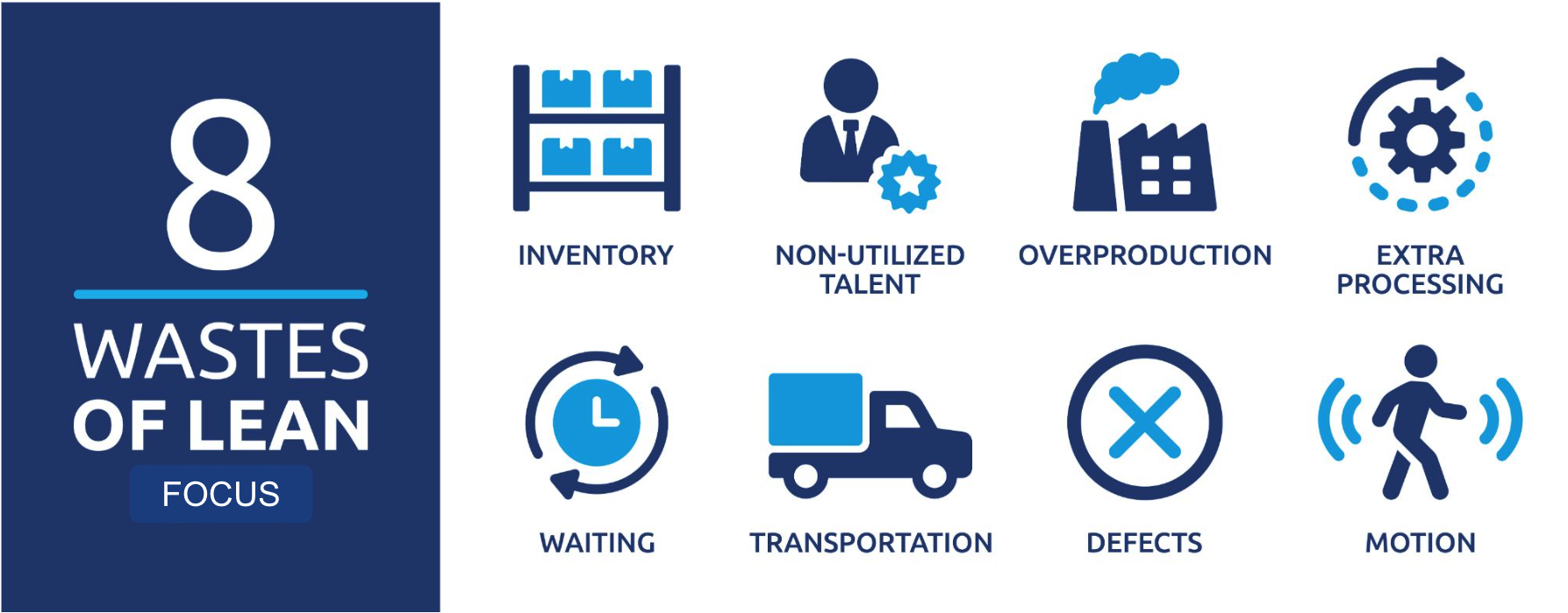
Best Practices for Manufacturing Supply Chain Management
To address the challenges described above and to improve supply chain management efficiency, manufacturers should adopt the following best practices:
AI and Digital Technologies
Implementing AI-powered predictive analytics helps manufacturers anticipate demand fluctuations, streamline procurement processes, and enhance operational efficiency. For example, Tesla uses AI-powered robots in its Gigafactories to automate material handling, assembly, and quality control, improving production speed and consistency.
Strategic Supplier Partnerships
Strengthening collaboration with key suppliers enhances supply chain resilience, ensuring consistent material availability and improved cost management. A notable example is Apple, which works closely with key suppliers like TSMC (for semiconductor chips) and Foxconn (for assembly) to ensure a stable supply of components and maintain product quality standards.
Flexible Sourcing Strategies
Diversifying supplier networks reduces dependency on a single source and helps mitigate risks associated with supply chain disruptions and economic fluctuations. After facing supply chain disruptions during the COVID-19 pandemic, many US companies shifted from relying solely on China-based suppliers to adopting a mix of local and international vendors to increase supply chain resilience.
Transparency with Blockchain Technology
Blockchain-enabled SCM solutions improve traceability, enhance security, and provide real-time visibility into production and logistics, leading to greater trust and efficiency across supply chain networks. An example of this is when IBM and Maersk developed TradeLens, a blockchain-based shipping platform that improved transparency and reduced paperwork in global logistics.

Case Studies: Effective Supply Chain Strategies in Manufacturing
- Example 1: Tesla, a leading automotive manufacturer, successfully implemented lean principles to streamline production workflows, reduce waste, and lower operational costs. By integrating JIT manufacturing and automation, they achieved significant improvements in lead times and efficiency.
- Example 2: GE uses digital twin technology to model and monitor the performance of industrial equipment and products like jet engines and gas turbines. These virtual replicas help predict maintenance needs, optimize performance, and reduce downtime.
- Example 3: Siemens leveraged AI-driven demand forecasting models to optimize inventory levels, reducing procurement bottlenecks and improving response times to market fluctuations.
The Future of Manufacturing Supply Chain Management
Emerging technologies and trends—including digital manufacturing tools like automation and AI, or sustainability and eco-friendly manufacturing practices—are driving the evolution of SCM. Practices that will impact the future of manufacturing supply chain management are described below.
Automation, AI, and Digital Twins
The use of AI-powered robotics automation, machine learning, and digital twin simulations is transforming supply chain decision-making. Integrating these tools helps with predictive maintenance, reduces inefficiencies and human error, and provides end-to-end supply chain visibility from raw material sourcing to final product delivery.
Sustainability Initiatives
With a growing emphasis on eco-friendly manufacturing, companies are integrating sustainable practices such as carbon-neutral logistics, recyclable packaging, and ethical sourcing to potentially gain a competitive advantage.
Regionalized Supply Chains
As companies seek to mitigate risks associated with global dependencies, many are shifting toward localized supply chains, either by nearshoring or reshoring. This helps reduce reliance on distant suppliers and improve manufacturing resilience in times of crisis.
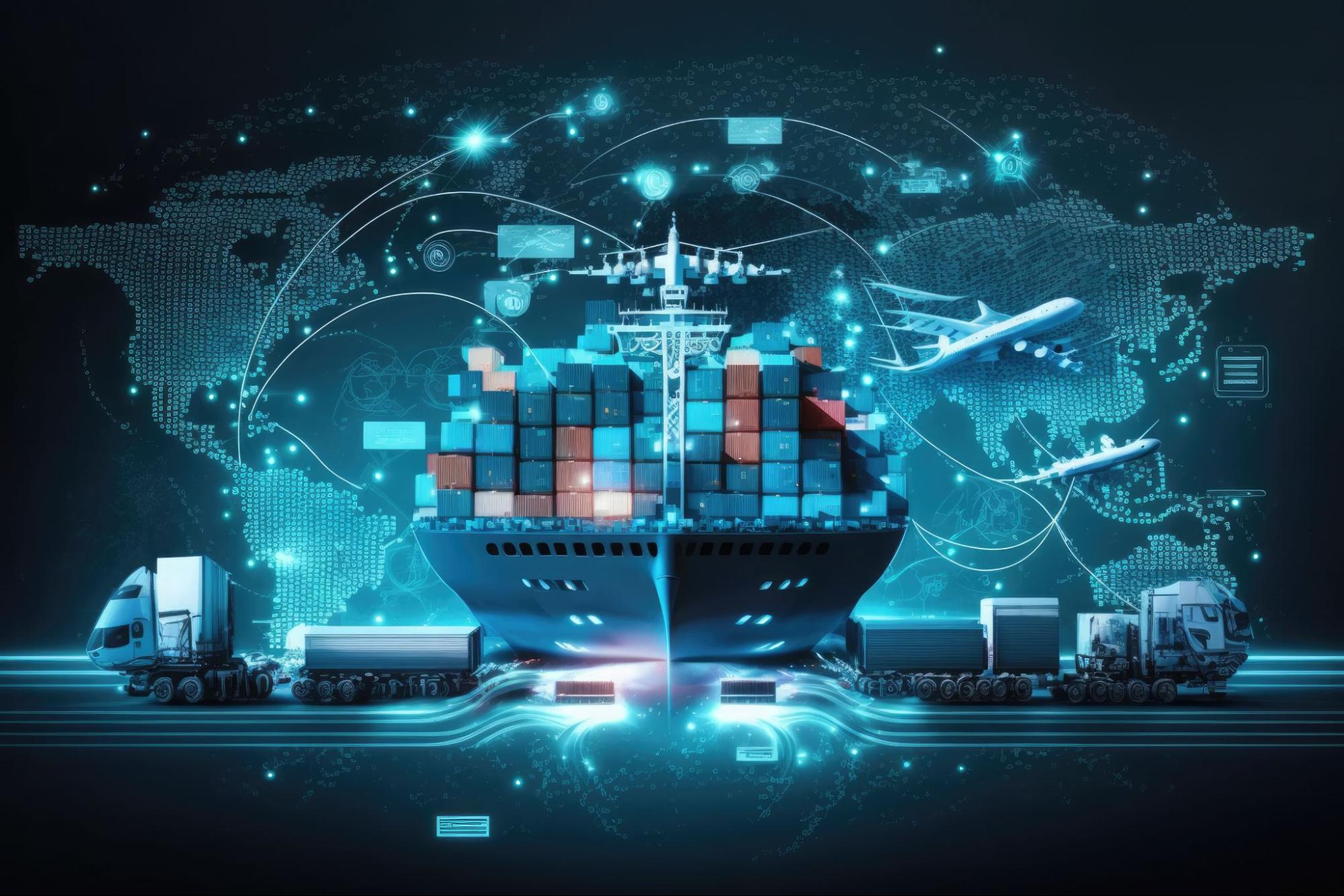
Optimizing Manufacturing Supply Chains Through Innovation and Technology
Manufacturing SCM is crucial for optimizing efficiency, reducing costs, and maintaining competitiveness. By implementing lean principles, embracing digital transformation, and addressing common challenges, manufacturers can build resilient, agile supply chains. Furthermore, the adoption of AI and automation further enhances visibility and decision-making, ensuring long-term operational success.
Companies must continuously refine their supply chain strategies to stay competitive in an increasingly complex manufacturing landscape. Fictiv offers digital manufacturing solutions, including CNC machining, 3D printing, and injection molding, to help streamline SCM processes.
Contact Fictiv to explore how these solutions can optimize your supply chain operations.