Time to read: 7 min
Introducing a new product to the market comes with many challenges and unexpected turns. It’s never as easy as it sounds, but having a structured plan for team alignment goes a long way.
The New Product Introduction (NPI) process follows a structured approach to ensure a product moves efficiently from concept to market launch. Each phase plays a critical role in refining the design, validating performance, optimizing manufacturability, and ensuring regulatory compliance. NPI is integrated with new product development (NPD) but includes later stages of bringing the product to market.
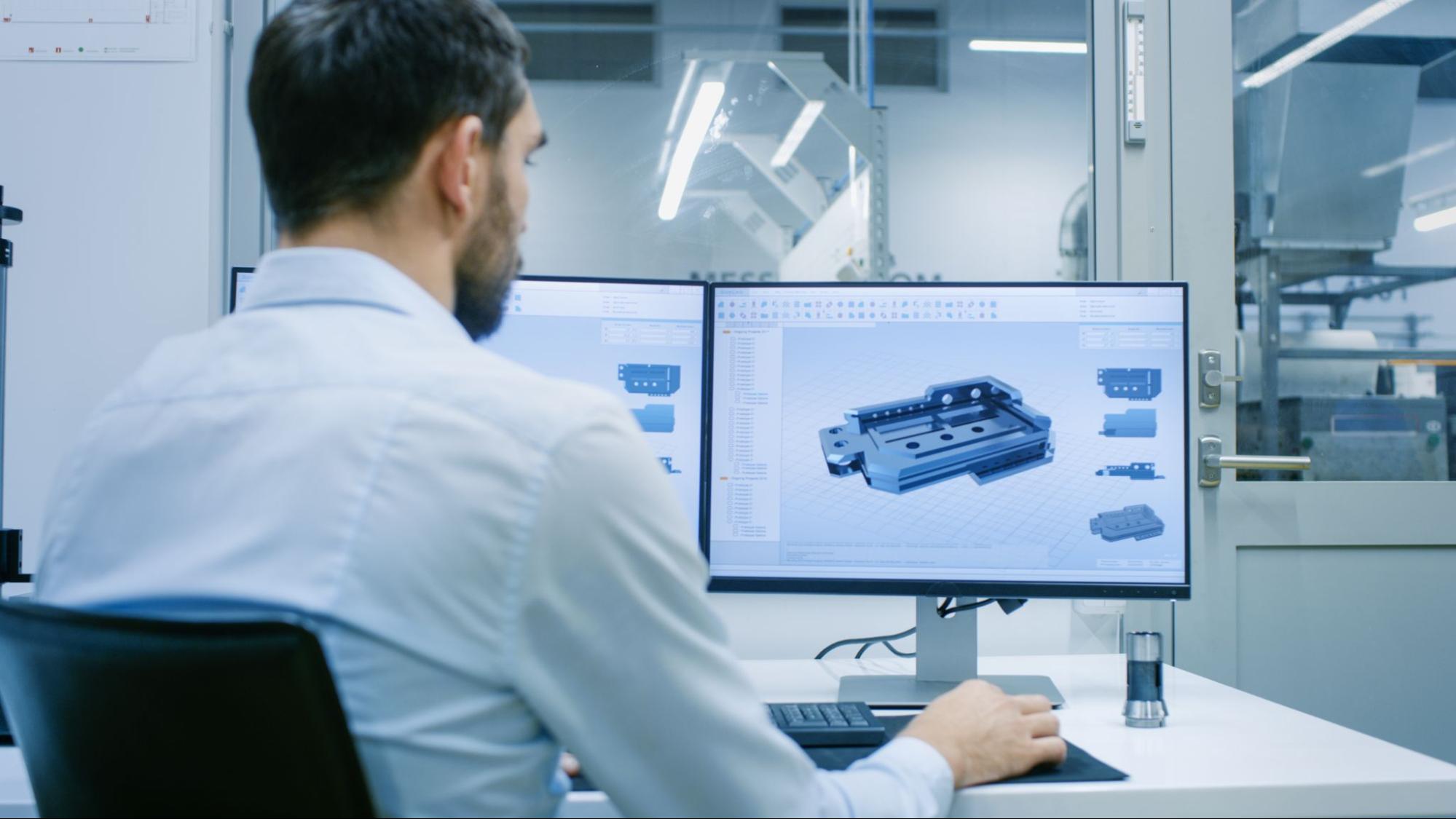
This article explores the traditional NPI process, the key players involved, and the critical steps necessary for alignment. It also examines various manufacturing processes, such as machining (CNC), injection molding (IM), and 3D printing (3DP), while incorporating case studies and data from Fictiv to illustrate how strategic planning and digital manufacturing can streamline NPI.
A well-executed process reduces risks, shortens development cycles, and increases the likelihood of a successful product launch. The following sections highlight how careful planning and cross-functional collaboration contribute to a streamlined transition from idea to production.
Phases of The NPI (New Product Introduction) Process

The traditional NPI process consists of the following phases:
Phase 1: Concept & Feasibility
This phase involves brainstorming, market research, idea validation, and feasibility analysis to ensure the product concept aligns with market needs and customer requirements. Market research includes gathering customer insights, assessing competitor products, and identifying gaps in the market.
Often this process involves evaluating similar designs, whether from prior iterations of similar concepts, or competitor ideas, to improve upon existing concepts or provide a solution where current designs are lacking.
Phase 2: Design & Development
During this phase, detailed product design work begins. Engineers develop CAD models, conduct simulations like finite element analysis or computational fluid dynamics, and build prototypes to validate the design’s form, fit, and function. Material selection is essential at this step to ensure that the chosen materials align with performance, durability, and cost requirements.
Engineers also work closely with suppliers and internal teams to optimize the design for manufacturability (DFM) and design for assembly (DFA) to reduce production complexity and costs. Various manufacturing processes, including CNC machining, injection molding, and 3D printing, are considered at this stage to determine the most efficient and cost-effective production method.
Digital manufacturing plays a key role in this phase by enabling rapid prototyping and iterative design improvements. To meet customer requirements, Fictiv provides human and AI design for manufacturability (DFM) feedback to ensure that the product concept is manufacturable before investing in further development. With digital platforms like Fictiv, teams can quickly generate and test multiple design iterations, allowing rapid design validation without the high costs of traditional tooling.
Phase 3: Testing & Validation
Once the design is finalized, the product undergoes extensive testing and validation to ensure compliance with quality, safety, and regulatory standards. Functional testing verifies that the product meets all performance specifications, while environmental and stress testing assesses its durability and reliability under various environmental and loading conditions.
Compliance testing ensures adherence to industry-specific regulations, avoiding legal and market-entry obstacles. Based on test results, engineers make iterative design refinements to improve both performance and manufacturability.
Different manufacturing techniques are validated to determine the best process for scaling production during this stage—whether CNC machining for precision parts, injection molding for high-volume production, or 3D printing for rapid iteration.
Phase 4: Pre-Production or Bridge Production
Pre-production, or bridge production, involves a limited production run to validate manufacturing processes, supply chain logistics, and product quality at scale. Standard operating procedures (SOPs) are established during this phase to ensure consistency and efficiency in full-scale manufacturing.
Engineers and process teams identify and mitigate potential bottlenecks in the production line to ensure a seamless workflow. Supplier reliability and material consistency are also validated to avoid disruptions in mass production. Final quality checks confirm that the product meets all design and performance specifications.
Additionally, feedback from early users or test markets provides valuable insights, enabling refinements before moving to full-scale production. Manufacturing processes such as injection molding may be fine-tuned at this stage to ensure consistent production quality, while CNC machining may be optimized for final precision adjustments.
Phase 5: Full-Scale Production & Market Launch
After successful bridge production, the product moves into full-scale manufacturing and is introduced to the market. Production is scaled up to meet market demand while maintaining quality control measures. Coordination with supply chain and logistics teams ensures the timely delivery of products to distribution channels. Simultaneously, marketing and sales teams launch campaigns to drive customer adoption and market penetration.
Early sales data and customer feedback are closely monitored, allowing the company to address post-launch issues and continuously improve the product. At this stage, automated production processes such as injection molding or CNC machining play a crucial role in ensuring consistency and efficiency in mass production. This phase marks the final step in the NPI process, ensuring a successful market entry and long-term product viability.
Key Roles, Factors, and Goals in NPI
A cross-functional approach is essential for a successful NPI. Each role and factor is critical to the successful rollout of a new product into the market. Table 1 is a breakdown of the primary contributors and their key responsibilities:
Cross-Functional Role | Goals and Responsibilities |
Design Engineer | Design engineers develop and refine product designs. They use their mechanical knowledge in making decisions about part geometry and tolerances to meet customer and industry specifications. |
Industrial Designer / Color, Material, Finish (CMF) Designer | Industrial and CMF designers support brainstorming creative solutions to ensure the original design intent and aesthetic requirements are maintained throughout development. |
Manufacturing Engineer | Manufacturing engineers ensure manufacturability and process optimization for quality and efficiency. They often design the manufacturing flow of a part/assembly and work closely with assembly lines. |
Supply Chain Specialists | Supply chain specialists source materials and manage supplier relationships. |
Product Marketing Staff / Product Manager | Product marketing staff define product positioning relative to competing products and help establish a go-to-market strategy. |
Quality Engineer | Quality engineers focus on ensuring new products satisfy customer and regulatory requirements. They manage quality issues as they arise in manufacturing and post-sale. |
Process Engineer | Process engineers, like manufacturing engineers, help optimize manufacturing processes but have a more refined focus on continuous improvement. |
Leadership | Leadership roles, including executive managers, senior engineers, and operations managers, provide strategic oversight throughout the NPI process and help allocate labor resources efficiently. |
Compliance | Compliance goes hand in hand with quality and is necessary to ensure new products comply with various government and industry regulatory requirements. |
Sales | Sales staff develop customer relationships, and their efforts help drive the adoption and purchase of new products. |
Primary Contributors and Their Key Responsibilities
Preparation and Planning in NPI
Careful and thoughtful planning is essential to an efficient NPI process. Proper preparation upfront can significantly shorten cycle times by reducing costly delays and rework. NPI is the structured methodology used to bring a product from concept to market, ensuring all teams are aligned and risks are mitigated early.
On average, the time required to introduce a new product to market can range from 500 to 5,000 hours, depending on complexity. Early collaboration among cross-functional teams, leveraging digital manufacturing tools, and defining critical requirements upfront can streamline the process and ultimately accelerate time to market. The steps below illustrate the best practices for ensuring a new product is introduced to the market as seamlessly as possible.
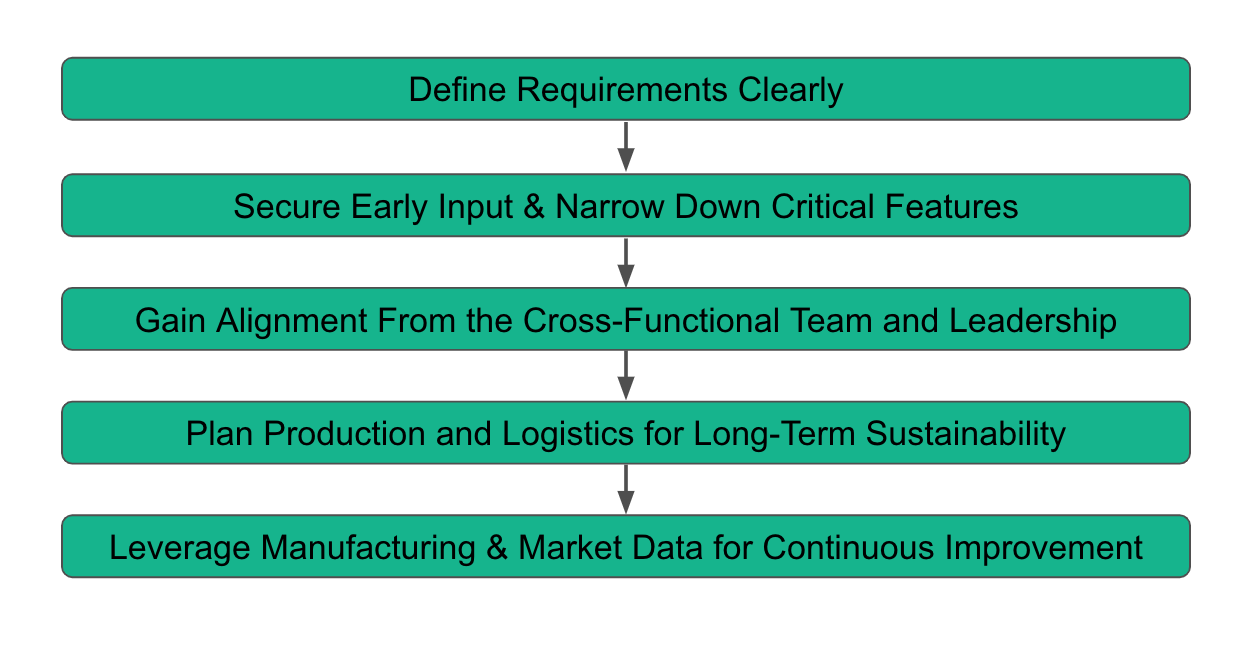
Step 1: Define Requirements Clearly
Each stakeholder must identify and negotiate the most critical constraints to ensure all team members align on key objectives. Customer requirements should always take precedence and be communicated clearly to avoid misunderstandings. A multi-pronged approach simplifies requirement alignment to reduce the need for costly rework later in the process.
Step 2: Secure Early Input & Narrow Down Critical Features
Key product dimensions, materials, and documentation must be identified early. Securing Design for Excellence (DFX) input from suppliers and internal stakeholders during alpha or beta testing helps refine the product before full-scale production. By integrating quality into the design from the start, companies can reduce costly iterations and mitigate risks related to manufacturing and performance.
Step 3: Gain Alignment From the Cross-Functional Team and Leadership
Clear communication channels and structured decision-making frameworks ensure that all teams remain aligned throughout the NPI process. Regular alignment meetings help maintain cohesion among stakeholders, while data-driven decision-making at each step of the NPI process supports the prioritization of key design and manufacturing parameters.
Step 4: Plan Production and Logistics for Long-Term Sustainability
A resilient supply chain strategy is crucial for long-term sustainability. Securing reliable raw material sources and incorporating sustainable manufacturing processes can minimize waste and energy consumption. Additionally, scalability and global logistics planning must be considered to ensure long-term production viability.
Step 5: Leverage Manufacturing & Market Data for Continuous Improvement
Real-time manufacturing data provides insights to optimize production processes, while quality and performance feedback drive iterative design improvements. Collaboration with marketing teams ensures that product features align with customer expectations and evolving market demands.
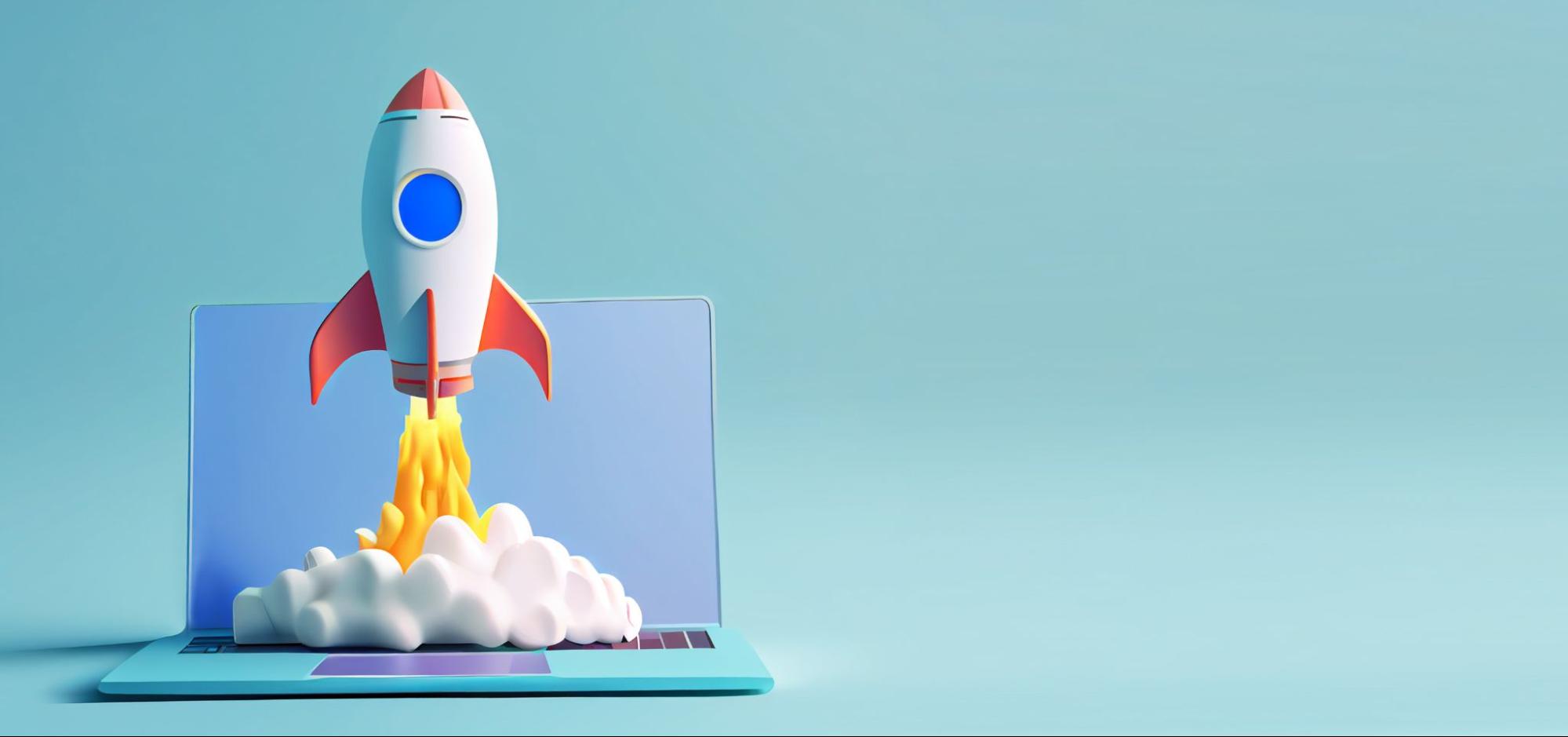
Accelerate Product Launches With a Streamlined NPI Process
The NPI process is key to successfully launching new products, involving stages from concept validation to production. Successful execution requires cross-functional collaboration, strategic planning, and advanced manufacturing technologies. Organizations can reduce cycle times and mitigate risks by defining requirements, prioritizing features, and aligning stakeholders.
Digital manufacturing solutions, like those from Fictiv, enhance NPI by enabling rapid prototyping, optimizing processes, and streamlining logistics. Technologies such as CNC machining, injection molding, and 3D printing offer flexibility, while AI-driven analytics improve quality and efficiency.To stay competitive in a fast-evolving marketplace, companies should leverage Fictiv’s advanced digital tools and built-in, well-structured NPI process to accelerate time-to-market, reduce costs, and improve product quality. Sign up with Fictiv today to bring your next product to life faster and more efficiently than ever.