Time to read: 6 min
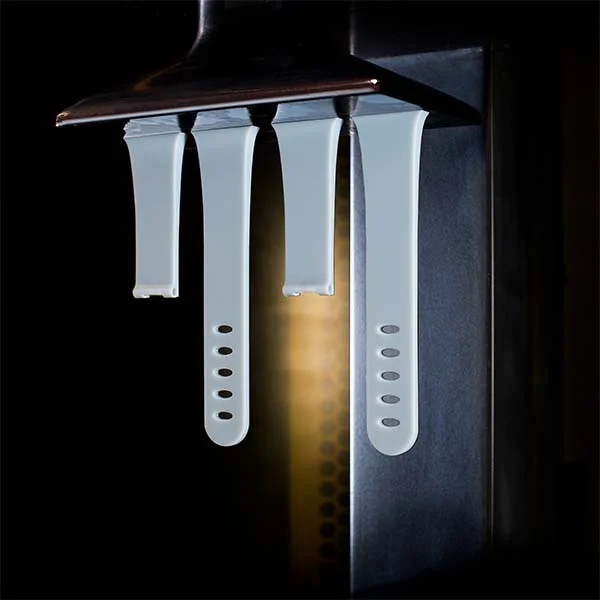
Fictiv, the operating system for custom manufacturing, today announced Carbon Digital Light Synthesis (DLS) 3D printing technology as part of our robust, production-level 3D printing capabilities. Carbon DLS printing offers injection molding level repeatability alongside the ability to manufacture complex geometries, similar to our stereolithography (SLA) and fused deposition modeling (FDM) options. Within this new offering is the capability to provide carbon DLS parts from the following proprietary materials:
- CE 221
- EPU 40
- EPU 41
- EPX 82
- EPX 86FR
- FPU 50
- MPU 100
- RPU 70
- SIL 30
- Loctite 3D IND405 Clear
- Loctite 3D IND147
- Loctite 3D 3843
- UMA 90
What is Carbon Digital Light Synthesis?
The carbon DLS process involves 3D printing of a liquid polymer resin, which is selectively cured using the digital light projection process, similar to SLA 3D printing. The bottom of the liquid polymer resin tank has an oxygen-permeable membrane, which creates a zone of uncured resin beneath the cured resin, known as the “dead zone.” This “dead zone” allows layers to be built on each other without the build layers sticking to the platform, enabling simplified removal of the part.
What Are the Advantages of Carbon Digital Light Synthesis?

Carbon DLS 3D printing offers parts with high homogeneity due to the nature of the curing process. Parts printed with carbon DLS manufacturing offer isometric properties; in other words, you get the same strength parts regardless of print orientation. The carbon DLS process is also advantageous for the following reasons:
- Reduce weight and maximize strength with innovative material selection.
- Higher production repeatability with printing that creates isotropic parts to ensure your assemblies fit properly the first time (within 0.10”).
- Injection molding results in reach at lower quantities; most cost-effective for 20-500 parts or geometries that are traditionally difficult to injection mold (such as undercuts or undrafted walls).
- Rapid print speeds Carbon DLS can achieve rapid print speeds compared to traditional SLA methods, thanks to its continuous liquid interface production (CLIP) technology
- Fully homogeneous parts, without voids or delamination. The digital light projection system ensures high-resolution printing, allowing for intricate details and fine surface finishes. The oxygen-permeable membrane and continuous printing process contribute to consistent layer-to-layer curing and reduce the risk of warping or deformation.
- A wide range of material options: Carbon offers a range of proprietary resins that can exhibit characteristics such as high strength, durability, flexibility, and biocompatibility, making them suitable for various applications.
- Production level parts: Carbon DLS is often used for both prototyping and end-use production, making it suitable for various industries, including automotive, aerospace, healthcare, and consumer goods.
How Do Carbon DLS Materials Compare to Common Thermoplastics?
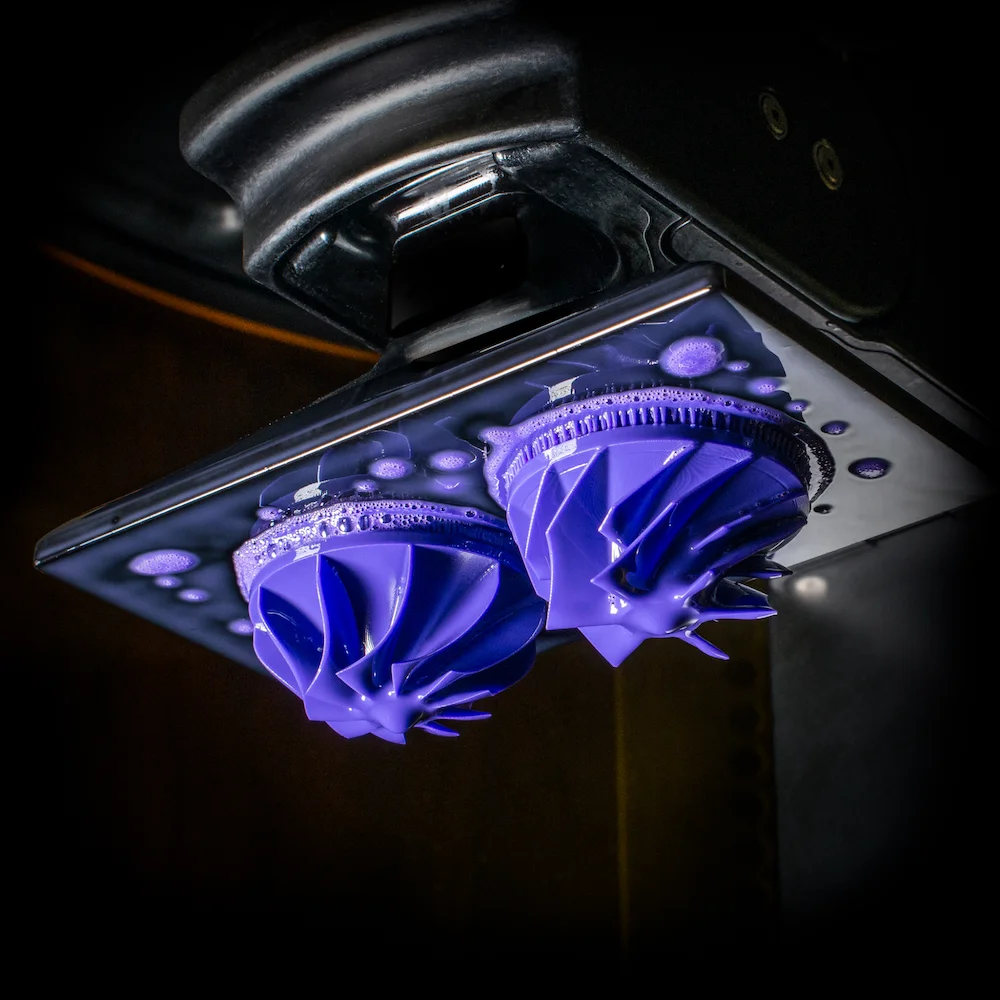
You can rest assured that there is a comparable carbon material with properties similar to your favorite thermoplastic. There are many options for comparable carbon materials for the most popular thermoplastics. Utilize the chart below to learn more about how these materials stand up to each other:
Common Thermoplastic | Thermoplastic Key Properties | Carbon DLS Material Alternatives |
ABS | Tough, rigid material with moderate temperature and chemical resistance. | RPU 70, Loctite 3843 and UMA 90 offer similar stiffness and are easy to use, but have lower impact toughness. RPU 130 offers comparable impact toughness and temperature resistance, but is slightly softer. |
Polyamides (Nylons) | Wide range of properties depending on specific polyamide (PA6, PA66, PA11, PA12, PA46).Unfilled grades have excellent toughness and stiffness, but can be prone to water uptake.Filled grades offer excellent strength, temperature resistance and chemical resistance. | RPU 130 is a good alternative to unfilled grades of Nylon due to acombination of temperature resistance, ductility and abrasion resistance. EPX 82 and EPX 150 are good alternatives to filled grades of Nylondue to a combination of high stiffness, temperature resistance andfunctional toughness. EPX 86FR offers similar performance and is UL 94 V0 Blue Card certified. |
Polycarbonate | Often used for its clarity and combination of strength, impact resistance and temperature resistance. | Loctite IND 405 Clear is a clear resin with functional toughness. EPX 82 and EPX 150 are good choices if stiffness and temperature resistance are most important. RPU 130 offers the best combination of high impact toughness and temperature resistance. |
PMMA | Great aesthetics, good optical properties, high gloss, scratch resistant. Poor chemical resistance and can be brittle. | Loctite IND 405 Clear is a clear material with functional toughness. RPU 70 and Loctite 3843 offer good stiffness, aesthetics and ease-of-use, but are only available in black. |
POM | Stiff and relatively tough, POM is known for its good lubricity, low creep and excellent fatigue properties. | RPU 130 offers best-in-class abrasion resistance for an additive material but is softer and less lubricious than POM.RPU 70, UMA 90, Loctite 3843 or IND 405 Clear can be good options if abrasion and temperature resistance are not as crucial. |
PBT | Notable for excellent electrical properties. Unfilled grades are tough and rigid, and filled grades add strength and temperature resistance. | EPX 150 is the best option for glass-filled PBT replacement, offering a similar combination of strength, temperature resistance, electrical properties, and functional toughness. EPX 82 is suitable for use cases up to 105°C. EPX 86FR offers similar performance and is UL 94 V0 Blue Cardcertified. |
Polypropylene | Commonly used for low cost, excellent acid/ base resistance and flexible, snappy properties, with moderate temperature resistance. Filled grades (talc, mineral, or glass) add increased temperature resistance and stiffness while sacrificing toughness. | RPU 130 or FPU 50 offer flexible, snappy properties. RPU 130 is stiffer, and FPU 50 is better for living hinges. EPX 82 is a good option for replacement of filled grades. Loctite IND 405 Clear offers good toughness and moderatetemperature resistance. |
High-Performance Thermoplastics (PEEK, PEI, PSU) | Generally, these thermoplastics have exceptional temperature and chemical resistance, exhibit high stiffness and toughness, and are commonly available in flame retardant grades. | CE 221 and Loctite IND 147 Black offer the high temperature and chemical resistance, but can be more brittle than these offerings. EPX 150 offers a combination of high temperature and chemical resistance with sufficient toughness and the ability to be steam sterilized. EPX 82 offers a strong balance of temperature resistance, strength and toughness. EPX 86FR offers similar performance and is UL 94 V0 Blue Card certified. RPU 130 can be an option if stiffness is not the most important criteria. |
Thermoplastic Polyurethane Elastomers (TPUs) | TPU elastomers can offer a broad range of properties, with varied durometer and resilience. They typically offer excellent tear strength, abrasion resistance, and chemical resistance. | Carbon has a variety of polyurethane-based elastomers that areexcellent matches for commercial TPU products: EPU 40 is a 68A durometer elastomer with moderate resilience. EPU 41 is a 73A durometer elastomer with high resilience. EPU 43 is a 76A durometer elastomer with good damping. EPU 44 is a 77A durometer elastomer with high resilience, suitable for industrial production workflows. EPU 45 is a 77A durometer elastomer with excellent damping. EPU 46 is a 78A durometer elastomer with excellent return and a full spectrum of colors. |
Carbon DLS as a Substitute for Injection Molded Parts
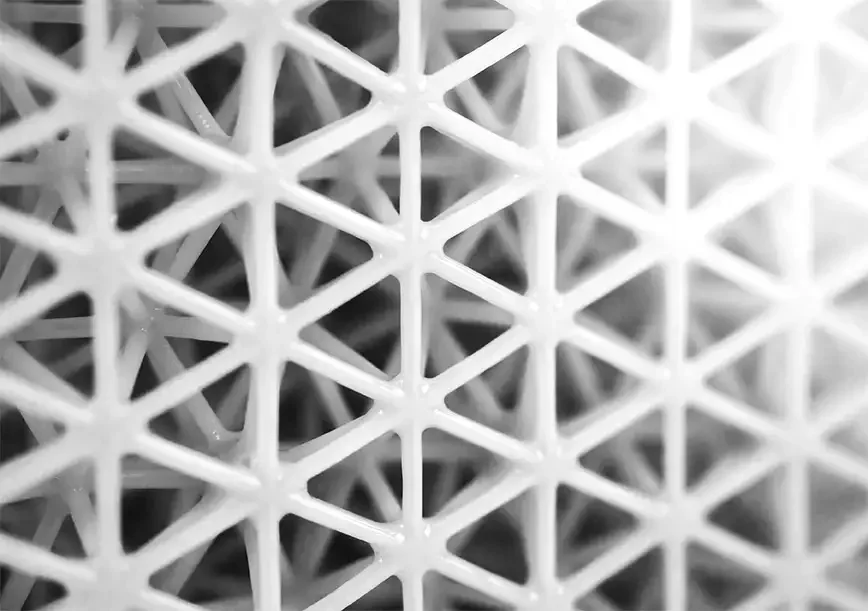
Carbon DLS has a wide array of possible use cases. It’s often used for prototyping and end-use production, making it suitable for various industries, including automotive, aerospace, healthcare, and consumer goods. Another interesting use case for Carbon DLS is as a substitute for injection molded parts.
In fact, for medium-level quantities (below mass-production or around 20-500 parts), Carbon DLS offers the following advantages over injection molding:
- No tooling costs upfront; maximize your cash flow by reducing capital expenditures
- Ability to print complex geometries which are often problematic when utilizing injection molding, such as undercuts and walls without draft angles
- Higher repeatability and homogeneity
To learn more about Fictiv’s 3D printing solutions, visit the company’s website.
About Fictiv
Fictiv is the operating system (OS) for custom manufacturing that makes it faster, easier, and more efficient to source and supply mechanical parts. Its intelligent OS, supported by best-in-class operations talent, orchestrates a network of highly vetted and managed partners around the globe for fast, high-quality manufacturing, from quote to delivery. To date, Fictiv has manufactured more than 25 million parts for early-stage companies and large enterprises, helping them innovate with agility and get products to market faster.