Time to read: 7 min
Injection molding is a fundamental manufacturing process that allows for precise and efficient production of plastic parts. In high-volume manufacturing, multi-cavity molds play a crucial role in meeting the demands of mass production while maintaining both product quality and cost-effectiveness. By enabling the production of multiple parts in a single molding cycle, multi-cavity molds have significantly transformed various industries, including automotive, healthcare, consumer goods, and consumer electronics.
This article explores the benefits and considerations of multi-cavity injection molding, offering insights into its applications and Fictiv’s expertise in the field.
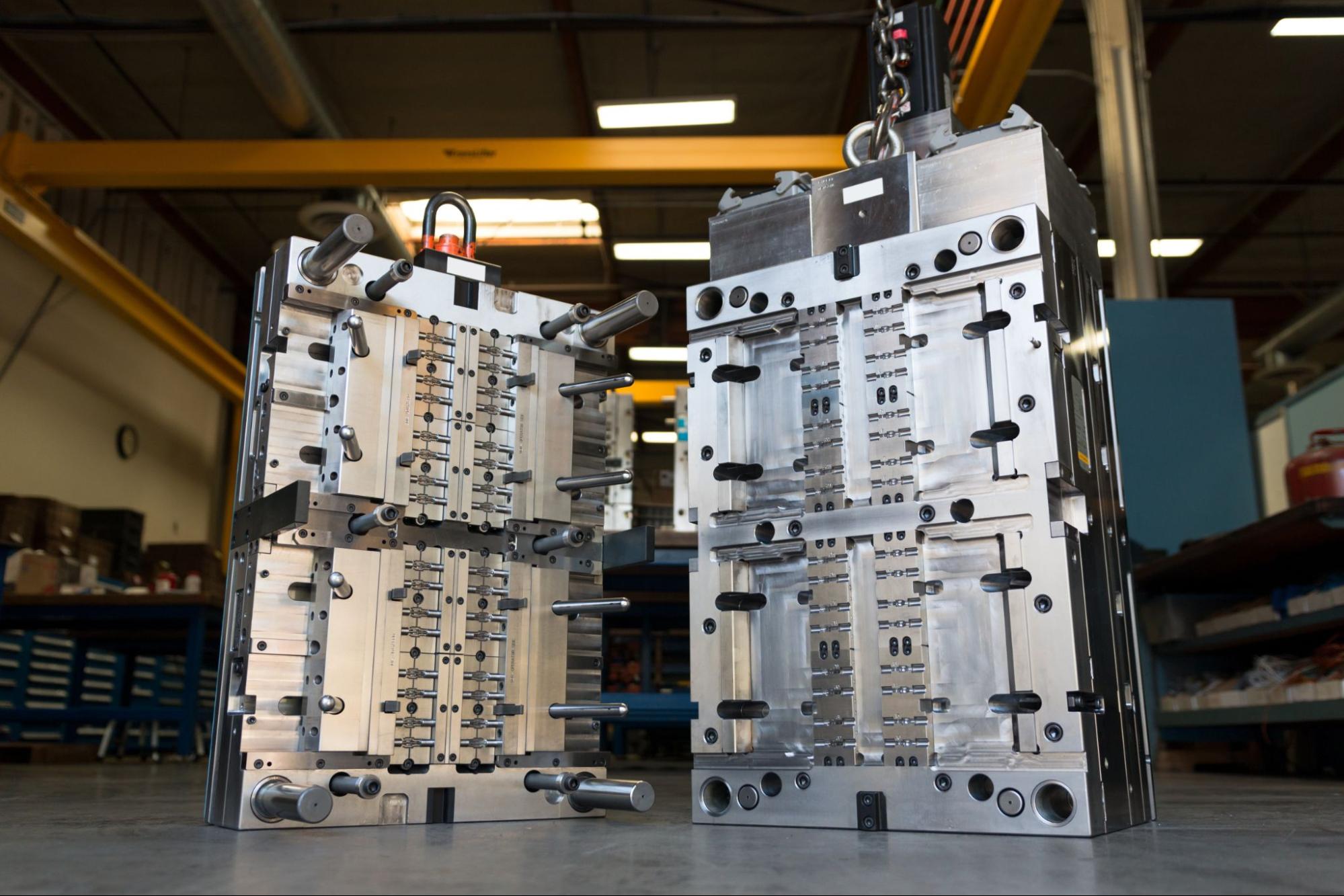
What Are Multi-Cavity Molds?
Multi-cavity molds are tools designed with multiple cavities within a single mold structure, allowing for the simultaneous production of several components in one injection cycle. In contrast, single-cavity molds can produce only one part per cycle. Multi-cavity molds are commonly used for high-volume production operations in which efficiency, consistency, and scalability are crucial. For example, a mold with eight cavities produces eight parts per cycle, significantly accelerating production timelines compared to single-cavity molds. The design and construction of multi-cavity molds involve precise engineering to ensure uniform part quality across all cavities. Factors such as cavity layout, cooling channels, and runner systems must be carefully optimized to achieve consistent results.
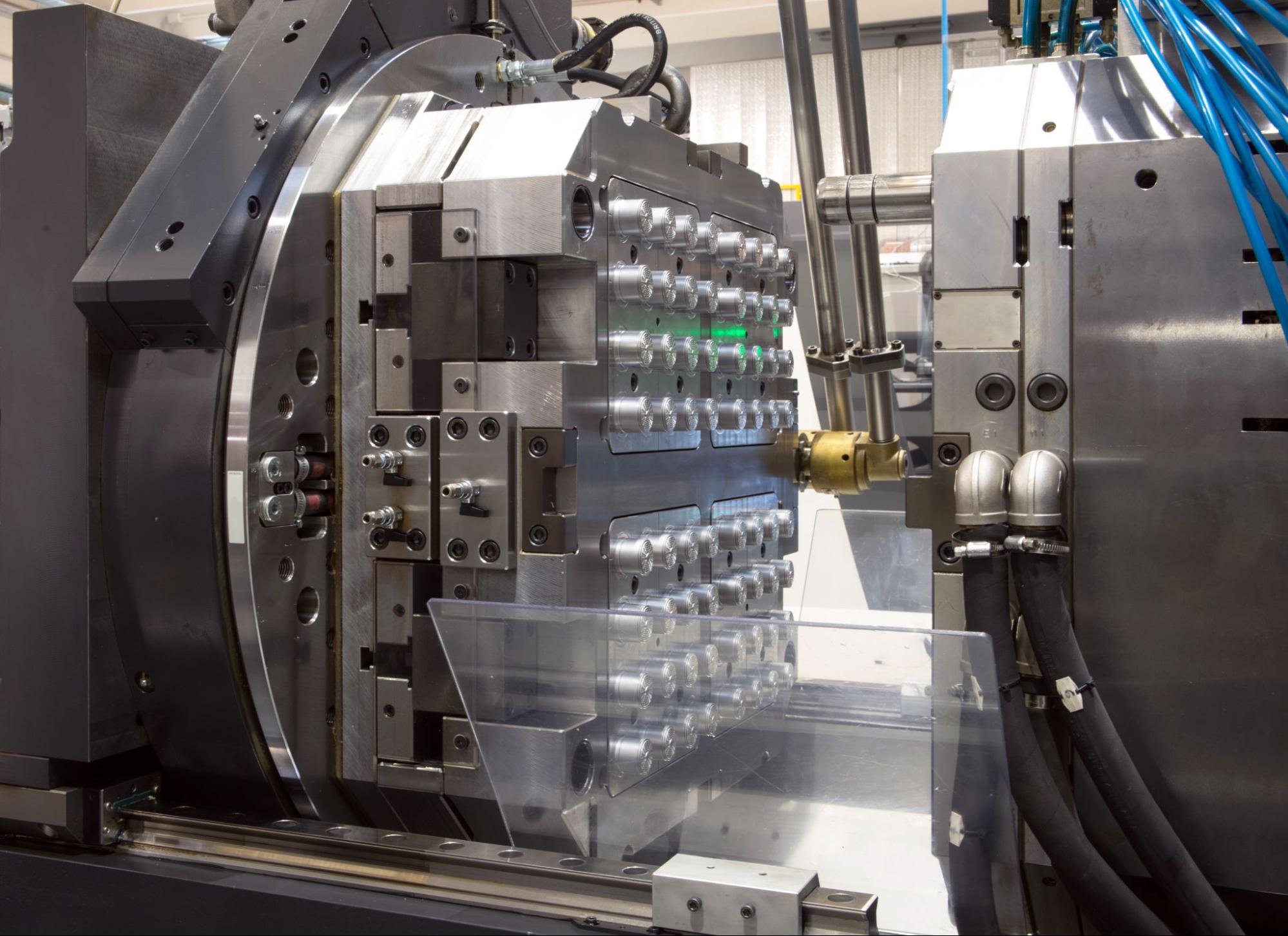
Benefits of Multi-Cavity Injection Molding
Multi-cavity injection molding offers a range of benefits that make it an attractive solution for high-volume production:
- Increased Production Speed: With multiple cavities, manufacturers can produce a higher quantity of parts in a shorter time frame to meet tight deadlines efficiently. This helps to accelerate new product development into full-scale production.
- Cost-Effectiveness: By consolidating production into fewer cycles, multi-cavity molds reduce machine operation time, labor costs, and energy consumption. This reassures manufacturers about the soundness of their investment in multi-cavity molds.
- Consistency: Advanced mold design that accounts for balanced filling of cavities by intricate runner systems and cooling channels ensures uniformity across all parts produced, minimizing the risk of defects.
- Scalability: Multi-cavity molds allow manufacturers to scale operations to seamlessly meet growing demand without significant changes to their production setup.
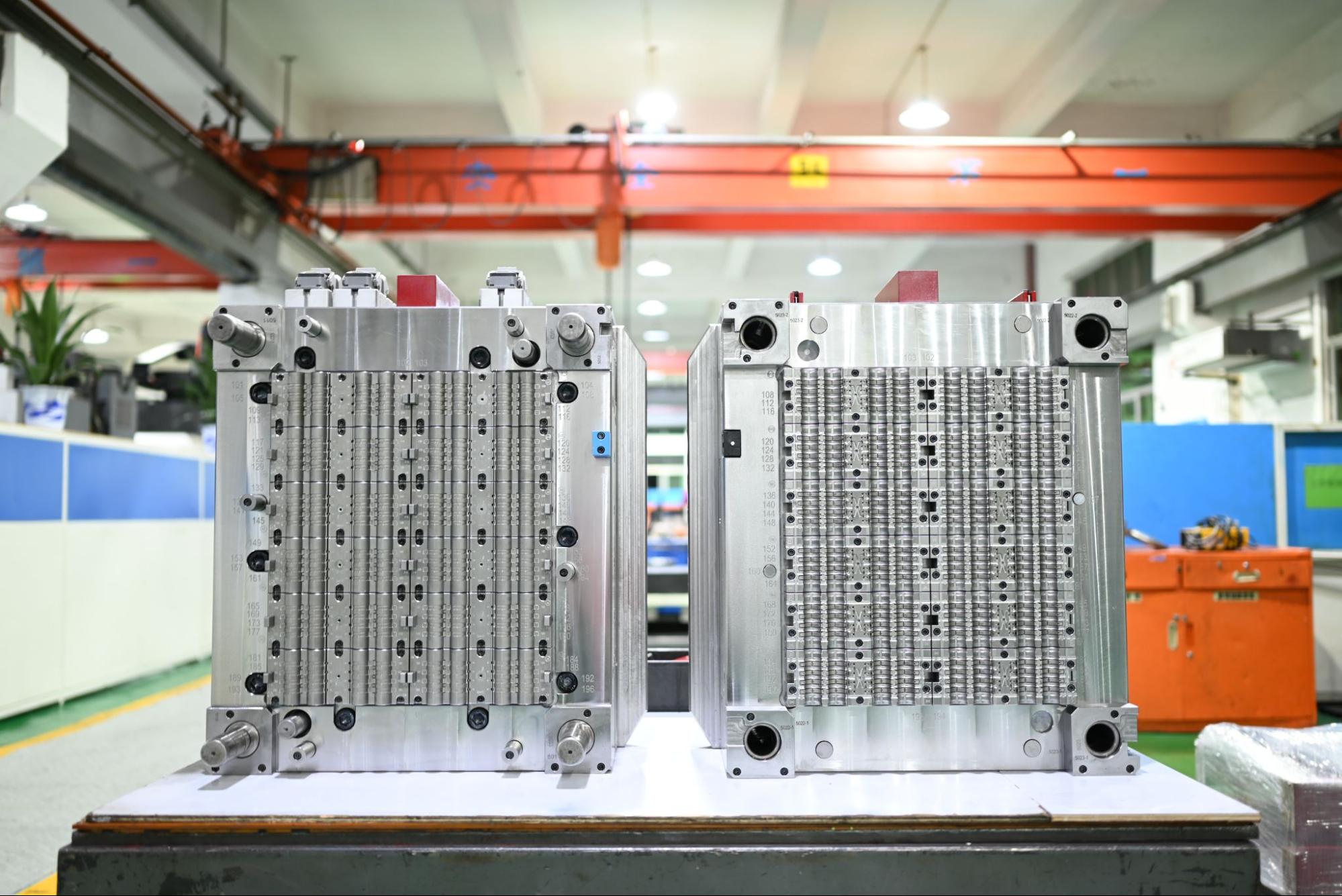
Ready to scale your injection molding? Fictiv provides seamless support from prototyping to full-scale production, offering flexibility, expert guidance, and high-quality results at every stage. Get a quote today and accelerate your manufacturing with precision and efficiency.
Enhancing Efficiency With Multi-Cavity Molds
Efficiency is a key advantage of multi-cavity injection molding since it streamlines the manufacturing process in several ways. Some of the methods by which multi-cavity molds accomplish this are:
Optimized Cycle Times
Producing multiple parts simultaneously reduces the overall cycle time for large production runs. The difference in production time between a single-cavity mold and a multi-cavity mold is staggering. For a 1000-piece order, a single-cavity mold will take 1000 cycles to complete the order, while a 10-cavity multi-cavity mold will only take 100 cycles.
Reduced Downtime
Downtime is often attributed to necessary tasks like mold changes, maintenance, and calibration. With fewer cycles needed to achieve the same output, machine downtime is minimized, and manufacturers can also significantly minimize such interruptions in production. This not only improves operational productivity but also allows companies to remain competitive in the market.
Adaptability Across Industries
Industries such as medical devices, packaging, and consumer electronics benefit from the efficiency of multi-cavity molds. For instance, in the medical device manufacturing industry, the ability to mold multiple products such as syringes, test tubes, or caps ensures quick turnaround times while still meeting industry standards. Similarly, in the consumer electronics industry, products like buttons and casings can be produced by the hundreds in a single cycle.
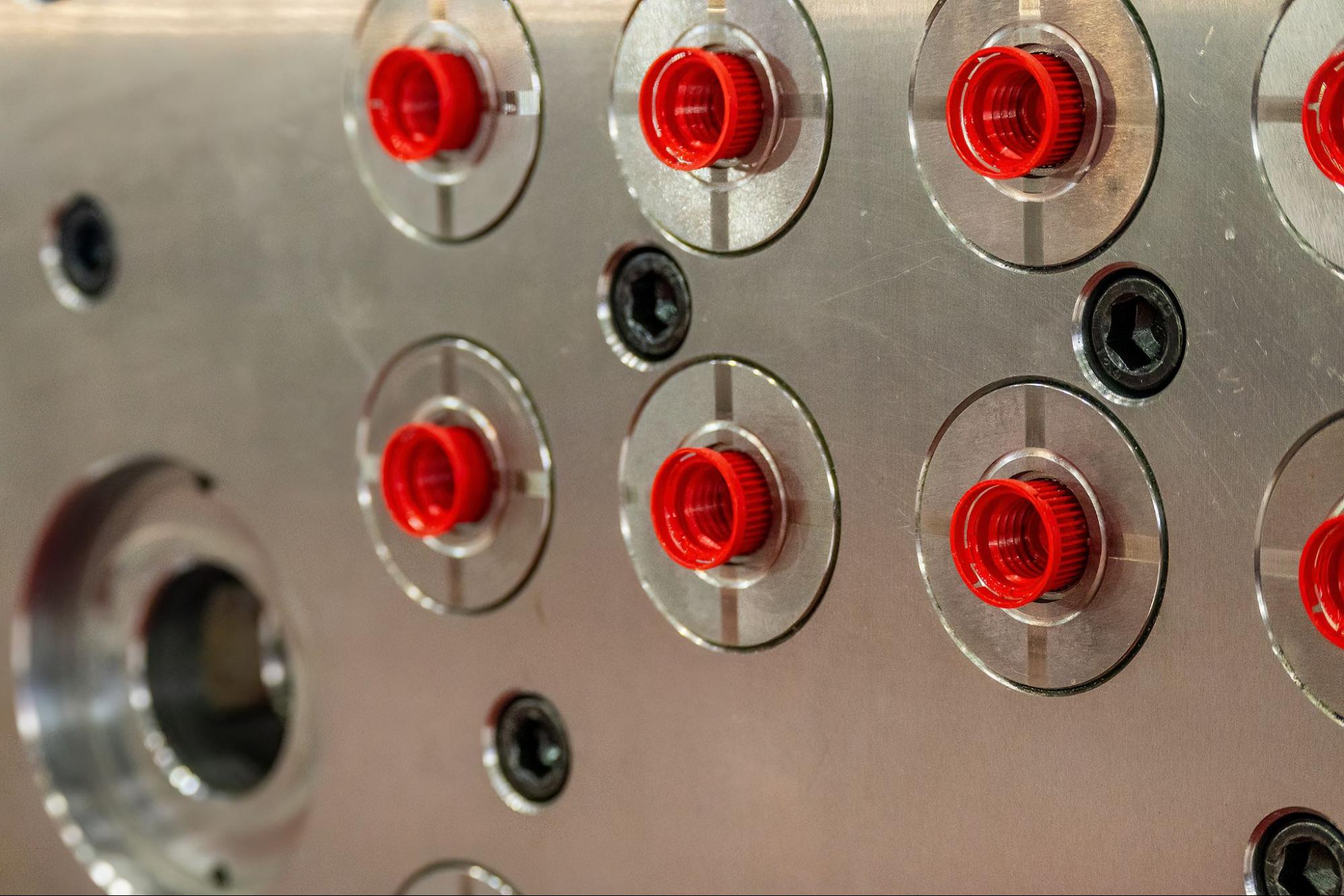
Reducing Costs With Multi-Cavity Molds
Cost reduction is a significant motivator for adopting multi-cavity molds. Here are some reasons why they lower production costs:
Material Savings
Efficient material usage and reduced waste contribute to overall cost savings. This can primarily be attributed to well-optimized runner systems and gating mechanisms that minimize the amount of scrap material generated.
Lower Price Per Part
The ability to produce more parts in each cycle decreases the cost per unit, which makes large-scale manufacturing more economical. Fixed costs like mold setup, machine operation, and labor are distributed across a larger number of parts, which allows manufacturers to maintain competitive pricing in the market.
Energy Efficiency
Energy consumption is a major consideration in injection molding, as the process involves the use of injection molding machines, heaters, cooling systems, and sometimes automated sorting and packing machines. With multi-cavity molds, a 1,000-part order may take 100 injection cycles to complete if there are 10 cavities, versus a single-cavity mold, which will take 1,000 cycles. With fewer molding cycles required, energy consumption per batch is reduced, which lowers overall utility expenses.
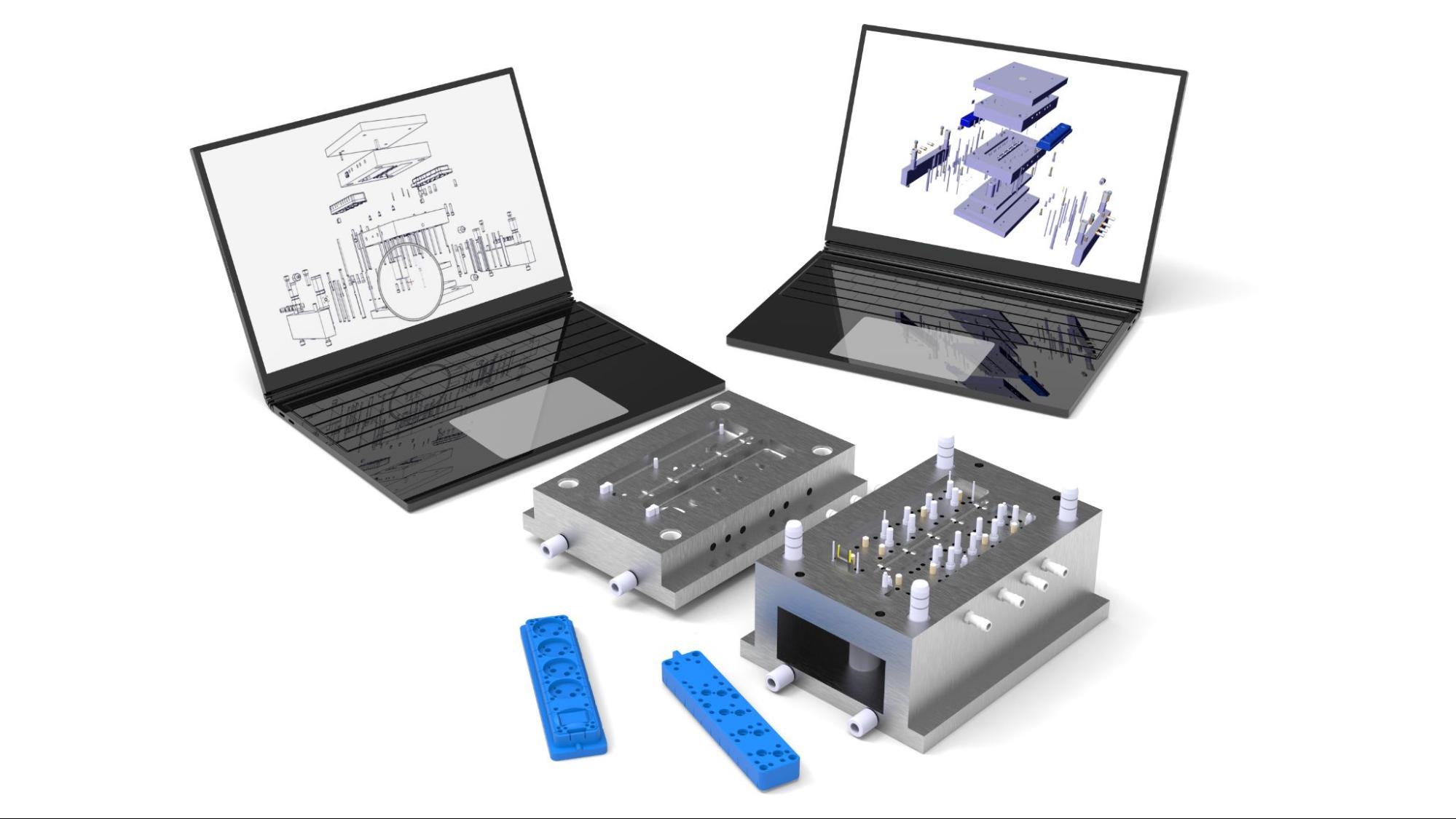
Challenges and Mold Design Considerations
There are many important tooling considerations to take into account when determining your production strategy. While multi-cavity molds offer numerous benefits, they also present unique challenges, including:
Design Complexity
Engineering a mold with multiple cavities requires precision to ensure uniformity in part quality. Each cavity in the mold must be identical, as even minor deviations in cavity dimensions, gate design, or cooling systems can result in inconsistencies across parts, leading to defects and increased rejection rates.
Higher Initial Costs
The upfront cost of designing and manufacturing multi-cavity molds can be higher than that of single-cavity molds. This price difference is primarily due to the mold material and additional engineering costs. High-quality materials like hardened steel are used to ensure tooling meets the demands of high-volume production, and engineering costs are often higher due to the increased complexity of multi-cavity mold design.
Tooling Maintenance
More complex molds require regular maintenance to prevent wear and tear from affecting performance. To mitigate these issues, regular inspections and preventive maintenance are essential. Manufacturers may implement cleaning and tooling inspection schedules and replace components as needed to prolong mold life and ensure consistent performance.
Material Flow
Ensuring even material distribution across all cavities is essential to preventing defects like short shots or warping, and it’s crucial to design and optimize the runner system precisely to achieve uniform material flow. Balancing pressure and temperature across all cavities guarantees that each one fills completely and uniformly. Simulation tools like mold flow analysis are often utilized to analyze material behavior and refine mold design before production starts.
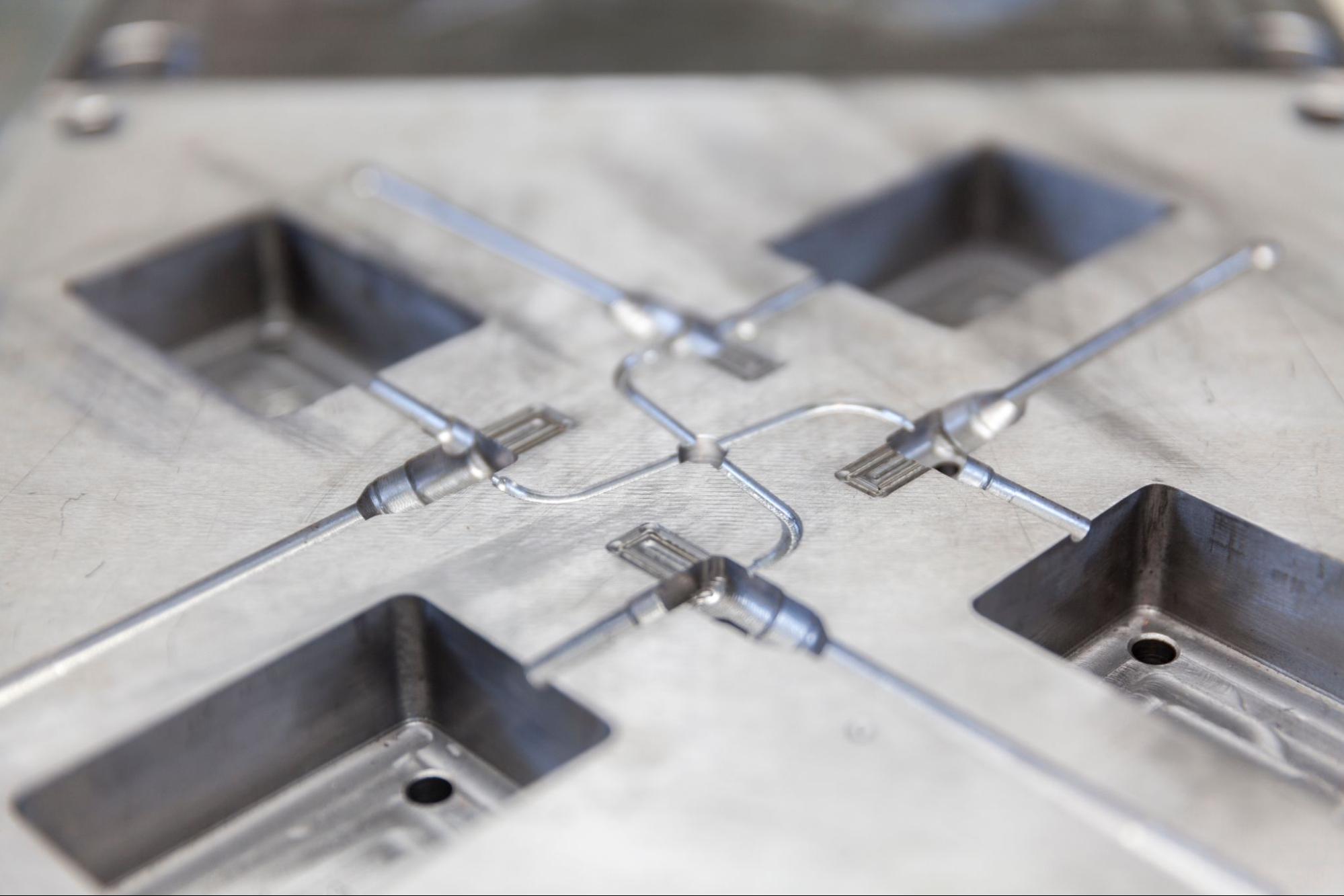
Family Tooling vs. Multi-Cavity Molds: What’s the Difference?
Family tooling is another injection molding approach in which a single mold contains cavities for different parts that may be similar in size or shape. This differs from multi-cavity molds, which produce identical parts in each cycle. One primary advantage of family tools is that they help manufacture multiple components of product assemblies in one cycle without multiple molds. A good example is two half-shells of an enclosure that can be assembled together.
While multi-cavity molds are best for high-volume production of identical parts, family tooling is ideal for smaller production runs or when multiple component types are needed simultaneously. Manufacturers must evaluate production goals, volume requirements, and part complexity to decide between these options.
Choosing the Right Molding Solution
Multi-Cavity Mold | Higher volumes of identical parts |
Family Mold | Different parts of similar size/shape |
Single-Cavity Mold | Low volumes or prototype parts |
Table 1: Recommended Applications for Various Injection Mold Types
Selecting the best molding solution depends on multiple factors, including production volume, part complexity, and budget. Here are some guidelines:
High-Volume Production
Multi-cavity molds are the optimal choice when the goal is to produce a large number of identical parts. These molds are specifically designed to maximize efficiency by producing multiple identical parts in a single cycle to reduce the overall cost per part, accelerate production, and ensure consistent product quality.
Diverse Part Production
Family tooling is a practical solution for projects requiring the production of multiple different parts. Family molds include multiple cavities for parts of a similar size or shape, allowing the simultaneous production of components that may later be assembled into a complete product.
Low-Volume Needs
Single-cavity molds are often sufficient for prototypes, low-volume production runs, or projects requiring specialized parts. These molds are simpler and more cost-effective to design and manufacture compared to multi-cavity or family molds.
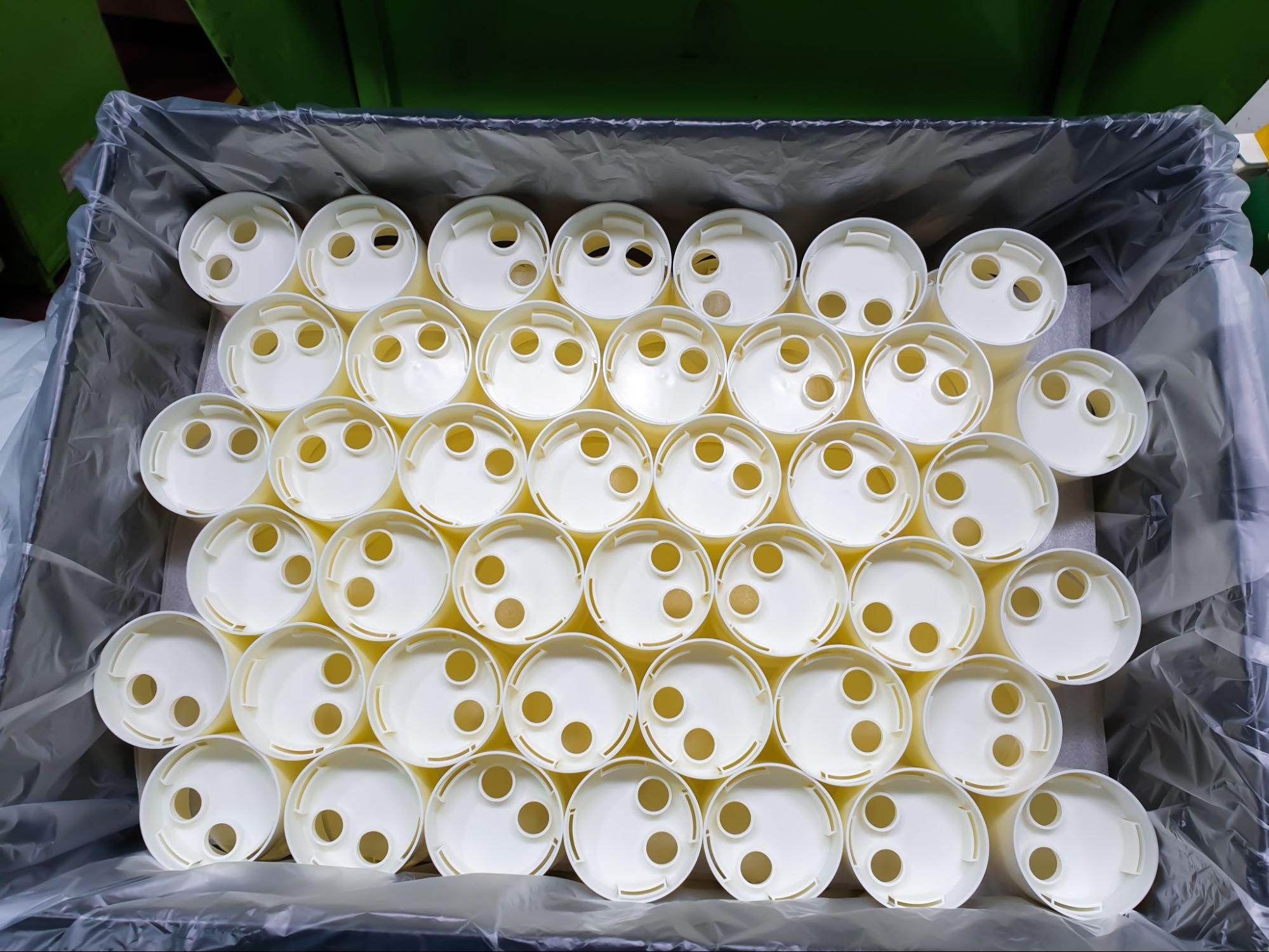
Fictiv’s Multi-Cavity Molding Services
Fictiv simplifies the complexity of multi-cavity injection molding, delivering high-quality tooling solutions with exceptional speed and efficiency by leveraging expertise within a global network to support clients’ manufacturing goals. Key features of Fictiv’s services include:
- Custom Design: Tailored mold designs to meet unique production requirements. Fictiv uses advanced technology like CAD and simulation software to ensure optimized material flow and cooling.
- Rapid Turnaround: Fictiv’s efficient workflow from initial design consultation to final mold delivery minimizes lead times. Additionally, advanced technology and prototyping capability help clients validate designs quickly and reduce the risks of delays.
- Material Options: Fictiv offers a wide range of advanced material choices to suit various applications. Fictiv ensures the right match for every application, from flexible materials to rigid thermoplastics.
- Expert Support: Fictiv’s team is composed of experienced engineers and professionals who provide guidance from cradle to grave on any project. The team not only offers technical expertise but also gives clients insights into their production strategies and how to align their manufacturing operations with their goals.
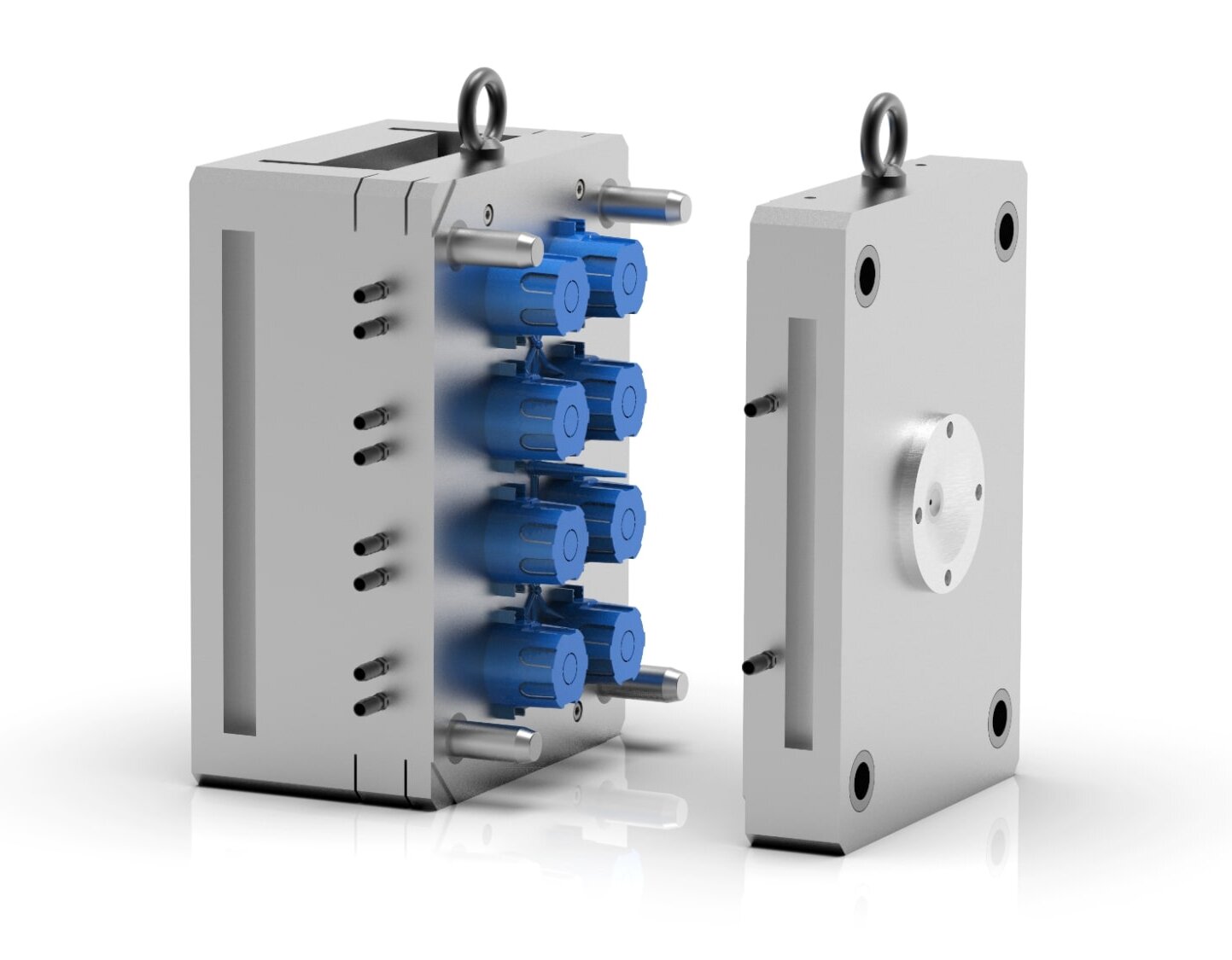
Scaling Up Injection Molding Production With Fictiv
At Fictiv, we specialize in delivering tailored, high-performance multi-cavity molding solutions to meet the unique demands of your production. Whether you’re scaling up from prototype to injection molding, increasing volumes for production, creating complex components, or looking for expert guidance on material selection and design optimization, Fictiv is here to support your success.
Fictiv’s AI-powered platform, global network of vetted manufacturers, and expert engineering support ensure you get high-quality, production-ready parts—on time and to spec. Get an instant quote today to discuss your project and see how Fictiv can help you streamline production, reduce costs, and accelerate time to market.