Time to read: 6 min
Stereolithography (SLA), the technology used to produce them, supports the creation of plastic parts with tight tolerances, intricate geometries, and smooth surface finishes. And parts printed using SLA stand out because of their exceptional accuracy, resolution, and level of detail. One key advantage of SLA is its ability to achieve finishes that are both highly polished and refined. After 3D printing is complete, SLA parts can undergo additional polishing and, if necessary, decorative painting or protective plating.
Over the years, SLA 3D printers have become increasingly sophisticated and the number of materials that they can use has grown. Today, there are many material options available, each with their own properties and applications. This article explores the different types of materials used in SLA 3D printing, their characteristics, and some applications for these high-quality 3D printed parts.
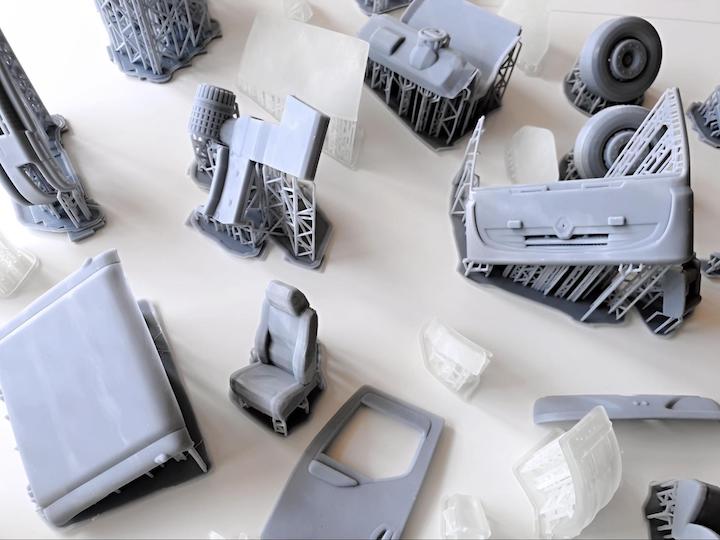
What Is Stereolithography (SLA) 3D Printing?
Stereolithography, or resin 3D printing, is a form of additive manufacturing. More specifically, SLA is a vat photopolymerization technology. With vat polymerization, a light source such as a laser or projector solidifies liquid resin into solid plastic structures a layer at a time. The core concept among various vat photopolymerization technologies remains the same, but there are differences in core components such as the light source, build platform, and resin tank.

SLA resins undergo a process called polymerization when exposed to specific wavelengths of light. During polymerization, the individual monomers and oligomers within the plastic resin form chemical bonds. As a result, the material solidifies into rigid or flexible geometries, depending on the specific resin.
SLA printing was one of the first 3D printing technologies and remains widely used today. Because it produces high-resolution parts with smooth surface finishes, SLA is suitable for creating prototypes that are both intricate and detailed. This form of additive manufacturing is used in industries where precision and accuracy are important, such as product design, dentistry, and jewelry making.
Materials Used for SLA 3D Printing
SLA 3D printing materials can be grouped into four categories:
- Standard SLA resins
- Engineering SLA resins
- Castable resins
- Dental and medical SLA resins
Standard SLA Resins
Standard SLA resins are cost-effective materials that produce rigid, high-quality parts with a smooth surface finish, which makes them a popular choice for rapid prototyping. Standard resins also have unique relationships between color and properties. For example, white resin is well-suited for parts requiring a sleek surface finish, while gray resin is better suited for parts with intricate features. Standard SLA resins include Plastic Accura® Xtreme™ and Accura® Xtreme™ 200.
Clear resins are also available that are versatile and achieve near-transparency after post-processing. Like other types of standard SLA resins, clear resin exhibits favorable mechanical properties, making it an excellent choice for producing rapid prototypes with intricate details. Clear resins, like Accura® 60, also deliver smooth surface finishes to enhance the overall aesthetic appeal of 3D printed parts.
Engineering SLA Resins
Engineering SLA resins are specifically designed for parts and prototypes that closely resemble injection-molded plastic parts. Note, however, that engineering SLA resins require post-curing under ultraviolet (UV) light to achieve their optimal mechanical properties.
Examples of engineering SLA resins include:
- Tough Resin: Ideal for applications that involve high levels of stress and applied force. Tough resin parts exhibit an impressive tensile strength of 55.7 MPa and a modulus of elasticity of 2.7 GPa. Additionally, tough resins are shatter-resistant, making them well-suited for snap-fit joint enclosures or rugged prototypes. Applications also include mechanical assemblies and functional prototypes.
- Durable Resin: These materials excel in terms of wear resistance and flexibility. They also offer smooth surface finishes, making them a great choice for the rapid prototyping of consumer products, low-friction moving parts, and ball joints.
- Heat Resistant Resin: Recommended for applications that require high thermal stability and the ability to withstand elevated temperatures. With heat deflection temperatures (HDTs) ranging between 200 to 300°C, these resins are suitable for casting, heat-resistant fixtures, hot fluid flow equipment, mold prototypes, and thermoforming tooling.
- Rubber-like/Flexible Resin: These flexible, tactile materials provide engineers with the ability to replicate the properties of soft rubber parts. With their low tensile modulus and high elongation at break, they are ideal for applications that involve bending or compression.
- Rigid Ceramic-Filled Resin: These resins are reinforced with ceramic particles, typically glass, to achieve high rigidity and smooth surfaces. They also provide thermal stability, heat resistance, and resistance to deformation over time. Rigid, ceramic-filled resins are used in fixtures, housings for automotive and electrical components, jigs, manifolds, molds, and tooling.
Castable Resins (Jewelry Resins)
Castable resins are highly versatile materials designed specifically for 3D printing applications in the jewelry industry. This type of resin can create intricate details and smooth surface finishes, meeting the high standards required in jewelry manufacturing. One notable advantage of castable resins is their ability to burn-out cleanly during the casting process, leaving no residue behind — this ensures that the final casted jewelry pieces are blemish-free.
Dental and Medical SLA Resins
Dental and medical SLA resins are divided into two sub-categories: Class I biocompatible and Class IIa biocompatible.
Class I (custom medical appliances resin) resins are used in the production of custom medical equipment such as surgical guides. Because SLA parts created with Class I biocompatible resins can withstand sterilization through autoclaving, they can be used safely in operating rooms. Class I resins also offer high precision and smooth surface finishes, making them ideal for medical applications where accuracy and quality are paramount.
Class IIa (dental long-term biocompatible resin) resins are formulated for orthodontic and long-term dental applications. These materials are designed to be in contact with the human body for up to one year. They also exhibit excellent resistance to fracturing, making them ideal for use in orthodontic retainers and other dental appliances that require long-term durability and biocompatibility.
Comparing Different SLA Printing Materials
The basic mechanical properties of some of the most common SLA materials are listed below:
Standard and Clear | Tough | Durable | Heat Resistant | Ceramic Reinforced | |
Tensile strength (MPa) | 65.0 | 55.7 | 31.8 | 51.1 | 75.2 |
Tensile Modulus (GPa) | 2.80 | 2.80 | 1.26 | 3.60 | 4.10 |
Elongation at break (%) | 6.2 | 24.0 | 49.0 | 2.0 | 5.6 |
Flexural Modulus (GPa) | 2.20 | 1.60 | 0.82 | 3.30 | 3.70 |
IZOD impact strength (J/m) | 25 | 38 | 109 | 14 | N/A |
HDT @ 0.45 MPa (oC) | 73 | 48 | 43 | 289 | 88 |
To improve material properties, metal plating is often used. This supplementary procedure applies a thin layer of copper-nickel coating to enhance the appearance, texture, and strength of an SLA part, without adding significant weight. Metal plating gives SLA plastic parts improved strength, durability, stiffness, wear resistance, and temperature resistance. Plus, in terms of aesthetics, the finished parts exhibit a striking resemblance to aluminum components.
SLA 3D Printing Applications
Different SLA printing materials have different applications in a variety of industries, as shown below:
Materials | Features and Advantages | Disadvantages | Applications |
Clear Resin | Near optical transparency. | Limited mechanical properties. | Millifluidics, parts that require optical transparency. |
Standard Resin | High-resolution parts.Smooth, matte surface finish | Limited mechanical properties and applications. | Concept models,prototypes. |
Tough and Durable Resins | High stiffness.Robust, strong, and dynamic.Can withstand compression, stretching, bending, and impacts without breakage.Materials with properties similar to PE or ABS.High wear resistance. | Not suitable for thin-walled parts (recommended minimum wall thickness of 1 mm) due to limited structural integrity. Exhibits a low heat deflection temperature, making it less suitable for applications requiring resistance to high temperatures. | Housings and enclosures,jigs and fixtures,connectors,Wear-and-tear prototypes. |
High Temp Resin | High heat deflection temperature.High precision.Smooth surface finish. | Brittle. Not suitable for parts with thin walls | Gas, hot air, and fluid flow,heat-resistant mounts, fixtures, and housings, inserts and molds. |
Flexible and Elastic Resins | Flexibility of rubber, TPU, or silicone. Ability to endure forces that cause it to bend, flex, or compress without breaking or deforming.High impact resistance. | Lacks the characteristics of genuine rubber, such as elasticity and resilience. Necessitates the use of substantial support structures during the printing process. Material properties deteriorate over time due to exposure to UV radiation, particularly sunlight. Inadequate for components with thin walls — recommended minimum wall thickness is 1 mm. | Special-effects props and models,compliant features for robotics,medical devices and anatomical models,prototyping of consumer goods. |
Medical and Dental Resins | Wide range of biocompatible resins for producing medical and dental appliances. | Limited to medical or dental applications | Dental and medical appliances, including surgical guides, dentures, and prostheses. |
Jewelry Resins | Easy to cast, with intricate details and strong shape retention | Limited applications | Try-on pieces,reusable molds, custom jewelry. |
Ceramic Resin | Stone-like finish.Can be heated in an oven or kiln to create a fully ceramic piece.Suitable for fine features. Stiffness. | Brittle.Low impact strength | Art and design, engineering research. |
Succeeding With SLA 3D Printing
SLA materials that are not plated or painted may undergo changes in appearance and mechanical properties when exposed to UV light and moisture over an extended period. This can lead to issues such as yellowing, part warpage, and brittleness. Therefore, SLA parts may not be appropriate for long-term use in some scenarios. Yet these 3D printed parts offer advantages in terms of their highly detailed form and fit during early prototyping stages.
Fictiv – Your SLA 3D Printing Partner
To get the best results for your project, it’s important to work closely with 3D printing experts who can help you select the right material and optimize the build orientation for your specific part application. Create your free Fictiv account to get started and request an SLA 3D printing quote today — we 3D print complex parts at ridiculous speeds!