Time to read: 7 min
Optimizing Injection Molding, Casting, Sheet Metal Fabrication, 3D Printing, and CNC Machining
Lean manufacturing, a proven methodology focused on continuous improvement and waste reduction, has significantly shaped modern industrial production. It prioritizes maximizing value for the customer while minimizing inefficiencies across both physical (materials and resources) and process (time and energy) aspects. With its widespread adoption, lean manufacturing remains a foundation of operational excellence for businesses aiming to stay competitive in today’s industrial society.
This article will further discuss what lean manufacturing is, how it is applied in various manufacturing processes, its role in digital manufacturing, and how it can be implemented.

What Is Lean Manufacturing?
Initially derived from the Toyota Production System, lean manufacturing is a production methodology that maximizes customer value through process improvements while minimizing waste and non-value-added practices. The core principles of lean manufacturing foster a culture of continuous improvement (or Kaizen, in Japanese). Some of the concepts are:
- Eliminating Waste (Muda): Identifying inefficiencies, such as overproduction, defects, waiting times, or underutilized resources, and systematically removing them.
- Continuous Improvement (Kaizen): Employees at all hierarchical levels actively refine strategies and improve processes daily.
- Just-in-Time (JIT) Production: JIT aims to minimize excessive inventories, which incur costs for production, storage, and retrieval. JIT focuses on maintaining only the materials that are immediately needed for fabrication and the products that are about to be sold.
- Standardized Workflows: Repeatable processes contribute to greater productivity and consistency.
- Quality at the Source: Empowers teams to detect and rectify production defects during manufacturing instead of post-production. This approach focuses on improving quality at each step rather than inspecting it at the end.
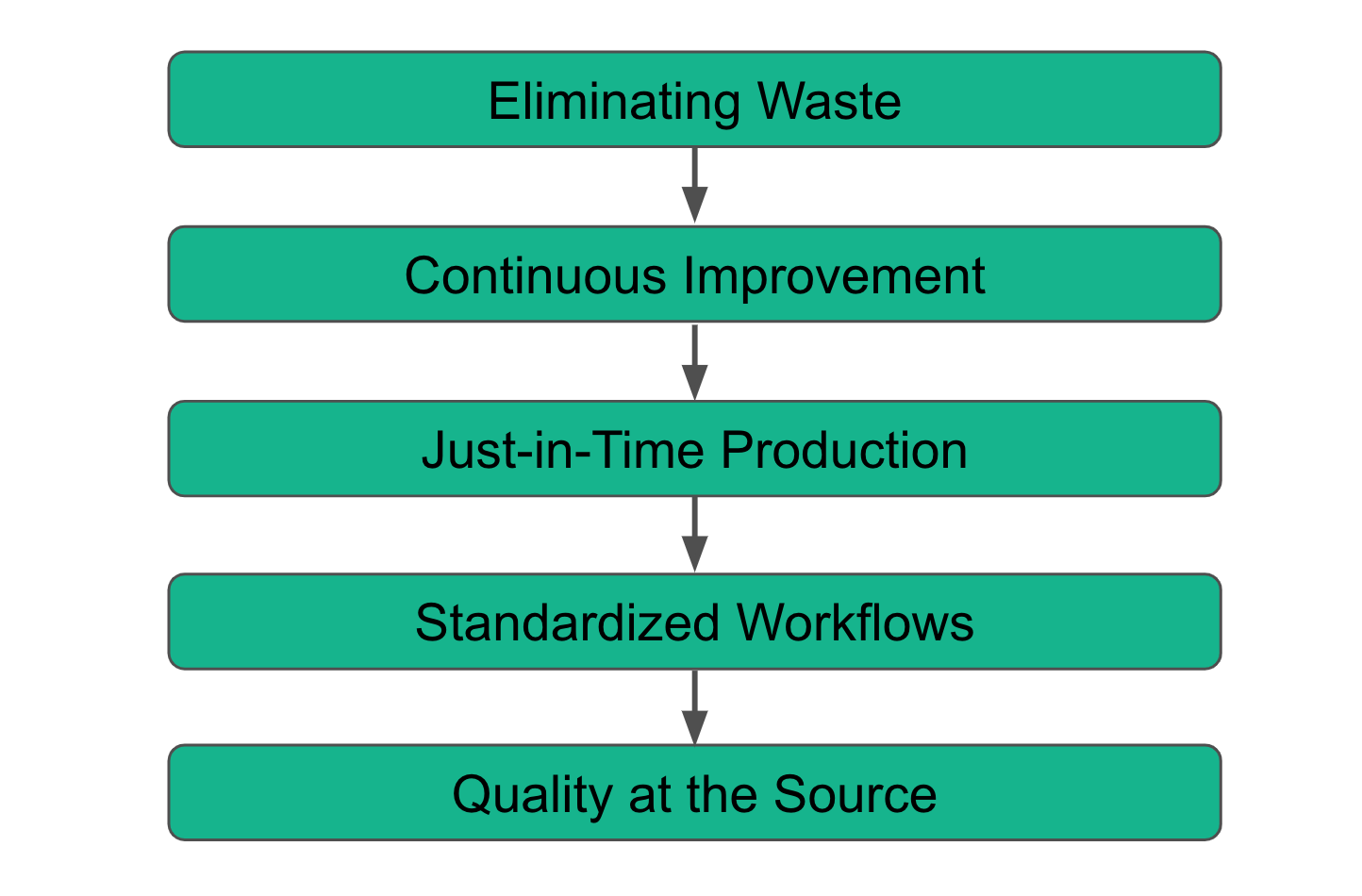
Lean manufacturing steps and techniques
Digital manufacturing platforms like Fictiv further enhance lean practices by enabling supply chain optimization, real-time collaboration, and on-demand production. These capabilities support just-in-time manufacturing, boosting agility and efficiency while minimizing waste.
Lean Manufacturing in Injection Molding
Injection molding is one of the most efficient mass production methods, but it faces several challenges that can reduce its cost-effectiveness and efficiency. These include tooling and setup lead times, material waste from defective parts, mold changeover inefficiencies, and poor production planning. Lean manufacturing offers targeted solutions to address these issues:
- DFM-Optimized Mold Design: Design for Manufacturability (DFM) ensures that molds are designed correctly from the start, minimizing defects and improving mold lifespan. By considering factors like mold flow and material properties during the design phase, manufacturers can reduce production errors.
- Automated Mold Changeovers: Single-minute exchange of dies (SMED) aims to reduce mold changeovers to under ten minutes by using automation and quick-change tooling systems, cutting downtime and increasing efficiency.
- Real-Time Quality Monitoring: Monitoring systems track parameters like temperature, pressure, and material flow during production, allowing for immediate defect correction and waste reduction.
Fictiv supports lean principles through on-demand injection molding, which eliminates the need for excess inventory and reduces storage costs. Its rapid prototyping and low-volume production capabilities enable quick design iterations, helping teams respond faster to changes and improve product development. Fictiv transforms injection molding into a more agile and cost-effective manufacturing process by minimizing waste and maximizing flexibility.
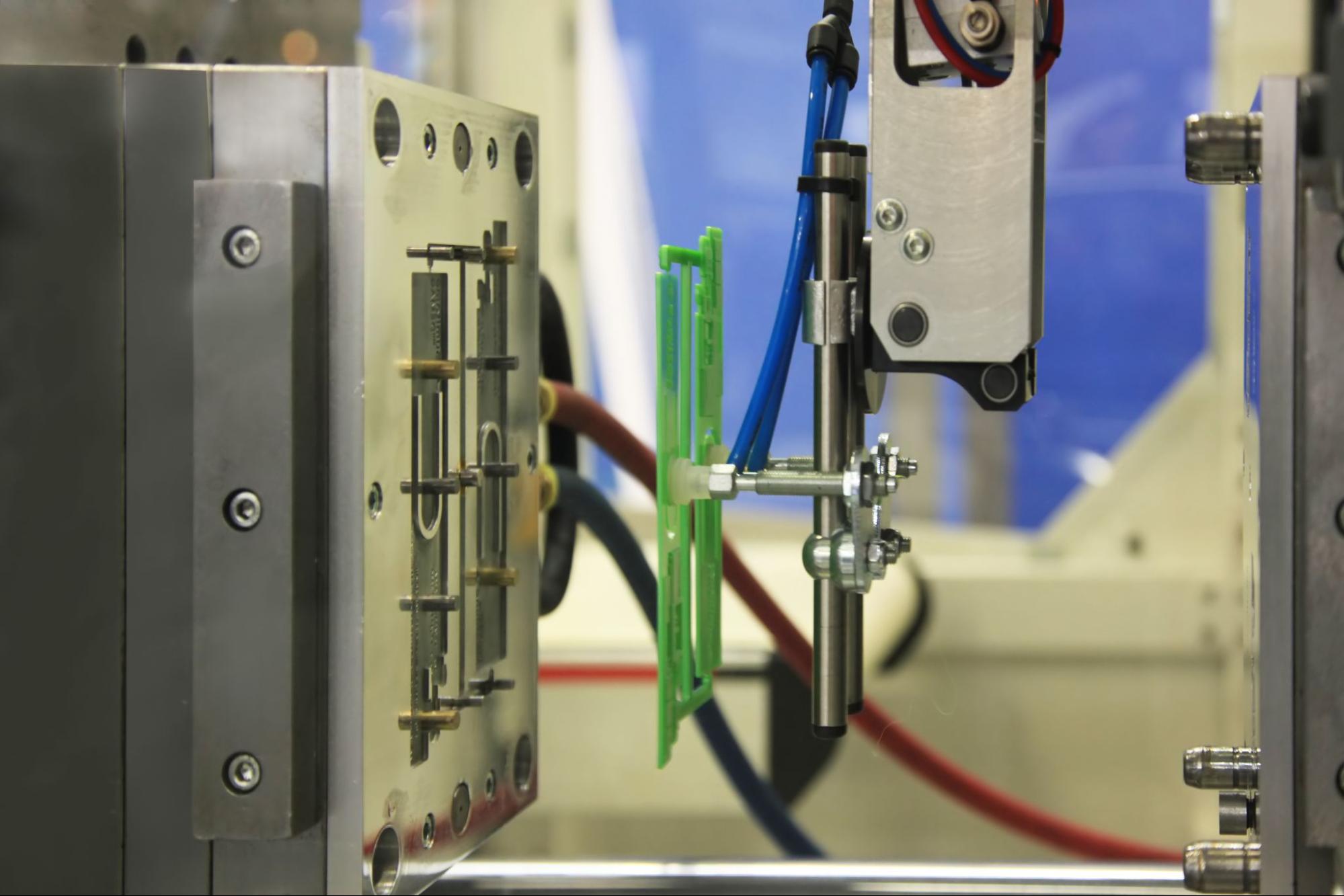
Lean Manufacturing in Casting (Die Casting, Urethane Casting, and Sand Casting)
The casting industry—including die casting, sand casting, and urethane casting—faces persistent challenges such as high scrap rates from defects, long tooling and mold fabrication lead times, and high energy consumption during production. Lean manufacturing offers targeted solutions to address these issues:
- Recycling Excess Material: Reprocessing scrap and defective parts reduces waste and lowers production costs.
- Optimized Gating and Venting Design: Well-designed gating and venting systems improve material flow and reduce defects like air traps and shrinkage.
- On-Demand Casting Production: Producing only what’s needed prevents overproduction and minimizes resource consumption.
- Energy-Efficient Equipment: Modern, energy-efficient machinery reduces power consumption without sacrificing output.
- Faster Tooling and Mold Fabrication: Lean practices like modular tooling and rapid prototyping shorten lead times and increase flexibility.
Fictiv enables lean casting by leveraging a global supply network to secure competitive pricing and reduce waste. Its automated quoting system and simplified production workflows cut down lead times and ensure faster, high-quality part delivery.
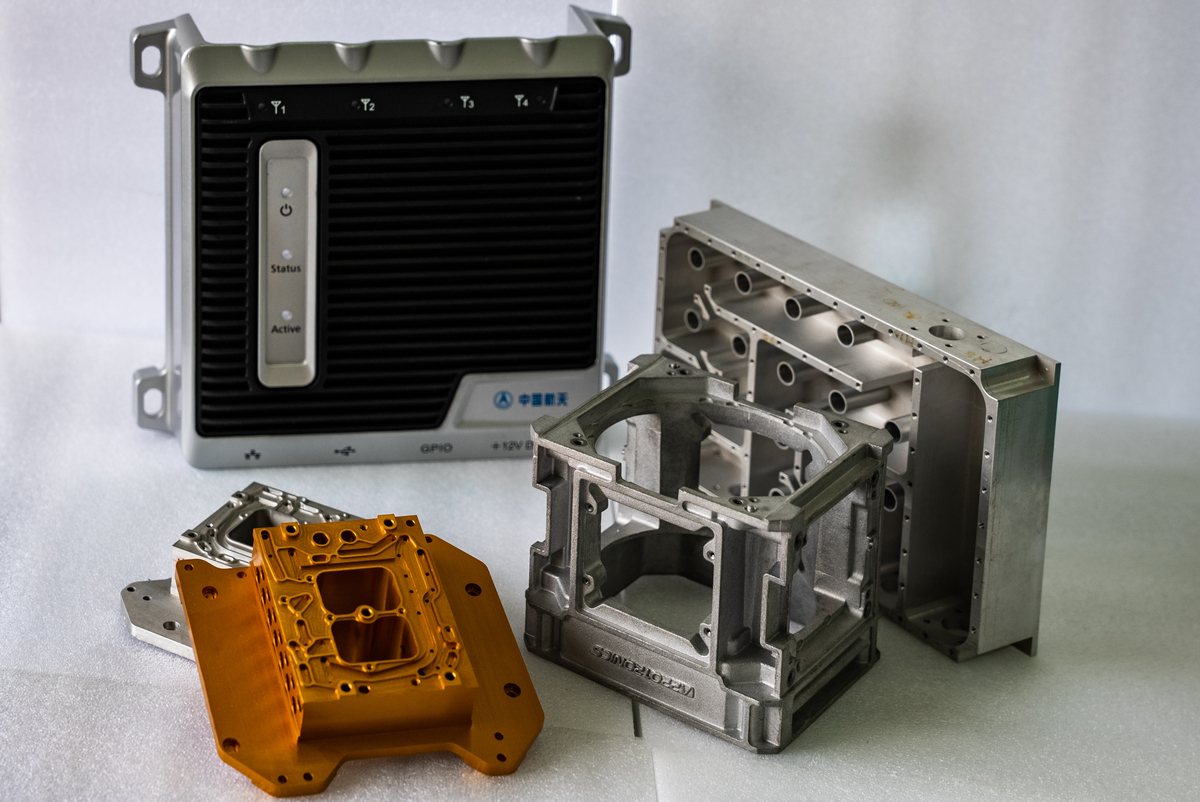
Lean Manufacturing in Sheet Metal Fabrication
Sheet metal fabrication is a complex manufacturing process. It is often plagued by excessive material waste from poor cutout arrangement and inefficient nesting, as well as production inefficiencies caused by over-reliance on batch production and lengthy setup times. Lean manufacturing offers targeted solutions to these challenges:
- Automated Cutting and Bending: Precision cutting and bending equipment reduce manual errors and minimize rework, speeding up production and improving accuracy.
- Optimized Nesting Algorithms: Advanced nesting software arranges cutouts efficiently on the sheet, maximizing material use and reducing waste.
- On-Demand Fabrication: JIT production minimizes overproduction and excess inventory, improving cash flow and reducing storage costs.
Fictiv enhances lean manufacturing by connecting manufacturers to a regional supplier network for competitive pricing and faster lead times. Its instant quoting and rapid fabrication streamline production, cutting delays and ensuring timely delivery of high-quality parts.
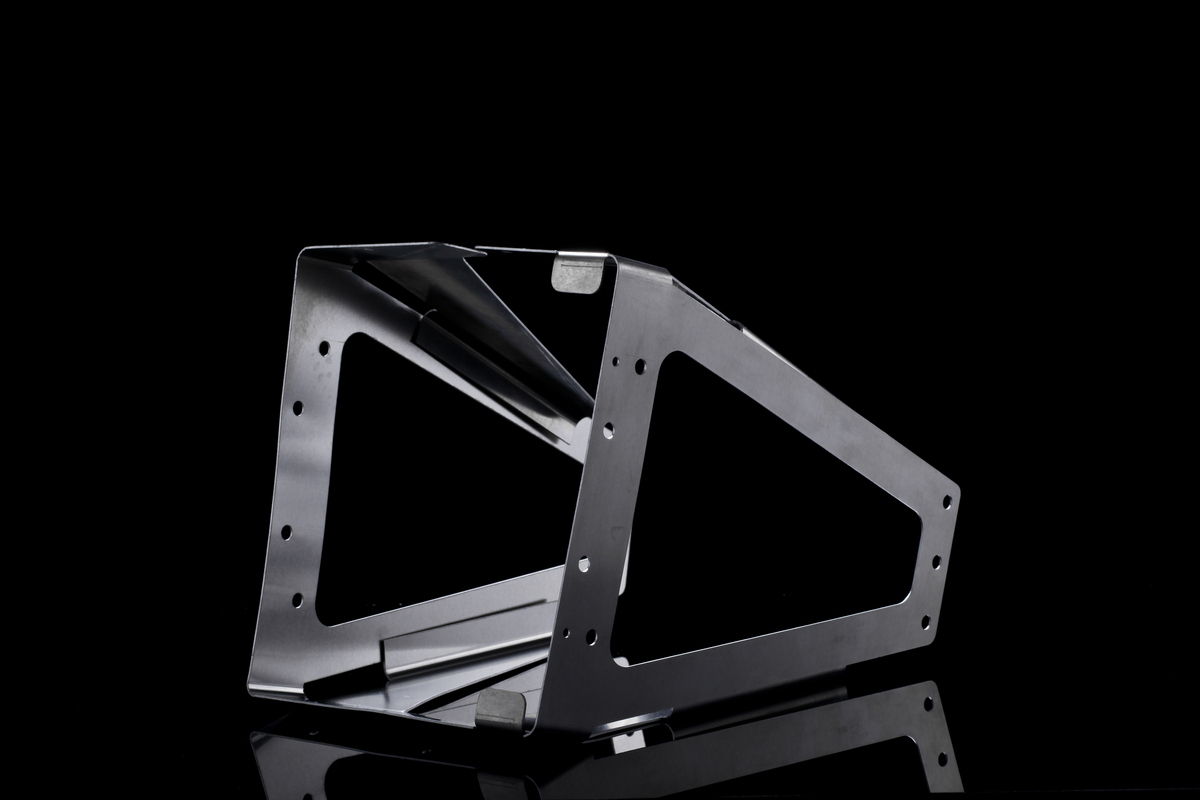
Lean Manufacturing in 3D Printing (Additive Manufacturing)
3D printing allows for great design flexibility and easy adaptation. However, the speed of part production still falls behind that of injection molding. Additionally, post-processing stages are often inefficient and costly, while material expenses remain high.
Lean manufacturing addresses these challenges by introducing more efficient production methods:
- Automating Print Optimization: AI-driven tools analyze and refine support structures and infill density. This reduces material usage and shortens production time by improving the efficiency of the printing process. Fewer adjustments mean faster production cycles and lower operational costs.
- Batch Printing & Parallel Production: Machine utilization is maximized by producing multiple parts simultaneously, leading to increased throughput. This approach allows manufacturers to meet production demands more effectively while maintaining consistency across parts.
- Reducing Material Waste: Closed-loop recycling systems play a key role in minimizing waste. Excess material from failed prints or support structures can be collected, processed, and reused, lowering material costs and environmental impact.
Fictiv supports lean manufacturing in 3D printing through on-demand production, which eliminates the need for excess inventory and reduces storage costs. Its integrated design feedback system allows for early identification of design flaws during prototyping, improving overall part quality and preventing costly reprints. By streamlining production and minimizing waste, 3D printing becomes more suitable for low- to medium-volume runs, offering a cost-effective and adaptable manufacturing solution.
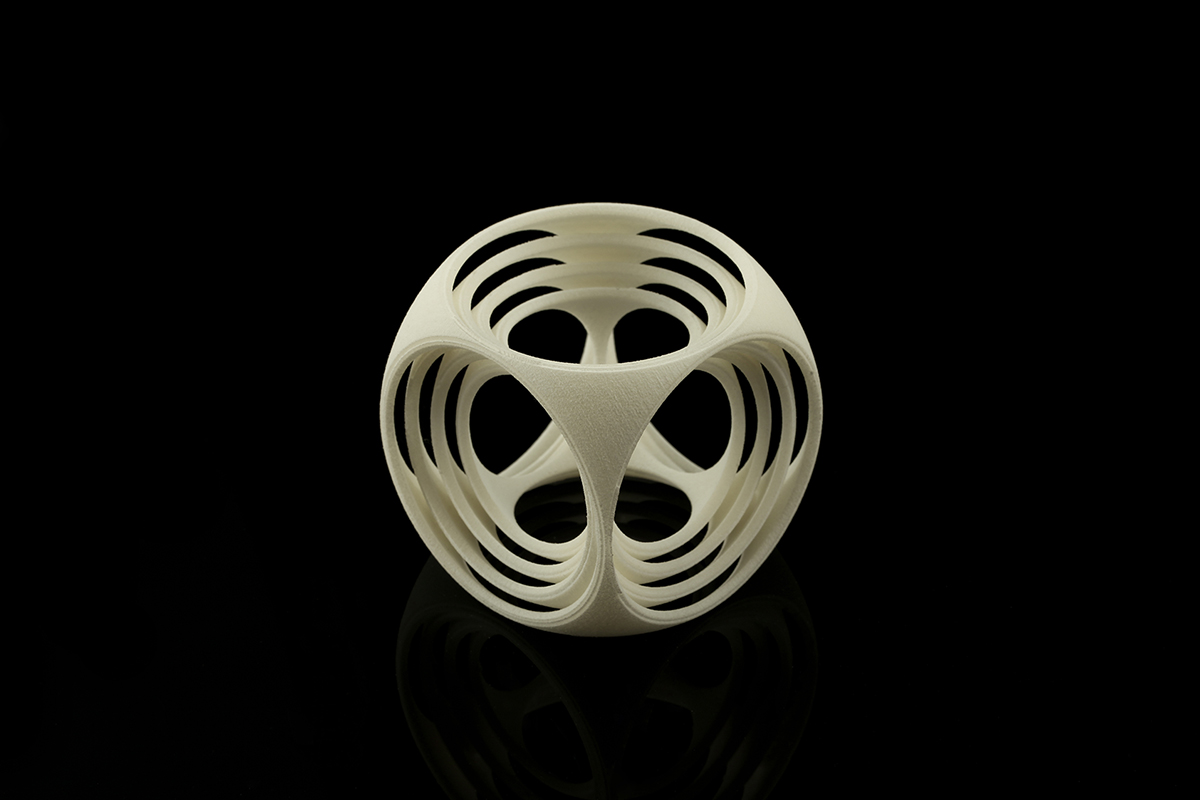
Lean Manufacturing in CNC Machining
CNC machining remains a critical component of modern manufacturing, but it faces several challenges that hinder operational efficiency. Common issues include high tool wear, frequent machine downtime, long setup and programming times, and scrap generated from machining errors. These problems drive up costs, disrupt production schedules, and reduce profitability. Lean manufacturing addresses these challenges through several strategies:
- Automated Tool Path Optimization: Most professional-level CNC machining software already includes tool path optimization to eliminate unnecessary movements and increase productivity. However, Fictiv’s value lies in refining this process through advanced automation, which reduces cycle times and enhances overall efficiency for manufacturers lacking the expertise or resources to optimize paths internally.
- Real-Time Monitoring & Predictive Maintenance: Modern monitoring systems detect anomalies early, allowing for proactive maintenance that reduces unplanned downtime and extends machine lifespan. This ensures that machines operate at peak efficiency, lowering overall production costs.
- JIT Production: Faster changeovers enable manufacturers to produce parts only when needed, reducing excess inventory. However, JIT does not always minimize lead times. While it increases efficiency by reducing storage costs and waste, fulfilling customer orders may still take longer compared to shipping from existing inventory..
Digital platforms like Fictiv enhance profitability through lean practices by offering automated instant quoting. This provides clear cost breakdowns and optimized pricing based on real-time market conditions. Fictiv acts as a marketplace, connecting buyers with CNC machining providers.
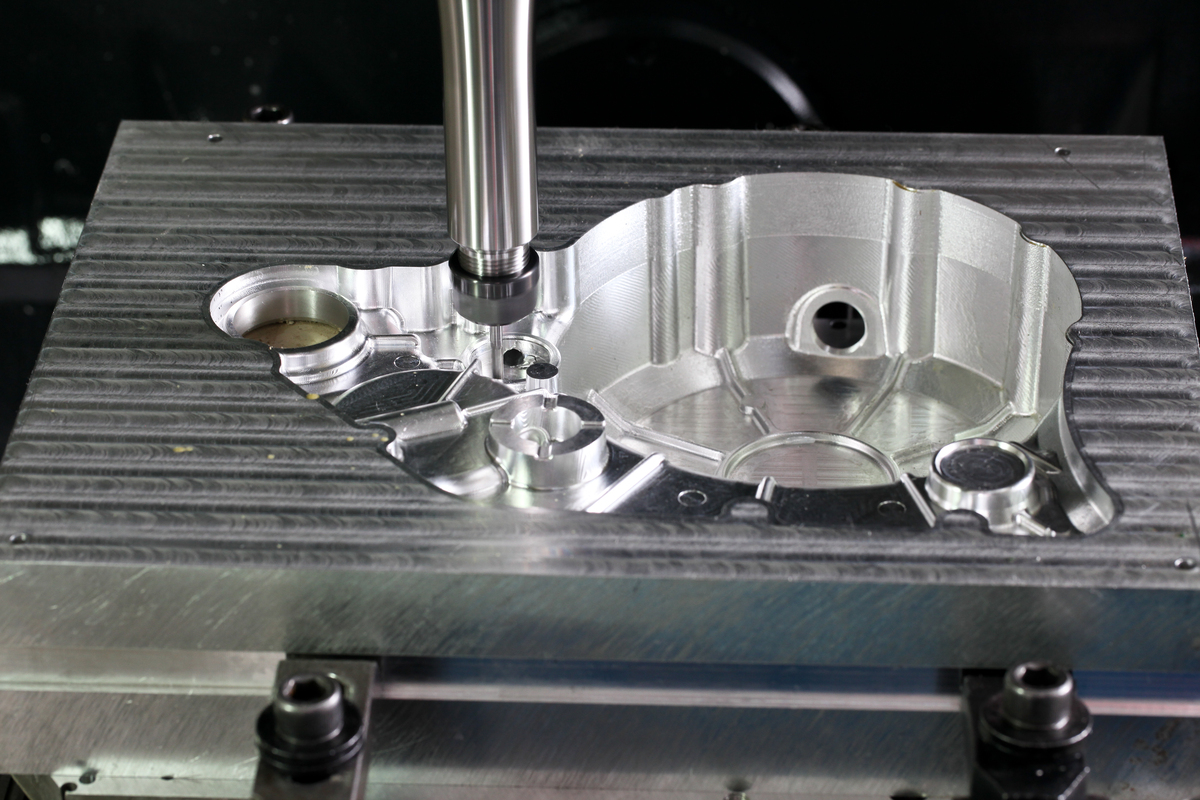
The Role of Digital Manufacturing in Lean Production
Digital manufacturing has reshaped lean production by increasing efficiency and simplifying workflows, allowing manufacturers to respond more quickly to changes in demand. Greater agility, speed, and cost-effectiveness are achieved with these key innovations that are closely aligned with lean principles:
- Cloud-Based Production Management: Real-time order and inventory tracking reduce production and delivery bottlenecks, improving overall efficiency. This ensures a steady production flow, minimizing delays and disruptions.
- AI & Automation in Manufacturing: AI-powered predictive analytics identifies inefficiencies, anticipates maintenance needs, and prevents waste before it escalates.. Automated systems refine processes, improving quality and reducing costs through smarter decision-making and faster adjustments.
- On-Demand & Distributed Manufacturing: Distributed manufacturing refers to a network of smaller, strategically located production facilities rather than relying on a single large factory. This reduces transportation costs and logistical inefficiencies by producing parts closer to the point of use. It supports JIT production by allowing manufacturers to produce only what’s needed, reducing surplus inventory and cutting storage costs.
Fictiv plays a key role in a lean manufacturing strategy by offering instant pricing and DFM feedback, helping to reduce engineering delays and accelerate production timelines. Its global network of vetted manufacturers supports JIT production, while scalable solutions—from rapid prototyping to full-scale manufacturing—provide the flexibility needed to adapt quickly to changing market demands.
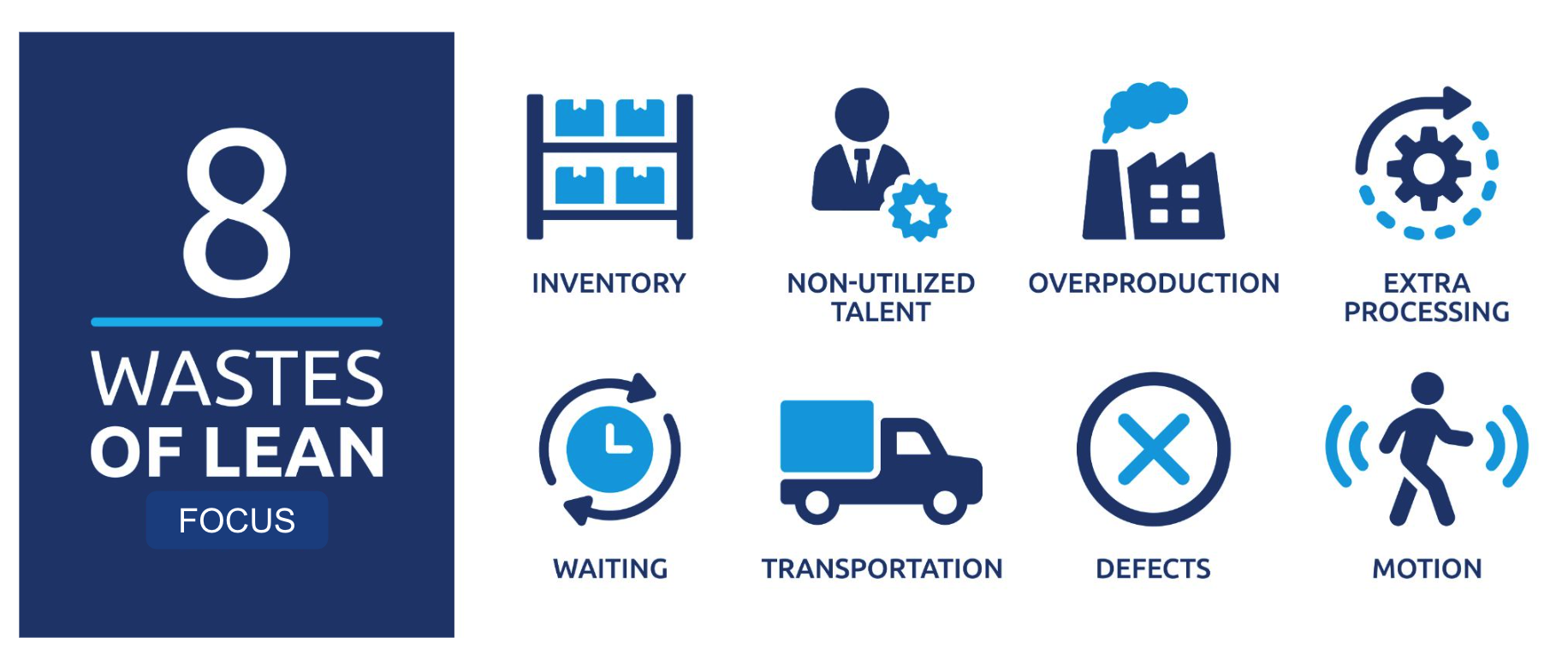
Eight waste reduction focuses in lean manufacturing
How To Implement Lean Manufacturing in Your Production Workflow
To effectively execute a lean manufacturing strategy, you need to optimize every stage of your operations. Identify what’s lacking in your molding, casting, sheet metal, 3D printing, or CNC machining processes. Use metrics and internal feedback to determine what’s “broken” and needs fixing—whether it’s excessive defects, slow mold changeovers, or high scrap rates.
Subsequently, incorporate digital and on-demand manufacturing services to eliminate waste. Just-in-time digital production platforms like Fictiv allow you to produce only what is needed, when it’s needed. This minimizes excess inventory, which lowers warehousing costs and improves resource utilization.
Fictiv helps businesses incorporate automation, AI, real-time data monitoring, and tracking technologies to optimize operational efficiency. Predictive maintenance tools help reduce downtime, while automation takes charge of tooling, cutting, and quality control. AI-driven insights allow for more effective management of production schedules, supply chains, and energy usage—directly aligning with lean manufacturing principles by cutting costs and improving resource efficiency.
Fictiv enhances your workflow by making it more streamlined and competitive. Our quoting tool provides instant, transparent pricing, while adaptive production systems ensure scalability to meet changing demands. Integrated design feedback helps improve part quality and reduce the need for costly rework.
Request a quote today to elevate your production efficiency and drive long-term profitability through lean manufacturing.