Time to read: 7 min
Liquid crystal polymer (LCP) injection molding is used to produce plastic parts with high heat resistance, inherent flame resistance, and excellent dimensional stability. LCP has various electrical, medical, and consumer applications and is available in filled, unfilled, and blended grades. Brands include Vectra®, a family of LCP materials that combine high-temperature performance with chemical resistance for thin-walled applications.
Because of its exceptional properties, injection molded LCP is a specialty plastic rather than a commodity material. LCP’s rapid crystallization during injection molding speeds cycle times, but LCP can crystallize before the mold is filled and cause part defects. During cooling, LCP is also susceptible to deformation from internal stresses.
If you’re considering LCP for your injected molded parts, reading this article is a good place to start because you’ll learn about the material’s:
- advantages
- disadvantages
- applications
- properties
- design guidelines
- processing requirements
- potential alternatives
Fictiv works with a carefully-vetted network of skilled LCP injection molders who can minimize the risk of part defects during prototyping or production. Plus, when you request a quote, you’ll receive design for manufacturing (DFM) assistance from our engineering experts to make sure you get quality results. Create a free Fictiv account and upload your design to get started.
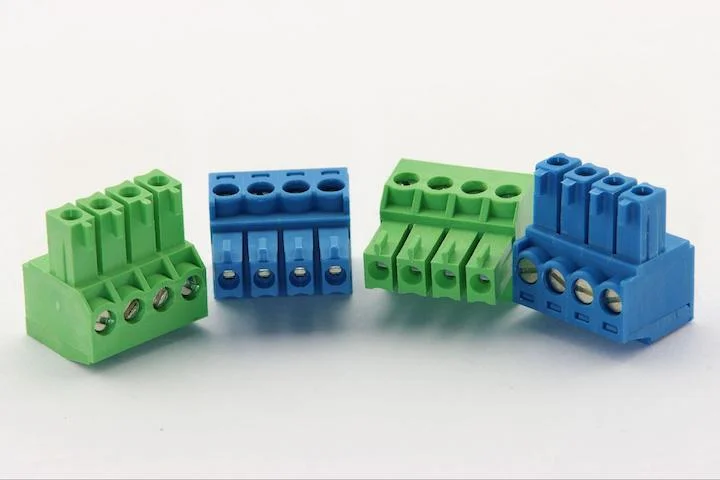
Advantages of LCP
In addition to heat and flame resistance and dimensional stability, injected molded LCP also has high dielectric strength, sterilizability, and biocompatibility.
Heat and Flame Resistance
Injection molded LCP has exceptional themal resistance — it has a continuous operating temperature up to 240°C and can withstand short periods at temperatures as high as 340°C. LCP is inherently flame resistant and does not require additives to achieve a UL 94V-0 flame rating. LCP’s heat deflection temperature (the temperature at which a sample deforms under a specified load) is 187°C for unfilled resin and 275°C for mineral-filled resin.
Sterilizable and Biocompatible
Injection molded LCP withstands sterilization and is not damaged by gamma radiation, high-temperature steam, and most sterilizing solvents. In addition, some grades of the material meet USP Class VI requirements for biocompatibility.
Dielectric Strength
A material’s dielectric strength refers to its ability to act as an electrical insulator, and LCP has a a dielectric strength between 32 and 47 kV/mm, which is considered to be high. The higher the dielectric strength, the greater the voltage the material can withstand before its insulating properties break down.
Dimensional Stability
Injection molded LCP has good resistance to shrinkage and, consequently, exceptional dimensional stability, especially in the direction of flow. There is greater shrinkage in the transverse direction, but less so with filled LCP materials.
Disadvantages of LCP
LCP isn’t the best choice for some types of injection molded parts because of its rapid crystallization, anisotropy, and high cost.
Rapid Crystallization
LCP’s rapid crystallization increases the risk of weld lines, a type of cosmetic defect that detracts from a plastic part’s appearance. In some cases, a weld line can also cause a loss of strength and impact resistance.
Anisotropy
Injected molded LCP is susceptible to anisotropy, a condition where material properties have different values when measured along axes in different directions. This can lead to warpage and problems with part quality and performance. Filled grades of LCP have less anisotropy, which is unusual since fillers generally increase anisotropy in resins.
High Cost
Liquid crystal polymer is a high-performance material that costs more than commodity plastic — it’s one of the most expensive injection molding resins available. PEEK is comparable in terms of price.
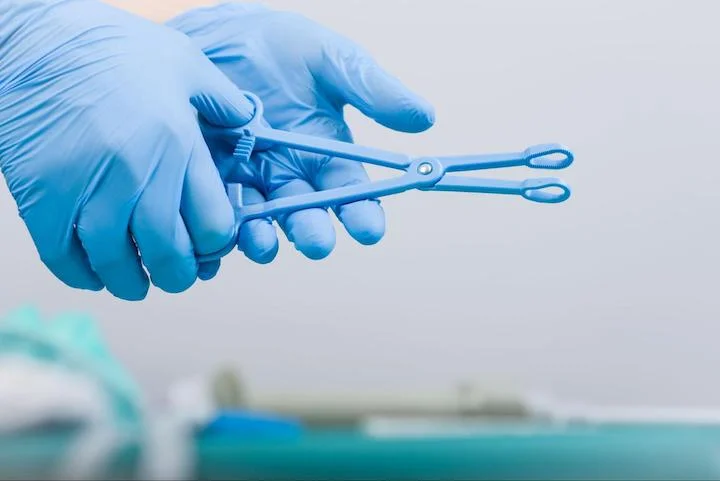
LCP Injection Molding Applications
Injection molded LCP is used for various electrical, medical, and consumer products. What follows are some of the most common applications for each.
Electrical Applications
Due to its dielectric strength and inherent flame resistance, LCP is used for:
- Electrical connectors
- Electronic support structures
- Lighting components
Medical Applications
Due to its sterilizability and biocompatiblity, LCP is used for:
- Catheter braiding
- Surgical instruments
- Replacements for stainless steel parts
Consumer Applications
Injection molded LCP is also used for:
- Cookware coatings
- Food containers
- Metal and ceramic replacements
Properties of Injection Molded LCP
Before deciding to use injection molded LCP, designers need to consider its physical, mechanical, and processing properties, and the most important properties are listed below. Note the differences between filled and unfilled grades of LCP, and how the choice of fill material and its percentage by volume affects performance.
Unfilled LCPA950 | 15% Glass-Filled LCPA115 | 40% Mineral-Filled LCPS540 | ||
Physical | Density (g/cm3) | 1.4 | 1.5 | 1.74 |
Linear Mold Shrinkage, flow (cm/cm) | 0 | 0.001 | 0.001 | |
Linear Mold Shrinkage, Transverse (cm/cm) | 0.0070 | 0.004 | 0.009 | |
Heat Deflection Temperature @ 1.8 MPa (°C) | 187 | 230 | 275 | |
Mechanical | Tensile Strength at Break (MPa) | 182 | 200 | 100 |
Elongation at break (%) | 3.4 | 3.1 | 3.0 | |
Flexural Modulus (GPa) | 9.1 | 12.4 | 9.20 | |
Flexural Strength (MPa) | 158 | 250 | 130 | |
Injection Molding | Drying Temperature (°C) | 150 | 150 | 150 |
Drying Time (hrs) | 4–6 | 4–6 | 6 | |
Melt Temperature (°C) | 285– 295 | 285– 295 | 365– 375 | |
Mold Temperature (°C) | 80–120 | 60 | N/A |
Table 1: Properties of LCP
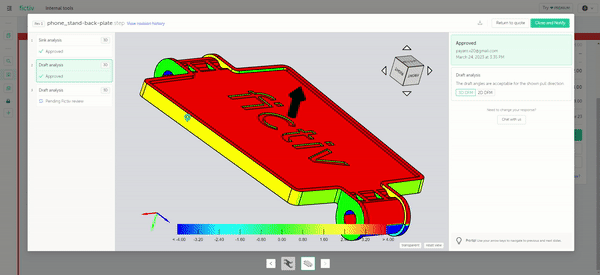
Design Guidelines for LCP Injection Molding
LCP parts that are poorly designed can exhibit injection molding defects but Fictiv’s injection molding experts can help you to refine your design so you get quality results. Plus, you should download our free Injection Molding Design Guide to use as a reference.
Download the Injection Molding Design Guide
There are also some material-specific design considerations you should account for if you choose to mold parts using LCP.
Wall Thickness
Because LCP has a low viscosity, it supports injected molded parts with very thin walls. In general, it’s advisable to keep wall thickness between 0.3 mm and 1 mm — though these are not minimum or maximum values, and thinner or thicker walls are possible. Also, using smooth transitions between different wall thicknesses improves moldability and prevents stress concentrations.
Radii
In general, radii should be at least 1.5 times the wall thickness for outside radii and 0.5 times the wall thickness for internal radii. Keep radii as large as possible to reduce stress concentrations and improve moldability.
Draft Angle
Applying a draft angle, or taper, to the walls of injected molded LCP parts makes it easier to eject them from the mold. For thin-walled components, apply a draft angle between 0.5° to 1°. For thicker-walled components, apply a draft angle between 1° and 2°. In some cases, such as when LCP parts are small and molds are highly polished, little to no draft angle is required. As a rule, however, deeper mold cavities require larger draft angles.
Part Tolerance
Injected molded LCP has highly precise and repeatable tolerance because of the material’s low thermal expansion and relatively low shrinkage, especially in the direction of flow. Parts produced with steel molds have tighter tolerances than parts produced with aluminum molds.
Weld Lines
Injected molded LCP is prone to weld lines that detract from a part’s appearance and cause a loss of strength and impact resistance. To minimize these injection molding defects, designers need to consider the location of the gate, the point where molten plastic enters the mold cavity. The injection molder must also vent the mold properly and use proper speeds and pressures.
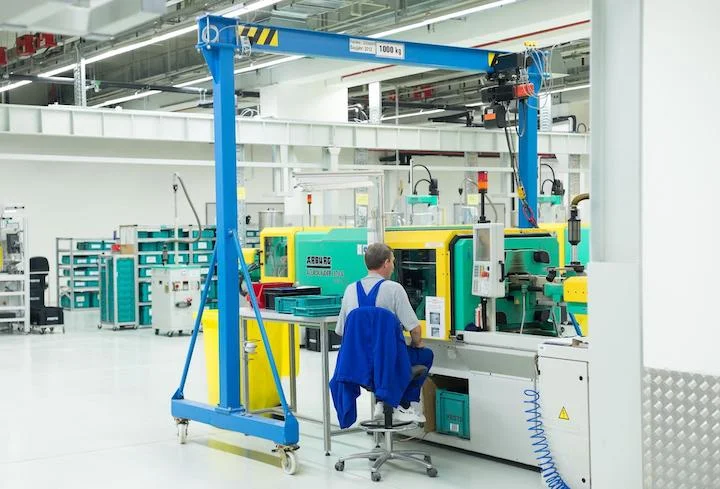
LCP Processing Guidelines
LCP injection molders need to follow specific processing guidelines for best results. Because adherence to these guidelines is beyond a part designer’s immediate control, it’s important to work with an experienced injection molder like those in Fictiv’s carefully-vetted network.
Moisture
LCP resins absorb only low levels of moisture, but drying is still recommended to achieve optimal results. If a plastic resin is overly moist, defects such as voids and blisters may occur. The exact drying time and temperature depend on the specific material grade. In general, however, LCP requires a drying temperature of 150°C between 4 and 24 hours, or until a moisture content of less than 0.01% is achieved.
Temperature Control
LCP’s melt temperature also depends on the specific grade, but it can be as high as 350°C to 370°C. Mold temperatures can be as high as 150°C, but should never be lower than 65°C. If smooth surface finishes are required, high mold temperatures are recommended.
Injection Pressure
With its low melt viscosity, LCP flows easily during injection molding, so lower injection pressures can be used. In general, an injection pressure between 0.35 MPa and 1 MPa is recommended. The holding pressure can be less than the injection pressure, and holding times are significantly shorter than with other semi-crystalline plastics because of LCP’s rapid crystallization.
Injection Speed
To avoid premature crystallization, an LCP injection molder needs to use a relatively fast injection speed. Some material suppliers recommend a filling time between 0.2 and 0.3 seconds, but this rate can be increased for molds that are difficult to fill. High injection speeds also reduce the potential formation of weld lines.
Shrinkage
LCP has a relatively low shrinkage rate because its polymer chains orient themselves in the direction of the melt flow — however, shrinkage can occur in the transverse direction. To minimize shrinkage, LCP injection molders may need to reduce mold temperatures, optimize the mold fill pattern, and increase cooling times.
Potential Alternatives to LCP
If LCP isn’t the right material for your injection molding project, polyphenyl sulfide (PPS) could provide an alternative. This high-performance thermoplastic has a continuous-use temperature between 200°C and 220°C. Like LCP, PPS is also inherently flame resistant. PPS and LCP can be blended together to create a compound with better flow at lower injection pressures and greater weld line strength.
Succeeding With LCP Injection Molding
LCP is a popular injection molding plastic, but a manufacturing-ready design and a skilled production partner are critical to get good results. Fictiv has the engineering experts and global manufacturing network you need to get high-quality injection-molded LCP parts. From prototyping through production, we’re here to help you succeed.
Create your free Fictiv account and request an injection molding quote today — we mold complex parts at ridiculous speeds!