Time to read: 8 min
The modern manufacturing landscape is constantly evolving, with a continued focus on minimizing waste and improving productivity. Just-in-Time (JIT) manufacturing was created with this philosophy at its core. It enables manufacturers to respond to changing market conditions and to meet the increasing consumer demand for high-quality products at lower costs.
JIT works in conjunction with lean manufacturing, sharing the same goal of improving value by eliminating waste. While JIT focuses on delivery and production, lean provides a broader framework for these processes.
In this article, we further discuss what JIT manufacturing is, how it works, and the difference between JIT vs. lean manufacturing.
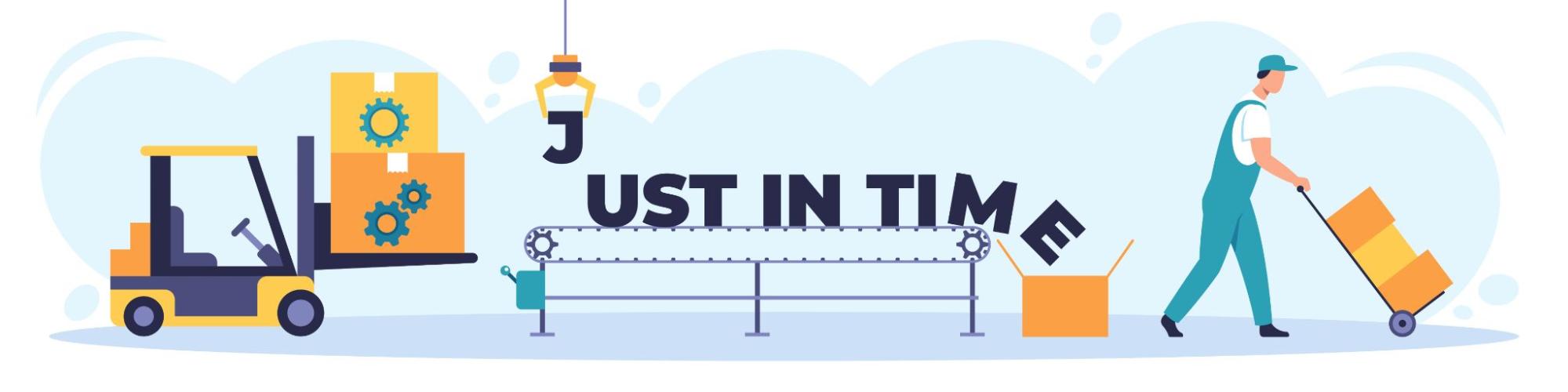
What Is Just-in-Time (JIT) Manufacturing?
Just-in-Time (JIT) refers to the precise moment something needs to be completed. In the context of JIT manufacturing, it relates to the manufacturing strategy that attempts to synchronize the production process with actual market demands to optimize efficiency.
Its basic principle is producing goods only when needed, in the correct amount required, and without excess stock. This makes JIT a crucial strategy in modern manufacturing systems because it focuses on waste elimination, cost diminishment, and optimal resource utilization. It is concerned with increasing efficiency, reducing turnaround time, and encouraging agility within production operations.
Just-In-Time (JIT) manufacturing has its roots in Henry Ford’s production line but was established in the mid-20th century through the Toyota Production System (TPS), developed by Taiichi Ohno. Faced with limited resources and intense competition, Toyota implemented JIT to improve productivity and reduce costs. This innovative system significantly transformed the automobile industry.
With this strategy, Toyota was able to attain astonishing levels of efficiency and maintain high standards of quality control during production. Today, its principles are quite popular as a foundation of lean manufacturing practices across industries.
How the Just-in-Time Manufacturing Process Works
The JIT manufacturing system is designed to operate with seamless coordination at every stage of production, ensuring that each step is perfectly synchronized. This high level of integration helps eliminate waste and maximize efficiency. Here’s how it works:
- Demand Forecasting
The prerequisite for demand forecasting is an accurate estimate based on data trends, and is the base for JIT manufacturing. By utilizing analysis of market trends, consumer behavior, and past data, manufacturers can estimate the demand and ensure that production falls within the boundaries of customer needs, so that what is produced does not become surplus or insufficient.
It is very important to create dependable relationships with all suppliers. Suppliers need to be able to provide raw materials and components right before the need arises, and production will be disrupted if this becomes unreliable. Trustworthy and clear communication, along with efficient logistics, are needed to prevent delays.
- Production Synchronization
In these systems, every step of the process is interconnected with the next. Each component is added only when needed to prevent bottlenecks and sustain a consistent pace with production cadence. This coordination removes downtime, improving output and paving the way for more efficient operations.
- Excess Inventory Avoidance
Manufacturers incur cost and space savings by eliminating stockpiles of raw materials and finished goods due to a lack of available storage. Materials are bought and consumed immediately, optimizing the processes.
- Quality Inspection and Ongoing Improvement
Standards have to be set and maintained while carrying out JIT manufacturing to assure proper control of quality. The undertaking may be disturbed if the quality of the products or the parts is not adequate. Therefore, an appropriate control procedure is performed at all operative levels. Continuous improvement principles like Kaizen—which emphasize minor, ongoing process enhancements—are applied to help operations adapt to changing market conditions.
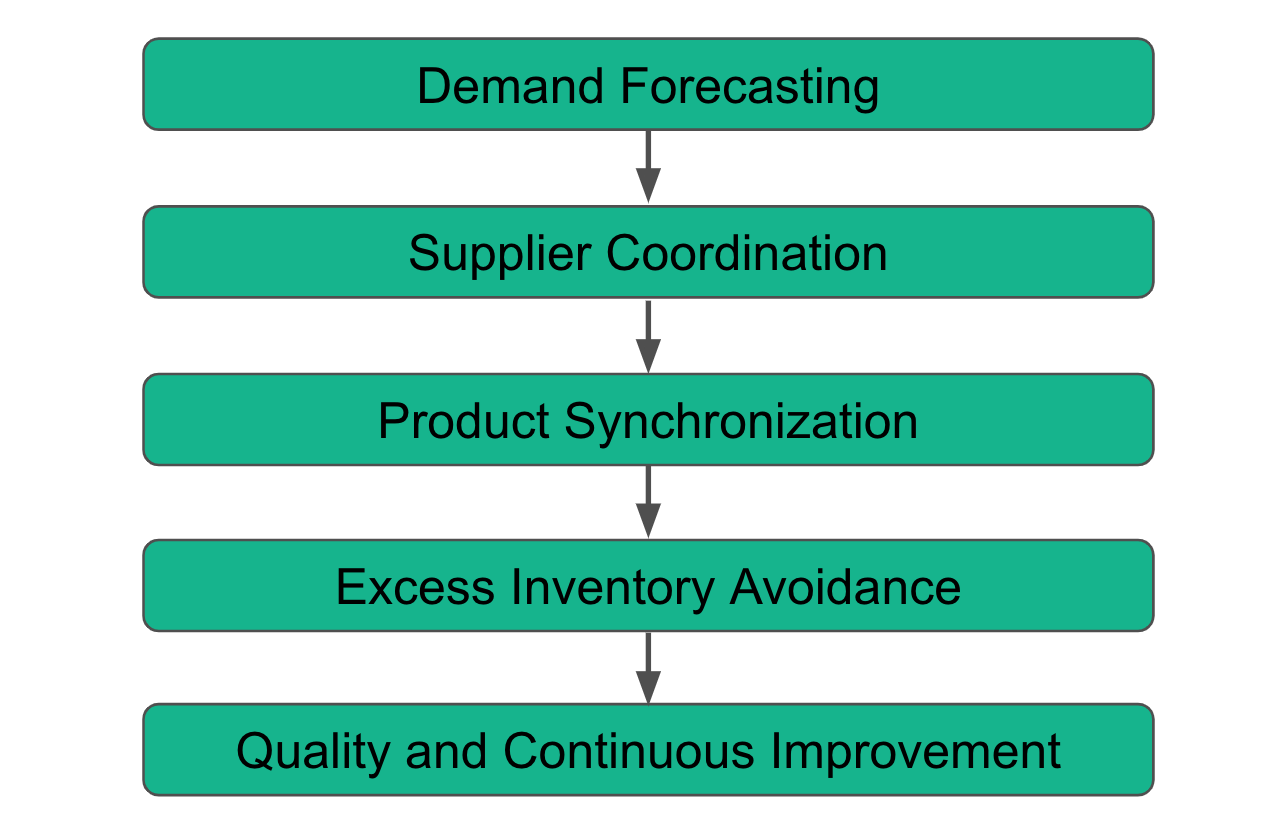
Just-in-Time Manufacturing Process Steps
Just-in-Time vs. Lean Manufacturing
Lean manufacturing and Just-In-Time manufacturing are similar because they each try to eliminate waste from the individual steps of a process. Lean manufacturing looks at the complete system and eases the work of eliminating waste, whereas JIT focuses on “when” and “how much” to produce or procure. Together, these methodologies form a powerful combination, optimizing processes and driving improvement.
Similarities
Both strive to eliminate waste in any form, including:
- Overproduction
- Excess inventory
- Unnecessary work
- Inefficient processes
Another common factor is that both approaches focus on customer value, drive efficiency and responsiveness, work under the same principles of continuous improvement (Kaizen), and set high operational quality requirements.
Differences
JIT focuses on inventory control within the context of on-demand production. In contrast, lean manufacturing takes a more comprehensive view by looking at organizing workflows, reducing downtime, and improving general workplace structure. Lean includes a wide range of tools and techniques such as value stream mapping, 5S, and Kanban; one of the strategies within lean manufacturing would be JIT.
When to Use JIT vs. Other Lean Strategies
JIT is best suited for firms that experience and have access to a steady demand and a reliable supply chain. Other lean options–like safety stock or some form of flexible processing–could better address other cases of supply chain unpredictability, frequent supply interruptions, or high demand variability. Most manufacturers blend JIT with lean principles to form a more suitable strategy for their operational requirements.
Sign up or log in with Fictiv today for support on manufacturing strategies for your product production.
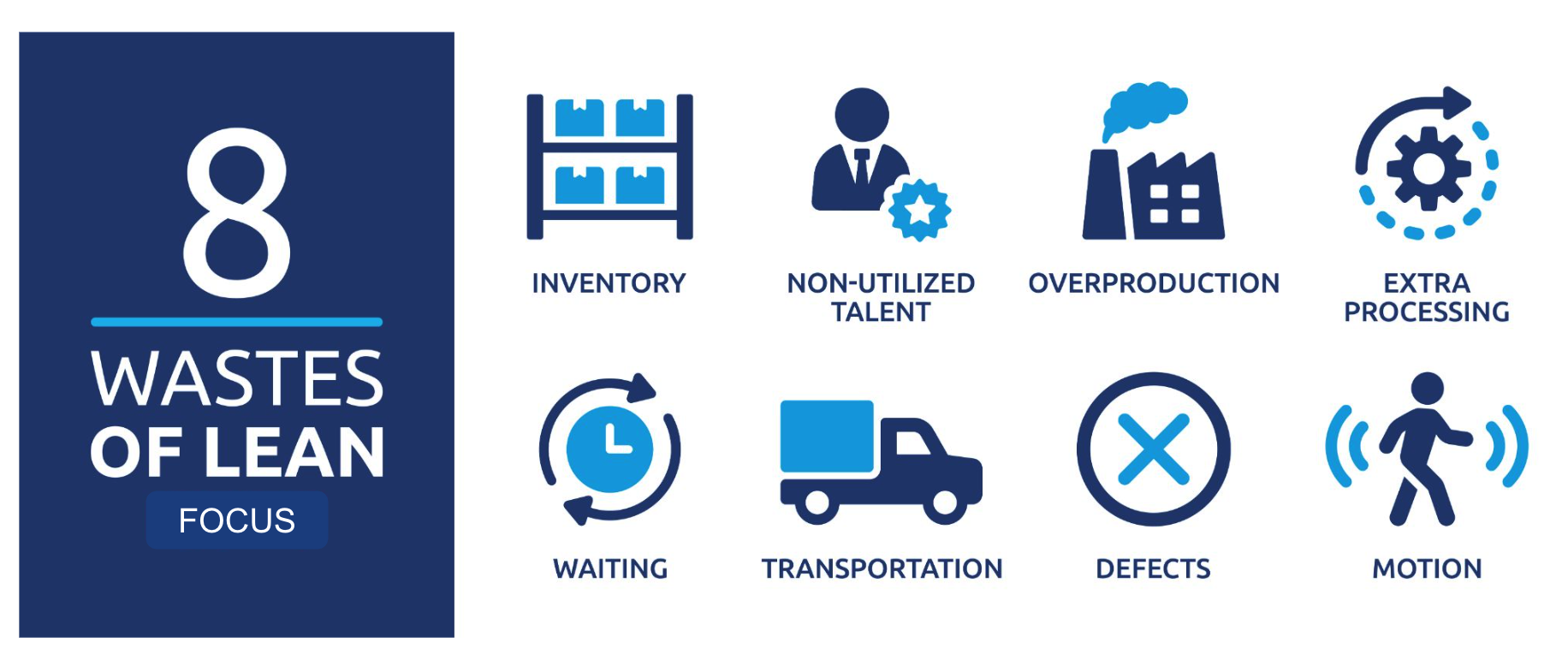
Advantages of Just-in-Time Manufacturing
Just-in-time manufacturing offers several key advantages, making it a vital part of modern production systems. By streamlining processes and focusing on efficiency, JIT positively impacts various aspects of manufacturing:
- Reduced Inventory Costs
Instead of accumulating large stocks of materials and finished goods, businesses using JIT only produce goods based on actual demand. This reduces infrastructure and storage costs, freeing up valuable resources that can be used to support other business operations.
- Minimized Waste and Inefficiencies
JIT aims to eliminate waste at every stage of production. By accurately aligning production with demand, resources are used more effectively and overproduction is avoided. As a result, unused materials are reduced and workflow bottlenecks are prevented, ensuring smoother operations. This ongoing refinement process helps maximize asset utilization and increases the likelihood of long-term business sustainability.
- Faster Response to Market Demand
Since the focus is on production as it occurs, businesses can meet consumer needs and develop new products sooner, allowing them to remain ahead of competitors in fast-changing sectors.
Considering the reduction in inventory levels, JIT improves cash flow because resources are more efficiently used. Operating costs are lowered, and resources can be used in other areas of the company, which will increase profitability.
- Higher Product Quality
Active, rigorous inspections coupled with improvement procedures guarantee that only those products that are confirmed to be of high standards will be sold to customers, thereby increasing their satisfaction and loyalty.
Challenges and Risks of JIT Manufacturing
While JIT offers useful advantages, it also creates challenges. This can affect the implementation as well as the longevity of success in some industries.
- Supply Chain Disruptions and Dependency on Suppliers
Supply chain disruptions, such as delays, transportation issues, or supplier failures, can completely stop production. This highlights the need for effective partnership and contingency programs with suppliers.
- Demand Fluctuations and Forecasting Accuracy
Market demand shifts or inaccurate forecasting can result in production delays, failure to meet customer order targets, or surplus production. Containing variation in demand while maintaining operational efficiency is a critical challenge.
- Implementation Challenges in Different Industries
Adopting or implementing JIT is different among different industries. Sectors such as automotive manufacturing with predictable demand can use it, while industries with unpredictable demand and complex production processes may struggle. There is a need to invest in a personalized approach to developing strategies that align with lean, efficient, and well-coordinated production paradigms.
Even with these challenges, an adequately coordinated plan along with technological integration can allow JIT to operate seamlessly.
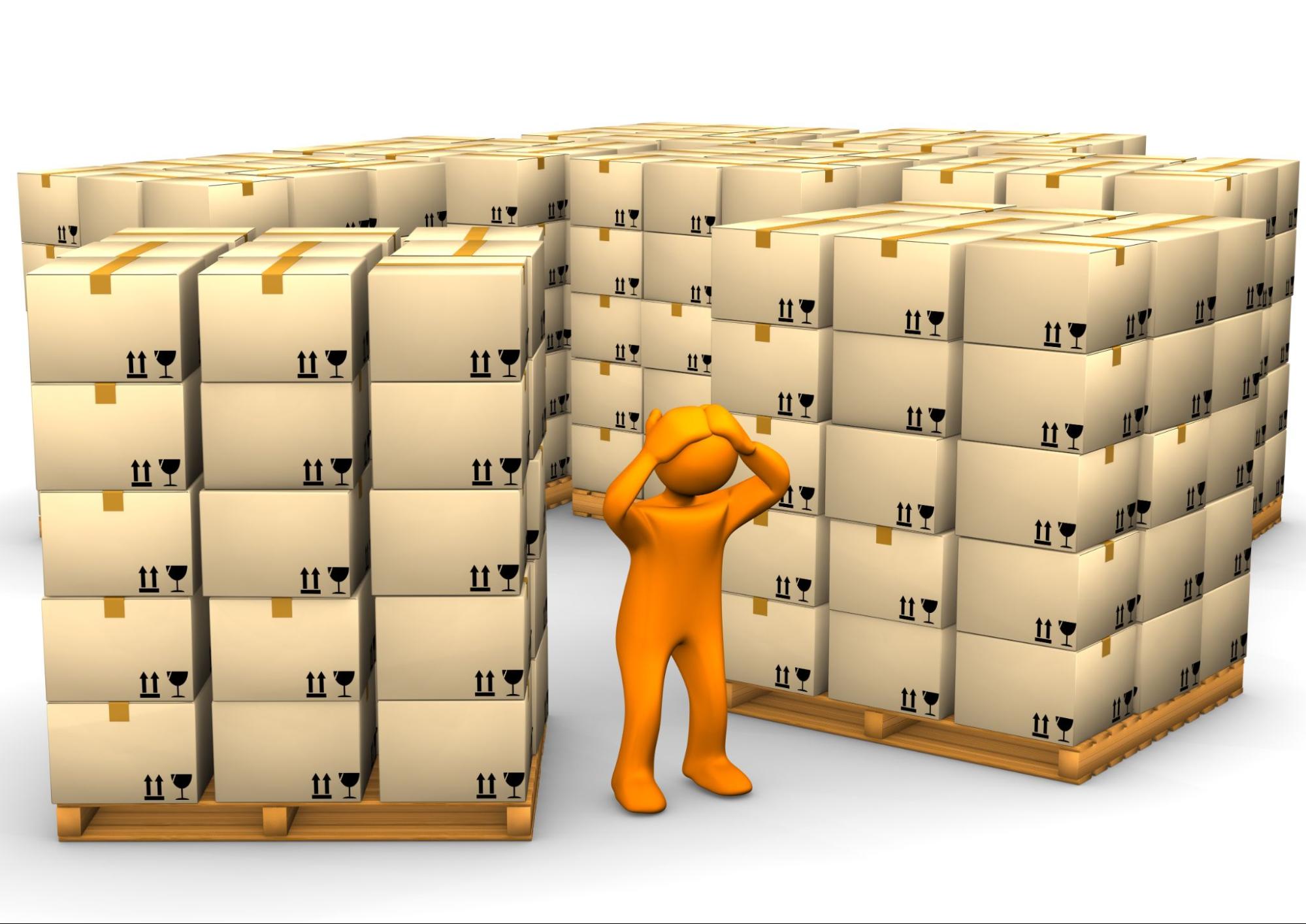
Real-World Examples of Just-in-Time Manufacturing
Toyota’s Just-in-Time is recognized as the superior standard within the entire industry and scope of reference. The TPS (Toyota Production System) served as a precursor to JIT, as it helped Toyota scale its production to synchronize with demand, manage inventory, and improve overall operational efficiency. It is this shift that allows Toyota to succeed globally while serving as an inspiration to many other industries.
JIT principles are adopted in almost every other industry, such as electronics, medical devices, and food and beverage. Companies like Dell implement this system to quickly fulfill orders that can be refreshed on demand, while healthcare device manufacturers use it to ration critical devices, ensuring timely delivery with minimal waste.
JIT in Digital & On-Demand Manufacturing
Fictiv and similar platforms have transformed the scope of digital and on-demand manufacturing, as they specialize in the application of JIT principles within modern systems. With the help of advanced technology, these platforms manage to optimize production processes to meet real-time demand. These platforms offer manufacturers unparalleled accuracy and agility by offering lower-volume rapid prototyping and efficient distribution.
Digital platforms like Fictiv that showcase instant quoting features allow cost assessments and informed decisions to be made within short timeframes. They help manufacturers locate suppliers with the best pricing structures and lead times and guarantee delivery of materials and components. Also, decreased spatial separation between production and consumers in distributed manufacturing networks enhances the ability to minimize transportation lags, supply chain risks, and seasonal variations.
Modern cloud-based manufacturing systems paired with JIT principles create a multitude of advantages. Workflows and resources are observable in real-time, relating to current and future production, which boosts forecasting and inventory accuracy. This integration of cloud technology and JIT improves response times, waste mitigation, operational efficiency, and alignment with cloud systems.
Ultimately, adaptive, seamless, and cost-efficient environments focused on the production needs of an agile global market are possible with the integration of digital mechanisms and JIT principles.
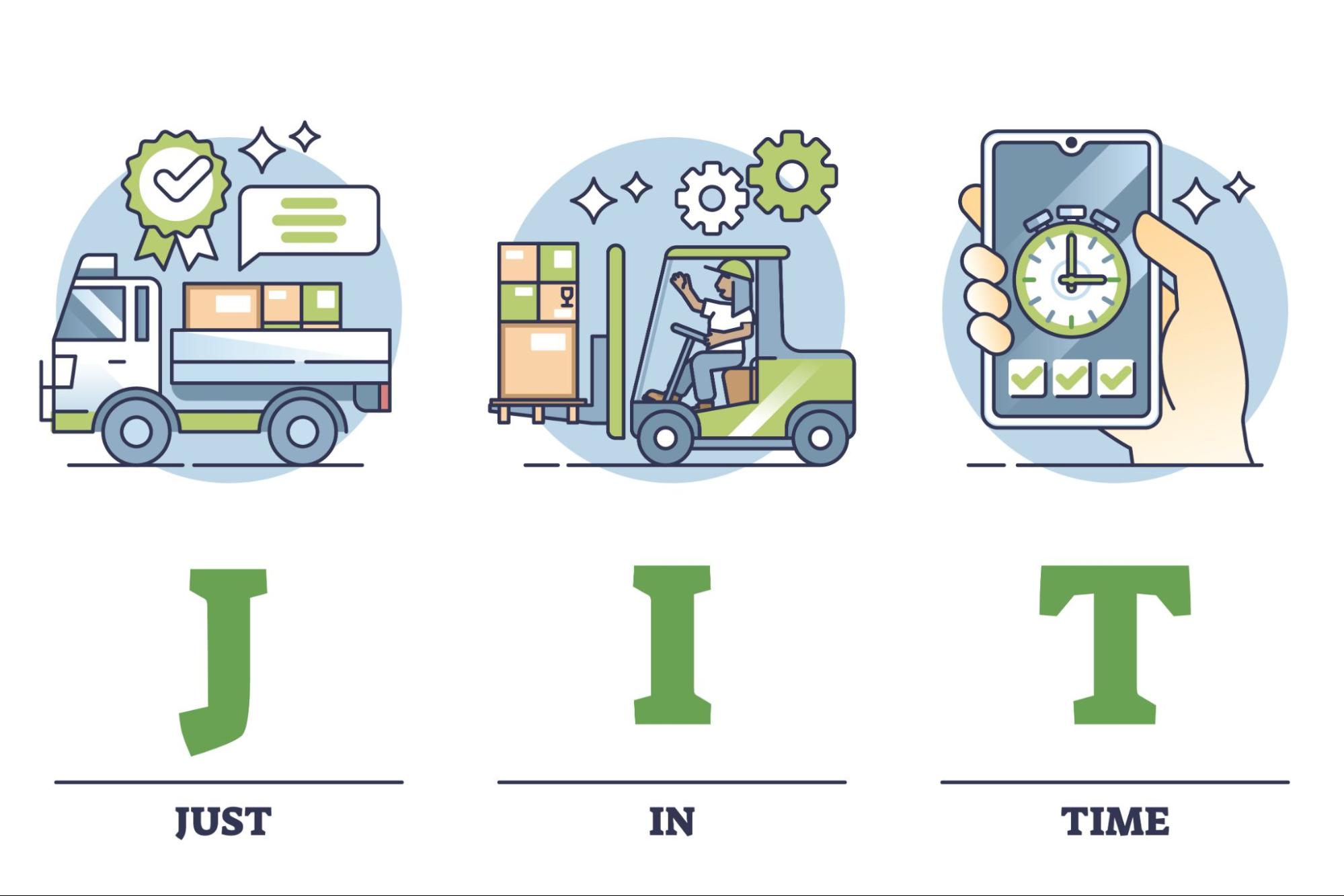
The Strategic Role of Just-in-Time Manufacturing in Modern Production Systems
Just-in-time manufacturing is an effective approach to optimizing processes and enhancing organizational efficiency. It has transformed businesses by minimizing inventory and waste while increasing flexibility, enabling companies to gain a competitive edge. When combined with lean manufacturing principles, this method enhances customer value and supports the development of sustainable production systems.
Determining whether this approach is the right fit requires strategic evaluation. Companies must assess factors such as supply chain reliability, demand volatility, and the overall production environment. It works best in settings with stable supplier networks, predictable demand, and well-coordinated logistics. For industries facing frequent disruptions, adapting their principles or integrating complementary strategies may be necessary.
Looking ahead, the integration of emerging technologies will continue to shape the future of JIT. Tools like AI, real-time data analytics, and cloud-based manufacturing systems are enhancing its flexibility and effectiveness. As innovation progresses, this methodology remains a cornerstone of efficient, forward-thinking operational models focused on continuous improvement and excellence.
At Fictiv, our digital manufacturing platform empowers our clients with state-of-the-art technologies, helping them optimize processes, improve agility, and reduce lead times. Enjoy effortless sourcing, AI-based quoting, and a distributed system of manufacturing partners that guarantees parts are available when you require them. Get an instant quote today!