Time to read: 4 min
The market for plastic injection molding continues to grow due to increased spending, faster technological progress, the development of on-demand injection molding, and shorter supply chains through reshoring. However, reduced labor availability, especially in the United States, presents a challenge for injection molders.
This article discusses the trends that are poised to shape the injection molding industry for the remainder of 2023 and beyond.
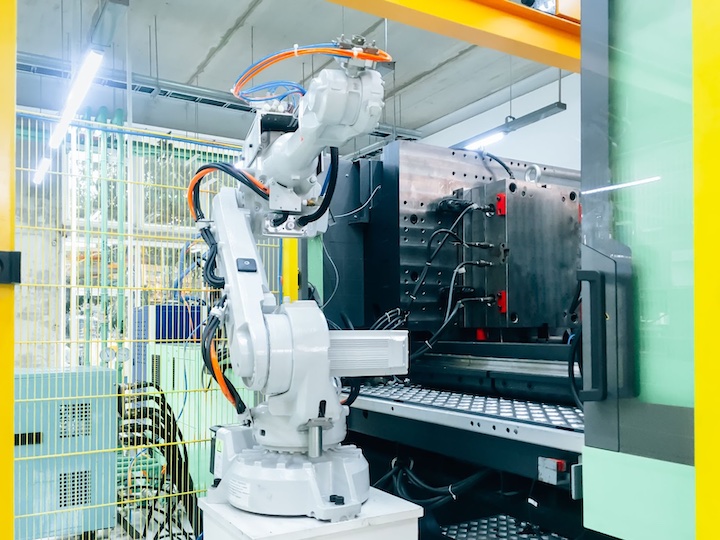
Injection Molding Trends in Key Markets
The injection molding industry is projected to maintain its post-pandemic momentum throughout the rest of 2023 and into 2028 with an expected CAGR (Compound Annual Growth Rate) of between 3.5–5%. Geographically, the fastest growing market, as well as the largest market overall, will be the Asia Pacific region — with China, India, Japan, and South Korea as the largest contributors.
Increased demand for medical devices, automotive components, and consumer products are expected to drive this growth in key markets over the next 5 to 7 years:
- Medical Devices: From 2023 through 2030, forecasts predict increased demand for injection molded plastics in the medical industry, with a projected CAGR of 5.7%. This will be driven in part by increased demand for low-cost, high-quality medical equipment.
- Automotive Components: From 2023 through 2028, forecasts predict increased demand for injection molded plastics in the automotive industry, with a projected CAGR of 6.34%. The electric vehicle market will be a major driver because EVs require high production volumes, increased component durability, lightweight components, and low-cost materials.
- Consumer Products: From 2023 through 2028, forecasts predict increased demand for injection molded plastics in the consumer-goods industry, with a projected CAGR of 4.39%. Increased consumer spending is driving this trend, in large part due to retail and e-commerce packaging requirements.
Six Factors Driving Injection Molding Trends for 2023
There are six factors driving injection molding trends for 2023.
- Increased adoption of automation
- On-demand injection molding
- Adoption of new technologies
- Shorter supply chains
- Increased focus on sustainability
- Labor shortages
#1 Increased Adoption of Automation
Injection molding is already a highly automated industry, especially for high production volumes. However, there is still room for injection molding facilities to implement advanced technologies. Today, robotic systems are becoming more user-friendly and cost-effective as more companies enter the market. In fact, the industrial robotics market is predicted to have a CAGR of 7.2% until 2033. Look for new, more-affordable automation solutions for the injection molding industry that reduce cycle times and lower per-part costs.
#2 On-Demand Injection Molding
Injection molders need the ability to support on-demand product development on increasingly tight timelines. Today, designers need to rapidly iterate while producing smaller quantities for pre-production prototyping and market testing. By producing cost-effective tooling for lower production volumes — like soft and semi-hardened steel tooling for prototyping and low-volume injection molding — injection molders can meet this demand.
#3 Adoption of New Technologies
Artificial intelligence (AI) continues to advance in 2023 through powerful LLMs (Large Language Models). These AI technologies have not yet had a direct effect on injection molding equipment, but there is potential for AI-driven productivity increases in all industries. Meanwhile, Industry 4.0 IIoT (Industrial Internet of Things) technologies are already collecting real-time production data so that injection molders can improve production rates and reduce costs.
AI systems can analyze this data to highlight potential pain points and reveal opportunities to increase efficiencies. This can be achieved, for example, with the introduction of in-mold sensors that measure cavity pressure and optimize injection molding performance. There is also increased demand for multi-material injection molding machines that are able to inject multiple materials into a mold during a single cycle to create complex components in one shot.
#4 Shorter Supply Chains
Supply-chain concerns during the pandemic have encouraged many companies to bring their manufacturing back to the United States, including injection molding and tooling manufacturing. However, Plastics Today reports that the percentage of plastics processors relocating back to the U.S. declined by 10% in Q4 2022, though nearshoring to Mexico is also a growing trend. Still, reshoring still provides many benefits, such as increased product quality, reduced transportation costs, reduced lead times, and increased sustainability.
#5 Increased Focus on Sustainability
Sustainability within the plastics industry continues to be a major point of discussion due to increased public awareness of the high levels of pollution created by plastics waste. This has, in turn, increased demand for sustainable products, which has driven companies to incorporate plastics that can be recycled or are biodegradable, such as PLA or bio-PET materials, into their offerings.
There is also increased adoption of all-electric injection molding machines that can provide significant energy savings over traditional hydraulic-based machines. In terms of supply-chain regulatory changes, the EU has begun implementing requirements that companies perform due diligence on their suppliers to identify human rights violations and adverse impacts on the environment.
#6 Labor Shortages
Economists predict that labor shortages in the United States will continue through 2023, and Plastics Today reports that workforce development remains the top issue for U.S. mold makers. Although some injection molders are increasing automation and retraining their current employees, a lack of qualified machinists has the potential to force U.S. companies to look elsewhere for tooling, and even for injection molding services.
The Future of Injection Molding is Fictiv
There is no sign that the market for injection-molded plastic parts will trend downward within the next five years. The adoption of new technologies will improve overall productivity, while increased regulatory oversight will require a greater focus on sustainable practices. Plus, part designers have powerful options if they know where to look.
Fictiv is staying on top of market trends and leveraging its knowledge to provide solutions that deliver what customers need — complex injection molded parts at amazing speeds. When it’s time for your next injection molding project, create an account and upload your part drawing. Along with your quote, you’ll get expert design for manufacturing (DFM) feedback and guidance throughout the process to ensure you get great results.