Time to read: 11 min
Known for quickly producing parts with consistent precision, injection molding is one of the most popular methods for creating high-quality plastic components. This manufacturing process creates parts by forcing molten plastic into a mold at high pressure, which cools and solidifies into the desired shape. It’s used across various industries to efficiently produce complex, durable products at a relatively low cost per unit.
Injection molding tooling is essential for the entire process. The mold, also known as the tool, is engineered to withstand high temperatures and pressures over hundreds of thousands of cycles. Many factors, including the type and material of the mold, affect its overall cost, output, and durability.
This article covers important considerations for injection molding tooling to produce high-quality products cost-effectively. For injection molded parts with complex geometries at ridiculous speeds, create a Fictiv account and upload your part design today.
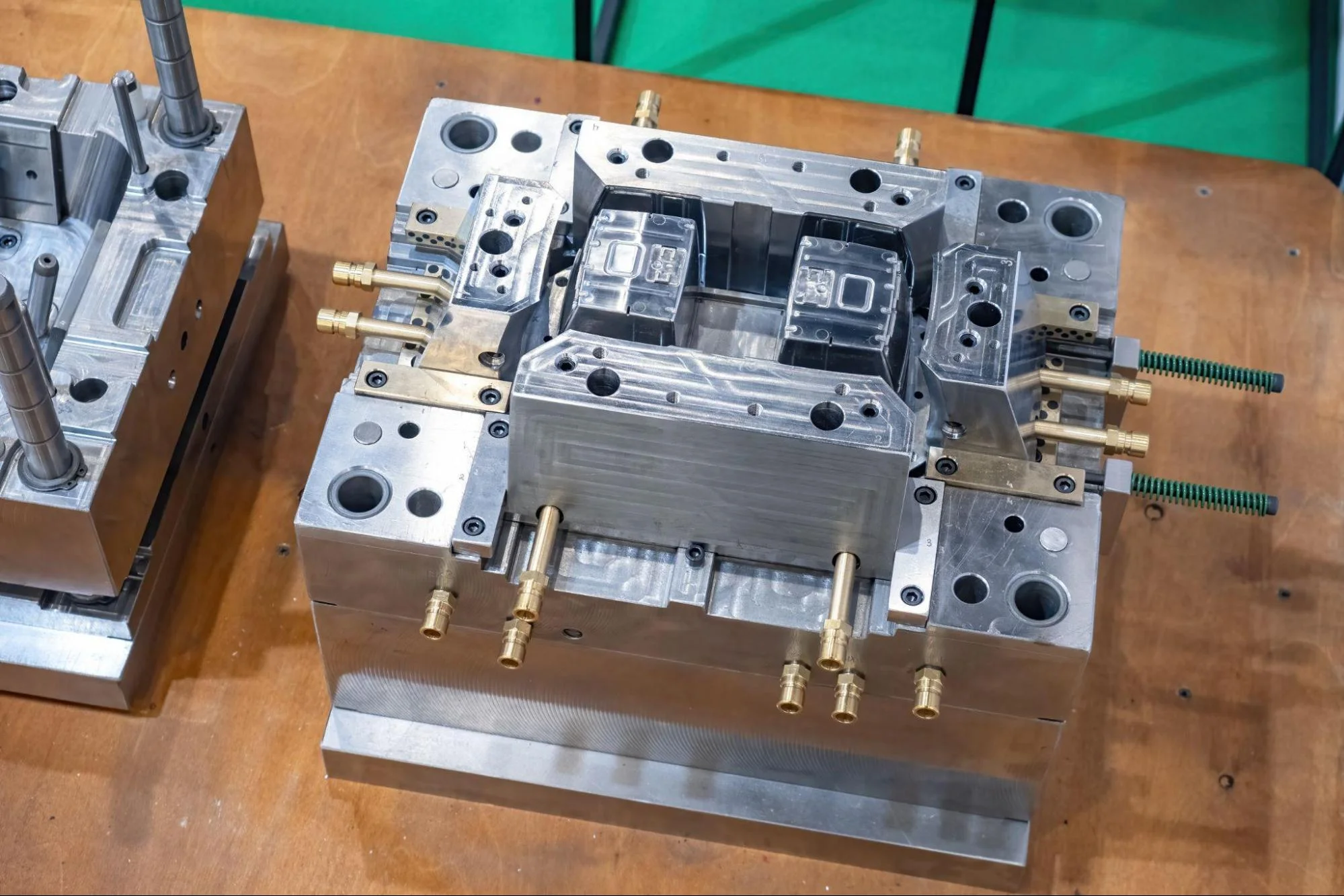
The Critical Role of Tooling in Injection Molding
Effective tooling design and selection significantly impact efficiency, cost, and overall product quality. A well-constructed mold facilitates smooth production and high-quality output, whereas tooling failures or inefficiencies can lead to increased downtime, defects, and significant financial losses.
In an industry where precision and speed are critical, robust tooling is essential for a successful molding operation. Using proper molding parameters, a well-designed tool can quickly and repeatably produce intricate features with tight tolerances as small as +0.002″ (0.05 mm).
Types of Injection Molds and Key Components
In injection molding, the mold itself is the most important component, as it defines the shape, quality, and efficiency of part production. Factors like production volume, part complexity, and cost considerations determine the type of mold used. In addition to selecting the appropriate mold type, understanding key mold components is essential for optimizing performance, ensuring proper material flow, and achieving consistent part quality.
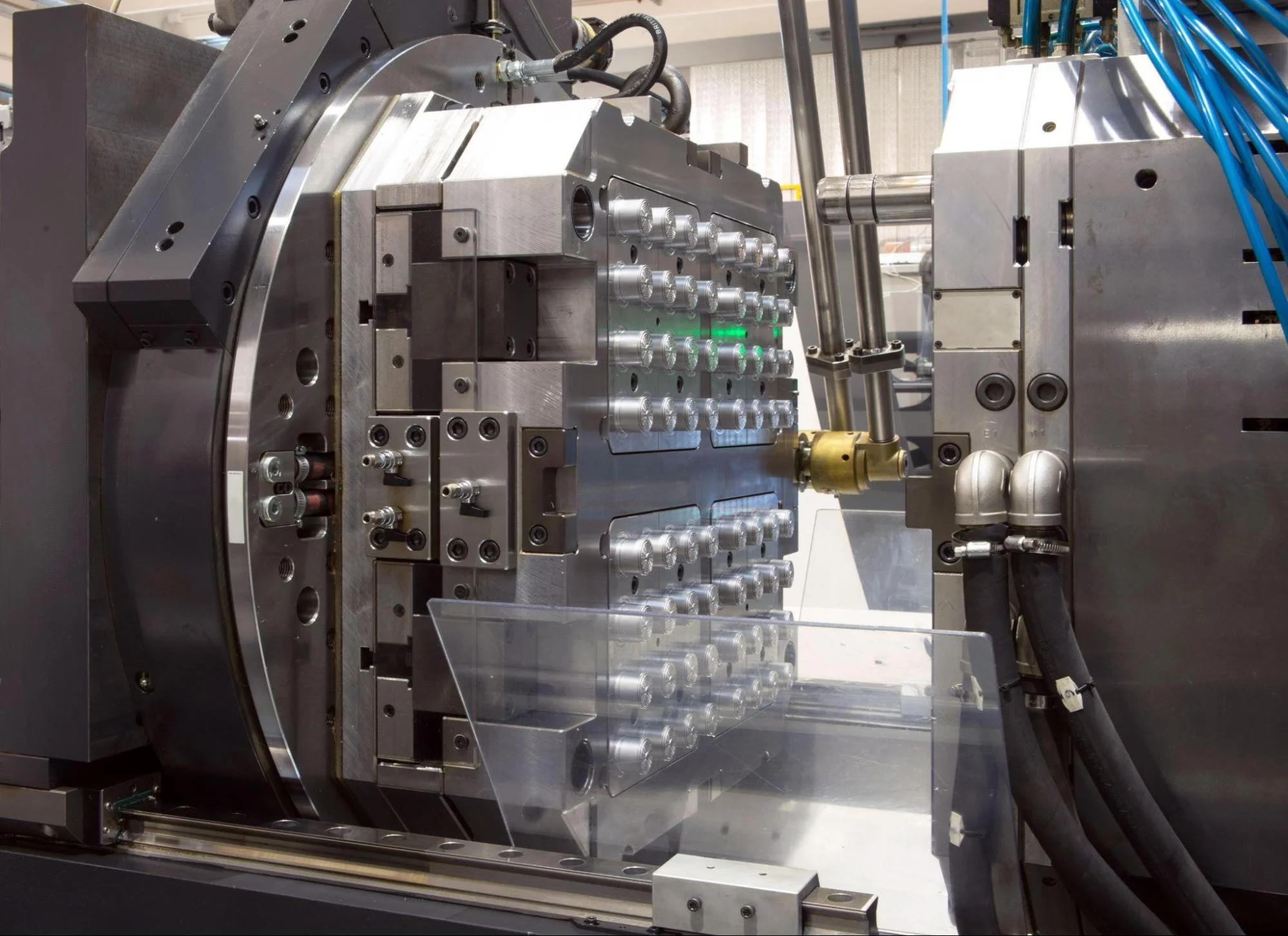
A multi-cavity injection molding tool.
Types of Injection Molds
1. Single-cavity molds
A single-cavity mold produces one part per cycle. This mold type is best suited for low-volume production runs, prototyping, or when the cost of producing multiple cavities outweighs the benefits. Although slower in production than other mold types, single-cavity molds are less complex and less costly to manufacture, making them ideal for smaller projects or highly specialized parts.
2. Multi-cavity molds
Multi-cavity molds contain multiple cavities within the same mold. These allow for the simultaneous production of several identical parts in a single cycle, which is efficient for high-volume production since it significantly reduces per-unit costs and increases output. The challenge, however, lies in maintaining consistent quality across all cavities. Consequently, precision in mold design and processing is critical to maintaining consistent quality in the finished product.
3. Family molds
Family molds are designed with multiple cavities that produce different parts in a single cycle. This mold type is useful when producing parts that are to be assembled together. However, it can be more challenging to balance material flow and ensure uniform part quality since different cavities may require different flow rates and cooling times.
4. Stack molds
Stack molds feature multiple levels, or stacks, which increase the number of parts produced without needing a larger machine. This design enhances production efficiency by maximizing output from a given machine footprint. Stack molds are commonly used in large-scale manufacturing environments where reducing cycle time and increasing production volume are critical.
5. Rapid or “soft” tooling
For prototyping or short-run production, rapid tooling made from a 3D-printed polymer or softer metal such as aluminum can quickly produce and validate design concepts. While optional, a “proto tool” (soft tool) is often recommended before committing to full-scale production tooling.
Key Injection Mold Components
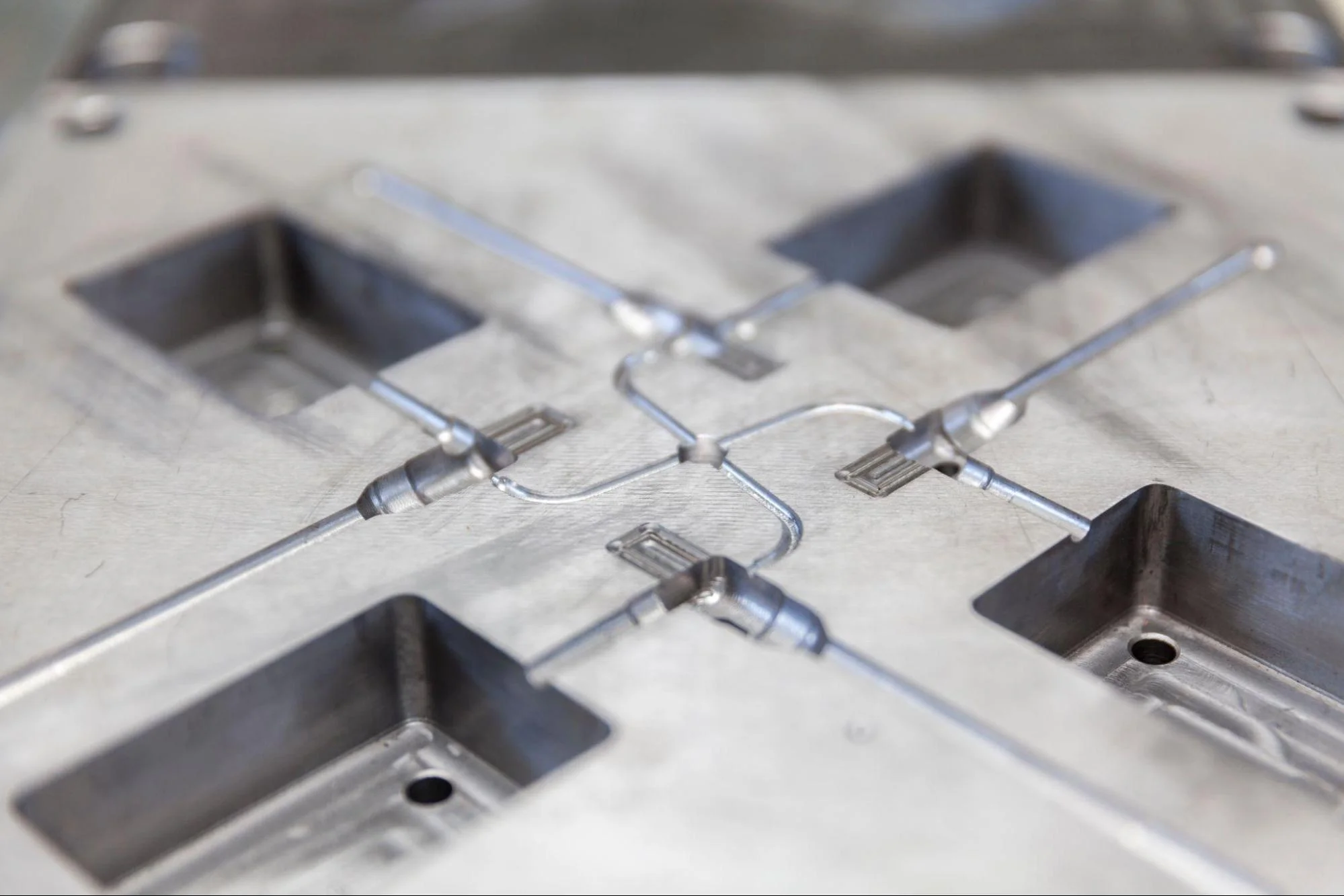
Listed below are the key components that influence a mold’s function and efficiency:
1. Injection Mold Halves (Core and Cavity)
- Mold cores: The core is convex and forms the internal geometry of the part, including features such as holes, recesses, and hollow areas.
- Mold cavities: The cavity is concave and forms the external geometry of the part, including features such as ribs, bosses, logos, and cosmetic textures.
2. Runners and gates
Runners are channels that direct molten plastic from the injection nozzle to the mold cavities, while gates are the entry points into the cavities. The design and placement of runners and gates are critical to ensuring proper material flow, minimizing waste, and avoiding defects like short shots or uneven filling.
3. Cooling systems
Efficient cooling reduces cycle time and prevents part defects such as warpage or shrinkage. Cooling systems are typically composed of channels through which coolant, such as oil or water, flows. The channels are strategically placed throughout the mold to ensure even temperature distribution. Proper cooling system design significantly impacts part quality and production speed.
4. Ejector systems
After the part has cooled and solidified, the ejector system removes it from the mold. This system typically consists of ejector pins or plates that push the part out without causing damage. The timing and force of the ejection process must be carefully controlled to avoid part deformation and minimize scarring.
Together, the mold type and design of its components play a significant role in determining the production speed, efficiency, quality, and cost-effectiveness of the injection molding process.
Managing Costs Without Compromising Tool Quality
Several factors, including mold material, mold complexity, and expected production volume, influence tooling costs. However, cost-effective solutions can be found without compromising quality. Listed below are some methods for managing injection molding tooling costs:
- Material choices: Consider the type of material that will be used for the mold. Opt for aluminum rather than steel for low-volume runs to reduce costs significantly.
- Simplifying mold design: Reducing unnecessary complexities like undercuts and large features in the mold can decrease manufacturing time and cost.
Injection Mold Tooling Materials: Optimizing Durability and Performance
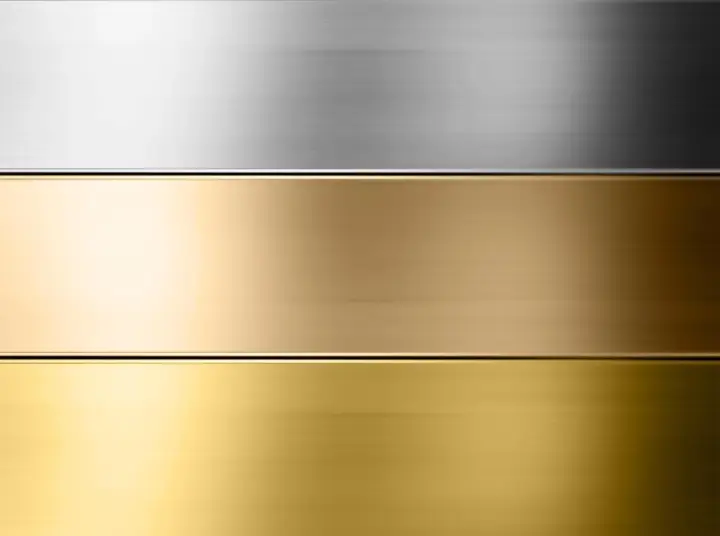
Mold materials greatly influence durability, wear resistance, and the total production volume the tool can handle. Material selection is also an important factor in injection molding costs. Common material choices for injection molding tooling include:
Steel
Injection molding fabricated from steel is excellent for long-term, high-volume production. Steel molds are durable but typically more expensive than other options. There are different grades of steel that vary in cost and durability, such as:
- P-20: A pre-hardened, high-quality tool steel that’s a good choice for a general-purpose mold. With a moderate hardness, it is known for its machinability, polishability, and versatility.
- NAK80: A pre-hardened, high-performance tool steel with excellent wear resistance and dimensional stability. Its higher hardness level makes it well-suited for high-precision molds and longer production cycles.
- 738h: A pre-hardened steel with a slightly higher hardness than P-20 but lower hardness than NAK80. It provides a balance of machinability and strength, making it a good option for medium to high-volume production.
Aluminum
This lightweight material is easier and quicker to machine, which makes it cost-effective for low-volume or prototype production. However, aluminum injection molds are less durable than steel molds and have a shorter lifespan.
Brass
Known for its excellent thermal conductivity, brass is sometimes used for specialized tooling applications.
Surface treatments and coatings such as nitriding and physical vapor deposition (PVD) enhance the durability and lifespan of a mold by improving wear resistance and reducing the chances of tool corrosion. These are significant factors influencing the lifespan of injection molding tools.
Designing for Precision: Best Practices in Tooling Design
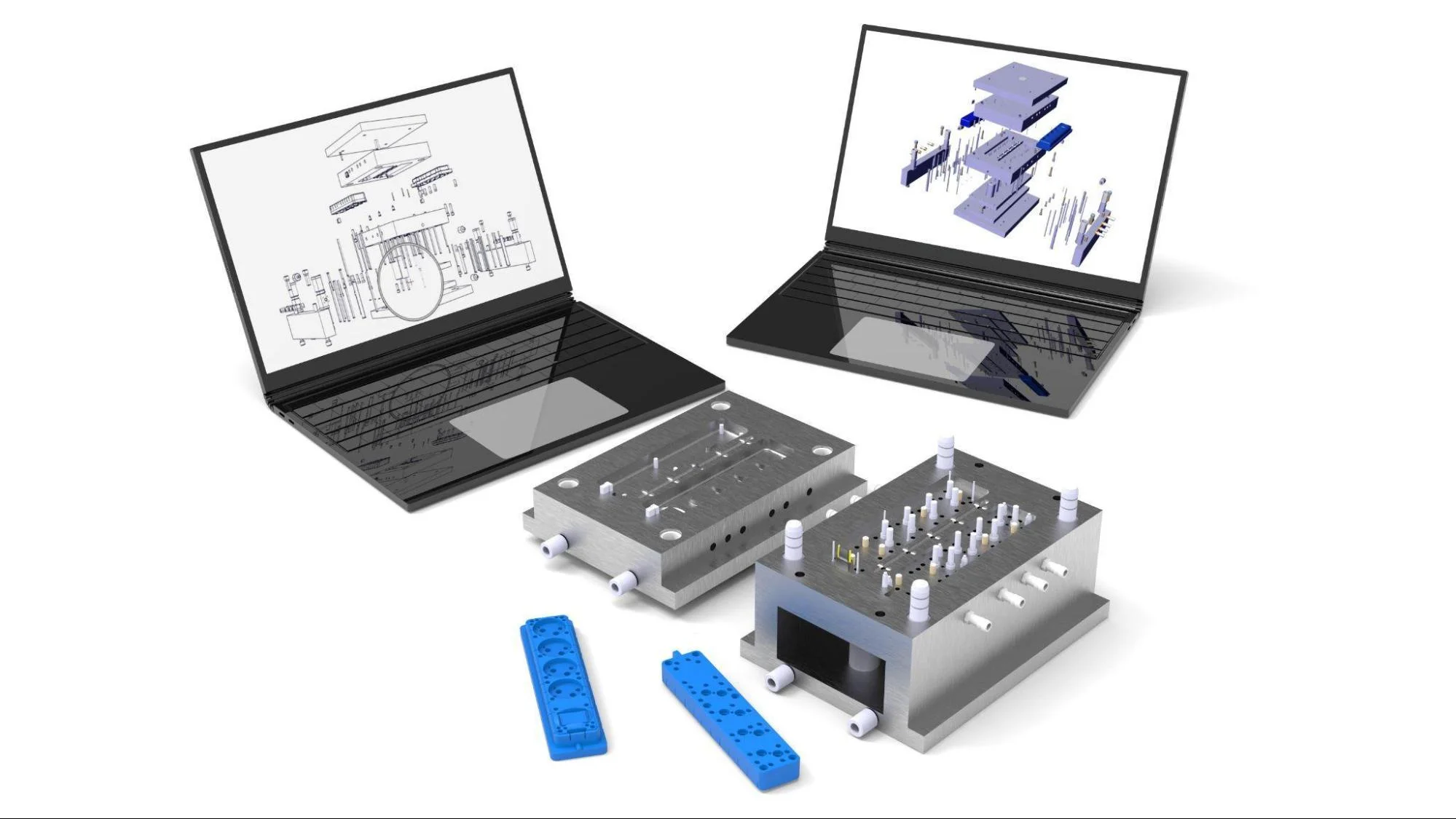
Tooling design in injection molding is a critical factor that determines part quality, production efficiency, and the overall success of the manufacturing process. A well-designed tool ensures that the part meets all specifications, minimizes cycle times, reduces waste, and prevents defects. To achieve this, designers must pay close attention to several critical aspects of the tooling process, including:
Tooling CAD and simulations
Computer-aided design (CAD) software allows designers to visualize the mold, simulate plastic flow, and make necessary adjustments early in the design phase. Simulations help predict how molten plastic flows into the mold, cools, and solidifies. This is crucial for identifying potential issues such as air traps, uneven cooling, or improper material distribution. By optimizing the mold flow through simulations, designers can reduce the risk of defects like warpage, sink marks, or short shots before the mold is even manufactured. Early identification of these issues helps to save time and costs associated with mold rework or production downtime.
Cooling line placement
The placement of cooling lines is vital to ensure that heat is removed from the mold as uniformly as possible. Uneven cooling can lead to warpage or distortion, especially in larger or more complex parts. Proper cooling line design involves strategically positioning channels within the mold to achieve uniform temperature distribution across all areas of the part. The cooling system must also be optimized to reduce cycle times without compromising part quality. The faster the mold cools, the sooner the part can be ejected, and the next cycle can begin, which increases production efficiency.
Molding pressure and tight tolerances
Proper pressure ensures that all areas of the mold are filled, which is especially important for parts with complex geometries or fine details. However, applying too much pressure can lead to flashing (excess material at the edges), while too little pressure can result in short shots (incomplete mold filling). Designers must carefully balance injection pressure with tight tolerances to ensure the part is accurately formed without defects. Achieving this balance requires careful control over the molding parameters, including temperature, pressure, and cooling rates, to ensure that the final part meets all dimensional and quality requirements.
By focusing on the critical practices described above, designers can create tools that produce high-quality parts efficiently and cost-effectively. Download our design stack to learn more about designing for injection molding and tooling.
Tooling Manufacturing Process: From CAD to Finished Injection Mold
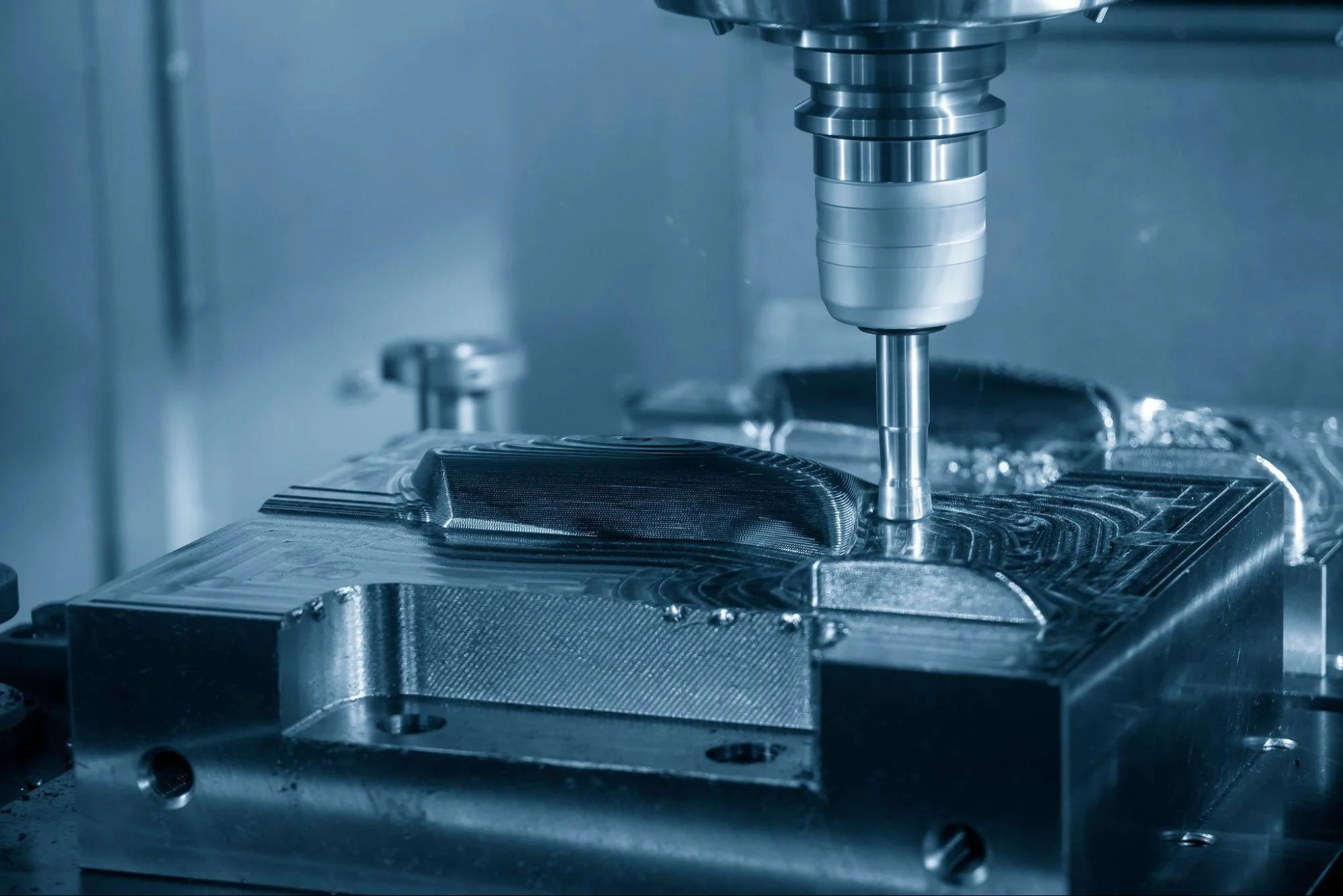
Once the tooling design is complete, the mold manufacturing process follows these general steps:
- CNC machining: Precision machining using 3, 4, or 5-axis machining is used to create the mold cavities to accurately replicate the part’s design based on the CAD model.
- Electrical discharge machining (EDM): This process occurs after conventional machining to create intricate details and features in the mold that are difficult to achieve with traditional machining methods. Features like engravings, runners, undercuts, or features with tight tolerances as small as +0.002″ can be cut with EDM.
- Finishing: After machining, the mold surfaces undergo polishing or texturing, depending on the required surface finish for the final part.
Together, these essential steps create a streamlined manufacturing process that ensures precision and high-quality outcomes.
Injection Molding Tool Validation and Testing
Before a mold goes into mass production, rigorous testing and validation are necessary to ensure it meets the required specifications. Listed below are two ways injection molding tooling is validated:
- Design validation: Before the tool is fabricated, computer simulations often check for potential design flaws, such as air traps, improper flow, or cooling inefficiencies.
- Test shots: Once fabricated, early production trial runs (test shots) are conducted. The optimal injection molding parameters are established during this process to help identify and correct issues related to part defects, mold flow, or cooling.
Manufacturers reduce the risk of production delays, costly rework, and defective parts by validating and testing tooling early.
Life Cycle and Maintenance of Injection Molding Tooling
Proper maintenance is crucial for extending the life of a mold and ensuring consistent production and product quality. Below are some items to consider for the maintenance of injection molding tooling:
- Cleaning and inspections: Regular cleaning and inspection prevent plastic material build-up in the mold and help identify signs of wear or damage.
- Repairs: Proactive repairs, such as recoating surfaces and replacing worn parts like ejector pins, springs, or mold inserts, help extend tool life and improve process repeatability.
- Monitoring wear: Keeping track of wear over time helps anticipate when maintenance is needed. This helps reduce unexpected downtime during long production runs.
Specialized Tooling Solutions: Overmolding and Complex Geometries
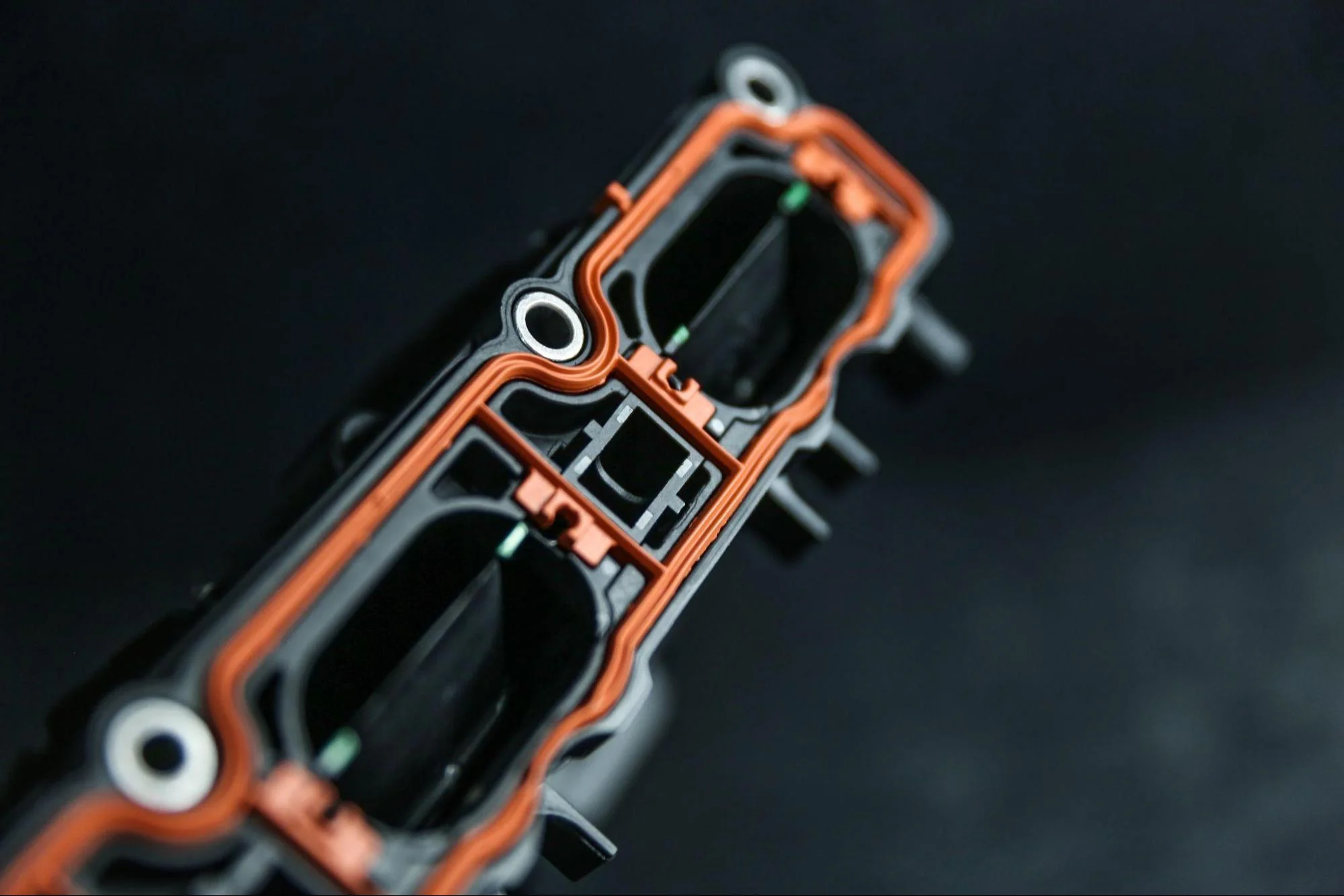
Certain injection molding projects involve complex production requirements that demand specialized tooling solutions. These advanced techniques allow manufacturers to create multi-material parts, integrate various components, or achieve complex or hollow geometries.
Overmolding
Overmolding combines two or more materials in a single part by injecting one material over or around another. This technique often adds ergonomic grips, protective layers, or multifunctional elements to a base component. Overmolding creates parts with enhanced functionality, durability, and aesthetics when executed properly.
Another type of overmolding is two-shot molding, or double-shot molding, when two materials are combined in one injection operation. This method typically has a higher upfront tooling investment but greater efficiency and lower costs for high-volume production.
Insert molding
Insert molding integrates non-plastic components, such as metal or electronics, into a plastic part during the injection molding process. The insert (e.g., a metal thread or electrical contact) is placed in the mold, and molten plastic is injected around it, encapsulating the insert and forming a single cohesive part. This method is commonly used in applications like medical devices, automotive parts, and electronics whenever metal components need to be combined with plastic.
Three-plate mold
Three-plate molds add an extra plate for more design flexibility and gating options. They’re often chosen for parts with highly cosmetic surfaces, thin walls, or uniform material distribution, as the gating flexibility helps achieve a uniform flow and appearance.
Unscrewing mold
Unscrewing molds contain threaded cores or cavities for parts requiring internal or external threading. The mold has mechanisms to unscrew the part, making it possible to produce threaded components.
Gas-assist
Gas-assisted molding uses gas (usually nitrogen) injected during molding to create hollow sections in thick areas. It reduces material use and can make the part lighter while maintaining strength.
Rotational mold (Rotomolding)
Rotomolding uses centrifugal force to distribute material evenly in the mold, typically for large, hollow parts. It is an alternative method to blow molding for these types of parts.
Specialized tooling solutions expand the range of possibilities in plastic part design and provide opportunities to reduce costs and improve performance in complex assemblies.
Troubleshooting Common Injection Molding Defects with Tooling Solutions
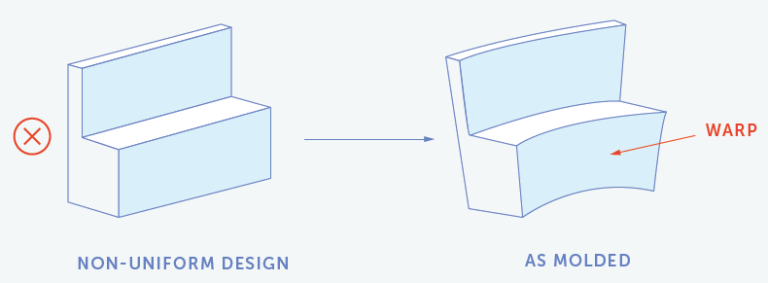
Tooling design and maintenance significantly influence the occurrence of injection molding defects. Understanding these defects is essential for improving production efficiency and product quality:
- Flash: Excess material at the edges of a part. This often occurs due to mold misalignment, wear, or excessive injection pressure. To mitigate flash, ensure precise mold alignment, and maintain mold integrity while controlling injection parameters.
- Warpage: Occurs when parts deform after cooling, usually due to uneven cooling. Inadequate cooling channel design can cause certain areas to cool at different rates, which leads to internal stresses that need to be adequately alleviated. Optimizing cooling line placement and monitoring material properties can help prevent warpage.
- Sink marks: Depressions on a part’s surface are typically caused by insufficient cooling or packing pressure. To avoid sink marks, ensure proper cooling times, adjust injection pressure, and maintain uniform wall thickness in part design.
- Short shots: This happens when the mold cavity isn’t filled and is often due to insufficient injection pressure or material flow. Optimizing injection pressure and improving runner and gate design can help prevent this defect.
Addressing these defects through tooling adjustments and maintenance enhances production efficiency and part quality. Regular inspections and proactive design improvements are crucial for minimizing issues like flash, warpage, sink marks, and short shots.
Effective Injection Molding Tooling with Fictiv
Fictiv is a custom manufacturing operating system that simplifies and accelerates the sourcing and supply of mechanical parts for high-volume production. With an intelligent platform and exceptional operational talent, it connects users to a global network of vetted partners, ensuring fast and high-quality manufacturing from quote to delivery.
Companies can achieve substantial savings by carefully balancing initial investment with long-term efficiency without sacrificing tool performance. Fictiv helped Purcell with their injection molding production and supply chain needs to get to market 4-6 months faster than expected and gain an additional $100,000 in revenue.
If you’re tasked with sourcing and supplying mechanical parts, create an account and upload your part designs to get an instant quote and free DFM feedback today.