Time to read: 5 min
Injection molding is a multi-step process that injects molten plastic into a metal tool called a mold. The plastic material then cools into a solid and the part is ejected. This process is easy to understand, but part designers, mold makers, and injection molders all need to speak the same language. Fictiv’s Injection Molding Glossary defines the terms you need to know.
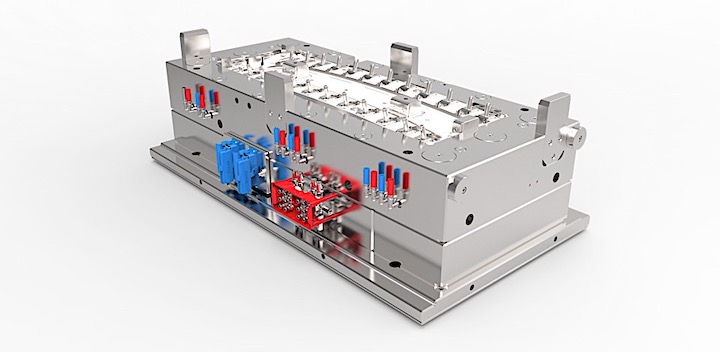
Barrel – The part of the injection molding machine where the plastic resin is heated and mixed.
Boss – A round protrusion in a part. Bosses provide a channel for a screw and are used to aid the assembly of molded parts.
Cavity – The void or space inside the mold where molten plastic is injected.
Clamping Force – The force that is applied to keep the mold closed during injection and cooling.
Cooling Time – The amount of time it takes for the injected plastic to cool and solidify.
Core – The bottom half of the mold. Typically, injection molded parts are ejected from the core.
Core-out – Part features that reduce or eliminate plastic in thicker areas. These pockets produce uniform wall thickness, reduce part weight, and/or reduce the chance of warping.
Cycle Time – The total time that is required for a complete injection molding cycle (i.e., injection, cooling, and ejection).
Draft Angle – A slight angle or taper on a part’s vertical surfaces. Draft angles facilitate part ejection and improve tooling shutoffs so that post-molding machining is not required.
Ejector Pins – Pins that push against the surface of the molded part and release it from the mold after the part has cooled and solidified.
Flash – Excess material that escapes through the parting line between the mold’s core and cavity. Flashing, as it’s also known, produces a thin, unwanted film on edges of parts.
Gate – An opening through which molten plastic is injected into the cavity from the runner.
Gate Vestige – A small witness mark that’s left on the molded part after a gate is removed.
Hand Load – A feature inside of a mold that’s used to produce an undercut. Hand loads are ejected, manually removed, and then re-inserted into the mold for the next shot.
Injection Molding – The process of making plastic parts by injecting molten material into a cavity within a multi-part mold. The molten material cools, becomes a solid, and is ejected.
Injection Unit – The section of the injection molding machine that melts and injects plastic into a mold.
Insert – This term can have two different meanings in injection molding. 1) A part, such as a threaded fastener, that is inserted into the mold and then overmolded with plastic. 2) A removable section of a mold that supports design updates, deeper features, or the venting of challenging areas.
Lifter – An injection mold mechanism that pushes up and at an angle while a part is ejected. Lifters move parts away from undercuts and support part removal.
Mold – The tool that’s used to produce injection molded parts. Molds include the core, cavity, material channels, cooling channels, sprues, runners, gates, and ejection mechanisms.
Overmolding – The process of molding a material over a previously molded material.
Resin – The raw material used in injection molding, usually in the form of pellets.
Ribs – Thin, blade-like support structures that provide additional walls or boss strength without excessive thickness, or that help to reduce warping.
Runner – A channel in a mold that directs molten plastic from the sprue to the gates.
Screw – A barrel component that moves plastic forward and mixes it as it melts. Screws also provide shear, which aids in the melting of the plastic.
Shear – Friction inside of a mold that is induced by speed and pressure. Shear helps maintain the plastic melt while the cavity fills.
Short Shot – An injection that fails to fill a mold cavity completely. Short shots can be caused by low shear, improper venting, or improper mold parameters and settings.
Shot Size – The maximum amount of molten plastic that the injection unit can deliver in one injection (shot).
Shrink Rate – A measure of how much a plastic shrinks as it cools. The shrink rate of each thermoplastic is tested and measured, and mold designers need to consider this amount in order to produce tools that produce parts with proper size once cooled.
Side Action – Any slide, lifter, or hand load that is used to release an undercut from an injection mold.
Sink Marks – A surface defect on an injection molded part that has a sunken or dimpled appearance. Typically, sink marks are caused by nonuniform walls, extra-thick walls, or added thickness at rib/boss intersections.
Slide – An injection mold mechanism that releases undercuts and allows parts to eject freely. When the mold is opened, a slanted pin removes the slide.
Sprue – The primary cone-shaped channel through which molten plastic is introduced into the mold from the injection unit.
Sprue Bushing – The part of the injection molding machine that connects the injection unit to the mold sprue.
Steel Safe – The process of leaving excess metal on a mold to support potential changes to part features or tolerances. After the results of initial sampling are known, a mold maker can remove this excess metal instead of using inserts or welding, both of which add costs.
Thermoplastic – A plastic resin that can be melted and solidified multiple times without significant degradation.
Thermosetting Plastic (Thermoset) – A plastic resin that, once molded and cured, cannot be melted and reshaped because of a chemical reaction that leads to the plastic’s solidification.
Undercut – A feature on a molded part that prevents its easy ejection from the mold. Examples include holes on vertical walls and snap features on the inside of part walls.
Venting – Small, very thin channels within a mold that allow air to escape from the cavity as it is replaced with plastic. Vents ensure a good molded part without shorts or burnt material.
Warpage – The deformation or distortion of a molded part because of uneven cooling or other factors.
This glossary is comprehensive, but you might hear some other terms during your next injection molding project. For information and assistance, ask Fictiv. Our engineers are ready to help and can provide the design for manufacturing (DFM) expertise that you need to succeed. To get started, create a Fictiv account and upload your part drawing.