Time to read: 6 min
Injection molding flash, or flashing, is excess plastic that forms on the surface of injection molded parts. Although some amount of flash is considered to be a normal part of the plastic injection molding process, excessive flash can mar the surface finish of parts or interfere with part seating, mating, or assembly.
In this article, you’ll learn about the causes of flash and how toolmakers and injection molders can identify and address parts flashing. Fictiv works with a global network of Manufacturing Partners who have the toolmaking and injection molding expertise you need for high-quality plastic parts with low levels of flash.
Keep reading to learn more about injection molding flash, or create a Fictiv account to request a quote for your next project. When you do, you’ll get design for manufacturing feedback (DFM) that’ll help optimize your design to minimize flashing — and you can download our free guide for even more design insights.
Free Injection Molding Design Guide
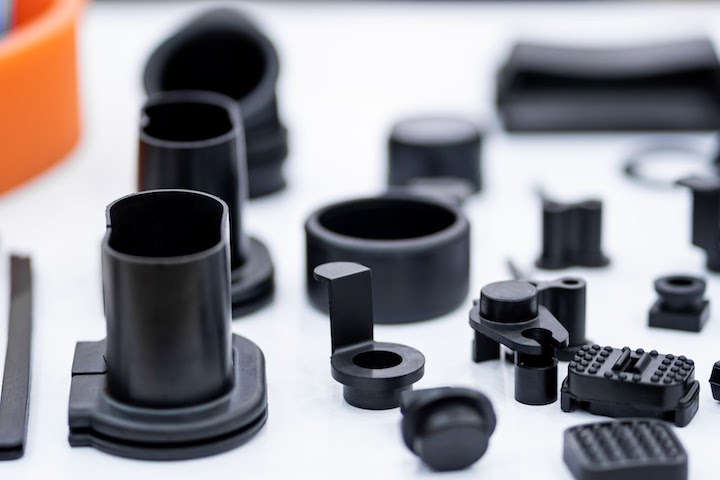
What Causes Injection Molding Flash?
The causes of flash in injection molding are numerous and include:
- parting line mismatches
- improper venting
- low clamping pressure
- low viscosity
- uneven flow
Some of these issues are related to tooling, but others are a function of processing.
Parting Line Mismatches
Flash usually occurs when material is forced out of the mold cavity at the parting line, the point where the two halves of an injection mold separate to release the plastic part. During the injection step in the molding process, these two halves come together and remain closed. If the halves do not align properly, molten plastic escapes through gaps and produces flash.
During the tool making process, mold makers seek to prevent flash through a process known as mold fitting. By adjusting the mold halves so that they come together completely, and by aligning the halves as necessary, a skilled toolmaker can eliminate gaps that might otherwise allow molten material to seep through.
Over time, however, tooling wears out. Pressure can deform the metal surfaces of plates, and mold cavities that are worn won’t fit tightly together. Complex part geometries can complicate mold closure, and contaminants such as dust, dirt, and residues can keep the halves of a mold from closing properly. In these situations, tooling can be cleaned and refit.
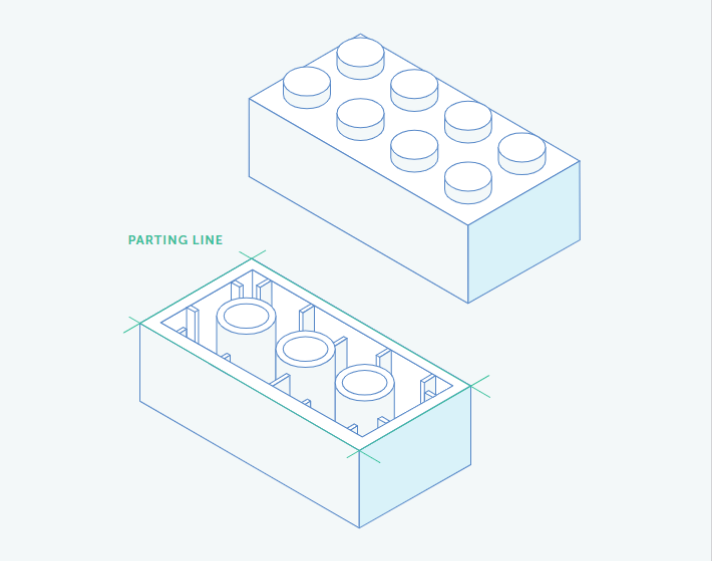
Improper Venting
Toolmakers cut vents into molds so that air can escape and molten plastic can fill the cavity completely. Without vents, air would become trapped and compressed, causing the plastic to burn. Vents are typically standard features with injection molds, but improper venting can still cause flashing.
Vents need to be large enough so that air is pushed out during injection but small enough so that molten plastic does not escape. The number of vents, depth of venting, and vent locations all are all important considerations. Venting also supports the injection molding process by reducing the injection pressure that is required so that the mold halves won’t separate.
Insufficient Clamping Pressure
Clamping pressure, a measurement of the force needed to hold the mold closed during injection, is related to flash formation. Pressure that is too high or too low can be problematic.
- If the pressure in the mold is greater than the clamping pressure of the injection molding machine, the two halves of the tool could be forced apart.
- If the clamping pressure isn’t high enough to resist this force, plastic may leak from the mold even if the two halves of the tool fit together well.
Low Viscosity and Uneven Flow
Processing conditions can also contribute to flash formation by causing plastics to flow too readily (low viscosity), or to fill the mold too rapidly. Examples of these processing conditons include melt temperatures that are too high, residence times that are too long, residual moisture from inadequate drying, and the excessive use of coolants.
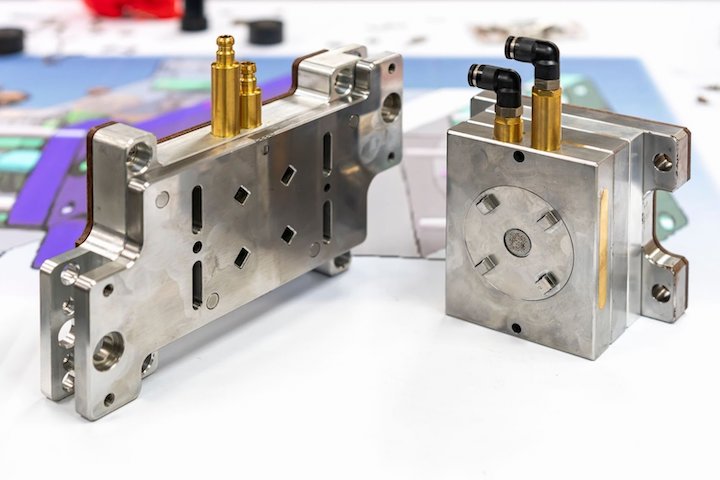
How to Troubleshoot Injection Molding Flash
In general, the industry standard for mold flash is less than 0.004” (0.10 mm). To put this in perspective, you wouldn’t feel anything sharp if you ran your finger along the edge of the part. Flashing that is 0.002” (0.05 mm) or less is possible, but it requires greater attention during tooling design, construction, and mold fitting. Lower levels of flash also increase tooling costs.
If your injection molded parts need these lower levels of flash, Fictiv recommends sharing your requirements during quoting and DFM. Typically, flash elimination is the responsibility of the molding partner. Some partners may propose trimming flash by hand, but that might not be the ideal solution. Hand trimming requires extra labor, and part-to-part variations may occur. Also, if flashing is excessive when the tool is new, the problem is likely to worsen as the tool wears.
If your parts have excessive flash, Fictiv recommends asking your molding partner to take some specific troubleshooting steps and address problems in these areas:
- parting line mismatches
- insufficient venting
- insufficient clamping pressure
- low viscosity and uneven flow
- mold deflection during fill
Parting Line Mismatches
Ask your molding partner to ensure that the two halves of the tool are aligned properly, and that there aren’t any gaps. This process is known as spotting, and it’s done by applying ink to one half of the tool and then closing the two halves together. By transferring ink to the other half of the mold, spotting reveals problems that require additional mold fitting. Blue ink is used in the United States, and red ink is used in China.
Insufficient Venting
If parts molded from new tools have excessive flash, ask your partner to confirm that your tool contains vents. Sometimes, factories may skip this step. If vents exist, find out if they are spaced 1” to 2” apart. Also, ask your molding partner if the vents are the proper depth since vent depth is a function of the plastic that is being molded. If your parts have been in production for awhile and flash is just now appearing, cleaning the vents may be the solution.
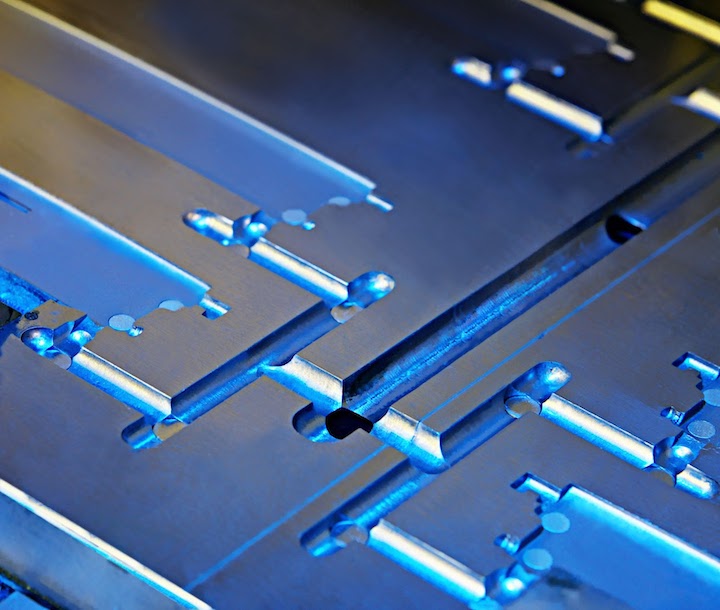
Insufficient Clamping Pressure
Injection molding has three stages: filling, packing, and holding. Flashing can occur during any of these three stages, so start by asking your molder to produce some fill-only parts. If the flash is excessive, ask your molder to check the press’ clamping tonnage and to clean any debris from the mold. Tonnage is the clamping force that the injection molding press can produce.
If flash occurs during the packing or holding stages, your molder may need to adjust the pack and hold pressure. During packing, additional material is injected into the mold to account for shrinkage and backflow. During the holding stage, the plastic material is kept at a pressure equilibrium until the gates are frozen and cooling beings.
Low Viscosity and Uneven Flow
Melt temperature is the temperature at which the solid plastic pellets that are used in injection molding melt while leaving the nozzle and entering the mold. Plastics manufacturers provide melt temperature as a range, but different plastics have different ranges. There may also be batch-to-batch variations among polymers that have the same basic formula.
Injection molders monitor melt temperatures carefully, but sometimes problems such as low viscosity and uneven flow occur. Because plastics that flow too quickly or unevenly can cause flash, Fictiv recommends asking your molding partner to verify that the melt temperature on the injection molding machine is within the range recommended by the material’s manufacturer.
Mold Deflection During Fill
Finally, flash can be caused by mold deflection during the fill stage. Generally, this type of tooling distortion is the result of clamping and cavity pressures. Ask your molding partner to check the dial indicators on the tooling’s platen. To prevent mold deflection, additional support hardware may be needed for the tool.
The Best Way to Address Injection Molding Flash
There are plenty of things that can go wrong and cause mold flashing, but a skilled partner can help you get it right. That’s why Fictiv, your operating system for custom mechanical parts, is the smart choice for your next plastic injection molding project. We have the resources and know-how to tackle flashing issues and deliver the quality injection molded parts you need. Create an account and get an instant quote today!