Time to read: 9 min
Advanced injection molding technologies and techniques are used for designing and manufacturing parts that have complex features, use high-performance materials, and/or leverage advanced features in molds, machinery, and equipment.
If you’re new to injection molding, Fictiv’s Injection Molding 101 is a great place to start. This article explores what you need to know about design for manufacturing (DFM), high-performance polymers, advanced mold design and tooling – and much more.
Fictiv provides DFM feedback along with a quick response to your request for a quote, so create a free account and upload your CAD file today.
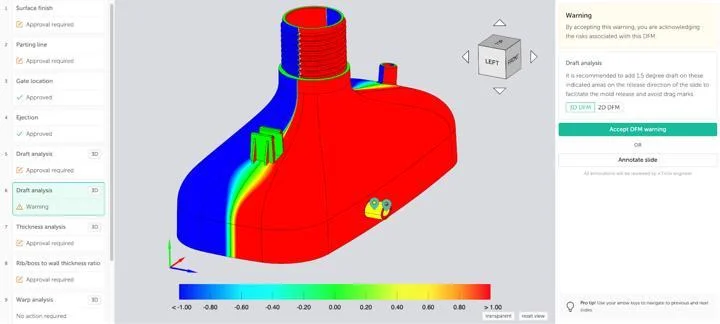
DFM in Advanced Molding
Design for manufacturing or design for manufacturability (DFM) is the process of designing parts for a specific manufacturing process to obtain the best possible outcome during production.
With injection molding, there are advanced considerations that go beyond basic part design guidelines. These features and processes include:
- Clips and snap fits
- Living hinges
- Bosses and stand offs
- Text and logos
- Overmolding and insert molding
Fictiv’s Injection Molding Design Guide covers the basics of DFM topics such as material selection, wall thickness optimization, and draft angles. Download it here.
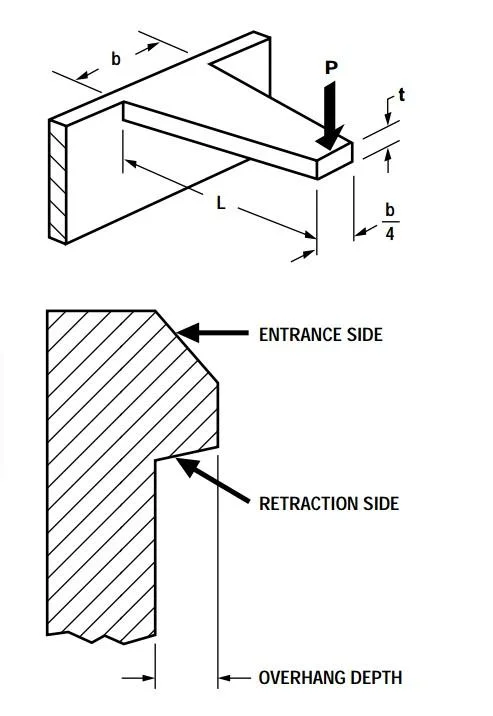
Clips and Snap Fits
Clips and snap fits secure the covers of products like tool sets and electronic devices. These flexible, hook-like features extend into and catch a slot or pocket on a mating part.
There are two ways to create clips and snap fits, depending on the part’s function, aesthetics, and overall design.
- Option 1: The tooling uses slides or lifters, mechanisms that release the part when the mold opens. Sliders are used with difficult-to-eject features on the part’s outer surface. Lifers are used with challenging features on the part’s inside surface.
- Option 2: The part design includes a pass-through hole to allow a sliding shutoff to form the feature. As its name suggests, a sliding shutoff slides into the mold to prevent material from flowing into the area with the hole.
Note that with Option 2, the designer must align the clip or snap fit with the direction in which the mold opens. In addition, extra draft may be required.
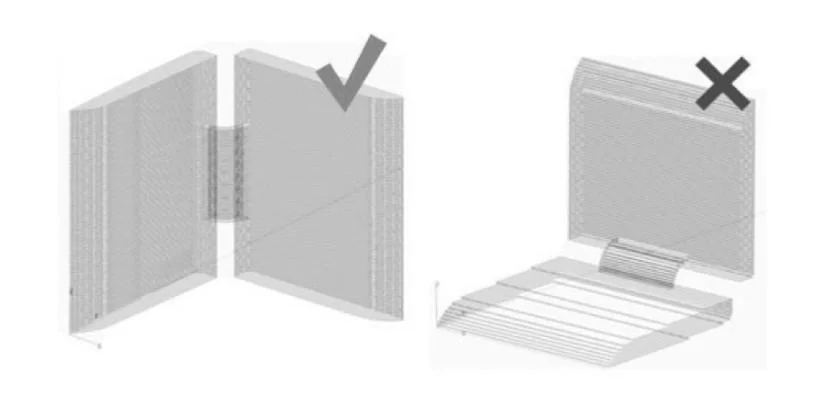
Living Hinges
Living hinges are another way to open and close molded containers. Material selection is key because the hinge must withstand many cycles. A stiff, strong plastic such as polycarbonate might be a good choice for a clip, but polypropylene is more flexible and, therefore, a better choice for a living hinge.
In addition, designers need to follow these best practices
- Add Generous Radii: This improves the flow through the hinge during molding and reduces stress concentrations during use.
- Include Shoulders: Shoulders create a flat recess, ensuring the hinge will bend in the center and that the part can deform enough so that the hinge has room to close.
- Use Thinner Hinges: A thinner hinge is more flexible. A thicker hinge may seem more robust, but the greater elongation can cause the material to exceed its yield point.
- Divide Long Hinges: To improve hinge life, design hinges that are longer than 6 inches in two or more parts.
- Experiment with Thickness: You may have to experiment with multiple thicknesses to strike the right balance between a hinge that feels stiff and one that feels floppy.
Bosses and Stand Offs
Bosses and standoffs are molded-in features that can accept a self-tapping screw, pin, or insert for part assembly or mounting. To avoid ejection problems, a designer may need to apply extra draft to these features. If a boss or standoff is especially tall, a deeper mold is required. In addition, DFM may add vent holes to avoid injection molding defects like short shots.
Text and Logos
Advanced injection molding supports the use of text and logos on parts. For best results, use a non-serif font large enough so that all the letters are visible. Raised text is easier to mold and read than sunken text.
Also, consider placing text closer to the mold’s parting line and farther from tall features. With most injection molded materials, it’s best to make the text face the direction of mold pull.
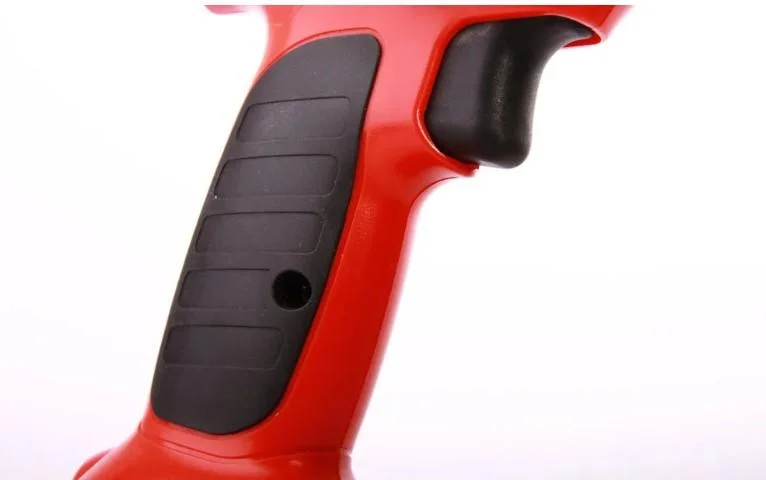
Overmolding and Insert Molding
Overmolding and insert molding are advanced injection molding techniques for bonding parts together seamlessly and without fasteners.
- Overmolding molds one part from one material and then molds another material over the first molded part. A toothbrush with a hard handle and soft grip provides an example
- Insert molding places a pre-fabricated, pre-formed, or previously molded part into a mold and then molds it over with a different material. A metal-bladed screwdriver is an example.
When designing overmolded parts, make the overmold’s thickness less than or equal to that of the overmolded part. In addition, avoid making the overmold so thick it could shrink away from the overmolded part during cooling.
When designing insert molding parts, use inserts that are smaller than the molded parts in which you plan to embed them. To control costs, use standard inserts instead of ones that require custom machining. Also, avoid smooth inserts in favor of knurled ones.
High-Performance Materials for Advanced Molding
High-performance materials for advanced injection molding are used in applications that require exceptional mechanical, thermal, or mechanical properties. The table below describes some of these filled materials, high-performance thermoplastics, and engineered resins.
Material | Properties | Applications |
Glass-Filled Nylon | Enhanced stiffness, strength, and dimensional stability compared to unfilled nylon, while maintaining good wear resistance. | Automotive parts, industrial machinery components, and consumer electronics. |
Liquid Crystal Polymer (LCP) | High mechanical strength, excellent dimensional stability, low moisture absorption, and good chemical resistance. LCP also has low warpage and shrinkage. | Microelectronics, connectors, and high-precision components. |
Polyamide-imide (PAI) | High mechanical strength, excellent wear resistance, and thermal stability. PAI is one of the strongest and stiffest thermoplastics available. | Bearings, bushings, and other high-stress components. |
Polyaryletherketone (PAEK) | High mechanical strength, excellent chemical resistance, and can withstand high temperatures. Similar to PEEK, but with slightly different properties depending on the exact composition. | Medical devices, aerospace, and oil & gas industry components. |
Polybenzimidazole (PBI) | Outstanding thermal stability, exceptional wear resistance, and excellent mechanical properties at high temperatures. | High-temperature seals, insulators, and aerospace components. |
Polyetheretherketone (PEEK) | High strength, excellent chemical resistance, and outstanding thermal stability. PEEK can withstand continuous use in temperatures up to 250°C (482°F). | Aerospace, medical devices, and automotive components. |
Polyimides (PI) | Exceptional thermal stability and can withstand temperatures up to 300°C (572°F). Good mechanical properties and excellent dielectric properties. | Aerospace, electrical insulation, and high-performance coatings. |
Polyphenylene Sulfide (PPS) | High temperature resistance, good dimensional stability, and excellent chemical resistance. | Automotive parts, electrical components, and industrial applications. |
Thermoplastic Polyurethane (TPU) | High elasticity, excellent abrasion resistance, and good chemical resistance. TPU is also highly versatile, available in a range of hardness levels. | Medical devices, automotive components, and industrial parts. |
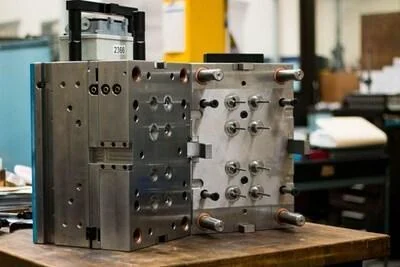
Advanced Mold Design and Tooling
Advanced injection molding uses complex mold designs to create intricate, high-precision parts with tight tolerances and challenging geometries. Features and techniques can also be used for higher part volumes, fewer injection molding defects, and more efficient production.
- Multi-cavity molds produce two or more identical parts in a single cycle. Their design ensures uniform filling and cooling across all cavities, each of which produces a part.
- Family molds are a type of multi-cavity mold where each cavity produces a different type of part. They’re used for complex assemblies like multi-part connectors.
- Stack molds have multiple levels of cavities. They can increase the number of parts produced per cycle without increasing the mold’s footprint.
- Hot runner systems use a heated manifold to deliver molten material directly to the mold’s cavities. Because these runners, or channels, don’t have to solidify before they’re moved, hot runner molds speed cycle times and reduce material waste.
- Conformal cooling systems incorporate cooling channels into the mold that conform to the shape of the part. This promotes more efficient and uniform cooling, which helps to reduce part defects.
- Collapsible cores are used to create internal undercuts that would otherwise complicate part ejection. With these molds, the core collapses or retracts after molding is complete.
- Rotational or indexable cores enable multi-shot molding and complex part geometries. During the injection molding process, parts are rotated or indexed within the mold.
- Side actions and lifters are mechanisms that move within the mold to create features like undercuts, holes, or other complex details.
Virtual Prototyping and Advanced Simulation
Advanced injection molding can use virtual prototyping and simulation software for molding analysis and optimization. There are cost-saving benefits to using these techniques before metal molds are machined and physical prototypes are produced. Part designers can also accelerate product development while iterating and experimenting more rapidly.
Virtual Prototyping in Injection Molding
Virtual prototyping involves creating a 3D CAD model of both the part and the mold. This model includes all the details of the part’s geometry, as well as the mold’s structure, including cavities, cooling channels, and gate locations. CAD software such as SOLIDWORKS and Autodesk Inventor can be integrated with simulation tools for further analysis.
Simulation Software for Molding Analysis
Simulation software is used to model and simulate the injection molding process for a part design with a specific tool. Software like Autodesk Moldflow, Moldex3D, and SIGMASOFT can provide insights about how a material will flow into a mold, cool, and solidify. Designers and engineers can use this information to predict potential defects and modify part or tool designs as necessary.
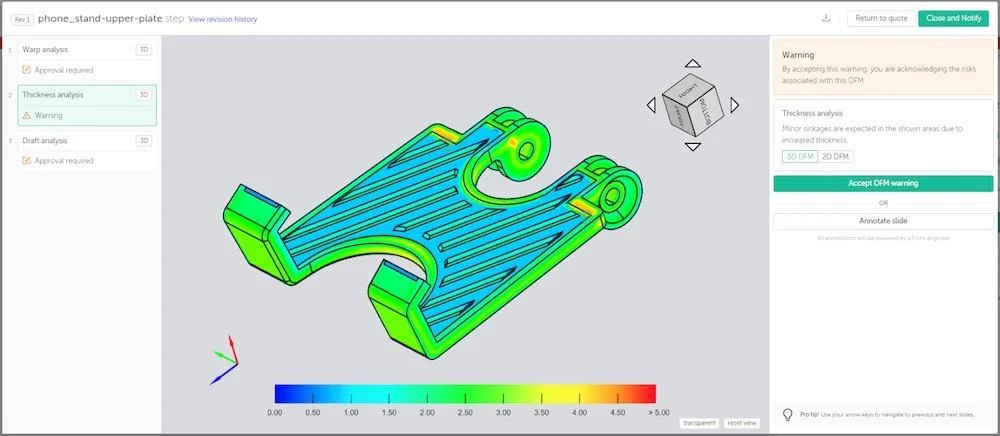
Advanced Injection Molding Technologies for Parts Production
Whether it’s for prototyping, low-volume or bridge production, or high-volume manufacturing, advanced injection molding supports the use of automation and robotics, process optimization and control, and quality control.
Automation and Robotics in Advanced Injection Molding
Advanced injection molding can use automation and robotics independently or in combination.
- Automation uses programmable systems such as computers to control part handling and other aspects of the injection molding process
- Robots are also programmable, but they can complete injection molding tasks such as loading inserts or unloading parts either autonomously or semi-autonomously.
- CNC robotics, a technology that uses automated CNC equipment with industrial robots, combines the consistency of computer-numeric control (CNC) with the flexibility of robots.
Advanced Process Optimization and Control
Advanced process optimization and control is used to fine-tune the injection molding process for maximum efficiency, quality, and consistency. By improving cycle times, material usage, energy consumption, and product quality, injection molders can achieve the best possible outcomes.
- Scientific injection molding uses advanced sensors and software to establish optimal process parameters before production begins.
- Real-time monitoring and control, or in-process monitoring, uses sensors and software to track key process parameters during production.
- Closed-loop control systems automatically adjust process parameters based on feedback from sensors to improve consistency and reduce the risk of defects.
Machine learning algorithms, Internet of Things (IoT) devices, and artificial intelligence (AI) that leverage data analytics can also be used to optimize process parameters.
Advanced Quality Control in Injection Molding
Machine vision systems, automated quality control, and real-time defect detection are also used to ensure that injection molded parts are produced without defects. With advanced injection molding, the focus is on preventing defects rather than detecting them after the fact. By contrast, traditional approaches to quality depend upon the inspection of manufactured parts.
Statistical process control (SPC) is a quality control method that uses statistical techniques to identify problems and find solutions. Injection molders can use SPC to meet a customer’s requirements for quality, lead times, tolerances, delivery, and cost. The actionable data that a molder receives can also help avoid bottlenecks during production.
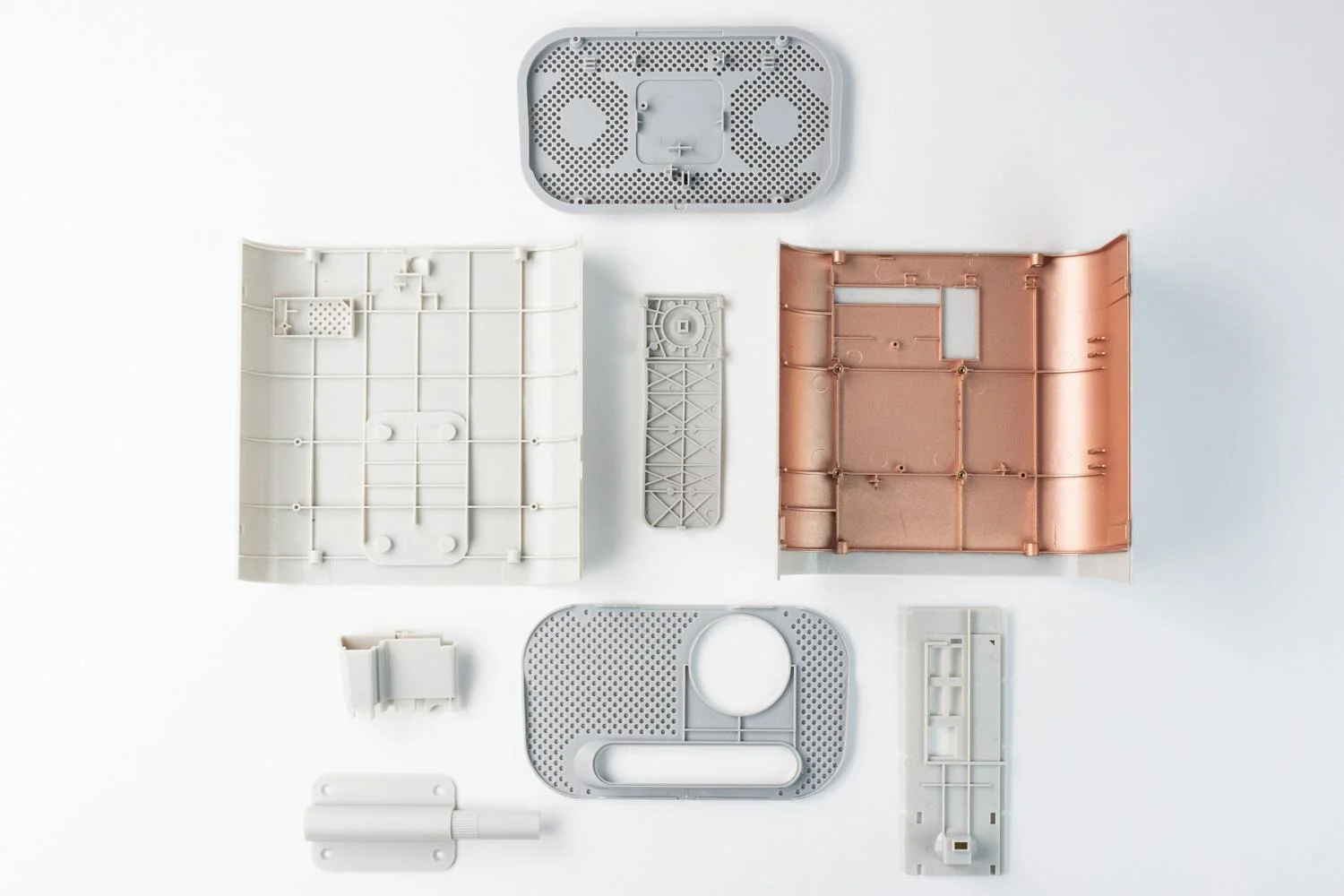
Current Applications and Trends in Injection Molding
Today, advanced injection molding is meeting the needs of designers who are bringing innovative medical devices, automotive components, and consumer electronics to market. It also supports emerging technologies such as augmented reality (AR) and supporting design trends in lightweighting and environmental sustainability.
Case Study: Lampix
Lampix is an augmented reality projector with a lamp-like form factor that can transform any flat surface into a dynamic AR display. The design team includes a Massachusetts Institute of Technology (MIT) alumnus with three Master’s degrees, but Lampix still welcomed Fictiv’s DFM feedback during the quoting process for a low-volume run of injection molded parts.
The Lampix parts were complex and required tooling that could support recessed undercuts. In addition, this advanced injection molding project needed a special UL 94 flame-rated plastic. Two of the parts also required a specialized coating against electromagnetic interference (EMI). Fictiv delivered T1 samples in just 21 days and 500 injection-molded beta units in four weeks.
As a member of the Lampix team explained, “Fictiv has great pricing, great communication and they provide you with everything you need in terms of manufacturing and design feedback.”
Environmental Sustainability and Advanced Injection Molding Machines
The future of advanced injection molding is also bright because of its support for environmental sustainability. Increasingly, product designers are concerned about waste reduction, energy consumption, and the environmental impact of molded products.
Advanced injection molding can use recycled materials and biodegradable and bio-based plastics, but it can also optimize its use of petroleum-based plastics. Reducing part thickness, eliminating unnecessary features, and selecting plastics with the best performance-to-weight ratio can all help.
Advanced injection molding machines are also part of a more environmentally sustainable future. Molders are investing in 100% electric equipment with variable speed drives and insulation barrels. With both new and existing equipment, automation and other technologies are also improving waste reduction.
Choose Fictiv for Advanced Injection Molding
Fictiv works with a network of global manufacturing partners who leverage the latest advances in molds, machinery, and equipment. Our engineering experts can help you design parts with complex features and with high-performance materials if you need them. Plus, you’ll love how you can get T1 samples in just a few weeks. Are you ready to get started? Create a free account and upload your CAD file today.