Time to read: 8 min
Note: This article is based on a previously published version by Sylvia Wu and has been updated to reflect Fictiv’s current capabilities, as well as 2022 innovations.
When designing a product for the consumer market, industrial usage, or aerospace industry, how the product looks, feels, and functions is critical. Color, material and finish (CMF) are all characteristics that must be defined and carefully considered to ensure your product has longevity and is appealing to consumers and end users.
At large, design-centric hardware companies, CMF designers work alongside industrial designers and product design engineers to ensure that the product’s chromatic and tactile identities are on brand and in vogue. On smaller teams, a lone industrial designer or design engineer often takes on this role as part of the design process.
During the design phase, CMF is often communicated with stakeholders via renderings and descriptive language. However, for appearance models or production units, CMF needs to be expressed more precisely so that there’s no room for misinterpretation. In this article, we’ll introduce some terms you can use for lean, effective CMF communication as well as best practices for relaying CMF.
Pro-Tip: Ensure that your CMF requirements are clearly called out, and it’s best practice to call these out on the engineering drawing and/or bill of materials. I have seen many companies relay important CMF details in purchase orders where they get overlooked.
Color
You may not be an expert on color. For example, did you know that the sky is blue because light rays within the shorter wavelength have a tendency to scatter more (a phenomenon known as Rayleigh scattering)? Violet and blue light have the shortest wavelengths out of all colors, which is why the sky appears blue during the day.
There is literally a whole world of color out there, and to define those colors, we use color model systems. A color model system helps us to designate or define a color with a set of numbers and/or letters. For example, the RGB color model is popular when working with digital designs. The RGB color model, like many color model systems, is based on Color Theory. At a broad level, Color Theory is the science of color and human perception of color, as well the harmonious utilization of multiple colors.
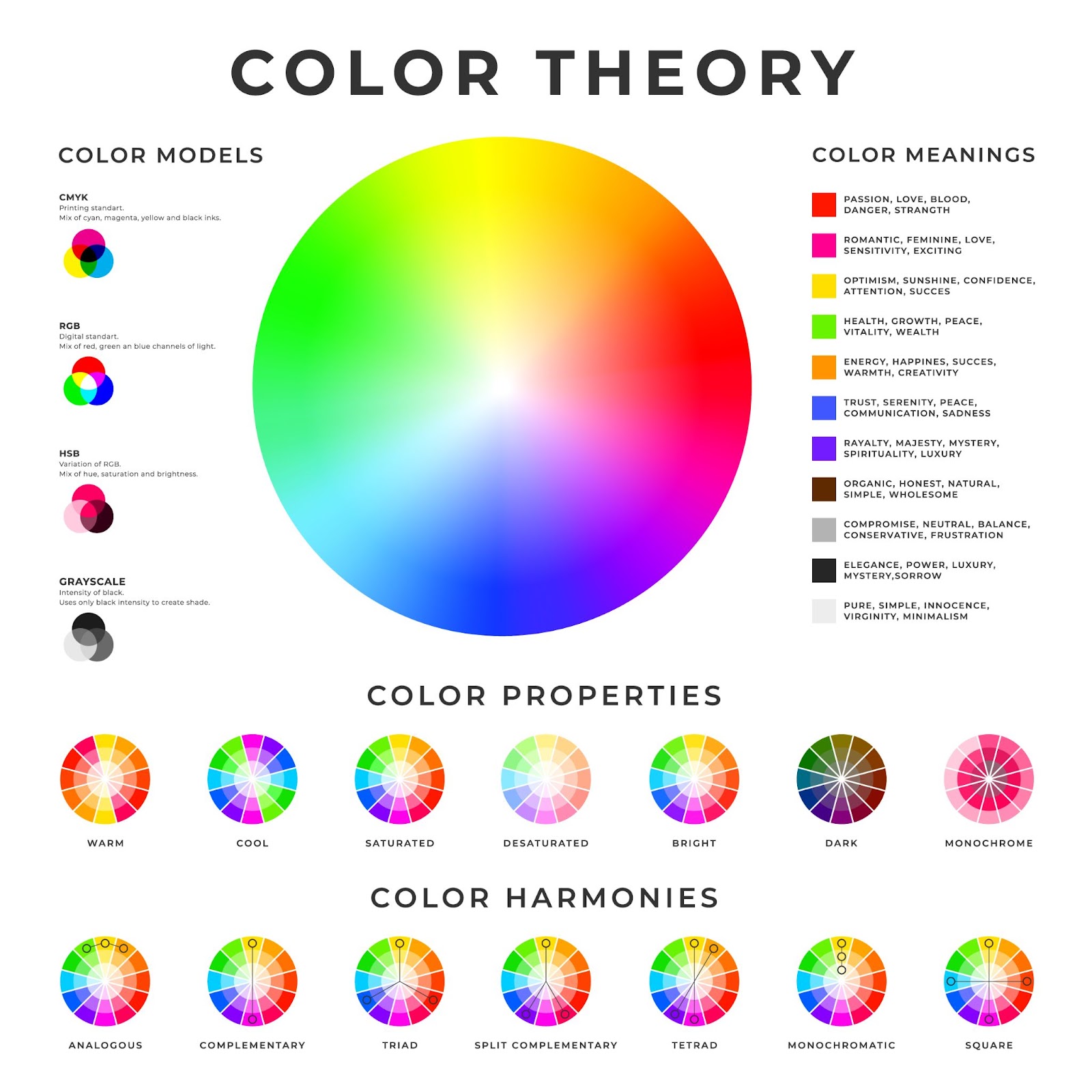
Here is a brief overview of some of the most popular color model systems for defining product colors:
HEX Color Reference System
The HEX color reference system is widely used within the digital design space and industrial manufacturing. HEX stands for hexadecimal and consists of a hashtag followed by six letters or numbers (i.e. #A0A2A6 for a shiny silver color). The first two characters represent the amount of red, the second pair represents the amount of green, and the third pair represents the amount of blue. This easily translates to the RAL and Pantone color reference systems, and it is widely used. Here is the format for the HEX Color Reference System:

Pro-Tip: for all your 3D printing color needs, check out this website that lists each filament by HEX, Pantone, and RAL color reference systems.
Pantone Color Reference System
Pantone Matching System (PMS) or Pantone Color Reference System is often regarded as the most effective way to communicate color; therefore, it’s a good idea to obtain and utilize the Pantone Coated Combo.
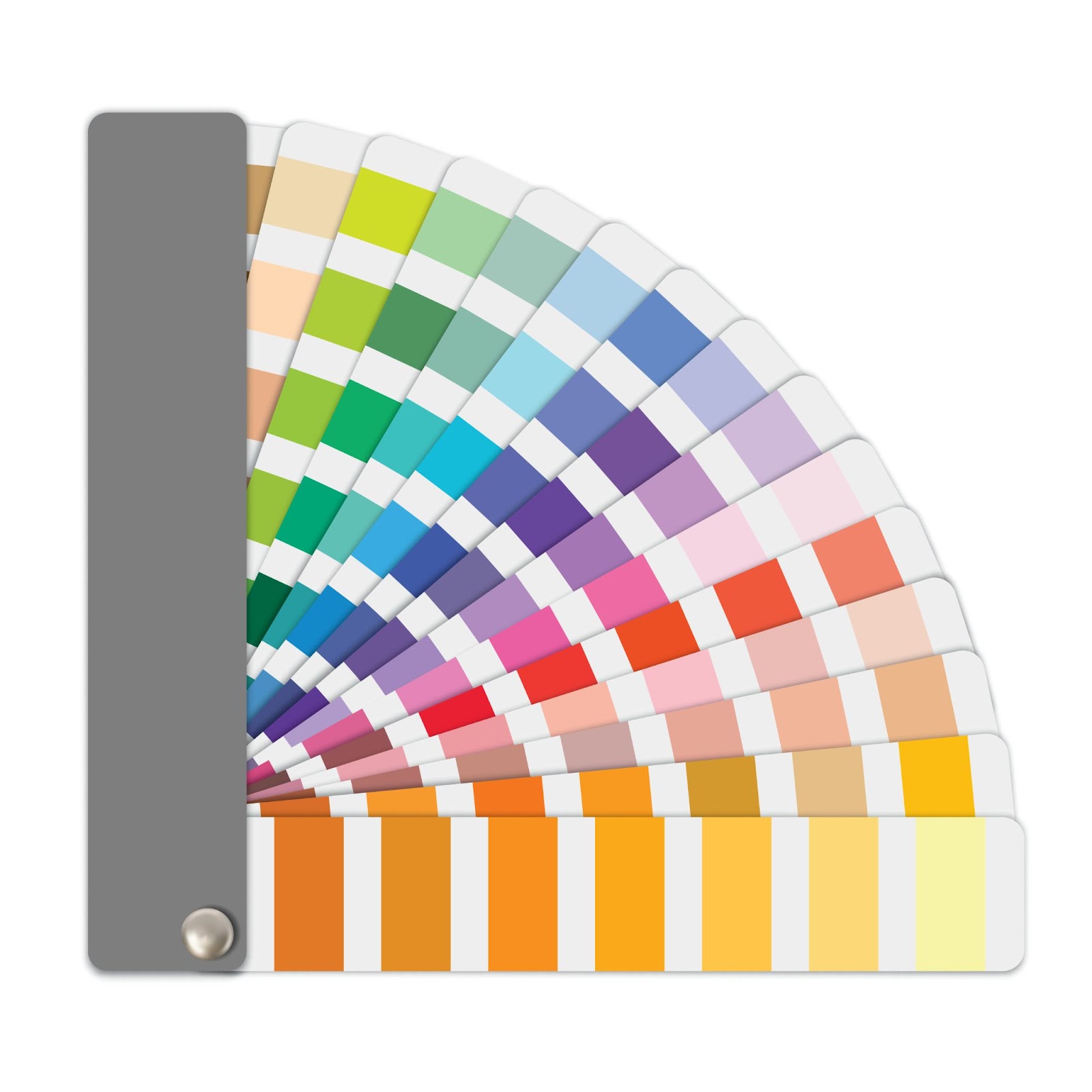
Pantone also sells a book of opaque and transparent plastics. A complete set costs several thousand dollars, but because the small injection molding factories won’t have these, it may not be as useful as the ink-on-paper formula guide. If you want a factory to refer to plastic chips, you may have to provide them. For 3D printing, plastic products, and hard goods needs, Pantone offers individual plastic color chips for use in a variety of applications such as food/beverage, consumer electronics, fashion, home goods, toys, and medical devices.
Now, I’m the first to admit that matching a printed swatch to plastic has limitations. If you want to get plastic chips for reference, I recommend using the formula guide as a starting point, then finding the corresponding plastic number here. Then you can buy single chips here to double-check that the color is what you’re looking for. Here’s a online store from Japan where you can glance at all the plastic colors.
In Europe, the RAL color matching system is more prevalent, and Chinese manufacturers often have both Pantone and RAL reference fans.
Manufacturer-Specific Color Reference System
There are also proprietary, manufacturer-specific paint or coating colors that may be designated for a product, such as:
- Sherwin-Williams, a popular manufacturer of paint for industrial and consumer applications
- Aerospace companies like Boeing and Cessna have paint called out with specifications instead of color codes
Material
Specifying Metal Materials
There are over 190 currently known metal alloys that can be used for a variety of applications today. As a refresher, a metal alloy is a mixture of two or more metals that have been combined under exacting conditions. While ‘pure’ metals can be machined, it is likely that you will be working with alloys — and 100% pure metal is exceedingly rare as it’s nearly impossible to eliminate all impurities from a given metal.
These are the most commonly machined (or CNC machined) metal alloy families:
Generally, choosing the most optimal material for your engineering design project is the most important selection you will make. You have to choose a material with the correct strength, resilience, rigidity, and composition for a successful and lasting design. But the battle isn’t won when you choose the correct material; you also have to correctly communicate your material selection. To ensure you are correctly specifying the metal you want, you should specify the following in your bill of materials or on your engineering drawing:
- Specific material grade: For example, 6063 Aluminum or 360 Brass
- Material condition: For example, heat treated, quenched, annealed, quenching, etc.
- Material specification: If you want the material to be manufactured, tested, and/or certified to a specification, then you must clearly identify the specification, including any revisions.
- Special requirements: This includes traceability, record retention, incoming inspection, approved suppliers, etc. Special requirements may be included in another engineering document like a Request for Quote (RFQ) or Engineering Requirements Document (ERD)
Specifying Plastic Materials
Plastic material selection is similar to metal material selection, but plastics are less straightforward. For instance, you cannot manufacture plastic components the same way for every type of plastic. This has to do with the structure of the plastic material itself, as well as the lower melting temperature of plastics versus most metals.
For plastics, it’s best to designate the type of resin you want (e.g., UV-resistant ABS, food-safe HDPE), and work with your manufacturer to find the exact resin. I like to get a few recommendations from the manufacturer, then read the data sheets to make the final decision. Bear in mind that you don’t want to do a lot of research by yourself, only to find out that your dream resin has a twelve-week lead time and an unreasonable minimum order quantity. Fictiv’s Experts can help with specifying the resin for your next project.
Here are some characteristics to consider when specifying a plastic material on an engineering drawing or bill of materials:
- Regulatory or compliance requirements such as FDA, USP, NSF, USDA, etc.
- UV resistance, chemical resistance or other special environmental conditions the material will be exposed to
- Material transparency/opacity
Finish
Injection Molding or 3D Printing Material Finish Options
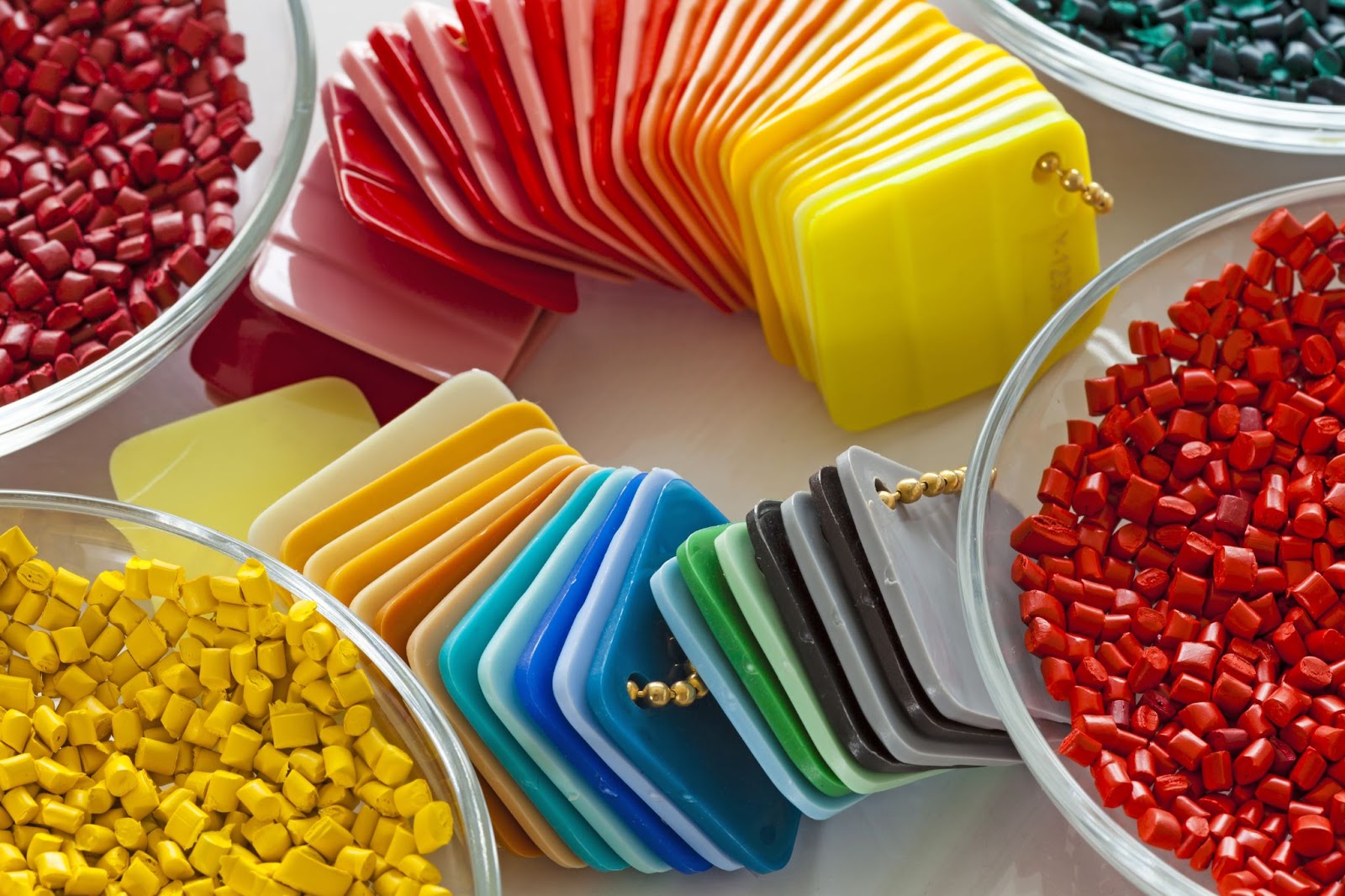
Luckily, injection molding and 3D printing finish options are not as numerous as the choice of colors for resins. For injection molded parts, the most basic finish designators are SPI (Society of Plastic Industry) surface comparator standards.
B-1 is the most common, no-frills cosmetic surface SPI finish, and C-1 is typical for non-cosmetic internal surfaces. A-class surfaces are very expensive, and if this is a requirement, make sure that your tool steel is hardened, or the mirror finish will degrade quickly.
In addition to SPI finishes, there are myriad in-mold texture options available — anything from a brushed texture to fake leather.
Mold-tech and Yik-Sang are two big names in the mold texturing business. Mold makers send the finished tools to these two companies for texturing at an additional cost and lead time. Mold-tech and Yik-Sang catalogues are both pricey, but we own a set at Fictiv, so if you think this process might be for you, just ask us!
In addition to in-mold finishes, painted finishes are also an option for both metal and plastic parts. Glossy, matte, and soft-touch paint are all available.
For 3D printed parts, you want to specify the post-processing steps to apply the finish. Vapor smoothing is a popular finish type for PA12 and PA12 with glass beads, and hand grinding and polishing may also be specified. Bear in mind that it may be difficult to achieve a specific surface roughness with a manual process.
Finishing CNC Machined Parts
There are numerous CNC machined part finishes that you can specify to enhance the surface of your parts, or to provide extra capabilities or protection to your part.
- Functional Finishes: These finishes enhance or add functionality to your part. For example, increased wear resistance (nickel plating) or corrosion resistance (zinc plating). You may also specify a surface modification process like Chem film or Alodine™ (chromate conversion coating) or anodizing, which build a protective oxide layer on the surface of aluminum parts or other alloys. When specifying a functional finish, always call out the standard and the revision, type and class where applicable — otherwise the company can use their discretion.
- Surface roughness: This refers to the microscopic peaks and valleys of the material’s surface. For more information on surface roughness and how to specify it, check out Keeping it Smooth: Optimizing Surface Roughness in Manufacturing.
- Cosmetic finishes include paint and powder coatings.
Pro-Tip: For more information on surface finishes, check out The Ultimate Guide to Finishing CNC Machined Parts.
CMF Document Example
Some companies choose to convey CMF requirements in a CMF document or CMF specification. Now that you’re equipped with industry terms, you can make a CMF document that precisely captures the decorative qualities you want in your product. Best practice is to use a combination of text and CAD or rendered images to call out different CMF components on a single product.
Here’s a simple CMF example:
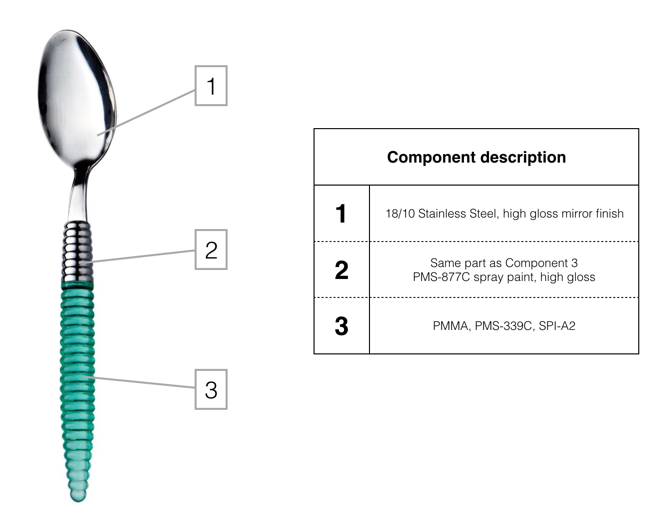
These techniques for communicating CMF work for both production parts and one-off appearance models, and will help you achieve high aesthetic standards painlessly!
Sourcing Simplified – Start Your Next Project With Fictiv
For all your 3D printing, injection molding, CNC machining and finishing needs, Fictiv has you covered. We’re experts at producing custom mechanical parts in a variety of materials and we simplify part sourcing with intelligent, streamlined, automated workflows.
Fictiv is your operating system for custom manufacturing that makes part procurement faster, easier, and more efficient.
If you need assistance selecting the proper color, material, or finish for your next project, create an account, upload your design and reach out to one of our experts. We’re here to help, so find out what our instant quote process, design for manufacturability feedback, and intelligent platform can do for you.