Time to read: 7 min
Fictiv’s June 17 webinar on best practices for engineering teams who are working remotely to build physical products was hosted by Hiro Shimozato, Fictiv’s Director of Product Management. Hiro talked with Ann Torres, Senior Vice President of Engineering at Synapse, and Chris Evans, Director of Engineering at Cooper Perkins, about their companies’ strategies for helping engineering teams stay productive, now that workplaces have shifted largely to remote work.
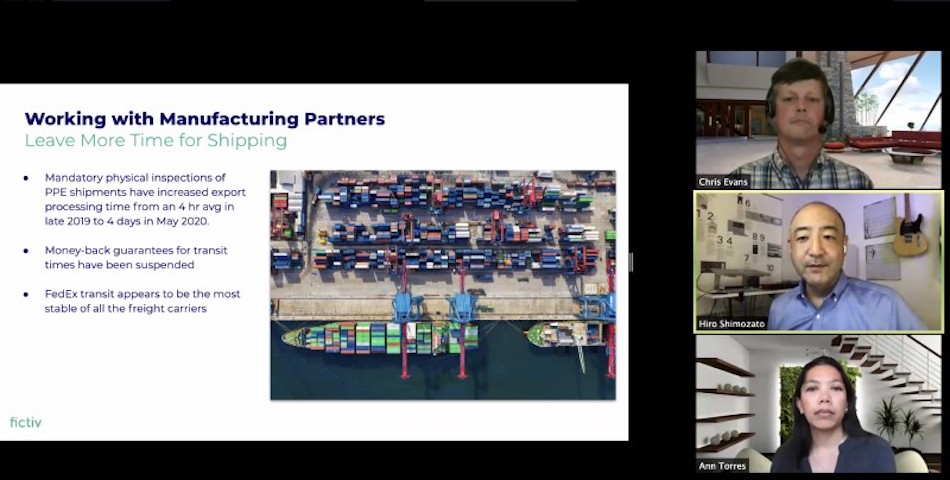
Recreating Workflow at Home
Both panelists agreed that physical space is a key issue when attempting to recreate an engineering workflow at home. They shared several examples of at-home setups, including a vertical setup with a variety of capable and inexpensive pieces of equipment, including an oscope, a microscope, a power supply, a soldering iron, and a programmer/debugger. Additional lo-fi, inexpensive options include a power brick, a phone camera, and a DMM.
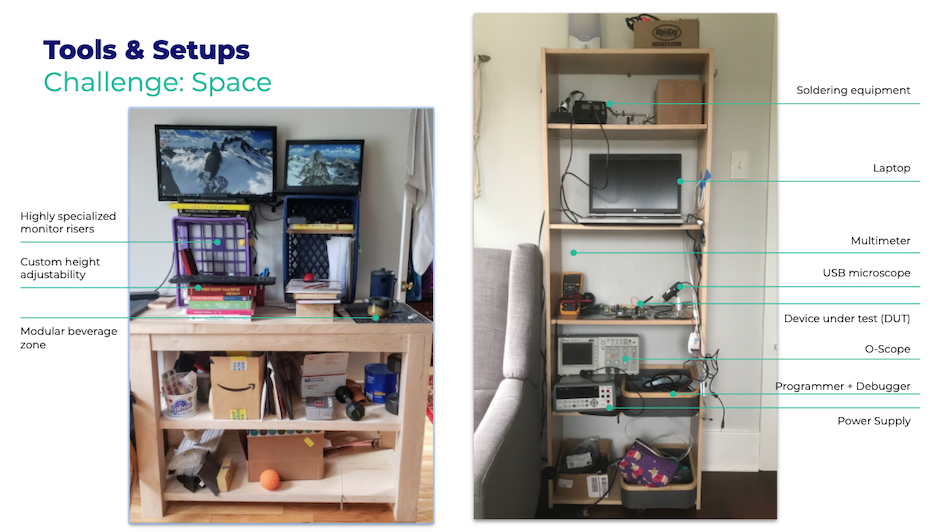
“People made do with the space and accessories they had available at the time,” said Chris. “Future improvements can build on this. Home spaces have not been designed with work requirements in mind, and with the lines blurred between work and home, it’s challenging to figure out how to get work done, and how to do it without interfering with home life.”
Rapid Prototyping at Home
Ann explained that rapid prototyping has been a pain point for her mechanical engineering team.
One of her mechanical engineers told her, “When I had an idea, I just used to go to the lab and work it out quickly. I’m anxious to get back in the office and the lab because I don’t want to theorize away some of my best concepts.”
Ann pointed out that engineers are intuitive and use their hands to solve problems and said she’s talked with her team about ways to set up for rapid prototyping at home, sharing examples of desktop 3D printers, which she said are capable and inexpensive.
“We recognize not everyone has access to more hi-fi systems, so sometimes remembering you can go back to your roots and use lo-fi stuff around the house to have a sense of moving and playing around can be helpful,” she said. “You can use Exacto knives, cardboard, paper, clay, and building material to make simple mockups.”
Additional suggestions included tearing down old products like phones and speakers and ordering analogous products to benchmark, teardown, and modify.
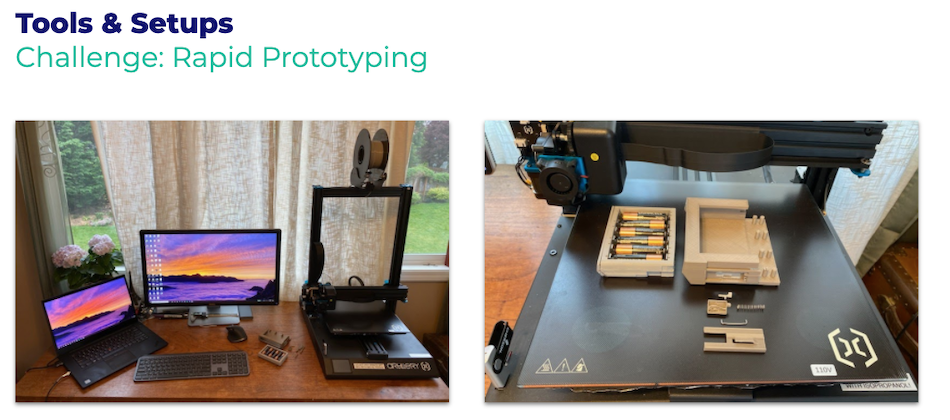
Access to Specialty Labs
Another pain point has been access to specialty labs. Ann explained that one of Synapse’s early stage development programs needed access to a wet lab to test early concepts and prototypes.
“One of the first things we did as the shutdown began was risk assessments of the impacts of working from home, highlighting the challenges of continuing to deliver for clients,” said Ann. “One of our lead engineers has a wet lab set up in her hallway in San Francisco, which is pretty amazing.”
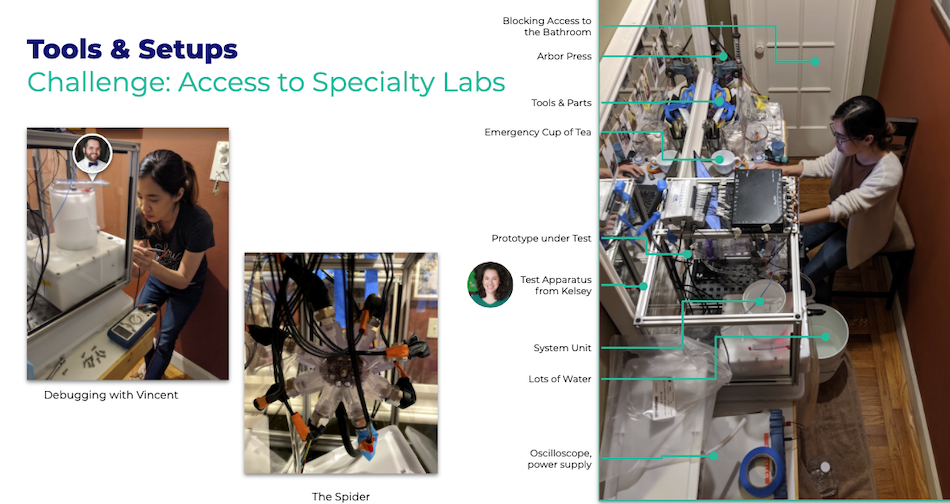
“There’s a range of completeness in the setups at home,” said Chris. “Some engineers can take advantage of specialized setups at home: a garage, a basement, a shed, or a spare room and may have equipment like lathes, milling machines, oscilloscopes, soldering irons, power supplies, and function generators.
Ann said that some members of her team took home specialty equipment for the short term. In the longer term, she envisions keeping the more expensive machines in the office, due to limited access to them, and setting up a standard remote work kit for engineers that includes less expensive 3D printers and electrical engineering equipment.
Creative Collaboration
Ann and Chris also shared the new ways their teams are collaborating and interacting remotely.
“In the office, it’s easy to have moments where you walk by an office or desk and can have a casual chat,” said Ann. “We want to talk about ways you can continue to promote that kind of creativity and collaboration, despite working remotely, and highlight the ways in which remote working has improved some of the ways people collaborate.”
Chris said the Cooper Perkins team has been using a virtual, collaborative whiteboard that allows team members to duplicate sketches and move them around.
“This allows for quicker exploration when searching for common themes and narrowing down to concepts, versus having a single piece of paper for each sketch,” said Chris. “Grouping and cross-pollination can happen live.”
The Synapse team is doing something similar, holding whiteboard sessions. using touchscreens for sketching and remote screen mark-ups.
“Virtual meetings and collaborations are easier in some ways, as everyone is remote now, so everyone can participate equally,” said Ann. “There’s no more sense of a geographical center of mass, with large meetings happening in one room, where a handful of people have to call in. Now, you can see everyone’s face, and it’s almost this level playing field. Brainstorming sessions and critical conversations feel like location and geography are not an issue, and that has been a real improvement.”
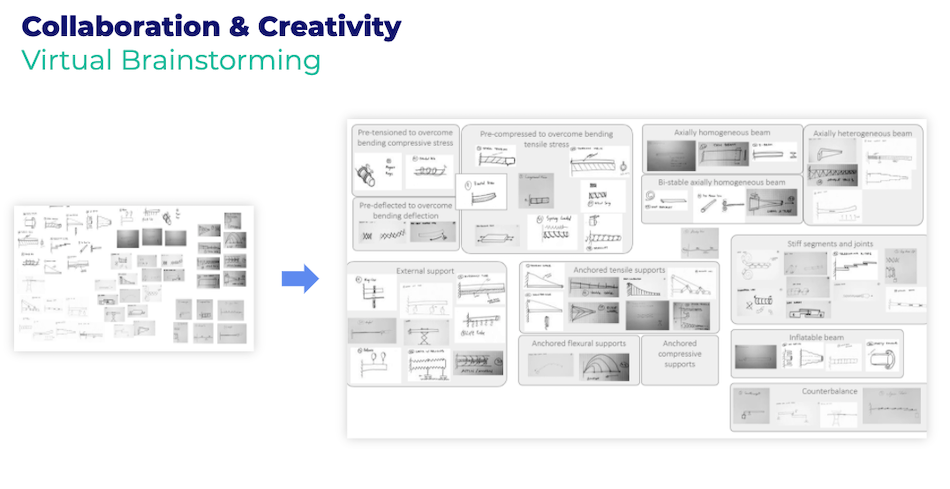
Ann emphasized the importance of managers driving connection and collaboration among fully remote teams.
“It’s not just about getting the work done; it’s also about building relationships and culture and an ethos around how the work gets done,” she said. “We have to find ways to create serendipitous moments, where you learn something about what people are working on, have a spark from a conversation, and learn about a problem you weren’t aware of.”
Chris said Cooper Perkins has implemented several ways to foster daily interactions, including daily project check-ins and creating ways to have spontaneous conversations.
“Daily project check-ins have become a core part of our process,” he said. “Bringing the team together frequently fosters both the formal project work and the casual conversations that tend to yield solutions to tricky problems.”
Also, now that the team doesn’t physically cross paths in the office, they’ve found it important to intentionally develop systems and put effort into facilitating opportunities to connect without a strict agenda.
“Before, it could be difficult to engage with a group of people in a room when you were dialing in from the outside,” said Chris. “Now that everyone’s remote, the dynamic has changed to become more inclusive of everyone.
Noting that many Cooper Perkins employees are either in San Francisco or Boston, which are three hours apart, Chris said it’s important to be aware of teammates’ home lives and constraints on their time.
“Recognizing that helps people feel like the organization cares about them,” he said.
Working with Manufacturing Partners
With travel disrupted, teams can’t meet with vendors face-to-face and may not have transparency when problems occur, so working with partners like Fictiv that have boots-on-the-ground support at supply locations, even overseas, to ensure quality parts, is critical. Likewise, volatility in international logistics has created shipping delays. Fictiv is providing regular international logistics updates, and Ann and Chris suggested allowing more time for shipping.
“Anticipate delays in last-mile shipping when planning builds, which seems more impactful than international shipping issues,” said Chris. “Ensure clients are aware of this, as well.”
Ann recommended conducting risk assessments to proactively identify and address critical issues in the areas of vendor availability, supply chain health, and safety. She suggested tracking vendor status, capability, engineering support and identifying alternate vendors/components/materials, to keep your supply chain resilient. Ann also recommended conducting safety assessments for things like equipment moved to homes, as well as interactions with clients and vendors. Finally, she emphasized the importance of setting stakeholder expectations with respect to budget, schedule, or deliverables.
In lieu of on-site visits to CMs or factories, Ann recommended finding vendor partners like Fictiv with boots on the ground, who can be your eyes and ears on the floor and help develop trust across teams.
Looking Ahead
Going forward, Ann believes we’ll see some changes in offices, as well as more development at home and more capable vendors and partners. She thinks office space will be focused around lab, assembly, and collaboration space, rather than desk space, with more space for specialized assembly areas and equipment.
She noted that manufacturers have always talked about being more strategic, and this situation forces that, which hopefully will result in more capable vendors and manufacturing partners.
“We generally use outside agencies to do rapid prototyping because we find that our time is well spent integrating, problem solving, and troubleshooting—not necessarily generating the parts, but perhaps in modifying them,” said Chris. “So the nature of our work hasn’t changed; we’re just doing this from home now. We internally don’t see a big demand to do rapid prototyping at home, but we’re doing what Ann described—finding ways to quickly breadboard concepts, so that we can learn about these concepts without spending an inordinate amount of time on them.”
Chris added that communication is key and that organizations will need to adapt so help employees be more efficient and productive.
“Let people take tools home, maybe with a checkout process; find out how to let people access the tools they can’t take home and maintain safety and efficiency; and make sure clients/vendors understand your protocols for office visits,” he said. “We’ll be carrying forward some newly established ways of working together, such as daily project check-ins, that have improved our efficiency over the last couple of months. As we encounter new phases of projects, including late stages of development, we’ll need to adapt and bring on new tools and techniques.”
As engineering teams adjust to the new normal, sharing best practices for remote product development is a useful way to help your own team evaluate what’s working and what can be improved and also help other teams work more effectively. And remember that Fictiv is your manufacturing partner in this new virtual world to help you get precision mechanical parts quickly, to accelerate development cycles and eliminate sourcing friction!