Time to read: 3 min
As Hollywood blockbusters tend to be laden with computer-generated imagery (CGI), it’s easy to assume the film industry no longer relies on hardware to wow audiences. Dig a little deeper, however, and you’ll find that hardware design and engineering are at the core of animatronics, a vital component to the process of modern movie-making magic.
Engineers, builders, and other artisans make futuristic technology, terrifying monsters, and fantastic creatures seem tangible and real to movie-going eyes. Plus, thanks to recent advances in fabrication technology, designers can create lifelike characters, realistic exotic locales, and credible props faster and more cost-effectively than ever before.
Here are three ways Hollywood uses hardware, cutting-edge engineering, and manufacturing techniques to make movies feel magical.
Animatronics Bring the Fantastic to Real Life
The multifaceted discipline of animatronics has been a staple of film production since the release of 1964’s Mary Poppins.
In the film, star Julie Andrews sings “A Spoonful of Sugar” with a clearly artificial but incredibly charming robin. The Walt Disney Corporation’s engineering subsidiary, WED Enterprises, created the groundbreaking technology called Audio-Animatronics for use in Disneyland’s Enchanted Tiki Room attraction.
As detailed by Popular Mechanics, the firm combined pneumatic tubes and compressed air rockets to give life to the exhibit’s creatures. The group also utilized a proprietary magnetic tape system to synchronize their bird’s movements with music and other audio.
In a Canadian Broadcasting Company interview with Walt Disney, the entertainment magnate revealed his staff adapted the effect for Mary Poppins. Technicians decided to run small electrical cables along Julie Andrews’ body so they could operate the robin on set. Though very cumbersome, the effect enchanted audiences at the time.
By the 1970s, animatronics had advanced significantly but still needed refining. In the middle of the decade, director Steven Spielberg enlisted art director John Alves and special-effects artist Robert A. Matlin to create the titular beast for his film Jaws. The team used tubular steel for the creature’s skeleton, pneumatic components to give it motion, and skinned it with hard polyurethane.
Though the multiple prop sharks’ mechanical breakdowns and unconvincing appearance caused Spielberg major headaches, the monster terrified a generation of filmgoers. Jaws became a critical commercial and smash hit that helped usher in the blockbuster of filmmaking, and Spielberg would again use animatronics in one of his most enthralling films, Jurassic Park.
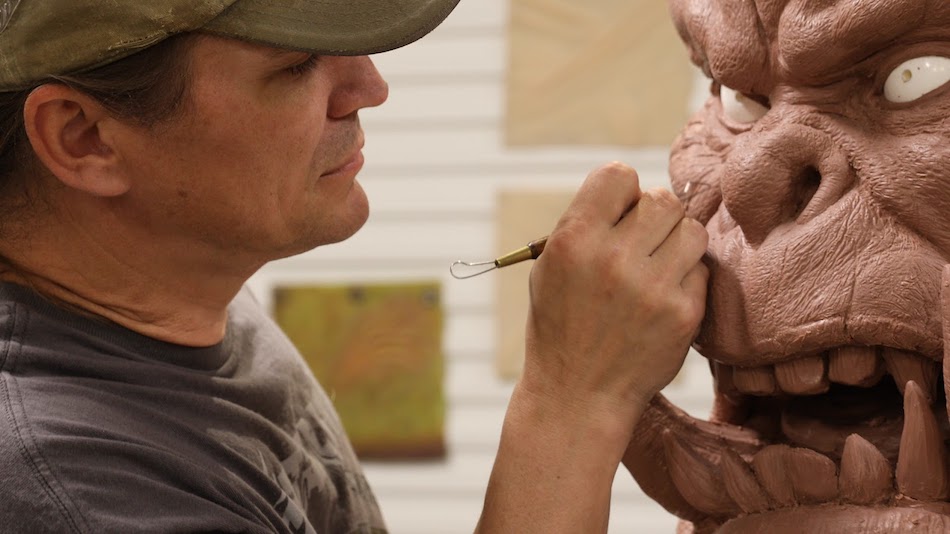
Modern Engineering Advancements in Animatronics
In the three decades since the release of Jaws, animatronic technology has reached a remarkable level of sophistication.For Spielberg’s Jurassic Park series, for instance, Sam Winston Studios (SWS) fabricated a 43.5 foot remote controlled Spinosaurus equipped with 43 hydraulic cylinders designed to simulate motion on land and underwater.
Using CNC sculpting, the firm crafted highly durable foam parts to fill out their dinosaurs’ muscles and skin, giving the animatronic weight and texture that can’t be matched by even the most advanced computer-generated images. Eight puppeteers used radiofrequency-enabled joysticks to give the Spinosaurus a full range of motion and flashes of visible emotion. Plus, the dinosaur was created with 1,000 horsepower, giving it a shocking amount of speed and mobility.
Companies like Animax Designs use complex machining and modern software to develop, design, engineer, and fabricate animatronics for film and theme parks, including everything from a life-like orangutan to a virtually-puppeteered human head.
3D Printing in Set Design and Props
Another modern hardware innovation Hollywood has adapted for its purposes is 3D printing.British production company Propshop 3D printed military-grade night vision goggles for the film Zero Dark Thirty, a spaceship for Guardians of the Galaxy, and even a full-sized tank for Fast & Furious 6. They also 3D printed entire sets for films such as Ex Machina and Avengers: Age of Ultron. Because Propshop can fabricate equipment and sets made to order, it offers filmmakers product design capabilities that can greatly expedite their pre-production process.
Though computer-generated graphics can be breathtaking, audiences still need practical elements to buy into a film’s reality. Accordingly, Hollywood studios will continue to develop animatronics and 3D printing to entertain filmgoers the world over.