Time to read: 3 min
In this part of our Butterball electric vehicle conversion series of articles, we’re discussing prototyping and making parts vs. buying them off the shelf — and you can learn more about the genesis of the project, its mechanical design, and electrical system in our other articles.
As a digital manufacturing company, we’re very familiar with ordering and fabricating parts, and many of us also have hands-on experience building things. For this EV conversion project, we knew had three options when it came to sourcing the parts we needed — we could buy off-the-shelf components, have others make parts, or we could make them ourselves.
Prototyping is Key
No matter which option we chose, a major lesson learned from this project was the importance of prototyping. Even simple prototyping is helpful and effective. You can learn a lot by just mocking up the size and shape of a part, which is why we used a LOT of cardboard, foam-core, particleboard, duct tape, and hot glue as we worked out our final designs.
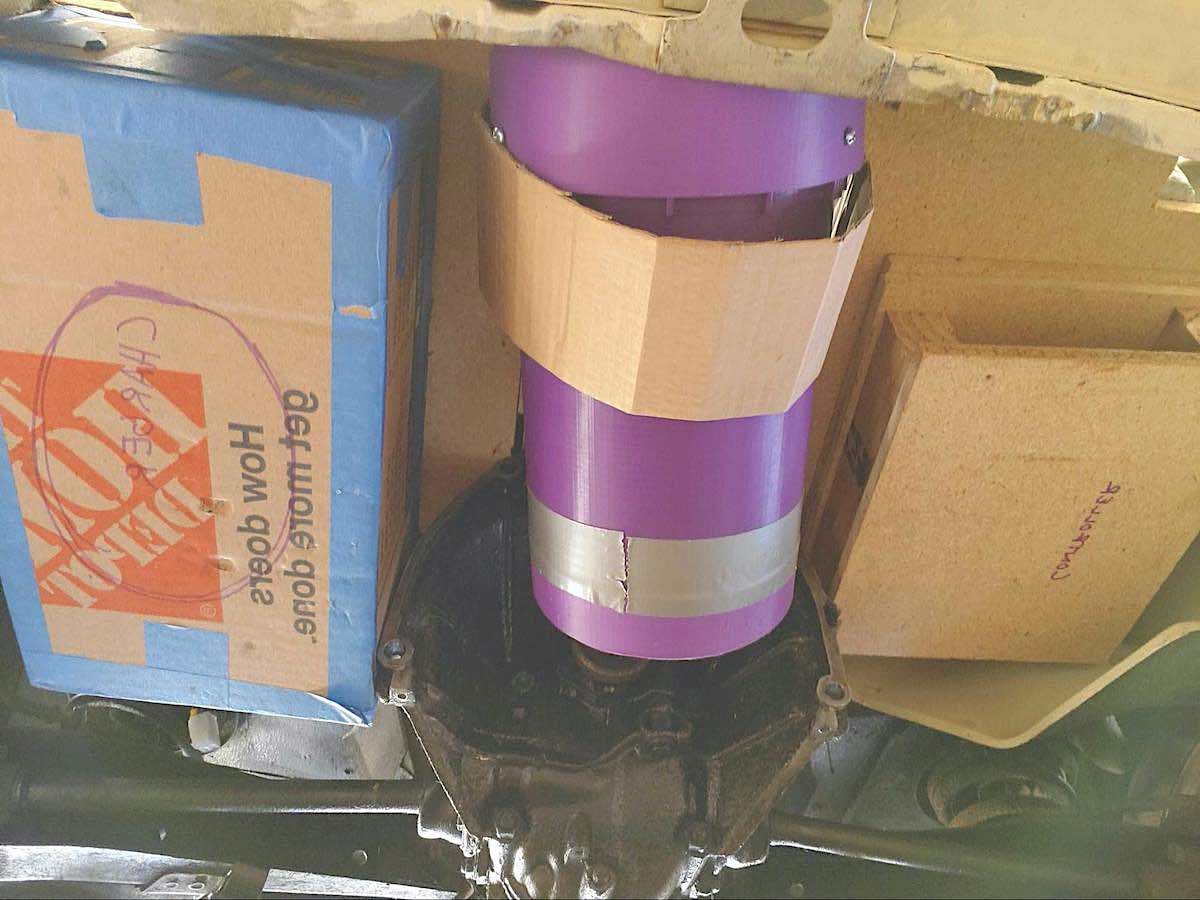
We found that these simple, lightweight prototypes were easy to move around and manipulate, which was critical to figuring out how everything would fit in the car. We even used the 3D printed motor prototype long after we ordered and received the actual motor — it was so much easier to move around, and there was no risk of damaging the real thing.
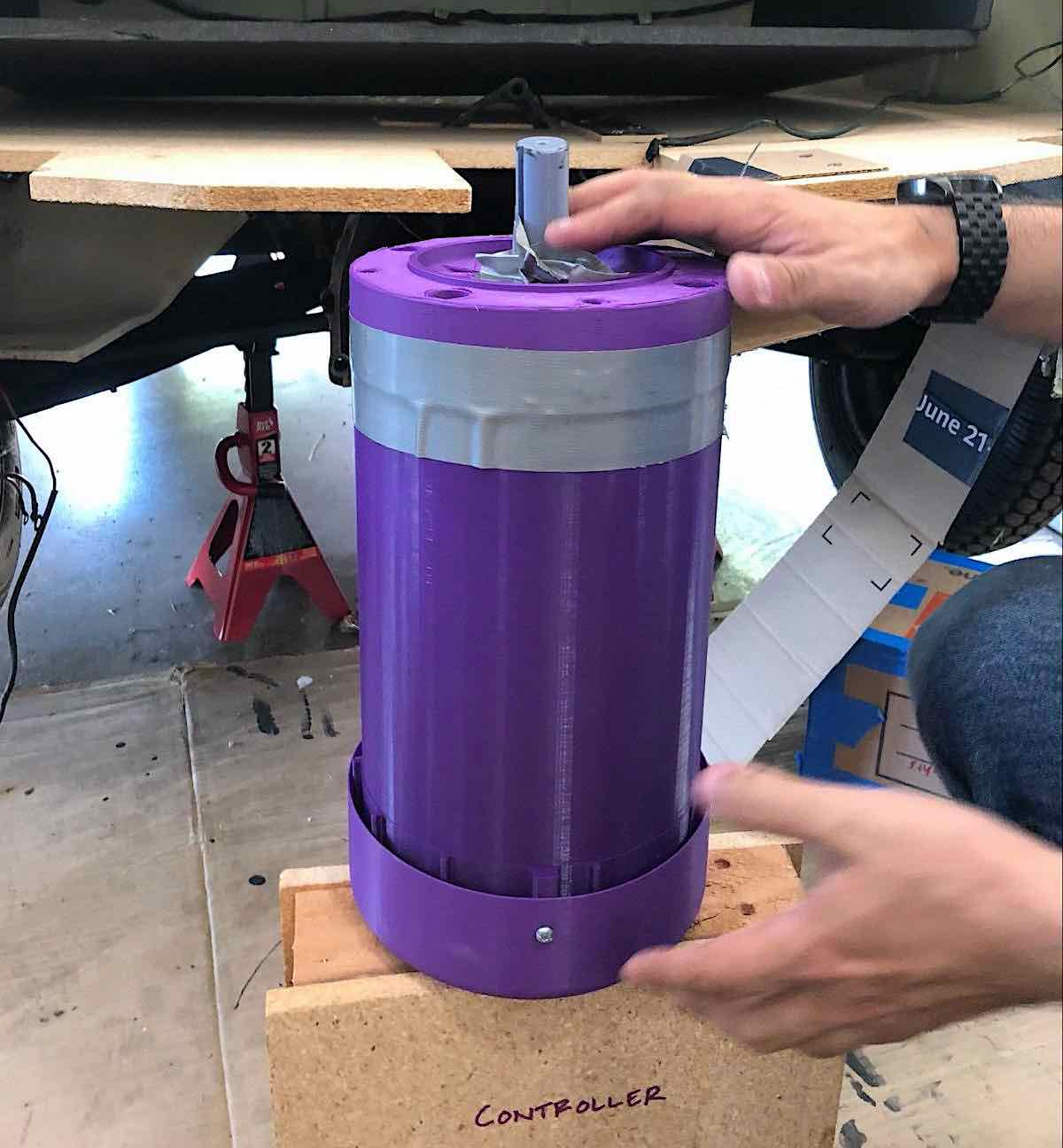
In addition to the motor mockup, we also 3D printed the coupler to do fit checks and test how much space it required.
Making vs. Buying Parts
The motor and coupler were two key items in our build that we didn’t make ourselves. Our electric motor was ordered as an off-the-shelf item, while we designed the coupler specifically for our needs and had it machined to our specifications.
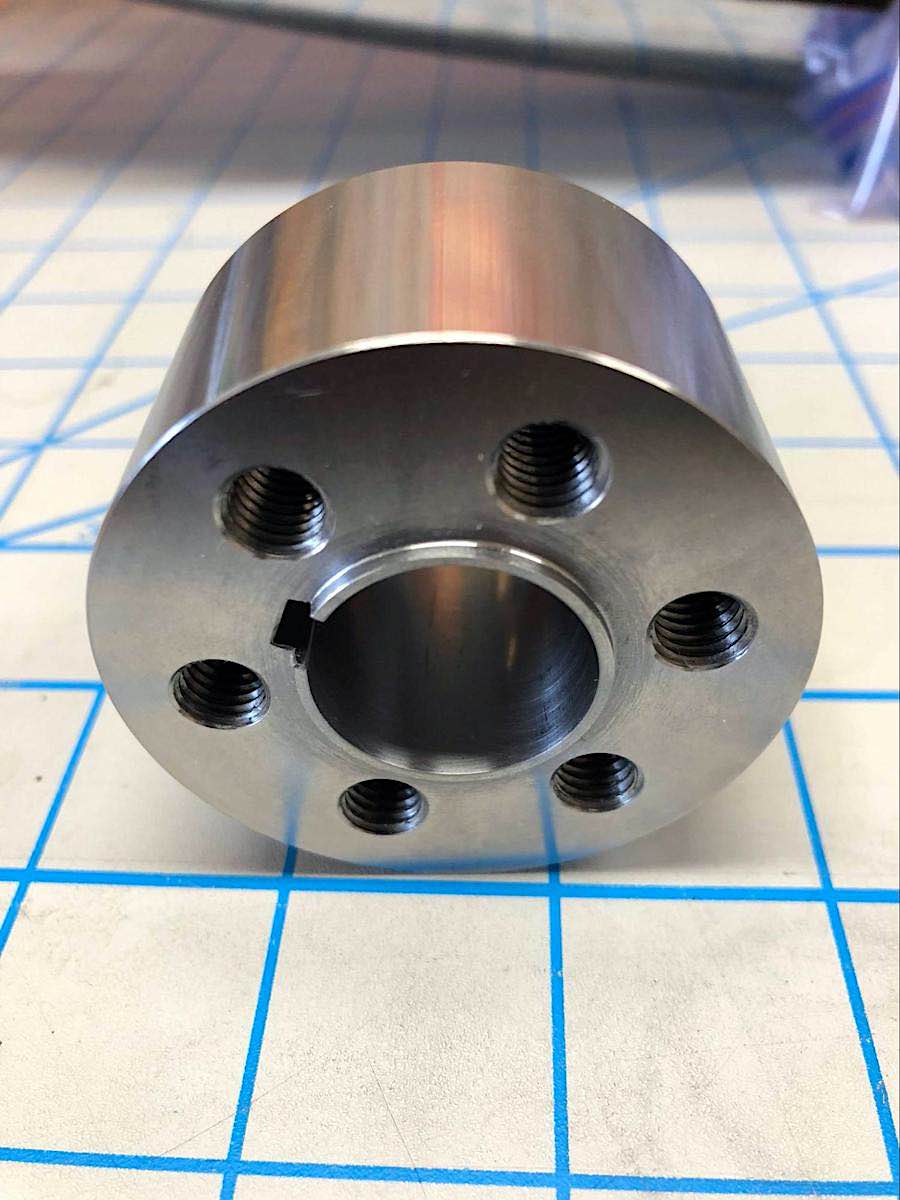
The aluminum base mounting plate and the battery boxes were the next two large components that were within our capabilities of making ourselves, but we had the option of buying elsewhere — it came down to whether we wanted to spend our time, or spend money to pay for someone else’s.
We decided to have the aluminum plate made to order because it could be quickly and easily cut by a machine, whereas it would have been difficult and time-consuming for us to do the fabricating. Plus, we couldn’t have done it with the same level of precision, which we needed to have a clean interface where the two halves of the plate meet in the middle.
A mistake in fabrication would have required us to buy more material, which would have been expensive and added a lot of time to the process. The plate ended up being one of the more costly parts of the build, but doing it ourselves wouldn’t have given us the result we needed.
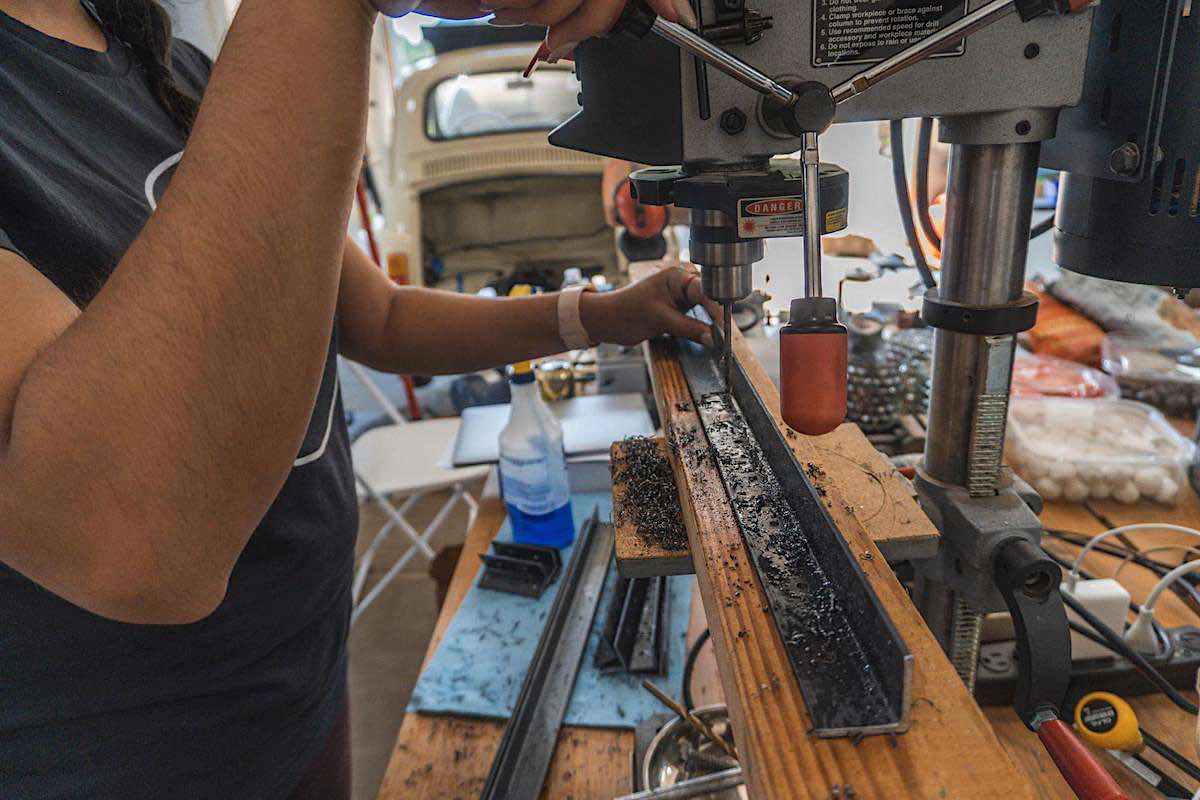
On the other hand, we opted to make the battery boxes ourselves. We had some of the necessary materials already, and the rest — like plastic sheet and steel angle bar — were inexpensive and readily available. Plus, building them ourselves gave multiple team members an excuse to work together and learn about these parts. However, building the battery boxes by hand took longer than anticipated — in part because we weren’t as detailed in our designs and changed things as we put them together.
Lessons Learned
Throughout this project, we learned how effective, and often essential, prototyping can be. It’s useful to test things out to make sure a component will fit before spending money or time procuring a final part.
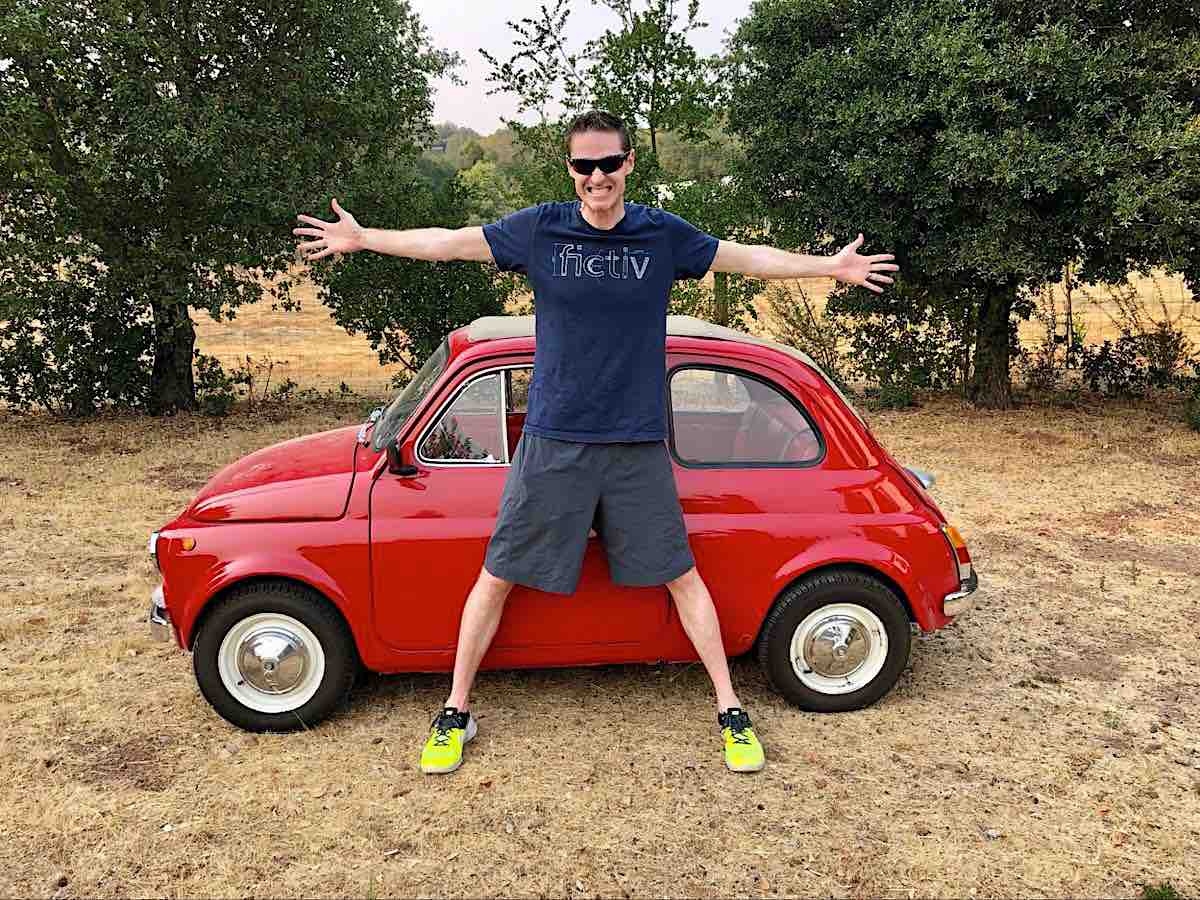
Also, it may seem cheaper to make something yourself to avoid upcharges or middlemen. But you also have to account for the time it takes you to make what you need and whether you can achieve the quality you need — it often takes longer than you think. In the end, we had fun making all the parts and working through this project together.
Want to learn more about how Fictiv can help with your project? Whether big or small, our 3D printing, injection molding, and CNC machining services can deliver the quality parts you need, fast. Create an account and upload your designs today!