Time to read: 8 min
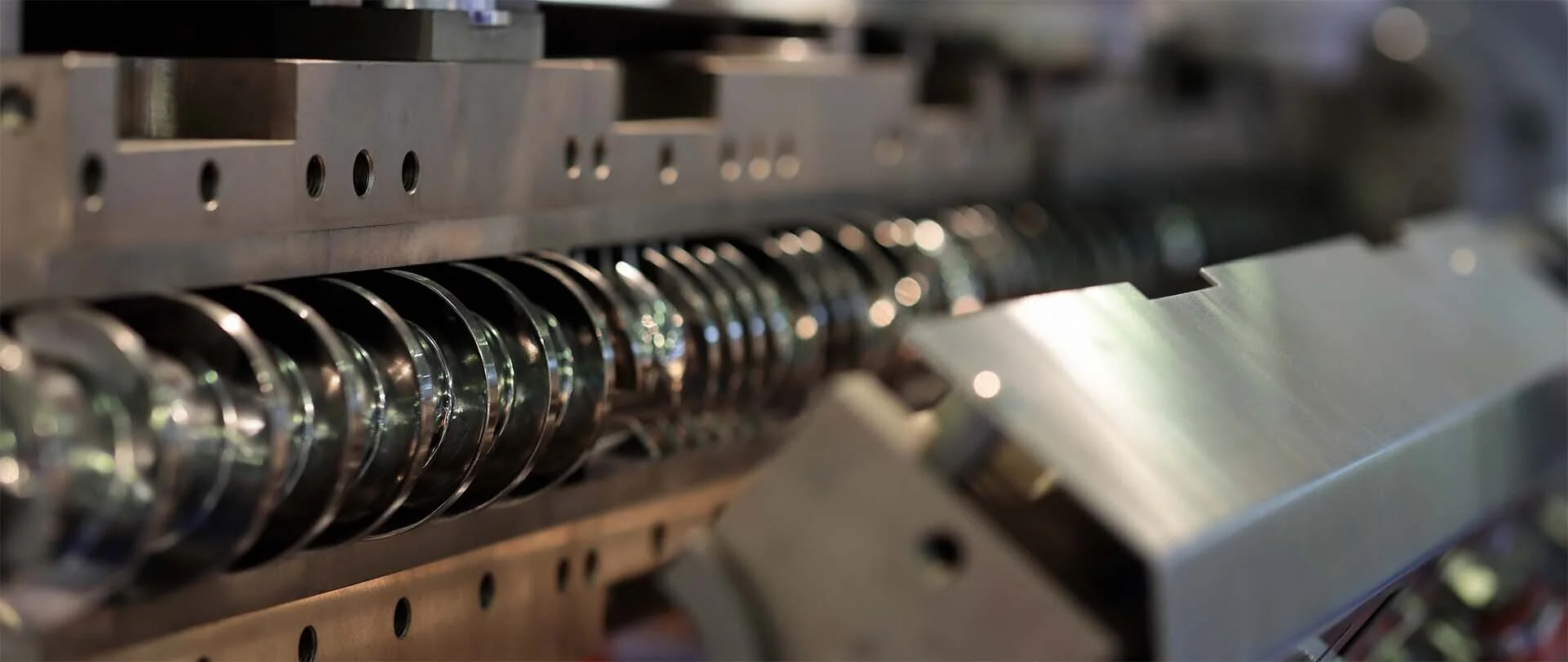
Extrusion and injection molding are two primary methods for manufacturing plastic and rubber parts. Extrusion creates continuous profiles by pushing material through a die to produce uniform cross-sectional shapes, ideal for pipes, tubing, and weatherstripping. Injection molding, on the other hand, injects molten material into a mold cavity and enables the production of intricate, three-dimensional parts suited for applications that require design complexity and precise tolerances.
This article examines extrusion vs injection molding in detail so you can determine whether extrusion or injection molding is the better choice for your project. It also compares these manufacturing processes in terms of cost, scalability, complexity, and efficiency. In addition, you’ll find information about advanced considerations, applications, and trends.
What is Extrusion Molding?
Extrusion is a proven process that molds continuous lengths of plastic and rubber so they have uniform cross-sectional shapes. These profiles can be as simple as a tube or cord but are sometimes more complex. For example, door and window seals can be extruded into shapes that resemble the letters D, E, J, P, or U. Typically, the extruded profile or extrudate is cut into lengths or individual parts.
Extruding machines can produce solid, semi-hollow, or hollow profiles with a smooth surface finish. First, plastic or rubber is fed into a hopper. Hot extrusion heats the polymer above its recrystallization temperature but cold extrusion is performed at room temperature instead. This material is then conveyed with a screw and forced through a machined metal die under high pressure to achieve the desired shape.
Process Optimization for Industrial Applications
Optimizing the extrusion molding process involves balancing material flow, cooling rates (for hot extrusions), and production speeds. The benefits include higher quality, increased efficiency, and reduced waste. Regardless of the type of machine or process, there are some best practices to follow when extruding plastic or rubber. Innovations are also improving quality.
Material Optimization
A well-designed die ensures the even flow of material across the entire profile. Feed rate control can also optimize flow consistency. Importantly, the screw needs to have the correct compression ratio and flight geometry based on the material’s properties. Adjusting the back pressure and the screw speed helps to control the melt pressure and ensures steady material output without degradation.
Cooling Rate Optimization
With hot extrusion, water baths or air systems provide fast or gradual cooling, respectively. For hollow profiles, internal air or fluid systems can be used to cool both internal and external surfaces at the same rate. Increasingly, infrared thermography or embedded temperature sensors are used to support real-time monitoring and control.
Production Speed Optimization
Higher screw speeds can increase extrudate output, but they can also result in inconsistent material flow. That’s why many extruders now use feedback systems that automatically adjust screw speeds based on processing parameters like melt pressure. If high-volume production is critical, hot extrusion equipment with fast-melting polymers may be required.
Material Considerations in Extrusion
Melt parameters aren’t the only considerations when it comes to extruded plastic or rubber.
- Plastic extrusions cool and solidify at different rates, and some shrink more than others. Thermoplastics soften when heated or re-heated and solidify when cooled. Thermosets cannot be remelted and, therefore, cannot be re-extruded.
- Rubber extrusions require vulcanization, a form of curing so that the extrudate achieves its final properties. Because rubber swells after exiting the die, dimensional changes may occur. This can be mitigated by optimizing the die design and processing parameters.
Plastic extrusion molding supports various polymers, including engineering thermoplastics, thermoplastic elastomers (TPEs), and high-performance materials like PEEK. If you’re used to working with machined metal parts, remember that the part tolerances for extrusions are not as precise because of the tooling that’s used and the material shrinkage that’s expected.
High-Volume Applications
Extrusion is one of the most widely used manufacturing processes for high-volume parts production. For example:
- The automotive industry extrudes windshield wipers and weatherstripping.
- For the building and construction industry, extruders supply pipes, tubing, fences, railings, window frames, and sheeting.
- Aerospace manufacturers use extruded wire and cable insulation in aircraft cabins.
- Medical tubing and medical devices such as catheters are also extruded.
Advantages and Limitations
Like any manufacturing process, the plastic extrusion method has its advantages and disadvantages..
- Advantages include lower per-part costs and support for continuous operations and high-volume production. Most extrusions also exit the die with a good surface finish.
- Disadvantages include high initial setup costs, variations in the size of the final product, and the fact that only one type of cross-section can be extruded at a time.
Now that you know more about the plastic extrusion process, it’s time to examine injection molding in detail.
What is Injection Molding?
The Injection molding process begins when plastic resin pellets are loaded into a hopper or liquid rubber is mixed. This material is then heated in a barrel until it becomes a thick liquid called melt and injected into a mold cavity under pressure. After the mold is filled, the molten plastic material takes the shape of the tool, which is typically machined from aluminum or steel. The parts cool and are ejected.
Injection molding produces solid parts but cannot create hollow ones. This plastic manufacturing process supports considerable design complexity, however. Depending on the quality of the tooling, injection molded parts can have tight tolerances. It’s also possible to injection-mold parts with a textured surface finish or features such as logos.
Process Efficiency and Complexity Management
Managing process efficiency and complexity in plastic injection molding is critical for optimizing production, reducing costs, and maintaining quality.
- Process efficiency involves cycle time and material usage optimization, machine performance and maintenance, and process monitoring and automation. Closed-loop control systems, real-time monitoring, and automated quality control promote efficiency.
- Complexity management includes mold design and engineering, controlling part variability, and reducing process and material complexity. Quick mold change systems, work cell flexibility, and setup optimization can speed production and reduce downtime.
Injection molding also benefits from the use of simulation software, Industry 4.0 and Internet of Things (IoT) integration, and greater integration with enterprise resource planning (ERP) systems.
- Simulation software includes tools for mold flow analysis and cooling optimization.
- Industry 4.0 and IoT integration span smart manufacturing systems and machine learning for process control.
- ERP integration encompasses production scheduling and supply chain management.
Material Integration for Advanced Applications
Injection molding supports the use of high-performance polymers like PEEK and other composites, such as glass-filled nylon, that are tailored to impart specific properties. Injection molding is also used with engineering plastics such as polycarbonate (PC) and some elastomers, such as liquid silicone rubber (LSR), for medical devices and aerospace parts.
Precision and Tolerance Control
Injection molding’s ability to maintain precise dimensions and tight tolerances across high volumes makes it an asset for demanding applications. Injection-molded parts are also suitable for industrial assemblies. Because each injection molded part has its own tolerances, designers need to account for tolerance stack-ups so that all of the assembled parts fit together.
Advantages and Limitations
Among its advantages, injection molding supports design complexity and has well-defined rules as described in Fictiv’s Injection Molding Design Guide, a free resource that’s available for download. The hardened steel molds that support tight tolerances are more expensive, but they can provide a cost-efficient return on investment (ROI) across a high volume of parts.
For prototyping and low-volume production, and for parts that require commercial tolerances instead of fine ones, molds made of soft or semi-hardened steels can be used instead. Master unit die (MUD) inserts, or MUD molds, can also help to control costs. These universal frames fit into an injection molding machine and hold a removable insert.
Key Differences Between Extrusion and Injection Molding
Extrusion and injection molding have important differences in three main areas:
- Cost and ROI
- Production scalability
- Part complexity and design versatility
Cost and ROI
In terms of the cost of extrusion vs injection molding, extrusion has lower tooling costs. That’s because the dies used are simpler, easier to machine, and therefore less expensive to produce. For the continuous production of simpler parts at high volumes, extrusion provides a faster ROI. For complex parts at high volumes, however, the higher cost of an injection mold can be spread or amortized across many parts.
In general, extrusion has lower production costs than injection molding. Parts that are extruded in long sections require less frequent stops, and there’s no need for ejection since the part is forced through and exits the die. Injection molding processes can achieve faster cycle times with optimized cooling systems, but that adds to a project’s total costs.
Production Scalability
Extrusion readily scales from small-to-medium production to higher volumes because of its low tooling costs and simple setups. Plastic molding is also scalable but may require a different tool. For example, a soft or semi-hardened steel injection mold isn’t suitable for producing hundreds of thousands of parts, even if commercial rather than fine tolerances are used.
Part Complexity and Design Versatility
Injection molding and extrusion molding differ significantly when it comes to the complexity and versatility of the parts they can produce. The table below provides an overview.
Factor | Injection Molding | Extrusion Molding |
Part Geometry | Highly complex 3D parts with intricate geometries | Simple, uniform cross-sectional shapes |
Surface Details | Fine details, textures, logos, variable wall thicknesses | Limited surface details, uniform thickness |
Multi-Material Parts | Possible with overmolding or two-shot processes | Co-extrusion in layers, but not multiple materials in one part |
Part Size | Small to large and lightweight to heavy | Best for long continuous parts because the die constrains the part’s width and height |
Customization | Highly customizable with complex features | Less customizable, requires secondary processes for greater complexity |
Material Options | Wide range of materials, including multiple materials | More limited materials but can achieve layered structures |
Next, let’s look at both manufacturing methods in terms of part design and geometry, features and details, and material flexibility.
Part Design and Geometry
Injection molding is ideal for producing parts with intricate shapes and complex geometries. It can also create fully three-dimensional parts with features such as ribs, bosses, snap fits, and complex internal cavities.
Extrusion is best suited for parts for simple, uniform shapes. Although it can create parts like window frames and trims with complex cross-sections, extrusion requires secondary processes to create fully three-dimensional objects or internal cavities.
Features and Details
Injection molding can create parts with fine surface details, including textures, logos, and intricate patterns. It can also mold parts with variable wall thicknesses within the same part. Plus, features like threads, snap-fits, and hinges can be molded directly into the component.
Extrusion can’t produce fine details or intricate surface features. Instead, the level of detail is limited to what can be achieved with a consistent cross-section. To add complexity or additional features, secondary processes such as cutting, drilling, or stamping are used.
Fictiv Provides Injection Molding Services
Fictiv provides injection molding services and delivers complex parts at ridiculous speeds. The tooling that’s used in injection molding is more expensive than the dies for extrusions, but injection molds made of soft or semi-hardened steels cost less than hardened steel molds.
When you request a quote for injection molded parts, you’ll also receive design for manufacturing (DFM) feedback from our engineering experts. This can help you to accelerate product development, and Fictiv can provide T1 samples in about two weeks.
Compare that to extrusions. You might have to wait a lot longer for tooling to arrive – and with far less support for design complexity.Are you ready to get started? Create a free Fictiv account and upload your CAD drawing.