Time to read: 7 min
When designing a product, you want to consider all the factors that will go into its success over the course of the development process. For most companies, this involves making the best quality product at the lowest possible cost.
Design for Excellence (DFX) is a modern product development approach and umbrella term that encompasses several other design strategies focused on optimizing design and manufacturing processes. DFX helps manufacturing teams make smarter decisions to enhance product quality, reduce costs, and boost performance throughout the product life cycle.
This article explores the core principles of DFX and how digital manufacturing supports its successful application.
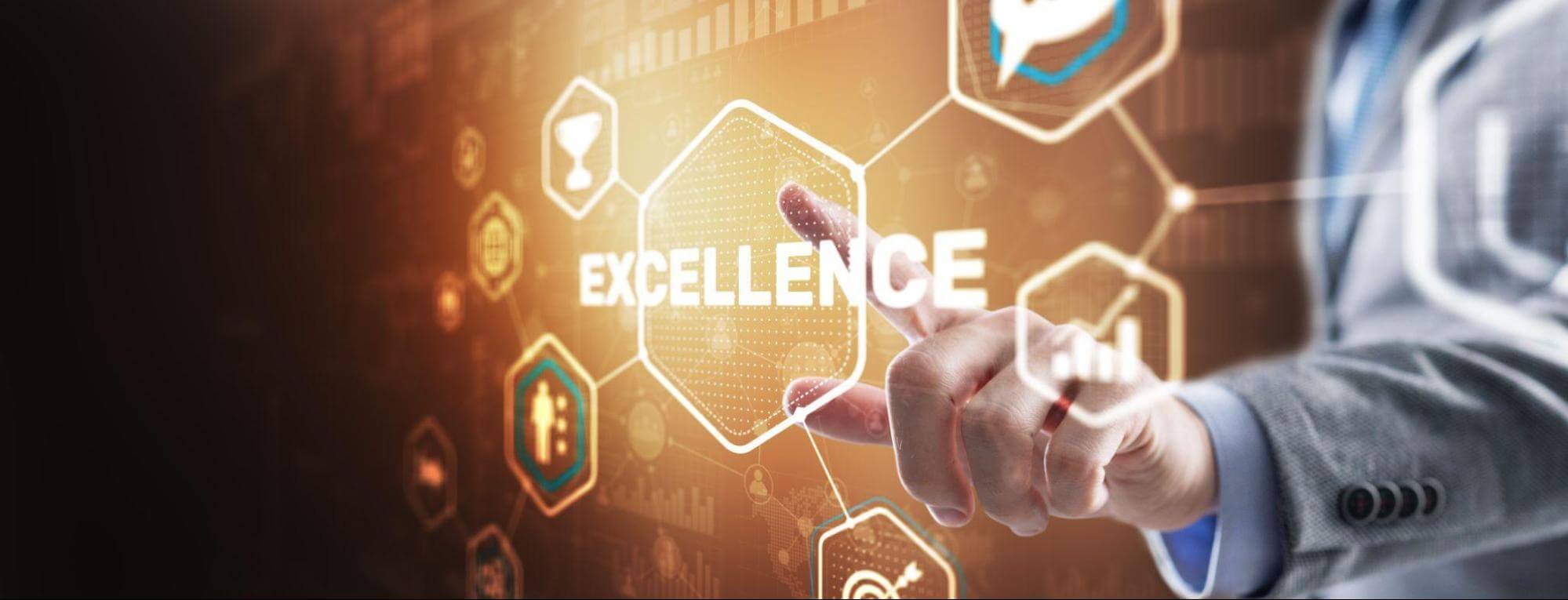
What Is DFX (Design for Excellence)?
DFX is a holistic and systematic approach to product design that prioritizes key aspects of the design and manufacturing process, including manufacturability, cost, reliability, sustainability, and serviceability. It is an integrated methodology that ensures that products are designed with quality, efficient manufacturing methods, and long-term performance in mind. Companies that adopt a comprehensive DFX strategy can quickly scale products to mass production and achieve long-term success.
DFX evolved from traditional design practices, incorporating concepts aligned with lean manufacturing and Industry 4.0. By implementing this approach early in the design phase, companies can identify potential inefficiencies, reduce waste, and enhance scalability. This proactive approach not only improves product performance but also streamlines production workflows, making it easier to adapt to changing market demands and technological advancements.
Digital manufacturing technologies, such as CAD/CAM, physical, thermal, and manufacturing simulation software, rapid prototyping, automated quotations, and DFM feedback, play a crucial role in implementing DFX principles. By applying DFX principles in tandem with digital manufacturing, companies can proactively address design challenges, streamline production, and minimize waste to reduce costs and improve product outcomes.
If you want to scale your products from prototyping to production with the factors of DFX in mind, sign up with Fictiv and upload your part files to get started!
Key DFX Methodologies and Their Benefits
Design for Excellence combines the practices of 6 individually developed methods that focus on improving a particular aspect of the product design and manufacturing operation. Fictiv utilizes these methods to help manufacturers refine and optimize their product design, manufacturing processes, material usage, costs, and more. The various Design for Excellence methodologies and their benefits are:
Design for Manufacturability (DFM)
DFM ensures that products can be efficiently manufactured at scale by optimizing design features to reduce material waste, tooling costs, and overall complexity. Engineers focus on refining part geometries to improve machinability and manufacturability for whatever production processes are required, including CNC machining, casting, injection molding, sheet metal fabrication, and 3D printing. DFM strategies such as minimizing undercuts, geometrical tolerancing, and selecting appropriate materials enhance efficiency and reduce production bottlenecks.
Fictiv offers instant DFM feedback through the quoting platform, and expert advice on best practices through design feedback.

Design for Assembly (DFA)
DFA focuses on simplifying product assembly by minimizing the number of components and designing for ease of assembly. This methodology helps reduce part counts, which lowers labor costs for assembly and improves production speed. Common DFA strategies include replacing screws with snap-fit features, designing modular components that can fulfill multiple functions and fit within different products for streamlined assembly, and standardizing parts to reduce complexity.
Fictiv aids in DFA implementation in the 3D modeling and drafting processes. By offering rapid prototyping services, Fictiv allows engineers to iterate and validate assembly-friendly designs suitable for mass manufacturing, while also ensuring compatibility with global supply chains. Download our free DFA checklist to learn more.
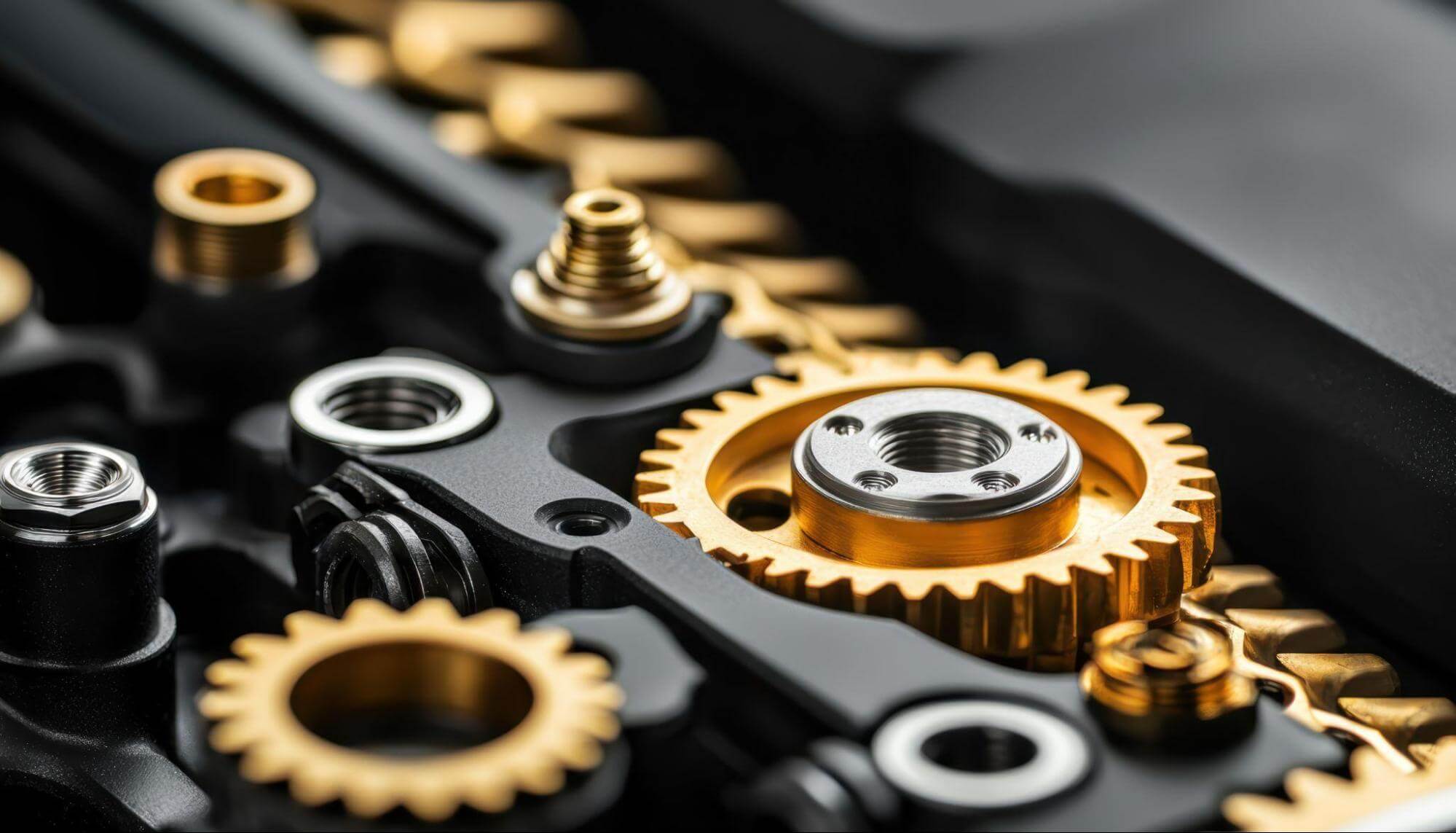
Design for Reliability (DFR)
Design for Reliability ensures that products maintain required performance levels throughout their planned design life, thus minimizing failures and warranty costs. Selecting high-quality materials that balance cost and quality while simultaneously resisting wear and environmental stressors is a key component of DFR. Fictiv engineers also conduct rigorous, accelerated thermal and mechanical stress and corrosion testing during the design phase to validate product longevity.
Fictiv supports DFR by minimizing the amount of physical testing to be completed for both product quality and manufacturing operations. While failure mode and effects analysis (FMEA) is highly effective in identifying potential risks throughout the design and manufacturing process, it is not a perfect method. Software and its integration with DFR practices synergize with FMEA to make everything from the product development stage to mass production seamless.
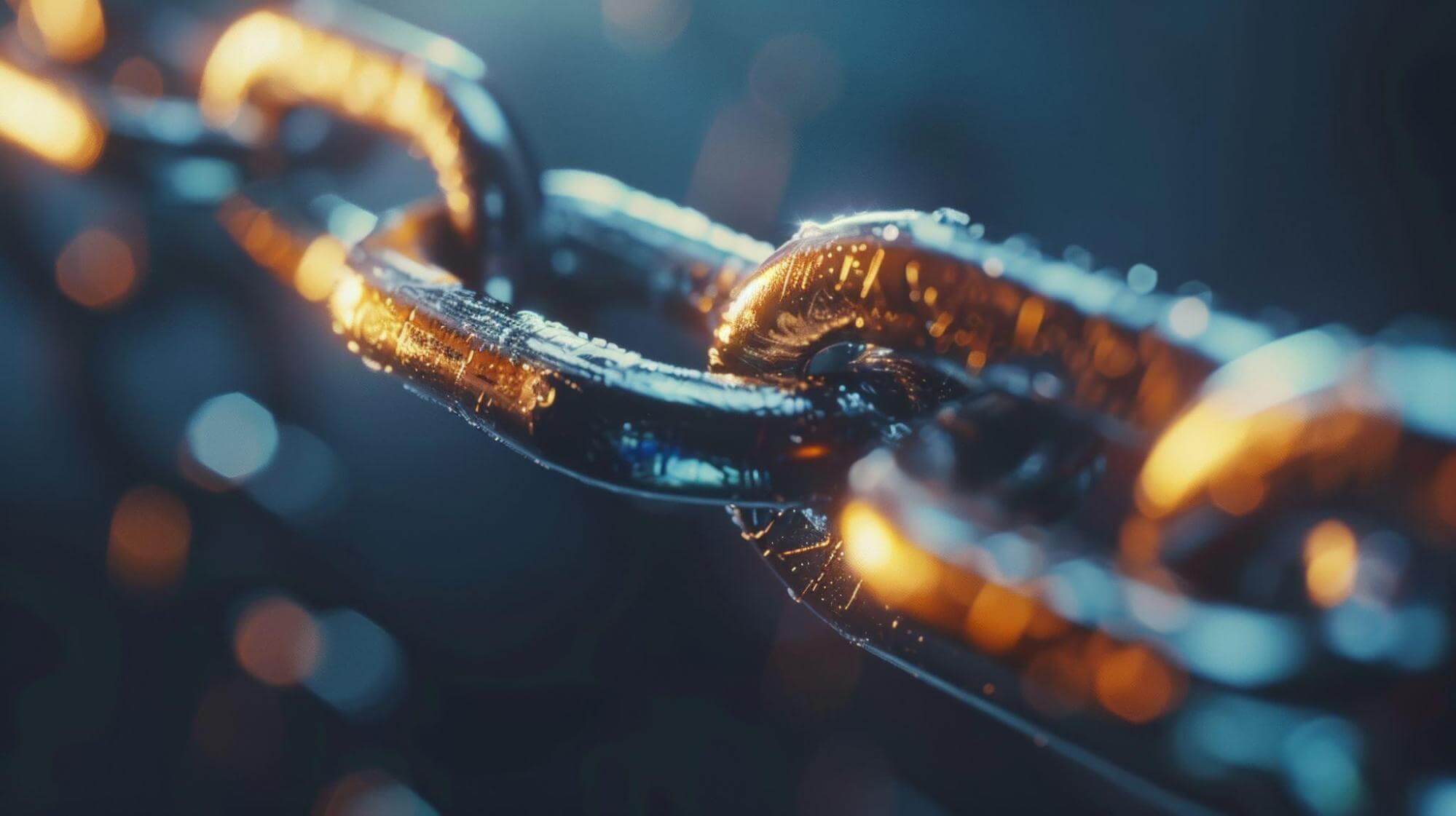
Design for Cost (DFC)
DFC aims to reduce overall production costs while maintaining high product quality by identifying cost-saving opportunities in materials, manufacturing techniques, and logistics. Strategies include substituting reinforced polymers for expensive metals, designing for efficient material usage, and leveraging standard off-the-shelf components instead of custom-machined parts. This method when used with existing products is also often referred to as “costing-down” your bill of materials.
Fictiv’s AI-powered cost analysis tools help engineers compare manufacturing options faster than typical FMEA processes, allowing them to make informed decisions that balance cost efficiency with performance.
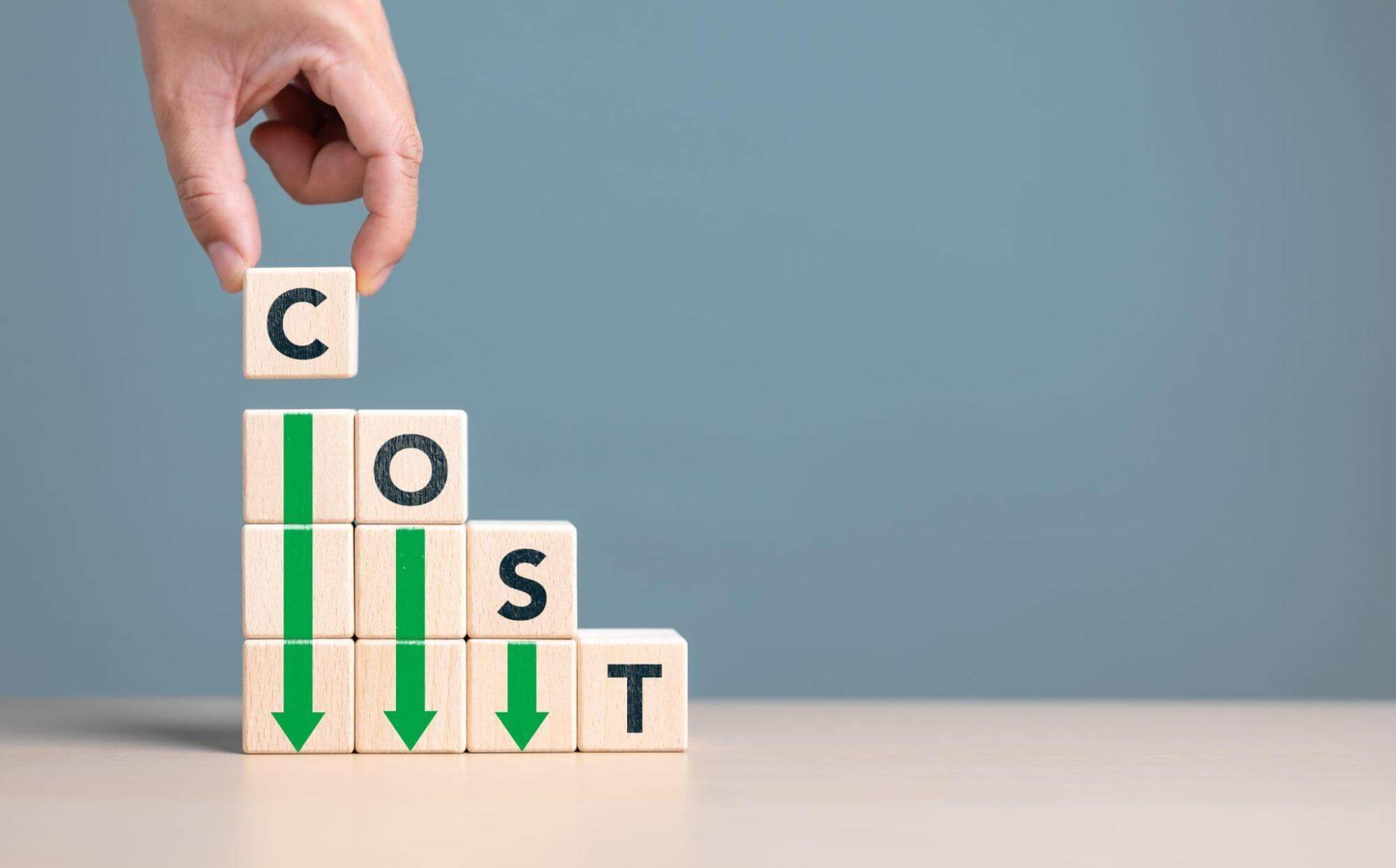
Design for Sustainability (DFS)
DFS is typically applied when eco-friendly manufacturing practices are desired. DFS emphasizes environmentally friendly design by proposing sustainable materials and optimizing processes to minimize waste. Engineers focus on selecting recyclable or bio-based materials, reducing excess material usage, and designing around energy-efficient manufacturing techniques. Weight reduction design strategies also help decrease material consumption without compromising structural integrity.
Fictiv supports sustainability efforts using DFS by offering eco-friendly material options and localized manufacturing services to reduce transportation-related carbon footprints.
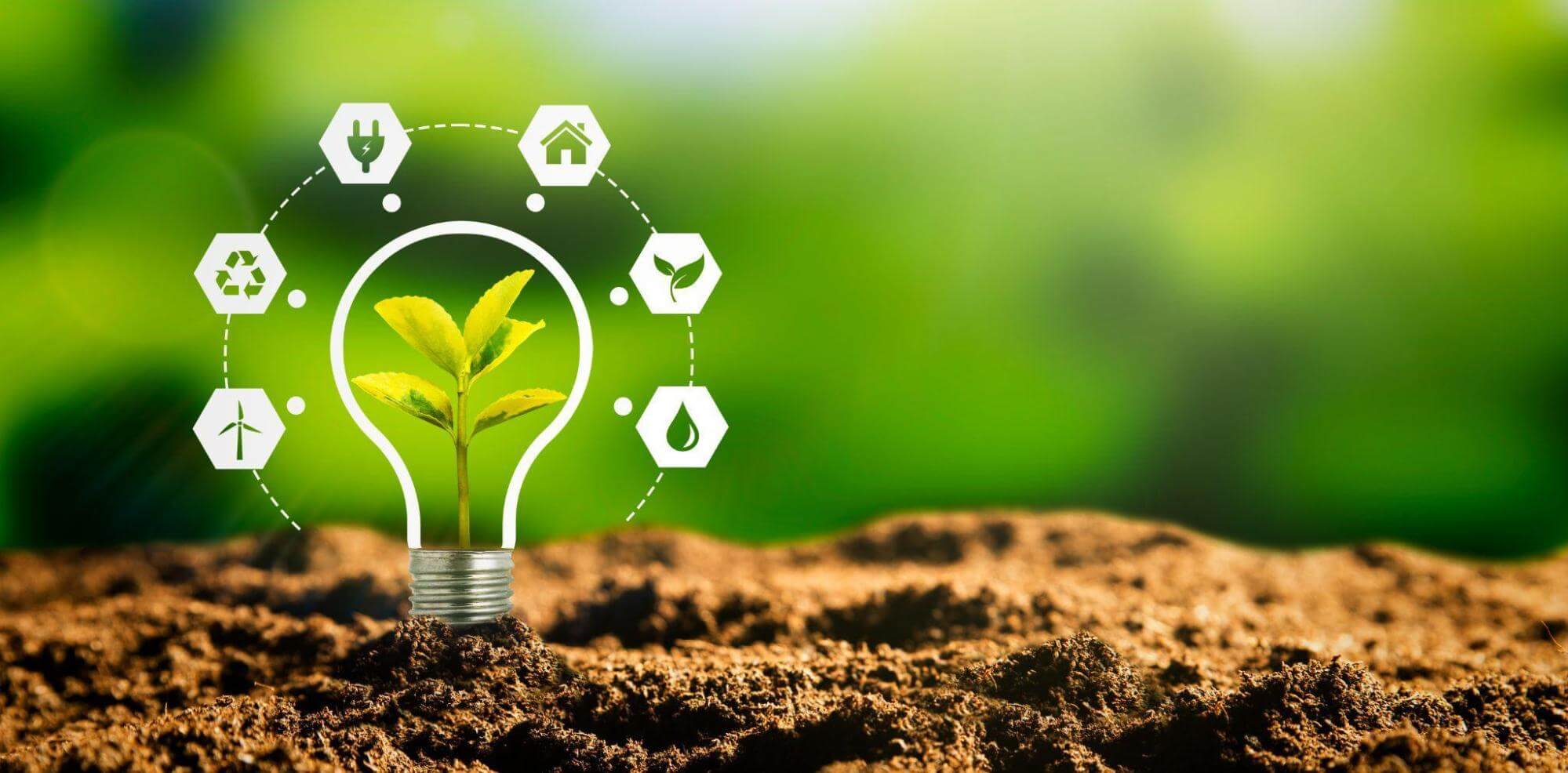
Design for Testing (DFT) and Design for Serviceability
DFT ensures that products can be easily tested for defects before full-scale production, while Design for Serviceability focuses on making products easier to repair and maintain. Engineers incorporate test points, modular components, and standardized fasteners to simplify quality assurance and servicing. For example, in printed circuit board design, integrated test points allow for quick diagnostics, while modular component layouts facilitate part replacement in consumer electronics.
Fictiv enhances these efforts by providing rapid turnaround prototyping utilizing advanced CAD and simulation software that enable functional testing and diagnostics before production and support iterative improvements based on real-world performance data.
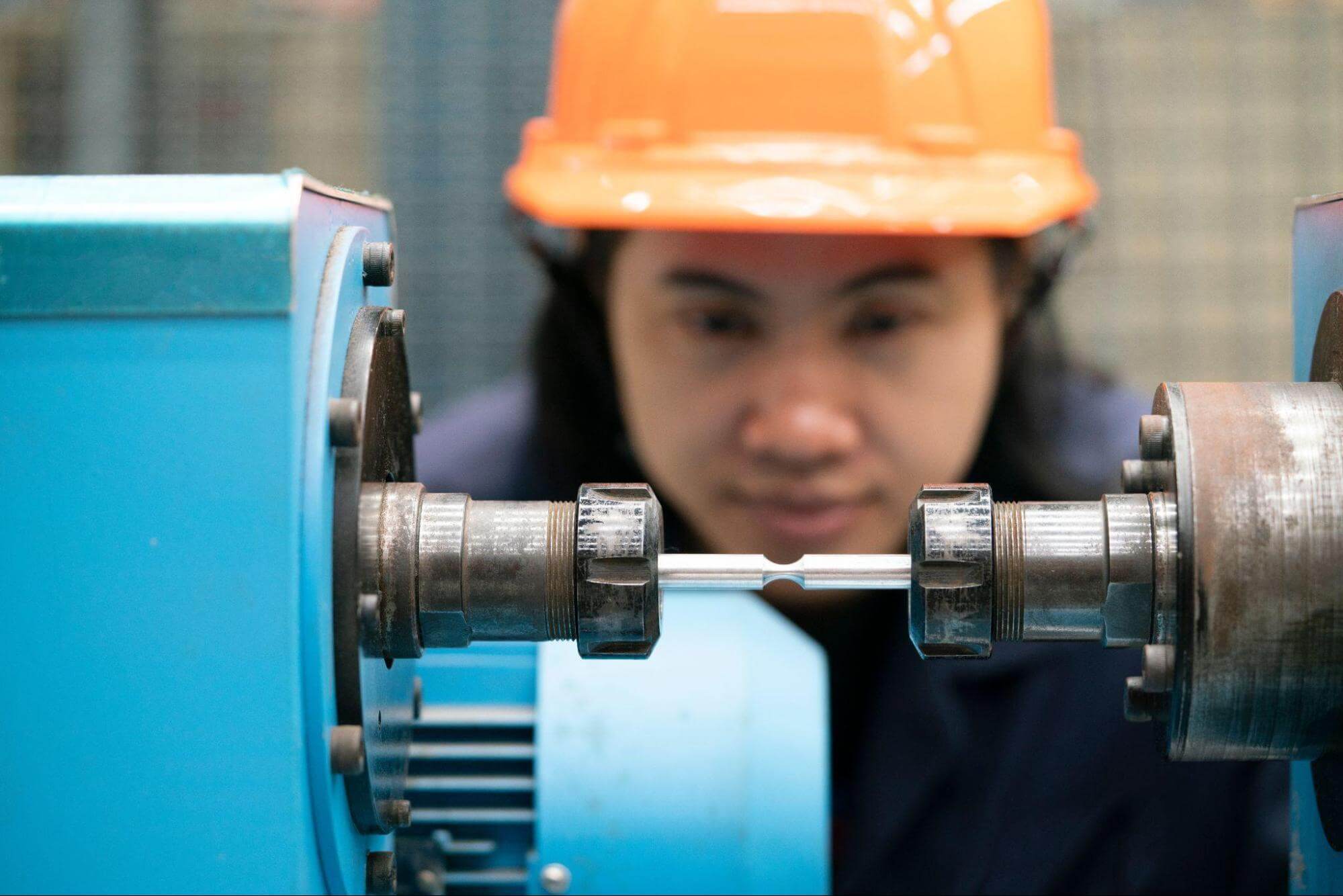
How DFX Improves Manufacturing Efficiency in Key Production Processes
Design for Excellence methodologies have been employed in numerous manufacturing sectors. Within those sectors, manufacturers who have adopted DFX have greatly benefited by reducing costs, optimizing lead times, minimizing time to market, and more. Some of the ways DFX improves manufacturing efficiency in different production processes are:
- Injection Molding:
- DFM benefits injection molding processes by pointing out potential changes that can reduce wall thickness variations, thus improving mold flow.
- DFA can be used to evaluate options for minimizing the number of components in multi-part assemblies, which simplifies production.
- DFS (Design for Sustainability) emphasizes environmentally friendly practices and materials by suggesting recyclable thermoplastic materials.
- Casting (Die Casting and Urethane Casting):
- DFM can help to optimize gating and venting to ensure smoother material flow, preventing defects, and inconsistencies in the final product.
- DFC assists the designer in using and applying additive tooling and practices to reduce die costs, and enable more cost-efficient mold creation without compromising precision.
- DFR offers manufacturers the opportunity to stress test to ensure durability against thermal fatigue.
- Sheet Metal Fabrication:
- DFM can improve the manufacturability of sheet metal components by simplifying bending processes for efficient forming and suggesting maximum deformation in the workpiece during each stamping operation.
- DFC aids in optimizing material utilization by determining how parts can be most efficiently laid out on a blank.
- Suggesting standardized fasteners for easier repairs enhances serviceability.
- 3D Printing:
- DFM helps optimize print orientation and layer alignment to enhance structural strength and maximize durability.
- DFC assists in selecting cost-effective materials for low-volume production, balancing performance with affordability.
- DFS employs lattice structures to minimize material usage while maintaining mechanical integrity, which contributes to sustainable manufacturing practices and lightweight yet strong designs.
- CNC Machining:
- DFM calculates ways to reduce tight tolerances in key locations and streamline and optimize machining processes.
- DFC produces optimal machining sequences to minimize tool changes, thus reducing cycle times and improving production efficiency.
- DFR enhances product longevity by suggesting mechanically and thermally resilient and corrosion-resistant metals that ensure long-term durability in various environments.
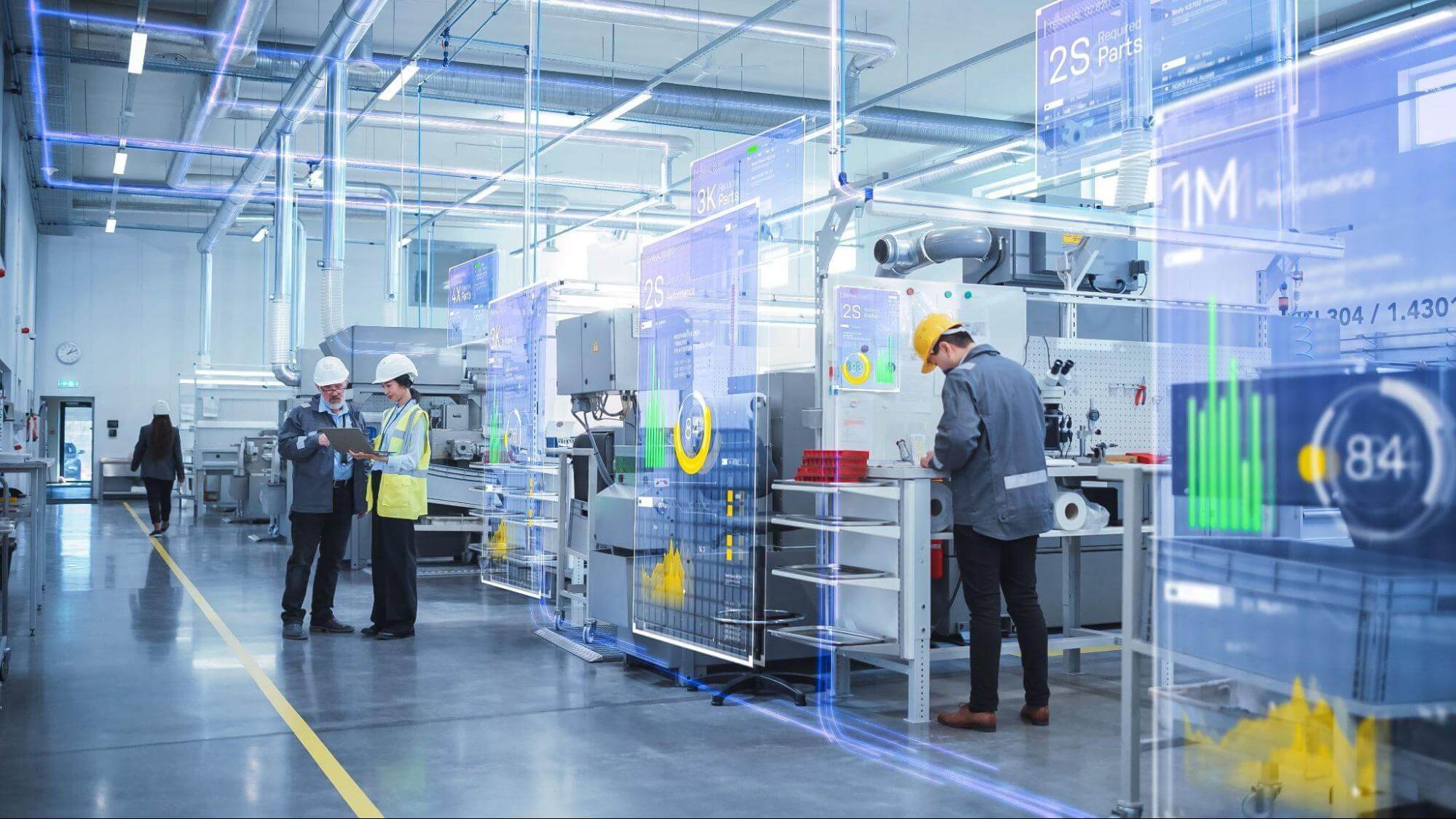
The Role of Digital Manufacturing in DFX
The integration of digital manufacturing with practices like cloud-based platforms, AI-driven design analysis, and on-demand prototyping further enhances the benefits of DFX implementation. This suite of technologies enables engineers to optimize product designs more efficiently, reduce costly design errors, ensure manufacturability without traditional “cut-and-try” iterations, and achieve a fully verified design before full-scale production begins.
Digital platforms allow real-time updates and quick DFM feedback loops on product designs. This facilitates seamless collaboration among designers, manufacturers, and suppliers and reduces the number of iterations needed before the product is ready for series manufacture. AI-driven tools analyze designs for potential manufacturing issues and suggest improvements instantly, enabling engineers to make data-driven decisions that improve quality and efficiency.
On-demand prototyping is a crucial element of digital manufacturing. It allows for the rapid validation of design changes through 3D printing, CNC machining, and other quick-turn fabrication methods. This capability significantly shortens development cycles and enables companies to test and refine their products before committing to large-scale production.
Additionally, digital manufacturing platforms provide instant quoting and cost analysis, helping organizations make informed financial decisions and compare different manufacturing approaches. By integrating these digital tools, companies can enhance their DFX strategies, leading to more cost-effective, reliable, and sustainable product designs.
DFX Principle | How Fictiv Helps |
DFM – Manufacturing | Instant DFM checks, expert reviews, tolerance guides |
DFA – Assembly | Additive part consolidation, assembly-friendly feedback |
DFC – Cost | Real-time cost estimation and process comparisons |
DFR – Reliability | Process-specific guidance, high-quality builds |
DFS – Sustainability | Less waste with on-demand manufacturing, eco-friendly material options, localized manufacturing |
DFT – Testing | CAD and simulation software that enable functional testing before production |
Table 1: How Fictiv Helps with DFX Principles
Why DFX Matters in Product Development and How Fictiv Helps
DFX (Design for Excellence) is a critical element of modern product development. It enables early optimization of manufacturability, cost-efficiency, reliability, and sustainability in product designs. By leveraging digital manufacturing services like Fictiv, organizations can accelerate DFX adoption to optimize product designs for superior performance and market competitiveness.Ready to take your product designs to the next level? Sign up with Fictiv today to access powerful DFX tools, expert guidance, and a seamless digital manufacturing platform that simplifies prototyping and production. Whether you’re refining early-stage concepts or scaling for mass production, Fictiv helps you move faster, smarter, and more sustainably—easily turning great ideas into market-ready products.