Time to read: 4 min
Your Guide to Fictiv’s Design for Manufacturability (DFM) Process
When plastic part designs reach a certain level of maturity, manufacturing methods like 3D printing and CNC machining can fall short on delivering high-caliber parts in the time (and at the cost) required. That’s why — due to its ability to quickly and cost effectively scale up production — injection molding is often the manufacturing method of choice.
Prototype (or low volume) injection mold tooling can produce near-perfect representations of final parts, which is critical for the design validation process. Injection molding also allows you to achieve more complex features at tighter tolerances. And once the mold is built, identical parts can be produced thousands of times over.
However, designing and fabricating an injection mold is a very exacting process where any mistake can result in out-of-spec parts and costly fixes. That’s why Design for Manufacturability (DFM) validation is such a critical step early in the injection molding process.
Fictiv’s DFM feedback process helps “detect” complexity and address part and mold design issues early on — effectively minimizing lead times and quality risks. This is achieved through a highly collaborative, transparent and evidence-based approach that combines automation with expert-driven methods. Now, let’s explore the process.
Project Fit Evaluation
After Fictiv receives an injection molding quote request, a team of technical experts evaluates the design and project requirements to determine whether the design, use case, size and quantity are appropriate for the injection molding process. If injection molding is deemed unsuitable for the project, an alternative process such as urethane casting, 3D printing or CNC machining may be recommended. This step helps prevent any wasted time on quoting and tooling, and helps you adopt a manufacturing process that better aligns with your design and application.
Preliminary DFM Feedback
Once a project is qualified for the injection molding process, DFM engineers evaluate the manufacturability of the part design by conducting pull direction, draft angle, parting line and thickness analyses. If a part includes elements that make it non-manufacturable or introduce risks to quality, design changes will be easier to make the earlier they are identified. During this time, you will also receive a quote, including price and lead time, for the mold and the requested parts.
Fictiv evaluates the manufacturability of the part design and provides a DFM report free of charge. The evaluation is enabled by Fictiv’s proprietary computational geometry technology. The report presents clarifying expert insight into the issues, a definition of project scope and next steps to address design issues.
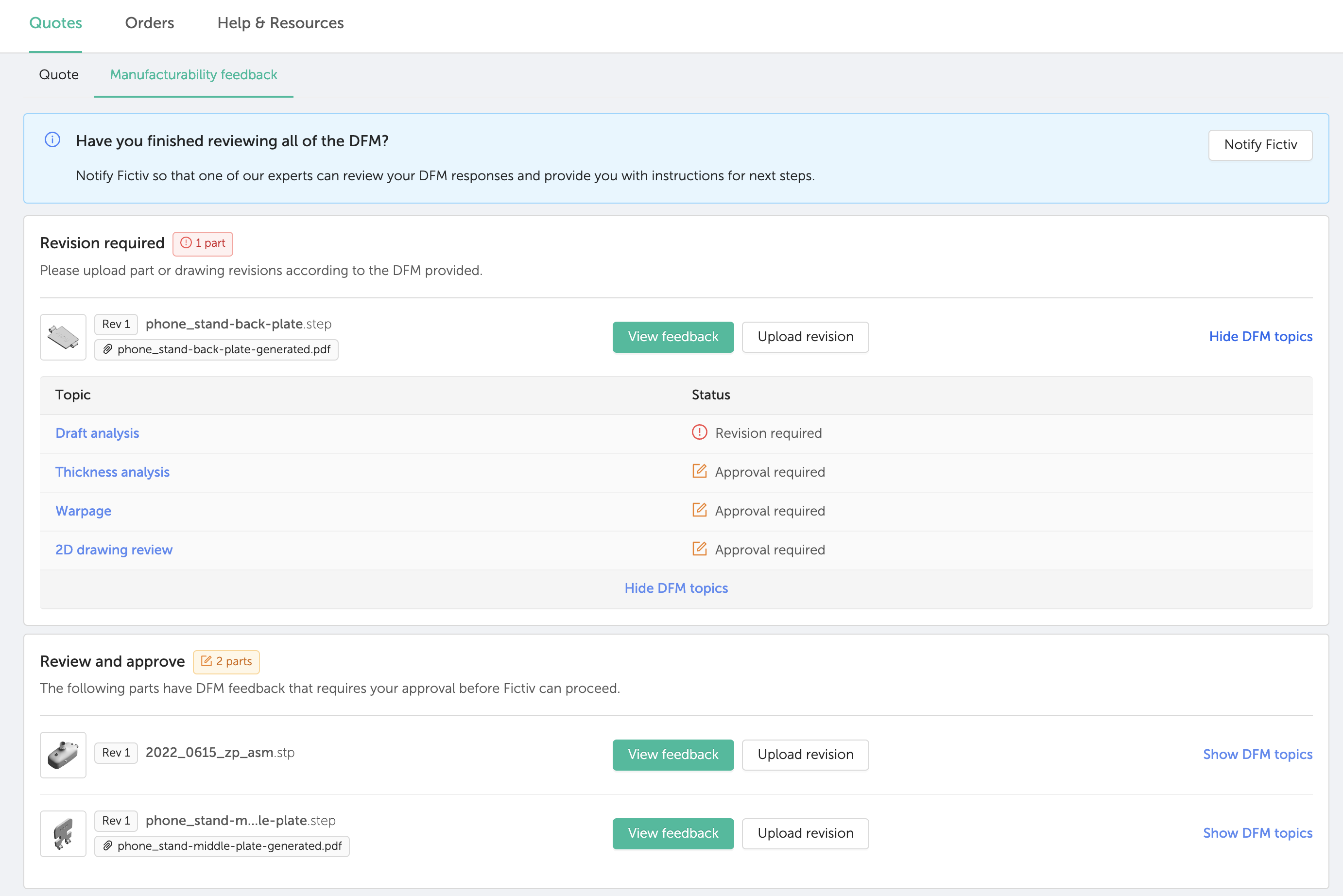
You can view all DFM reports online through Fictiv’s customer platform. The Fictiv platform is a secure web application that provides a fully streamlined process and makes all necessary information about your injection molding project available in one place. From the platform, you can:
- View important issues at a glance
- Upload updated CAD files based on provided DFM feedback
- Submit approval to proceed
- Follow project actions, updates and issue statuses
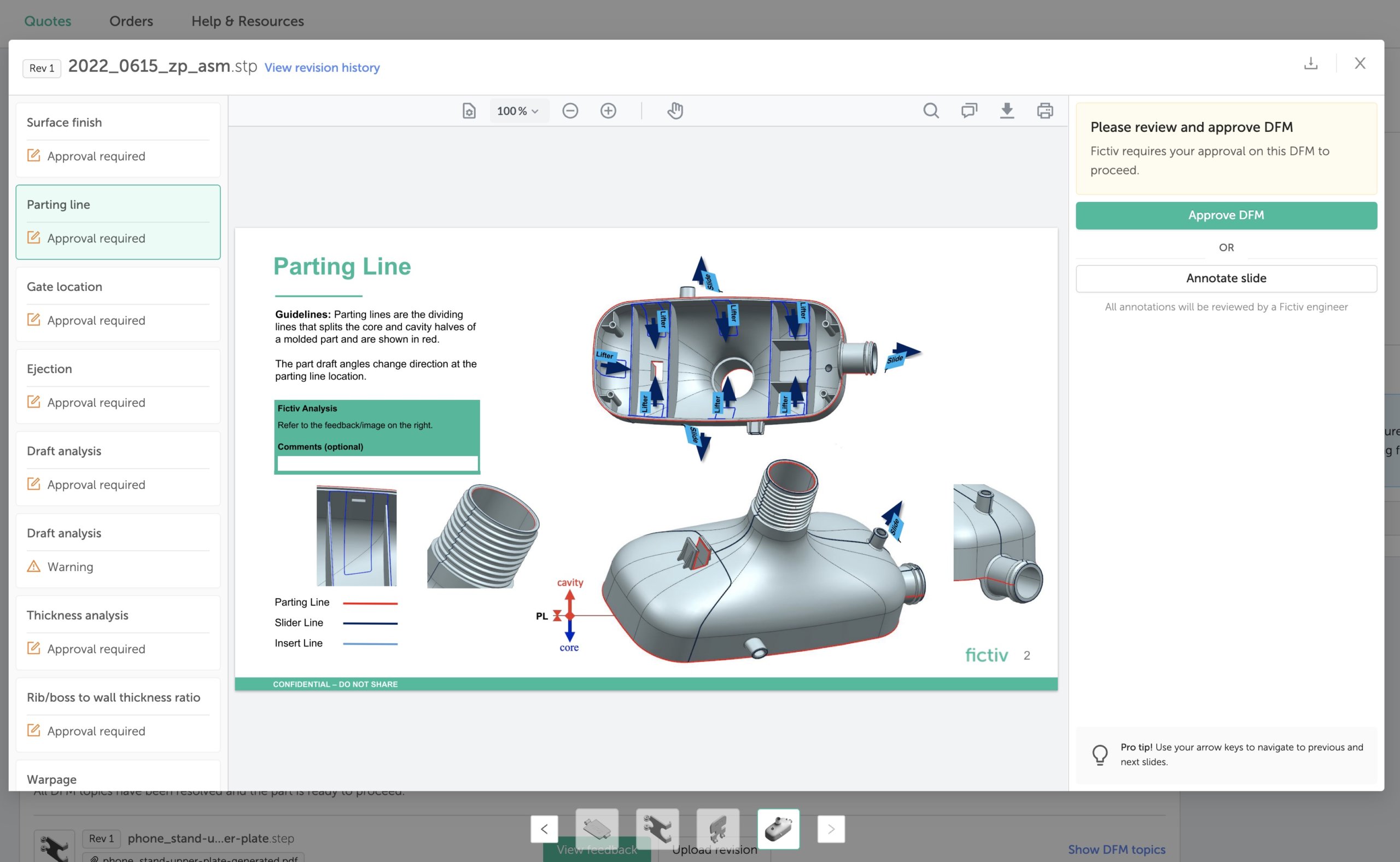
These capabilities have transformed the DFM process — removing the constant back and forth between customers and injection molding suppliers. This allows you to spend more time focusing on your part design and less time project managing.
Project Kickoff
Once preliminary design issues have been addressed and an injection molding order is placed on the platform, Fictiv will assign the project to an injection molding manufacturing partner who is best equipped to fulfill your project specifications. A second DFM analysis will then be performed to review mold and part design. Upon approval of all DFM feedback, Fictiv’s assigned manufacturer will begin the mold fabrication process.
Inspection and Quality Control
After completion of the mold, the next step is the production and inspection of trial T samples. Fictiv offers standard inspection methods like CMM and optical inspection as well as a variety of advanced methods like PPAP, GR&R, CpK, PFMEA and Control Plan for an additional cost. Certificate of compliance and material certificates are also available upon request.
Once the T samples pass inspection, Fictiv will:
- Make inspection reports available on the Fictiv platform
- Ship T samples to you for final approval
- Schedule the production run upon T sample approval
- Ship the parts to you
After the first production run, Fictiv will keep the mold. This makes ordering future parts from that mold more streamlined and convenient.
Change Orders
Fictiv covers injection molding needs in all stages of a product’s life cycle — from new product introduction to mass production — and design changes are an inevitable part of a plastic part’s evolution.
To be flexible with these design changes, Fictiv offers the ability to use steel molds for all kinds of use cases. The advantage of steel molds is that they can be modified numerous times without compromising the quality of the parts. Another important advantage of steel molds is that they are extremely durable and can endure hundreds of thousands of production cycles with little to no maintenance.
Fictiv allows design changes to parts and existing molds at any time, which can be done by uploading the new part design on the Fictiv platform. Whenever a design change is submitted, Fictiv will run another round of DFM evaluations, provide a quote and (once approved) apply the modifications accordingly. After that, a rerun will be initiated to produce the revised parts.
Enabling Efficiencies and On-Demand Production
Offering online injection molding services and DFM feedback is nothing new. Many traditional molders offer these things. But unlike traditional molders and other digital manufacturers, Fictiv is able to address process and design pain points quickly while offering the flexibility required for custom injection molded parts. Fictiv accomplishes this through its investment in best-in-class software, a geographically diverse network of manufacturing partners, and a focus on developing end-to-end solutions that provide speed, clarity, transparency and cost-effective results.