Time to read: 4 min
In plastic injection molding, the cooling of the mold is critical to the quality of the part. That’s because mold cooling affects the part cooling that occurs after molten thermoplastic is injected into the tool. Traditionally, cooling is achieved with cooling lines that are cut or drilled into the mold inserts to allow water or oil to flow through the mold block. These channels are cut as closely as possible to the surface of the part in order to provide optimal cooling.
Part cooling is one of the longest steps in the injection molding process and, therefore, has a considerable impact on part costs. Proper cooling can also make the difference between a quality part and one that has issues with warping, weld lines, and material degradation. Injection molded parts that are not cooled correctly tend to have inconsistent material shrinkage and, therefore, develop defects. Material that cools too quickly will increase the flow-front welding and cause weld lines or knit lines in the final part. Material that is not cooled quickly enough will begin to degrade and lose some of its physical properties.
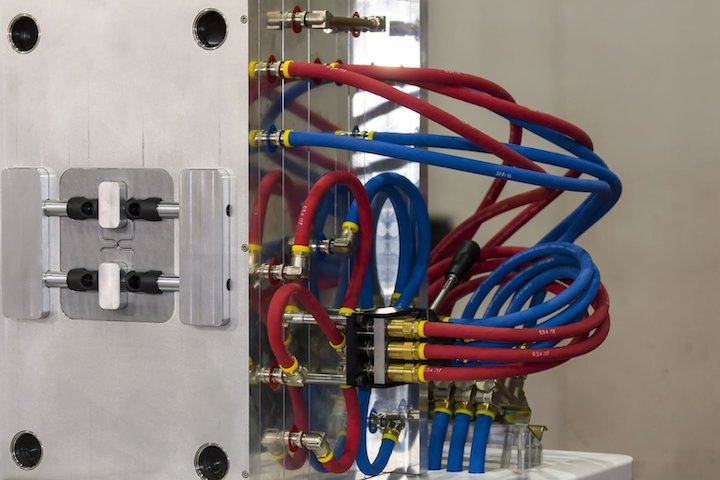
Although traditional cooling lines require drilling or milling, an advanced method called conformal cooling has become more mainstream over the past 10 or 12 years. Conformal cooling can be achieved with split inserts that are milled and soldered back together; however, this process is challenging and can reduce tool life.
Today, the most common way to produce conformal cooling lines is by 3D printing inserts with direct metal laser sintering (DMLS), or a similar process. With DMLS, you can 3D print an insert where the cooling lines are modeled directly into the insert and are printed at the same time as the insert itself. This allows for more complicated shapes and for the cooling lines to be closer to the part cavity than is possible with milling or drilling.
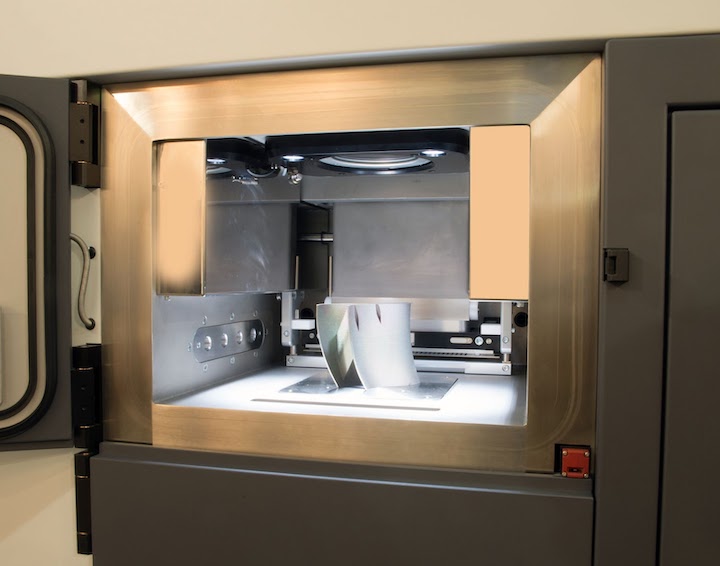
As with any technology, there are applications and circumstances when the conventional approach is more appropriate than the newer one. This article examines the advantages and disadvantages of conformal cooling vs. conventional cooling lines. But if you want to learn more about injection molding part design, check out our guide!
Download Fictiv’s Injection Molding Design Guide
What Makes Conformal Cooling Cool
The first and most notable advantage to conformal cooling is that you can design cooling channels in any shape and get them closer to the surface of the part. This improves the speed at which you can cool a part and, therefore, eject the part to begin molding the next one. Because time is money in injection molding, every second counts when you’re molding millions of parts. For this reason, when you consider a high-volume production tool, you should also consider using conformal cooling.
The second main advantage of conformal cooling is related to the first. By having the cooling channels closer to the part, you get more consistent cooling near the part’s surface and a higher quality plastic part. The greater control that conformal cooling provides supports consistent cooling, which helps to avoid warping and weld lines. Also, the quicker cooling cycle means that the plastic spends less time at higher temperatures — material held in a molten state for too long will begin to break down and degrade — which means higher quality parts and fewer molding issues.
Lastly, when a 3D printed insert includes conformal cooling channels, you have complete design flexibility over where the lines are placed, how close they come to the surface of the part, and what shape the lines take inside the tooling. In other words, you’re no longer bound by what you can do with intersecting straight lines. This means that you can easily run cooling lines into small areas that are impossible to reach otherwise.
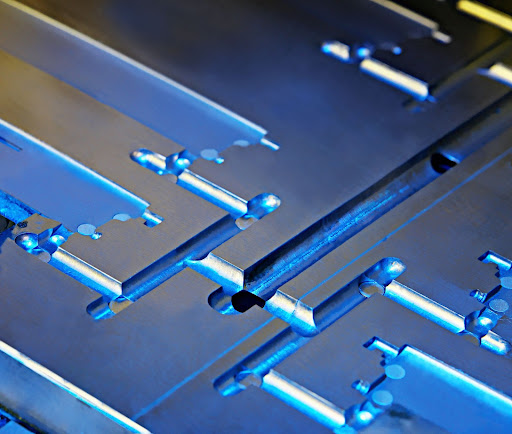
Drawbacks to Conformal Cooling
One of the biggest drawbacks to conformal cooling is higher costs on the front end. It’s significantly more expensive to 3D print a block of material than to CNC machine a block of similar size. Also, those 3D printed inserts require machining to achieve the flat surfaces required for mating with other mold components — it adds up to make conformal cooling pricey.
Secondly, it takes a different skill set to design conformal cooling channels than traditional cooling lines. Conformal cooling requires more complicated shapes, and the design time for conformal cooling can delay the start of tool making. If you’re injecting molding higher volumes, you can make up for this slower start over time. For low part volumes, however, delays in tool making make for noticeably longer lead times.
Lastly, maintenance and repair can be costly for inserts that are 3D printed. Because these lines are not easily machined, a repeated failure or leak probably means making a new 3D printed insert, and you’ll have to account for those costs. Having the water lines closer to the mold cavity also limits which types of engineering changes can be made to the tooling.
Where the Rubber Meets the Road
Ferraris are amazing machines, and driving one is equally amazing. Conformal cooling is a similarly amazing experience for injection molders. But, like making a run to Costco in a Ferrari, the amazing-ness of conformal cooling is contextual — it isn’t the best option for every situation. When you have a super-complicated part design, conformal cooling is the only way to go. For most other part designs, conventional cooling is plenty good enough to get you great results.
Fictiv — Complex Injection Molded Parts at Ridiculous Speeds
A good plan and skilled production partner are critical to avoid the added costs and risks that come with improper cooling methods for injection molded parts. Fictiv has the global manufacturing network and production experts you need to get quality injection molded parts, no matter how complex your designs. And we have the skills and know-how to help you choose the right cooling method for your parts, and support you from part design through prototyping and production.
Create your free Fictiv account and request an injection molding quote today — we mold complex parts at ridiculous speeds!